Diana Crawford
QA Management of Document Control, Change Control and Training at Kolon TissueGene, Inc.- Claim this Profile
Click to upgrade to our gold package
for the full feature experience.
Topline Score
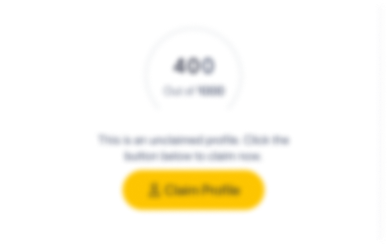
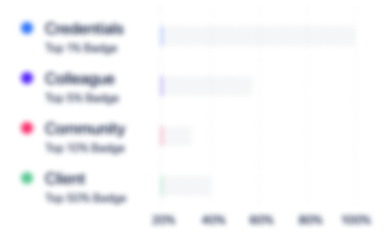
Bio

Steven Kyle Crawford
Diana is a knowledgeable and detail-oriented worker with a sharp eye for discerning issues related to the auditing process, both internal and external. She is proficient at designing plans to deal with issues and problems as well as working with colleagues to solve these issues and problems in a timely and efficient manner.

Steven Kyle Crawford
Diana is a knowledgeable and detail-oriented worker with a sharp eye for discerning issues related to the auditing process, both internal and external. She is proficient at designing plans to deal with issues and problems as well as working with colleagues to solve these issues and problems in a timely and efficient manner.

Steven Kyle Crawford
Diana is a knowledgeable and detail-oriented worker with a sharp eye for discerning issues related to the auditing process, both internal and external. She is proficient at designing plans to deal with issues and problems as well as working with colleagues to solve these issues and problems in a timely and efficient manner.

Steven Kyle Crawford
Diana is a knowledgeable and detail-oriented worker with a sharp eye for discerning issues related to the auditing process, both internal and external. She is proficient at designing plans to deal with issues and problems as well as working with colleagues to solve these issues and problems in a timely and efficient manner.

Credentials
-
Certified Lead Auditor
ASQ/Stat a MatrixSep, 2017- Oct, 2024
Experience
-
Kolon TissueGene, Inc.
-
United States
-
Biotechnology Research
-
1 - 100 Employee
-
QA Management of Document Control, Change Control and Training
-
Nov 2018 - Present
• Maintain a validated electronic document management system compliant with regulatory and quality requirements. • Perform Validations/Risk Assessment on quarterly upgrades of MasterControl, the Electronic Management Document System. • Manage Document Control support including but not limited to processing, publishing, and distributing controlled documents • Collaborate with cross functional departments to ensure timely implementation of document change requests • Ensure controlled documents are periodically reviewed for relevance and accuracy to ensure actual practices are reflected in procedures, work instructions and training materials. • Part of team that developed procedures for the records management system including secure storage, retrieval, retention and destruction • Within MasterControl, developed and designed templates for procedures, test methods, validations and various forms. • Evaluate capabilities of MasterControl and assess if improvements are necessary to maintain compliance • Participant in audits (internal and external) in order to verify that regulatory and quality requirements are met • Support establishment of departmental training matrices • Implement and maintain a training system compliant with regulatory and quality requirements. • Provide new hires an introduction to MasterControl as part of New Hire Orientation Program • Implement, maintain and support electronic Trial Master File system for Clinical Operations activities • Manage assigned duties of direct report. Show less
-
-
-
Canon BioMedical
-
United States
-
Medical Equipment Manufacturing
-
Senior QA Specialist Document and Change Control Management
-
Jul 2017 - Dec 2017
•Managed the Document and Change Control process to include working directly with authors, reviewers and approvers to facilitate document and change control workflow. •Responsible for pre-approval and final approval of change control to ensure all internal and regulatory requirements were met and supporting documentation was included. •Developed, implemented and managed a company-wide Electronic Document Management System. (EMDS). Initial responsibility was to write procedures for the electronic document management system (EDMS) that was in the process of being validated. •Served as EDMS administrator to assist end-users with system training, access, navigation and primary functions. •Assigned and monitored document numbers and reviewed documents for accuracy and completeness. •Part of the review team for all Quality Management System procedures. •Developed a training program for new hires and annual training of all employees for Good Manufacturing Practices. (GMP) •Author of document and change control process related procedures and training presentations. Show less
-
-
-
Kimberly-Clark
-
United States
-
Manufacturing
-
700 & Above Employee
-
Quality Assurance Engineer IV/Certified Lead Auditor (Consultant)
-
Jan 2016 - Nov 2016
- Responsible for implementing internal audit activities required to ensure compliance with quality management system regulations, good manufacturing practices (GMP) and ISO standards. - Presented internal audit findings to Executive Management Team and departments audited. - Worked with Team Leaders to develop corrective actions for internal audit findings. - Investigated Quality issues, determined root cause and implemented corrective actions for non-conformities and CAPA’s. - Mentored and coached manufacturing and quality personnel about the Quality Management System requirements and Good Manufacturing Practices. - Performed effectiveness checks on previous corporate audit findings, CAPA’s and non-conformities. - Created procedures, work instructions, quality management system records as required. - Implemented a compliant NIST calibration program. - Developed templates/co-authored Validation Protocols. - Final QA reviewer for validation protocols. Show less
-
-
-
Stryker, Neurovascular
-
Medical Equipment Manufacturing
-
1 - 100 Employee
-
Supplier Quality Engineer (Contractor)
-
Apr 2015 - Aug 2015
-Provide support for all Supplier Quality related activities which includes assist in Receiving Inspection operations (First Article), worked with suppliers to complete supplier surveys/questionnaires, and work with suppliers for non-conformities, corrective actions, (SCAR's) and process improvements as required. -Obtain and submit information from suppliers for REACH and RoHS to meet regulatory requirements for product submissions. -Attend weekly Supplier Quality meetings and provide input and approval for supplier audit pre-planning, audit reports and audit findings. -Part of global team for reclassification of suppliers (over 300 suppliers) used in North America for NV Stryker. Show less
-
-
-
Edwards Lifesciences
-
United States
-
Medical Equipment Manufacturing
-
700 & Above Employee
-
Supplier Quality Assurance-Consultant
-
Sep 2014 - Mar 2015
-Remediation of quality issues for Supplier Quality. -Review, revise and approve supplier audit reports to address a regulatory commitment. -Mentoring and coaching the current Supplier Quality Engineer’s on various best practices for auditing suppliers, and help with audit pre-planning activities for Suppliers. -Provide SQE’s follow up questions for performing onsite audits to provide a complete assessment of the supplier’s quality management system. -Developed supplier audit report templates and work instructions for various types of supplier audits. (Sterilization, Contract Laboratory, components, etc.) -Review finalized Supplier Corrective Actions (SCAR’s) for compliance and effectiveness checks. -Provided information and guidance, including solutions, for areas of supplier quality that could be improved. Show less
-
-
-
-
Senior QA Engineer -CAPA (Contractor)
-
Jan 2014 - Aug 2014
‒Perform retrospective assessments of previous CAPA’s, complaints, NCR’s and other Quality System records to ensure they complied with 21 CFR 820, ISO 13485 and Medical Device Directives (MDD) requirements. ‒Interact with Engineers, Operation personnel and other departments in order to write the investigations, root causes, risk assessment, corrective actions and effectiveness checks for current CAPA’s. ‒Revise quality system procedures to align with Zimmer Corporate. ‒Perform Supplier Quality Audits, enhance procedure and process. ‒Member of the Remediation Team to improve compliance throughout Synvasive since being purchased by Zimmer. Show less
-
-
-
-
Quality Engineer-Product Complaints Department (Contractor-US Tech)
-
May 2013 - Nov 2013
‒QA review of complaints to ensure appropriate investigation and risk assessment has been completed with supporting documentation in current complaint database. (Siebel System) ‒Ensure that complaints are in compliance with all applicable Corporate and Divisional policies/procedures, cGMP, FDA, EMEA, Health Canada, Japan and other country regulatory requirements. ‒Interact with Quality Engineers, Complaint Investigators and other departments for clarifications if needed. ‒Member of PCD Team to improve consistency and compliance within the complaints group. ‒Review and red-line complaint department procedures. ‒Provide input and review for responses to third party audit findings. ‒Provided input for root cause analysis & problem solving support for CAPA, NCMRs and customer complaints for timely closure. Show less
-
-
-
Abbott Medical Optics
-
Medical Equipment Manufacturing
-
QA Product Safety Analyst-Complaints (Contractor-Real Staffing)
-
Nov 2012 - Feb 2013
‒Responsible for final review/closure of complaints in validated database. (CATS Web). ‒Ensure that complaints meet the requirements with all applicable Corporate and Divisional policies/procedures, cGMP, FDA, EAME, Health Canada, Japan and other country regulatory requirements. ‒Follow up with manufacturing sites, engineers, and other complaint analysts for any discrepancies or corrections that are required to support the closing of the complaints. ‒Provided root cause analysis & problem solving support for CAPA, NCMRs and customer complaints for timely closure. Show less
-
-
-
Guthy-Renker
-
United States
-
Technology, Information and Internet
-
Quality Assurance Supplier Quality (Consultant through Oxford)
-
Mar 2012 - Oct 2012
‒Maintain and improve supplier quality program—identifying and implementing key program enhancements. ‒Rewrote supplier quality procedure to provide standard process for vendor classification and qualification audits. Develop and maintain master QA supplier list. Provide regulatory compliance guidance. ‒Collaborate with newly established supply chain group to evaluate and develop relevant criteria for potential vendors. Recommend vendor approval status to QA Management. ‒Develop questionnaires for various types of vendors/suppliers. (Contract manufacturer’s, API, components, labeling and packaging vendors) ‒Ensure that all new and current vendors are qualified according to the Supplier Quality procedure. ‒Work with supplier on product issues and assist in Supplier Corrective Action process. ‒Develop and schedule Supplier Quality Audit Schedule to meet company requirements. ‒Perform Supplier cGMP Audits as required. ‒QA Review of Change Control documents and engineering change control to ensure regulatory/compliance requirements are met. ‒Provide compliance and regulatory guidance as required for stability, validations, regulatory label review and SOP’s. Show less
-
-
-
Irvine Pharmaceutical Services
-
United States
-
Pharmaceuticals
-
1 - 100 Employee
-
Senior Compliance Officer/Document Control and Training Manager
-
Sep 2011 - Mar 2012
‒Lead Regulatory Agency Inspections, Client and Supplier Audits ‒Initially hired as Sr. Compliance Officer, within two months promoted to Training and Document Control Manager. ‒Implemented Corrective and Preventative Action (CAPA) program and evaluated Supplier Quality Corrective Actions. (SCAR) ‒Review and provide input for non-conformities and deviations insuring that root cause, corrective and preventative actions are addressed appropriately. ‒Under appropriate quality standards, completed the NCMR Non-Conforming Material Reports to report on defective material for vendors and customers. ‒Final QA review and approval for validation protocols that included the electronic Document Management System, (Master Control), temperature controlled equipment, water system, facility utilities and laboratory equipment. ‒Maintain and present Quality Metrics for monthly Management Review Meetings. ‒Develop procedures and work instructions for Compliance activities such as Change Control, Out of Specifications, QA review of protocols/validations. ‒Provide cGMP training as required, enhanced training program for new hires Show less
-
-
-
-
Regulatory Compliance Recall Coordinator (Consultant-Validant)
-
Feb 2011 - Jul 2011
‒Liaison for Regulatory/Compliance for the OTC Recall process team. ‒Submit documentation to FDA for new recalls, compile the data for Attachment B and send the 30 Day Status Reports for 25+ recalls. ‒Review and provide input for Field Alerts root cause, corrective and preventative actions. ‒Develop procedures and work instructions for managing the recall process. ‒Direct recall activities with the 3rd Party Reverse Distribution Company. ‒Handle inquiries related to regulatory filings for Recall activities both internally and externally. ‒Provide recall metrics monthly and quarterly to appropriate departments. Show less
-
-
-
QIAGEN
-
Netherlands
-
Biotechnology Research
-
700 & Above Employee
-
Lead Auditor-Quality Systems Specialist III Compliance
-
Feb 2007 - Nov 2010
‒Responsible for implementing audit activities required for local, state, federal and international quality standards to ensure compliance with all quality system regulations and standards. Assist the Director of QA Compliance for third party audits and management review activities. ‒Established and maintained the Internal Audit Program in Gaithersburg in accordance with 21 CFR 820.22, ISO 13485:2003, 8.2.2 and ISO 9001:2008, 8.2.2. ‒Key participant in third party audits for FDA inspections and ISO 13485/ISO 9001 Certification and Surveillance Audits. ‒Under quality standards and requirements, final QA Approver for NCMR Non-Conforming Material Report,/Deviations, CAPA’s to address audit observations as required. ‒Managed the Corrective Actions and Preventative Actions (CAPA) and Change Control associated with Internal and third party Audits. ‒Developed the Internal Audit Program to include the Germantown facility after merger with QIAGEN. ‒Performed Gap Analysis for Germantown facility to 21 CFR 820 in preparation for manufacturing of Class I Medical Devices. ‒Successful FDA inspection with no findings and recertification for ISO 13485/ISO 9001 for both facilities. ‒Part of Corrective Action Team to improve the labeling procedures and process. ‒Part of team that developed Design Control Process procedures and documentation to support new product development. ‒QA Reviewer and auditor of Design History Files (DHF) for two projects. ‒QA review and approve validation protocols for electronic Document Management System (Master Control®). ‒Company resource for QA Management and Regulatory Affairs for current and revised regulations and standards that are applicable for Class I and Class III Medical Devices. ‒Responsible for conducting New Hire and Annual cGMP/Regulatory Training for all employees. ‒Team Leader for improving the Training Procedure and conducting the training for roll out of revised training process to address audit findings. Show less
-
-
-
Celsion Corporation
-
Biotechnology Research
-
1 - 100 Employee
-
Senior Quality Assurance Systems Specialist (Consultant)
-
Jan 2006 - Jan 2007
‒Reviewed and enhanced standard operating procedures to be in line with the Quality System Regulation. ‒Established and maintained the Corrective and Preventative Action. ‒Addressed all NCMRs (Non-conformance material requisitions) ‒Final QA Reviewer for Design Control changes for product manufactured at contract manufacturers. ‒Assisted in the development of revised Complaint handling process. ‒Handled QA responsibility for review of incoming complaints for possible reportable incidents. ‒Coordinated recall activities with subcontractors and prepared updates for the FDA. ‒Audited subcontractors and monitored validation work required for supplement to PMA. ‒Advised management and staff of Quality/Compliance requirements for change control and qualification/validation of processes. Show less
-
-
-
-
Quality Assurance Systems Specialist
-
2003 - 2006
Responsible for reviewing all batch records and associated data such as deviations, failure investigations, and OOS (out of specification) to release products manufactured by Virus Production (cGMP), Contract Manufacturing (cGMP), Virus Isolation and Testing (GLP), and Cell Biology. ‒Established NIST traceable calibration program. ‒Implemented and maintained Corrective and Preventative Action (CAPA) program and Change Control Process for documents and engineering changes. Provided quarterly trending to Executive Management. ‒QE representative of Change Control Board. ‒Prepared annual report for FDA submission. ‒Provided input, review and final QA approval of validation protocols, validation reports and engineering studies. ‒Lead QA representative for Food and Drug Administration (FDA), client and vendor audits. ‒Developed and maintained compliant calibration program for all equipment that supported cGMP/GLP manufacturing and In-Process/Quality Control Testing. ‒Enhanced batch records, standard operating procedures, and Quality Control test procedures for cGMP compliance. ‒Established Engineering/Document Change Control/Design Control Process to capture changes made to FDA approved intermediate product. ‒Reviewed testing data and issue Certificates of Analysis for stability samples for various clients. ‒Interacted with Manufacturing, Vendors, Clients, Research and Development, and Regulatory to determine product impact/quality and recommend disposition. Show less
-
-
-
-
Quality Control Chemist (Lab Support)
-
2000 - 2001
-
-
-
Amgen
-
United States
-
Biotechnology Research
-
700 & Above Employee
-
Quality Assurance Data Analyst II (Lab Support)
-
1999 - 2000
-
-
Education
-
College of the United States Air Force
Bachelor of Science, Biochemistry -
United States Air Force
Associate of Science, Clinical Medical Technologist
Community
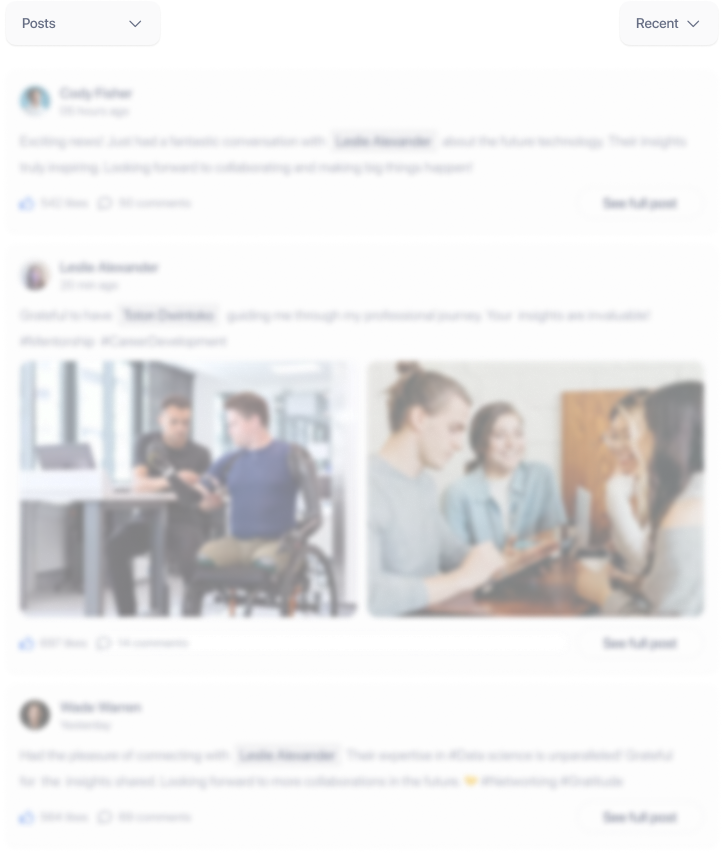