Devika Saraf
Quality Manager at WIK Group- Claim this Profile
Click to upgrade to our gold package
for the full feature experience.
-
English Full professional proficiency
-
German Professional working proficiency
-
Kannada Full professional proficiency
-
Hindi Professional working proficiency
Topline Score
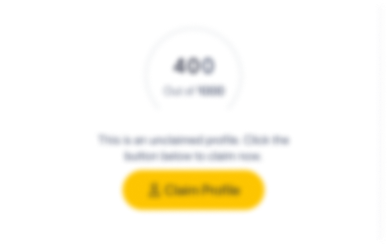
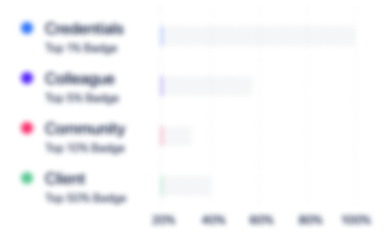
Bio


Experience
-
WIK Group
-
Hong Kong
-
Appliances, Electrical, and Electronics Manufacturing
-
100 - 200 Employee
-
Quality Manager
-
May 2020 - Present
-
-
-
Woodward, Inc.
-
United States
-
Aviation and Aerospace Component Manufacturing
-
700 & Above Employee
-
Customer Quality Engineer
-
Mar 2016 - Feb 2020
➢ Process Adherence & Improvements: • Performed Root Cause Analysis (RCA) and resolved issues utilizing Six Sigma methodology and as per Woodward Quality Management processes. • Monitored and achieved improvements in customer quality metrics. • Introduced and implemented APQP in Woodward RPS business. • Monitored and reported customer score cards on monthly basis. • Participated daily Tier-2 Stand-up meetings to resolve daily issues. • Represented quality in FMEA cross functional meeting. • Preparing Flow Chart for the Product development and Manufacturing process. • Created and updated the quality documents in WPDS (Woodward Documentation System) as per ISO 9001 • Training Woodward employees and suppliers on APQP, FMEA. • Presented APQP status and Quality issues in project Gate meetings. • Monitored and tracked customer quality data. Was responsible for raising tickets for Customer complaints in Woodward system, also to monitor and track the tickets and to send back the 8D reports to customer. • Actively participated in Corrective Action Committee (CAC) meetings to raise, discuss and to resolve critical complaints (internal/supplier/customer). ➢ Customer Focus: • Interacted directly with customer to fulfill APQP requirements and worked with internal teams to meet quality requirements such as FMEA, Master Product Plan/ Quality Assurance Plan, Product Quality Plan, Product Part Approval Process, 8D Report etc. • Responsible for internal and customer APQP for RPS projects. ➢ Audits: • Leads and follows up on internal audits and customer quality audits, • Reviewing report reports and raising appropriate actions. Show less
-
-
-
GE
-
United States
-
Industrial Machinery Manufacturing
-
700 & Above Employee
-
Quality Engineer
-
Oct 2009 - May 2014
Ø Process Adherence & Improvements: · Conducting Failure Mode Effect Analysis (FMEA), G8D reports, Corrective Actions & Preventive Actions (CAPA) using Quality Tools. · Preparing Standard Operating Procedure (SOP), work instructions, process flow chart & skill matrix for technicians. · Preparation of control plans and Quality Assurance Plans. · Analyzing the defects and providing the feasible solution using six sigma tools. · Worked on reducing the staff visit of suppliers by planning the work well and driving it in-house at GE Intelligent Platform, Bangalore, India. Ø Audits & Supplier Improvement: · Conducting the internal & supplier audits. · Work on improvement projects using Six Sigma tools. · To conduct the workout for suppliers & cross functional team. · Monitor and improve vendor quality Ø Customer Focus: · Handle customer inspection and obtain dispatch clearance for LV switchgears. · Co-ordinate with manufacturing and design team during internal & customer inspection Ø Testing: · Develop and test software, setting program in numerical relays. · Involved in conducting endurance test, IP & Temperature rise test. · Conducting the tests for LV switchgears. · Lead the team in problem solving using various quality tools for Quality improvement projects. . Knowledge of BOM, Electrical circuits, Single line diagrams, Electrical components. . Testing of Electrical components, Spares Inspection as per ISO. Show less
-
-
Education
-
Visvesvaraya Technological University
BE, Electrical & Electronics
Community
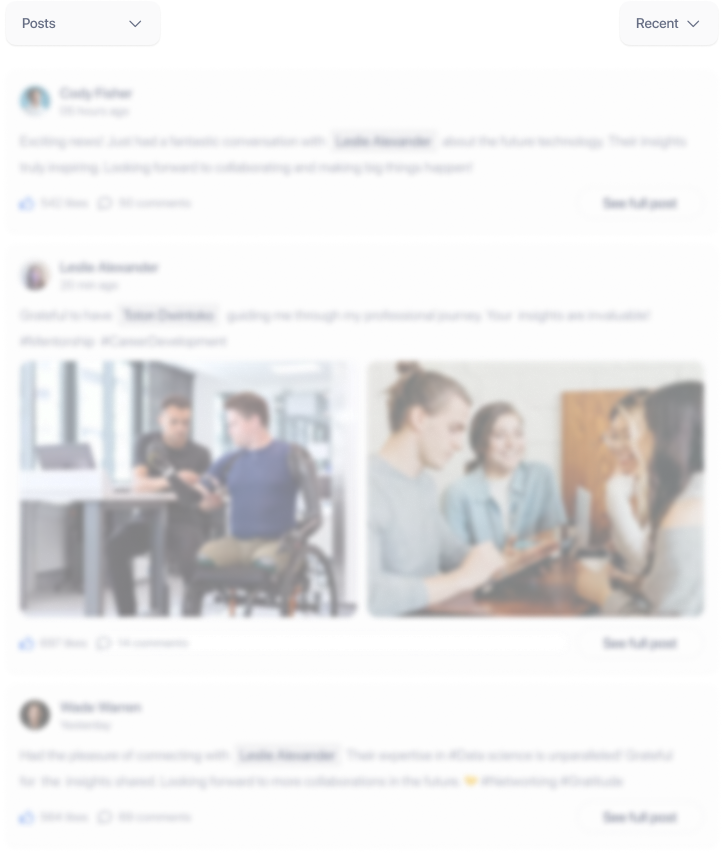