Diana Gonzalez
Quality / Safety Manager at Specialty Rolled Metals- Claim this Profile
Click to upgrade to our gold package
for the full feature experience.
-
English Native or bilingual proficiency
-
Spanish Professional working proficiency
Topline Score
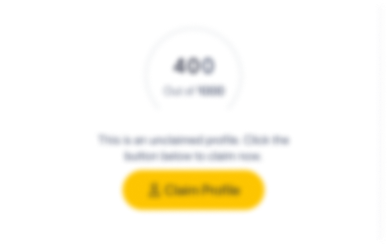
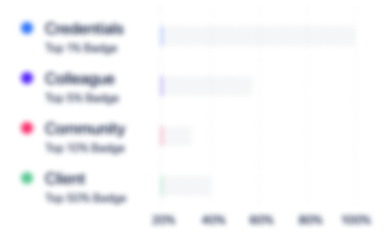
Bio


Credentials
-
EOSHA Consulting’s Train-the-Trainer certification: employee overhead crane and forklift operations
- -
OSHA 30 hour certification in General Industry
-
Experience
-
Specialty Rolled Metals (SRM)
-
United States
-
Mining
-
1 - 100 Employee
-
Quality / Safety Manager
-
Mar 2010 - Present
Quality Control • Manage, document, and implement ISO quality policies, metrics, management reviews, processes, inspection procedures, and plant operations for internal and customer audits • Execute project specifications, Return Material Authorizations (RMAs), mill claims, debits, logs, and replacements, including analyzing root causes and developing corrective and preventative action (CAPA) plans • Managed the process to certify the company for ISO/TS 16949, ISO 9001:2015, and ISO 14001:2015 certifications Safety Management • Implement and manage protocols for complying with COVID-19 guidelines and regulations according to the Illinois Department of Health and the CDC • Manage and implement safety policies, processes, and procedures, including emergency procedures and response plans • Develop and train employees on safety policies, forklifts, overhead cranes, lock-out / tag-out procedures, and machine guarding • Coordinate an annual hearing conservation program, along with a prescription safety glasses program • As lead insurance liaison, confirm adherence to self-insurance guidelines, document and communicate injury reports and claims • Manage and coordinate required third-party building inspections to comply with OSHA-mandated regulations Purchasing • Manage third-party contracts and negotiations, including maintenance products and services, leasing of forklifts, custom pallets, and sources of lumber • Oversee pricing and manage inventory on PVC, packaging supplies, customer-specific materials, and personal protective equipment (PPEs) • Demonstrate consistent cost-savings methods to stay within budget goals and maintain required inventories
-
-
-
Stainless Sales Corporation
-
Chicago, Illinois
-
Quality Assurance Manager
-
Apr 2008 - Mar 2010
• Developed and maintained quality metrics, system, process, and customer audits, corrective actions investigations • Investigated plant quality deficiencies, conducted task inspections, produced and monitored document control and quality records • Verified customer order specifications and analyzed any customer reported defects • Implemented quarterly safety meetings to review safety issues, problems, or hazards • Managed plant employees and oversaw daily workflow towards the completion of scheduled orders
-
-
-
Jones and Brown Company, Inc.
-
Addison, Illinois
-
Purchasing Manager
-
May 2007 - Feb 2008
• Researched and implemented opportunities to reduce costs and inventory investment • Negotiated with suppliers to procure quality materials within budget and time constraints • Oversaw facilities maintenance, collaborated with multiple departments to plan, direct, and control costs of structural steel material, anchors, plates, etc. to meet or be less than original budget estimations • Initiated and implemented a Material Requirements Planning (MRP) software, to produce cut lists for steel material buyout of projects and to coordinate a plant inventory control process • Measured and managed on-time supplier performance to meet all project scheduled deliveries and commitments
-
-
-
InterTech Development Company
-
Automation Machinery Manufacturing
-
1 - 100 Employee
-
Managing Buyer
-
Jul 2005 - Apr 2007
• Negotiated with vendors to secure cost-effective purchases for all types of electrical, pneumatic, and mechanical parts • Worked with a team of engineers to obtain project requirements and provide estimates • Used custom purchasing software to manage inventory, obtain quotes, and expedite orders on a daily basis • Sought and procured outside services such as plating, welding, grinding, EDM machining, and heat treating • Negotiated with vendors to secure cost-effective purchases for all types of electrical, pneumatic, and mechanical parts • Worked with a team of engineers to obtain project requirements and provide estimates • Used custom purchasing software to manage inventory, obtain quotes, and expedite orders on a daily basis • Sought and procured outside services such as plating, welding, grinding, EDM machining, and heat treating
-
-
-
Allrite Sheet Metal
-
United States
-
Mining
-
Purchasing Manager
-
May 1988 - Sep 2004
• Purchased project materials and negotiated with vendors to obtain competitive pricing • Worked with engineering and sales departments to verify customer requirements • Acquired necessary resources such as, painting, plating, anodizing, and heat treating per job finishing specifications • Was the customer’s primary point-of-contact • Documented new customer orders, expedited jobs to meet ship dates, worked with freight services to determine shipment means, and managed quality control on incoming materials • Verified customer invoicing, purchase orders through production control, and delivery receipts
-
-
Community
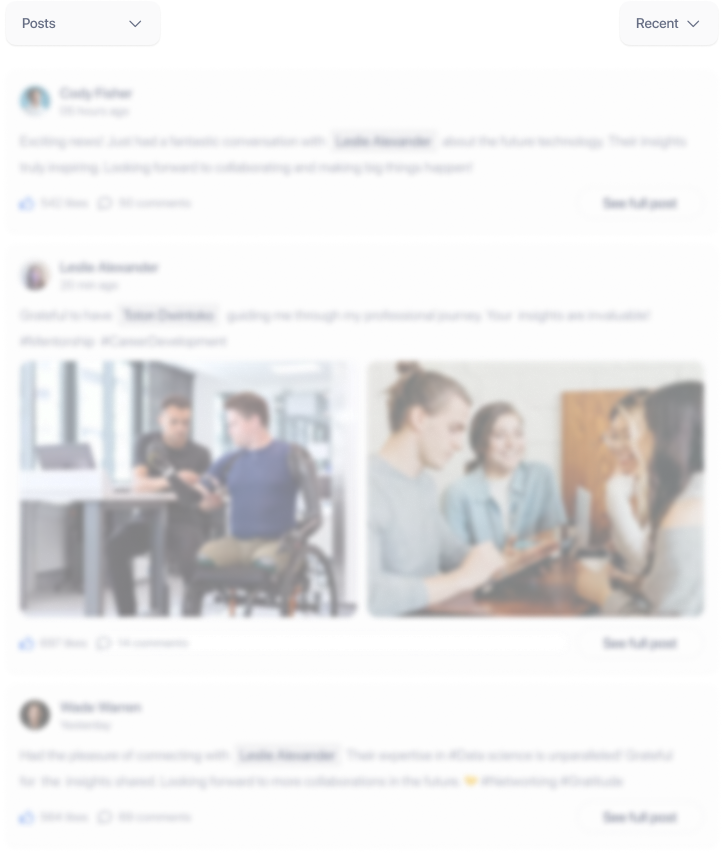