dhiren madlani
Managing Director at Flaretot Limited- Claim this Profile
Click to upgrade to our gold package
for the full feature experience.
Topline Score
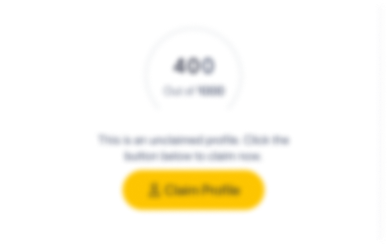
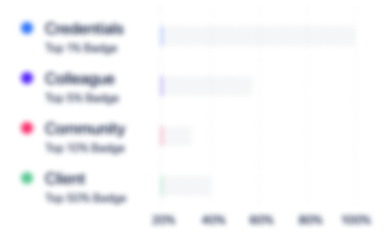
Bio

Frederik Rijkens
Dhiren was the Engineering manager for the Usan deepwater development. He contributed to the creation of value by his communication and leadership skills for the project's engineering work, with our contractor, and for the creation of coherent engineering&design and specifications for the packages to be contracted-out. This included FPSO, SURF, trees&control system and export buoy

Frederik Rijkens
Dhiren was the Engineering manager for the Usan deepwater development. He contributed to the creation of value by his communication and leadership skills for the project's engineering work, with our contractor, and for the creation of coherent engineering&design and specifications for the packages to be contracted-out. This included FPSO, SURF, trees&control system and export buoy

Frederik Rijkens
Dhiren was the Engineering manager for the Usan deepwater development. He contributed to the creation of value by his communication and leadership skills for the project's engineering work, with our contractor, and for the creation of coherent engineering&design and specifications for the packages to be contracted-out. This included FPSO, SURF, trees&control system and export buoy

Frederik Rijkens
Dhiren was the Engineering manager for the Usan deepwater development. He contributed to the creation of value by his communication and leadership skills for the project's engineering work, with our contractor, and for the creation of coherent engineering&design and specifications for the packages to be contracted-out. This included FPSO, SURF, trees&control system and export buoy
0
/5.0 / Based on 0 ratingsFilter reviews by:
Experience
-
Flaretot Limited
-
United Kingdom
-
Oil and Gas
-
1 - 100 Employee
-
Managing Director
-
Jan 2011 - Present
Part of a team of engineers with a total of over 150 years of experience in flare system design & operation, to develop and compile a integrated flare software solution for all aspects of flare system for Flaretot Limited , a leading supplier of technical software and in providing consulting to the oil & gas industry. Part of a team of engineers with a total of over 150 years of experience in flare system design & operation, to develop and compile a integrated flare software solution for all aspects of flare system for Flaretot Limited , a leading supplier of technical software and in providing consulting to the oil & gas industry.
-
-
-
Total E&P Nigeria Limited
-
100 - 200 Employee
-
Engineering Manager
-
Jun 2005 - Jan 2011
USAN Deepwater development Project, Nigeria Basic Engineering Phase: As part of PMT, joined the project at the start of Basic engineering and was in charge of overall project as client representative with the objective of developing the robust basic Engineering design for SPS, UFR & FPSO. Five ITT packages were developed during Basic Engineering to be sent to selected bidders. I was responsible for the flow assurance work for the project and to confirm the preservation strategy of the subsea flow lines. I was responsible for managing the budget and multi discipline engineering team during the basic engineering phase in the Contractor premises. As part of the project local content requirement, I was also responsible for managing 50,000 engineering man-hours in Nigeria. I was responsible for updating and maintaining SOR for the Project. Tender evaluation & Project sanction Phase: De-bottlenecking study for the project to increase the processing capacity from 160000 BOPD to 180000 BOPD, Participated in the tender evaluation activities, tender bulletins, responding to bidder’s queries, Evaluating and finalising LLI packages, I was responsible for preparing all the greenhouse emission figures for the project and documentation for COMITE RISQUES & COMEX for Project sanction. Interviewing and manning up engineering team for the project. Detail design Phase USAN FPSO; I was responsible for managing the multi discipline engineering teams located in three locations during Detail Design phase in the contractor premises in Lagos, Paris and Korea. Construction & Commissioning Phase: Responsible for managing the multi discipline engineering teams located in Ulsan, Korea. I was responsible for organising, coordinating and closing PTR3 and 4 for the Project,
-
-
-
Elf Petroleum Iran
-
Consumer Services
-
Engineering Manager
-
2002 - 2005
Engineering Manager Dorood Project Kharg Island Iran As part of Project Management Team, Joined the project at the tender evaluation stage of main EPCC contract as engineering manager and I was responsible for managing multi discipline engineering team of 15 Engineers within the PMT. I was responsible for all Detail engineering and technical aspect of EPCC Contract within the CONTRACTOR premises in UAE. Project consisted of installing new processing facility within the existing facilities on Kharg Island in Iran. The project consisted of processing 80,000 bbl/d of sour crude, Sour Gas injection (with up to 13% H2S) at 410 barg, Sea Water injection, interfiled pipelines, New flare facilities and Wellheads sites. I managed all the engineering of the project from Detail Engineering, Procurement, to assisting Construction, Commissioning and start-up of the new facilities.
-
-
-
Total E&P
-
France
-
Business Consulting and Services
-
Engineering Manager
-
2001 - 2002
-
-
-
TotalFinaElf
-
France
-
Wholesale
-
Lead Process Engineer Elgin & Franklin Project
-
1993 - 2001
Lead Process Engineer /Process Expert Elgin & Franklin Development Project UK (650 MMSCFD Gas/Condensate fileds) As a member of the PMT (Project Management Team) I was responsible for Process design for Elgin and Franklin Fields. Pre-Project Phase: I was involved from the beginning of the project as a client representative during screening and feasibility studies. These fields are most complex High Pressure (1100 bar), High Temperature (200°C) Gas Condensate fields in the world requiring innovative technology and approach to make the project viable. Basic Engineering: I was responsible for process design and Equipment layout during FEED phase; It was design competition between two concept TPG 500 Vs Conventional jacket + topsides Detail Design phase: As lead process engineer within the Alliance contract for TPG 500 during detail design. Construction & Commissioning Phase at site: As Start-up and Operation engineer providing general support to construction and commissioning teams. Offshore Start-Up: As Start-up and operation engineer, I was responsible for defining the start up phases and preparing the start-up planning and flare consent application and presenting it to Department of Energy. I was responsible for de-watering and commissioning of the 24” liquid and 34” Gas export pipelines and Start-up of utilities and process system facilities offshore. Seeing the project through all stages was a unique and rewarding experience.
-
-
-
Oxy
-
United States
-
Design Services
-
Chief Process Engineer
-
1988 - 1993
As a member of the PMT I was responsible for implementation & control of the process and utility systems design for Piper 'B', Saltire 'A' and Chanter fields. Feasibility and Conceptual Design Phase:- Evaluated different process and utility options and estimated the weight for the topside facilities. Technically responsible for final process and utility options selection for detail design. I was responsible for developing scope of work and the Design Basis Documents for next phase of the project. Detail & Post Detail Design Phase:- As lead process engineer responsible for supervising Engineering Contractors' work. At peak, there were 49 Process Engineers working on the project. Review and approve all relevant Process documents e.g. P & IDs, process data sheets, C&E charts, process philosophies, design reports etc. I was responsible for controlling and approving manning levels for the Project. Witnessed class III and I tests for the compressors. During the project I was responsible for technical audits for process, compression, flare, hot oil and study state and transient pipeline simulations. Hookup, Commissioning and Start-up Phase: - Responsible for supervising the integrated process team for this phase. Duties include reviewing and collating statutory operations, start-up, and commissioning and operations manuals for both platforms. I was Responsible for defining the start up phases and sequence and preparing the start-up flare consent application and presenting it to Department of energy.Participated in HAZOP, HAZID studies and assisted in preparing Safety Case for the Piper B field. General Project Management support, included preparing, reports, analysing problems and providing recommendations. I was responsible for developing FDS (functional design specification) for the training simulator and also for developing FAT (factory acceptance test) procedure for the simulator and testing it.
-
-
-
offshore Design Services
-
United States
-
Lead Process Engineer
-
Mar 1986 - Jul 1988
Lead Process Engineer Mossel Bay Project - MOSSGAS South Africa Worked as Lead Process Engineer and was responsible for detail design phase, supervising a team of 15 Process Engineers in Cape Town South Africa. This included overall technical responsibility for process design for Topsides and two pipelines and Landfall station. Responsible for checking and approving all the process related documents on the project. Lead Process Engineer Mossel Bay Project - MOSSGAS South Africa Worked as Lead Process Engineer and was responsible for detail design phase, supervising a team of 15 Process Engineers in Cape Town South Africa. This included overall technical responsibility for process design for Topsides and two pipelines and Landfall station. Responsible for checking and approving all the process related documents on the project.
-
-
-
Brown & Root
-
Oil and Gas
-
100 - 200 Employee
-
Lead Process Engineer
-
1984 - 1988
Lead Process Engineer Shell Exploration - Sole Pit Project. Lead Process Engineer responsible for the Process & utility systems for the complex. Lead Process Engineer Phillips Petroleum - Audrey Field Development Lead Process Engineer responsible for detail design of the Wellhead Platform for the Field. Lead Process Engineer Conoco, SBGD (Southern Basin Gas Development) Project. 1200MMSCFD Gas Complex (The project consisted of 6 Wellheads, 1 Production & 1 Accommodation platforms). Lead Process Engineer responsible for supervising a team of 14 Process Engineers. This includes overall technical responsibility for Process design of whole project. Responsible for approving all documents related to Process design e.g. P & IDs, PDS, C & E Charts, Estimating and controlling the process man-hours and manning levels for the project. Conoco, SBGD Project.(Compression Platform). Lead Process Engineer responsible for conceptual design work which involved preparing Design Basis Which included PFD's, P & IDs, compressor control and shutdown philosophy, PDS for compressors and coolers, etc. Carried out numerous process studies, e.g. compressor cooling system selection, compressor configuration studies etc. Marathon, Brae "B" Project. Developed design procedure for calculating thermal effects on structure steel from the flare radiation. Computer program was developed to carry out the design.
-
-
-
-
Principal Process Engineer
-
Aug 1979 - Apr 1984
British Gas Morecombe Bay Gas Field. (Production & Accommodation Platforms) Worked as deputy Lead Engineer responsible for supervising ten Process Engineers. This included overall technical responsibility for flare and vent system, pig launcher/receivers, Pipe type slug catcher, gas scrubbers, TEG dehydration, re-injection/export compressors, hot oil and waste heat recovery system, cooling medium and sea water system, main and standby power generation, etc. Responsible for checking & approving all the P & IDs, PDS's for equipment and instruments, C&E charts as per API 14C etc. I ws responsible for checking process design calculation for blowdown and low temperature etc. Responsible for carrying out operability reviews for different process systems. Marathon Brae "B" Project.(Gas Dehydration & Sweetening Facility). Worked as Principal Process Engineer responsible for evaluating different options for gas sweetening and dehydration, which involved evaluating different gas sweetening and dehydration processes, Marathon Brae "A" Project (Production Platform). Worked with Systems Control Department where I responsible for developing logic for control systems for compressors, Main Pumps, Selexol and Refrigeration system. All the details for start-up and shutdown etc. were considered while developing the logic. Supervised the writing of operating and start up manuals for the complex. NCB - Pilot Plants for Coal Liquefaction Assisted in process design for two pilot plants (Liquid Solvent Extraction and Supercritical Gas Extraction) which involved: preparing overall mass balances for both processes; developed a program to investigate different mode of operation i.e. solvent to coal ratios. I was responsible for fractionation and storage sections for both processes. Participated HAZOP studies for above sections.
-
-
-
-
Principal Process Enginerr
-
Jul 1977 - Sep 1983
Senior Process Engineer Mobil - Statfjord 'B' Development Project – (Brown &Root/NPC Joint venture Norway) Responsible for detail design of flare and vent system for the platform, which involved: Developed computer programs for vessel depressurising, Flare network, and flare radiation studies. Assisted in preparing UFDs, P &ID's for utility systems for the platform. Nigg Oil Terminal Project (BNOC) Heavy Oil Project with API of 22 to 25. Assisted in preparing Design Basis and SOW of the facilities which also involved evaluating different process schemes and feasibility studies. BNOC (Later BP) - Beatrice Field Development - Platform A I was Responsible for design of the Utility systems for the platform. Responsible for preparing Process design documentation like UFDs, P&ID's, Equipment Data Sheets, C&E Charts etc. Crude was very heavy and Waxy and required Heater/Treater design to maintain reasonable viscosity for transportation.
-
-
-
BP Chemicals
-
United Kingdom
-
Business Consulting and Services
-
Graduate Trainee Engineer
-
1974 - 1975
Worked as Graduate engineer on Ethylene plant and Offsite Facilities for the Petrochemical complex including flare systems and Work involved Troubleshooting, commissioning work on compressors, pumps etc on several Plants. Worked as Graduate engineer on Ethylene plant and Offsite Facilities for the Petrochemical complex including flare systems and Work involved Troubleshooting, commissioning work on compressors, pumps etc on several Plants.
-
-
Community
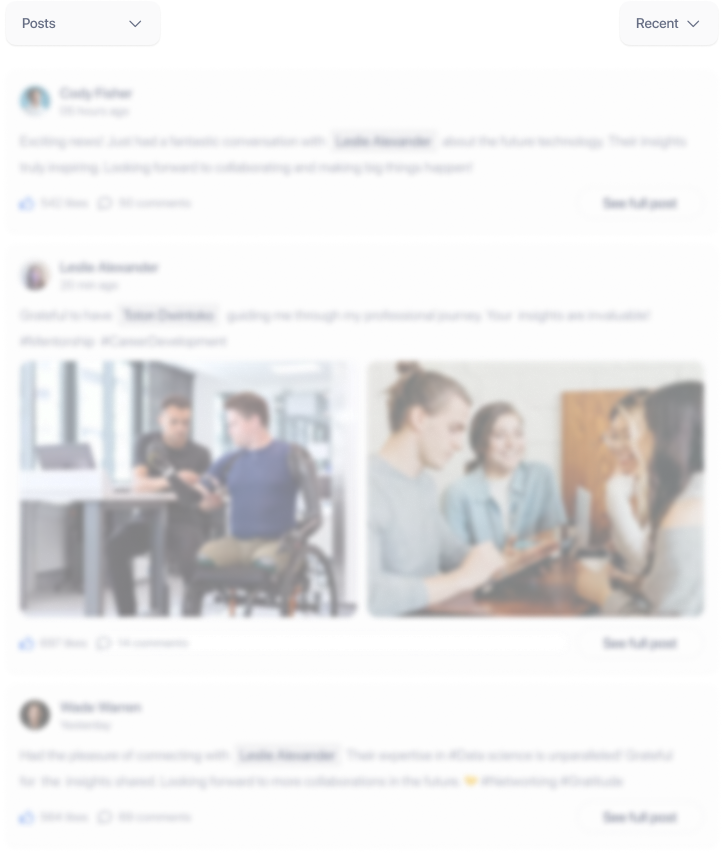