Didem Arı
Research Assistant at Manisa Celal Bayar Üniversitesi- Claim this Profile
Click to upgrade to our gold package
for the full feature experience.
-
English Full professional proficiency
Topline Score
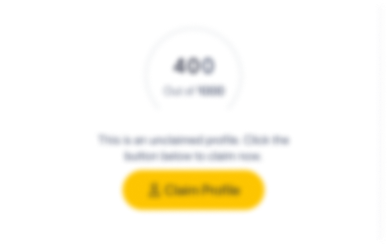
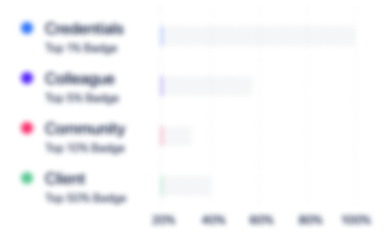
Bio


Credentials
-
ProQuest Writer Workshop Supporting Thesis Writing (Turkish)
ProQuestSep, 2021- Oct, 2024 -
Certificate of Basic Management Skills and Leadership Training (English- Turkish)
TSC AKADEMİNov, 2016- Oct, 2024 -
Certificate of ISO 14001:2015 Environment Management System Training (English- Turkish)
TSC AKADEMİNov, 2016- Oct, 2024 -
Certificate of ISO 9001:2015 Quality Management System Training (English- Turkish)
TSC AKADEMİNov, 2016- Oct, 2024 -
Certificate of OHSAS 18001:2007 Occupational Health & Safety Management System Training (English- Turkish)
TSC AKADEMİNov, 2016- Oct, 2024 -
Certificate of 5S-Methodology of Workplace Organization Training (English- Turkish)
TSC AKADEMİMay, 2016- Oct, 2024 -
Certificate of Kaizen Training (English- Turkish)
TSC AKADEMİMay, 2016- Oct, 2024 -
Certificate of Lean Manufacturing Training (English- Turkish)
TSC AKADEMİMay, 2016- Oct, 2024 -
Certificate of Teamwork & Problem Solving Techniques Training (English- Turkish)
TSC AKADEMİMay, 2016- Oct, 2024 -
English Certificate for C2
İngiliz Kültür Derneği Dil OkullarıMar, 2019- Oct, 2024
Experience
-
Manisa Celal Bayar University
-
Türkiye
-
Higher Education
-
1 - 100 Employee
-
Research Assistant
-
Apr 2022 - Present
-
-
-
SF TRADE TEKNIK TEKSTIL A.S.
-
Türkiye
-
Textile Manufacturing
-
1 - 100 Employee
-
Material Planning Engineer
-
Jun 2021 - Aug 2021
-
-
-
İlkim Makine Kalıp Plastik Fırça San ve Tic. A.Ş.
-
Türkiye
-
Plastics Manufacturing
-
1 - 100 Employee
-
Planning Engineer
-
Feb 2021 - Mar 2021
Getting orders from Micro system, creating production plans and presenting to related departments by making a meeting Creating a system on Excel to determine the required raw material and semi-product amounts of the products ordered Creating the work orders from the Micro system of the molds to be connected to the machines, hoses and absorbent brushs of vacuum cleaner to be producted and the products to be assembled, following and closing the work orders Entering Incoming and Outgoing Raw Material and Semi-Product Amounts into Micro System Getting labels from ZebraDesigner barcode system for products ready for shipment Creating machine stop codes and following stops Creating Pivot Table and making Pareto Analysis by entering machine stop datas on Excel Updating daily production reports Entering all data into daily production reports on Excel and making daily production meetings Creating scrap follow-up form to follow products going to recycle Providing follow-up breakdown related to machine and mold by creating a breakdown notification form Creating warehouse entry and exit registration forms on Excel to follow warehouse Presenting improvement ideas about the company Presenting to the R&D meeting members a project that the company desires to do by participating in the R&D Innovation and Industrial Application Support Program Decision Board Meeting and providing follow-up Following Potential Expenditures State Incentives Informing employees in production Making time study of the assembly department Ensuring to make maintenance by creating planned maintenance information form and maintenance follow-up schedule Making machine assignment of employees in production Show less
-
-
-
Delphi Technologies
-
United Kingdom
-
Motor Vehicle Manufacturing
-
700 & Above Employee
-
Quality Intern
-
Feb 2019 - May 2019
Checking & rewamping the documents Cancelling old documents using Excel & archiving the documents Updating new documents using Excel & filing the documents Giving change id for updated documents Updating weekly layer audit action plan, product audit, calibration, maintenance, FTQ & blocked part reports Updating contingency plan Preparing controlled copy for documents that are given to relevant department Attending layer audit at rework, quarantine, rail assembly & NHB lines Helping to design a ergonomic cupboard is called passbox for finished product by fulfilling future demands Show less
-
-
-
Güralp Vinç
-
Türkiye
-
Machinery Manufacturing
-
1 - 100 Employee
-
Planning Intern
-
Nov 2018 - Dec 2018
Making a Time Study for products and entering the solutions on Excel Taking information about the products from Netsis and entering the information on Excel for Cost Analysis Making a Time Study for products and entering the solutions on Excel Taking information about the products from Netsis and entering the information on Excel for Cost Analysis
-
-
-
ALFEMO
-
Türkiye
-
Furniture and Home Furnishings Manufacturing
-
100 - 200 Employee
-
Quality Intern
-
Jun 2018 - Jul 2018
Checking quality of raw materials, semi-products and entering the quality results on SAP Making report of Corrective And Preventative Action for defective products Obtaining information about curing, corrosion& dynamic endurance test Making quality control for products on the line of packing, accessory& perforating operation Entering the results of quality control on Excel and helping to show defective products’ data on Pie Chart Taking supplier information from SAP and entering the information on Excel Attending prototype and pilot products meeting Attending Kaizen and TPM meeting Helping to prepare Management Review Reports and Presentation Having information about QDMS, Novalab, Boysweb and Portal program Calculating efficiency with Job Sampling by determining the number of operators that work on main operations and not work Making a Time Study Making a System Analysis Study (Flow Diagram, Fishbone Diagram, Problem Tree Analysis, Force-Field Analysis, FMEA, Six Thinking Hats Technique, Scenario Analysis, Scenario Diagram, Data Flow Diagram and Entity Relationship Diagram) Making a Simulation Study by using Arena program in order to prevent bottlenecks Show less
-
-
-
Aero Wind Industry
-
İzmir, Turkey
-
Production Planning Intern
-
Jun 2017 - Jul 2017
Making a Time Study Making a Flow Chart and Fishbone Diagram Interpreting Productivity by using C++ Software Program Attending education about Waste Management and SAP Fulfilling demands and minimizing costs with mathematical modelling by using Lindo program Defining normal distribution conformity of orders by using MINITAB program Making a Time Study Making a Flow Chart and Fishbone Diagram Interpreting Productivity by using C++ Software Program Attending education about Waste Management and SAP Fulfilling demands and minimizing costs with mathematical modelling by using Lindo program Defining normal distribution conformity of orders by using MINITAB program
-
-
Education
-
Celal Bayar University
Master of Science - MS, Industrial Engineering -
Celal Bayar University
Bachelor of Science - BS, Industrial Engineering
Community
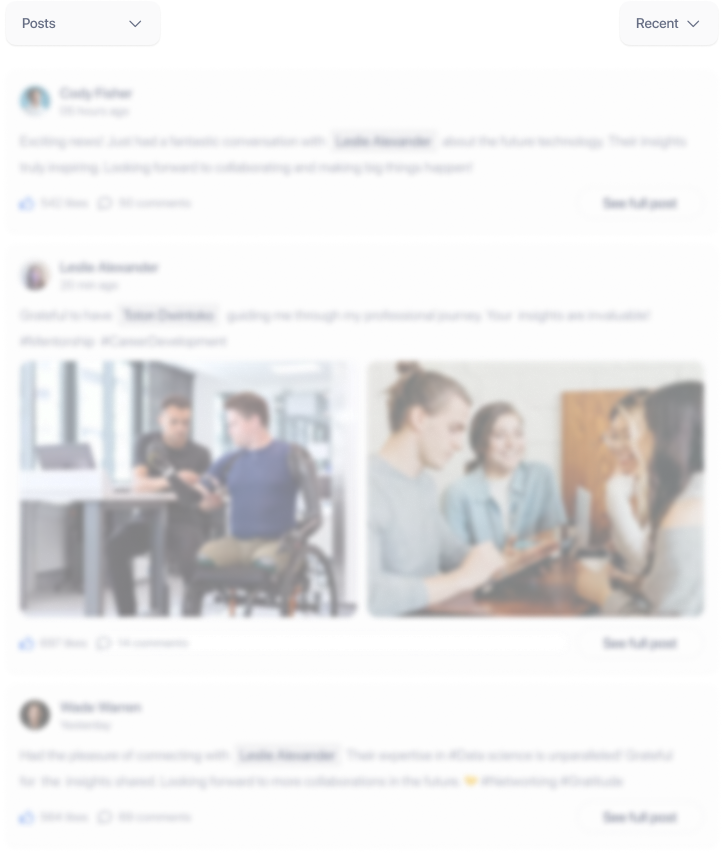