
Diedra Austin
Purchasing/Inventory Clerk at Darling Ingredients, Inc.- Claim this Profile
Click to upgrade to our gold package
for the full feature experience.
Topline Score
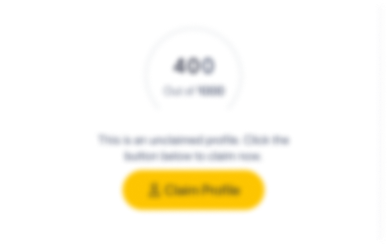
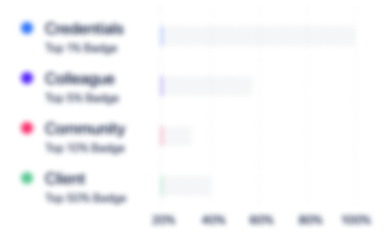
Bio


Experience
-
Darling Ingredients, Inc.
-
United States
-
Manufacturing
-
100 - 200 Employee
-
Purchasing/Inventory Clerk
-
Dec 2022 - Present
-
-
-
DynaTen Corporation
-
United States
-
Construction
-
100 - 200 Employee
-
Procurement Technician
-
Jun 2022 - Dec 2022
Contracted with Bell Helicopter Contracted with Bell Helicopter
-
-
-
-
Procrument
-
Mar 2022 - Jun 2022
-
-
-
Lone Star Dairy
-
United States
-
Dairy Product Manufacturing
-
1 - 100 Employee
-
Maintenance Planner
-
Mar 2021 - Dec 2021
-
-
-
-
Purchaser
-
Feb 2017 - Dec 2021
-
-
-
Grand Casino Mille Lacs & Hinckley
-
United States
-
Gambling Facilities and Casinos
-
400 - 500 Employee
-
Central Reservations Rep
-
Aug 2016 - Oct 2016
-
-
-
-
HVAC Dispatcher
-
May 2016 - Aug 2016
-
-
-
Hilmar
-
United States
-
Food and Beverage Manufacturing
-
500 - 600 Employee
-
Maintenance Admin Clerk
-
Sep 2009 - Apr 2016
check work orders and booked hr, upload to eamorder maintenance supplies for the shopsubmit pos for outside worksupply mechanics with tools and toolbox'sfile work orders and outside contractor invoicesprint work orders for the mechanicsschedule contractor pms such as scale calibrations, fire supression testing, sprinkler testing, alarm system testingdata entrykeep inventory of shop radioskeep inventory of supplies for the shopcreate work orders and work requestassign work ordersplanning and schedulinginsure that all department filing systems are updated and organizeddevelop and maintain department Operating Proceduresresponsible for gathering, creating and maintaining periodical compliance on all federal and state reportsmaintain, in conjuction with planner/scheduler, accurate equipment libraries and information systemworks closely with HR on new hire orientation, informationorganize and maintain all maintenance contracts and outside agreementsmanage po's for outside vendors/contractors, schedules and coordinate outside service for site repairsreview oustide vendors pricing for errors and billing for buyer, maintenance planner and office positionstrack all maintenance/facilities/water reclamation personnel data to include, PSR's, vacation, sick time, department safety records, and training records. in addition to other responsibilities assigned by the maintenance leadership staff. maintain an accurate key listing and organized lock boxmaintain all department information boards as requiredact as vacation relief and fill out for absences for all office positionspriovide clerical support for all maintenance/facilities salaried personnelutilizes excellent communication and leadership skills to gain the respect and confidence of clients and co-workersability to thoroughly research, analyze situations, propose creative solutions, develop good rapport, and bring projects to completion.
-
-
VAT OPERATOR
-
Aug 2008 - Sep 2009
PRODUCTION OF CHEESE. MADE SURE THE VATS FILLED WITH MILK AND GET THE PROPER AMOUNTS OF STARTER, CALCIUM, MILK AND COLOR IF NEEDED. MADE SURE THE VATS WERE SET WITH THE PROPER RECIPES. MADE SURE THE BELT HAD THE PROPER SETTINGS FOR WATER, AND SALT. CHECKED THE VATS FOR SET TIMES. TOOK MILK AND WHEY SAMPLES FROM THE VATS. TOOK PUMP OVER SAMPLES FROM DMM1, CURD SAMPLES FROM SMC, AND WHEY SAMPLES FROM THE TANK BY THE TOWERS. I WOULD RUN MY SAMPLES TO MAKE SURE THE CHEESE HAD THE PROPER MOISTURE, SALT AND PH READINGS. I WOULD RUN MILK AND WHEY SAMPLES TO MAKE SURE IT WAS IN SPEC. WE WOULD RUN THESE TO SEE IF WE HAD TO MAKE ANY ADJUSTMENTS IN STARTER, WATER, OR SALT. MADE SURE THE SALT HOPPER HAD PLENTY OF SALT IN THE DISTRIBUTOR AND CHANGED THE EMPTY SALT BAGS.DID PERIODIC CHECKS ON THE HTST CHART, AND WROTE DOWN TIMES AND SILOS FOR SILO SWITCHES. CIP VATS AFTER PUMP OVERS TO THE BELT WERE COMPLETED AND GOT IT READY FOR THE NEXT FILL. CIP STARTER CANS WHEN THEY WERE EMPTY. I WOULD ASLO ADJUST AMMONIA INJECTIONS INTO THE STARTER CANS AND TAKE STARTER SAMPLES AFTER THE LAST AMMINIA INJECT WAS INJECTED TO THE CAN AND TAKE THE SAMPLE TO THE CHEESE LAB. SHUT DOWN AND SET UP FOR CIP IN THE STARTER ROOM, HTST, CREAM, AND MILK LINES FOR PRODUCTION. ALSO SET UP CIP LINES FOR THE VATS, BELT AND CURD DISTRIBUTOR PRODUCTION LINES AND CIP THE BELT. I WOULD ALSO BELT PREP AND WASH CHEESE DOWN THE BELT TO PREPARE FOR THE END OF THE PRODUCTION RUN. I WOULD TAKE THE LEFT OVER RENET AND COLOR TO THE COLD BOX TO STORE UNTIL THE NEXT PRODUCTION RUN. I WOULD ALSO CHECK TOWER TIMES, AND TROUBLE SHOOT ANY ISSUES WITH THE VATS, BELT, TOWERS, AND CURD DISTRIBUTOR. MADE SURE ALL CHEMICALS FOR THE VATS, BELTS, AND TOWERS WERE READY FOR CIP.
-
-
BOXER ROOM OPERATOR
-
Jun 2008 - Aug 2008
MADE SURE ALL CHEESE WAS BOXED, AND WEIGHED AND HAD THE PROPER STICKERS ON THE BOXES. KEPT THE BOXER LOADED WITH THE BOXES FOR THE CHEESE. DID PERIODIC METAL DETECTOR TESTS ON THE METAL DETECTOR. MADE SURE BOTH PRINTERS IN THE BOXER HAD PLENTY OF STICKERS. THE PALLETIZER PALLETS WERE STOCKED IN THE PALLETS DISPENSOR MACHINE. MADE SURE THE PALLETIZER WAS RUNNING WITH THE CORRECT PATTERS. PUT SHIPPING LABELS ON CHEESE PALLETS THAT GOES OUT TO THE COLD BOX. MADE SURE THE STRETCH WRAPPER ALWAYS HAD PLASTIC WRAP FOR THE CHEESE PALLETS. I ALSO WOULD TROUBLE SHOOT ISSUES WITH THE BOXER, SCALES, CONVEYORS, PALLETIZER DISPENSOR, PALLETIZER AND STRETCH WRAPPER. I WOULD ALSO STOCK THE CARD BOARD BOXES FOR THE BOXER. MADE SURE THE BOXER ROOM WAS CLEAN BEFORE THE NEXT SHIFT CAME IN.
-
-
TOWER OPERATOR
-
Mar 2008 - Jun 2008
BAGGED CHEESE TOWERS FOR 40LB BLOCKS, SEALED BAGS THROUGH THE SEALER BEFORE THE CHEESE IS SENT TO THE BOXER ROOM TO BE PACKAGED. CLEANED TOWER AREA, EQUIPMENT AND FLOORS. TROUBLESHOOT TOWER ISSUES.
-
-
Education
-
Amarillo College
Criminal Justice and Corrections -
AUSTIN SCHOOL OF MASSAGE THERAPY
Community
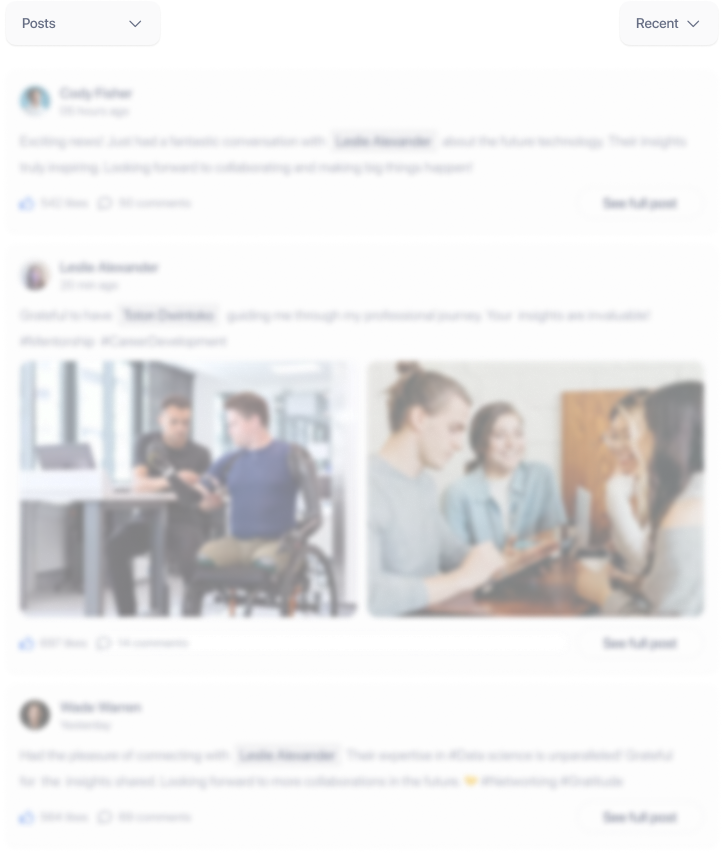