
DOMINIKA HORA
Production Manager at George Botanicals- Claim this Profile
Click to upgrade to our gold package
for the full feature experience.
-
English -
-
Polish -
Topline Score
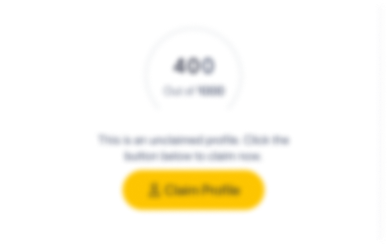
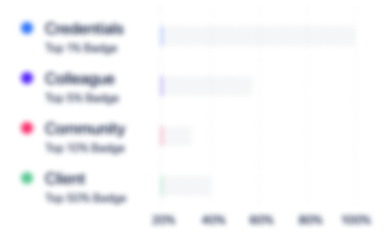
Bio


Experience
-
Goodbody Botanicals
-
United Kingdom
-
Alternative Medicine
-
1 - 100 Employee
-
Production Manager
-
Aug 2019 - Present
-
-
-
Dairy Crest
-
United Kingdom
-
Food and Beverage Services
-
500 - 600 Employee
-
HSE Coordinator
-
Apr 2016 - Jul 2019
• Regular review accident and, NM and dangerous occurrence • Development Emergency Plan• Develop maintain and promote the implementation of the project HSE• Lead the site H&S Committee and governance • Implement and ensure corrective actions are met in order to maintain compliance• Review Management system and Environmental Plan• Develop and maintains of the site records for compliance and training therefore a high level of document control, data management and reporting competency including trending and analysis• Create RA and SSOW• Supervisors delivery RA using appropriate methods• Promote a positive safety culture through proactive monitoring and enforcement • Conduct audits (include ISO 14001:2015 ,Integra audit)• Participating in regular HSE and Environment Meeting• Develop procedures to improve H&S performance • Check on subcontractor to ensure full compliance • Driving employee engagement with the behavioural safety programme, continual improvements, through annual plans and KPI’s• Working closely with the senior leadership team, members of group HSE as well as external agencies, to meet the requirements the requirements of any license/permit to operate• Demonstrates good coaching, influencing and presentation skills
-
-
Production Line Manager
-
Mar 2013 - Apr 2016
-Successfully promoted for the role passed internal lead develompment program-Taking resposibility as a FLM for over 40 people-Continuous improvement for waste management-A proven track record of developing and training staff -Daily performance monitoring and support team to reach target-Regular safety inspection-issues and avoiding hazard to protect all employees-Resolving my review and investigation, ensuring all employees are trained and developed for every required task-Conduct staff induction's and training in liaison with HR -Investigate and report on all injury accidents and occurrences throughout the production department-Dealing with time and attendence system on dail bassis- Ensure appropriate work instructions and SSOW and SOP are in place and team members adhere to them-Planning full time staff and agency worker allocation and training program-Strong background of supportind staff,drive team to receive best performance with best quality product-Improve product quality ,reduce waste and customer complaints-Resolving daily basis production problems-Managing & maximising efficiencies.
-
-
Production and Hygiene night Manager (temporary position)
-
Apr 2012 - Mar 2013
-Taking resposibility for over 35 people-Manage Bio-Trace system-Manage pest control -Regular safety inspection-issues and avoiding hazard to protect all employees-Manage hygiene systems, procedures and training( a prove track record of developing)-Manage the Hygiene Department to ensure all standards are met in a safe and healthy environment-Resolving my review and investigation, ensuring all employees are trained and developed for every required task-Conduct staff induction's and training in liaison with HR -Investigate and report on all injury accidents and occurrences throughout the production and hygiene department-Dealing with time and attendence system on dail bassis-Setting cleaning schedule-Resolving daily basis production problems
-
-
Team Leader
-
Feb 2005 - Mar 2012
-Look after 7 people-Lead and motivate a team-Monitoring of quality and production levels to highlight any problems -Ensure all non-conformities are identified and discussed with the Operations Manager at the earliest opportunity. -Arrange the work organisation with the team-Ensure all work meets with the customer’s specification, the production plan and the required quality standard-Support on new product introduction-Maintain good housekeeping practices throughout the working areas-Carry out additional tasks agreed with the Operations Manager-Review daily performance of team and ensure all KPI’s are achieved
-
-
Community
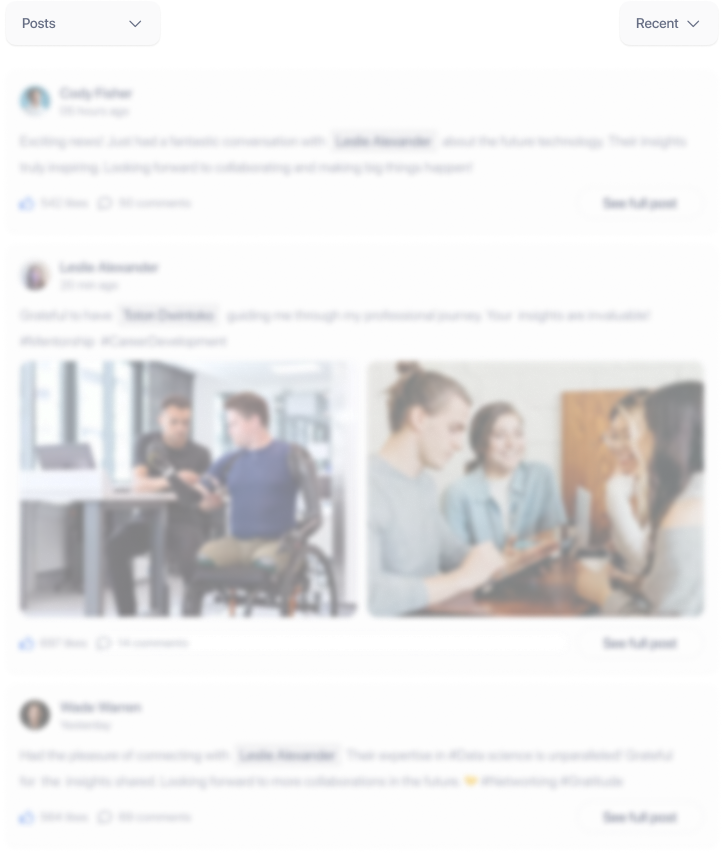