Denise Czarnecki
Quality Manager at Interstate Connecting Components (ICC), Div. of Heilind Mil-Aero- Claim this Profile
Click to upgrade to our gold package
for the full feature experience.
Topline Score
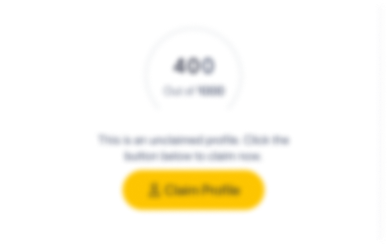
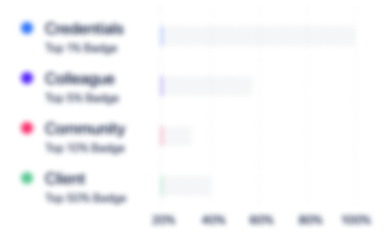
Bio


Experience
-
-
Quality Manager
-
Jul 2019 - Present
-
-
Quality Supervisor
-
Nov 2018 - Jun 2019
• Manage the Quality Management System (QMS), maintain the QMS compliance with AS9100D.• Serve as Management Representative to interface with the AS9100 registrar, including preparation for registration and surveillance audits.• Maintain and improve all QMS-related documentation, including the Quality Manual and related procedures, work instructions, workplace visuals and forms, external documentation and specifications, and training records, in accordance with AS9100 document and record control standards.• Maintain, disseminate, and improve all performance metrics for quality-related processes and, with the management team, establish and maintain key process indicators (KPI’s) and quality objectives, review trends, and establish quality plans for continuous improvement.• Manage the QMS corrective action process: recommend need for corrective action, review and assign corrective action, review all steps (interim action, root cause analysis, corrective action, implementation, verification, and approval) and maintain Corrective Action database.• Insure timely response to customer cases and RMA requests, and maintain applicable elements of the Customer Case database.• Identify technical and process risks, and ensure preventive actions and improvement plans are put into place as required.• Oversee in-process, final, and heightened inspection at all stages of quality-related processes.• Oversee the management and disposition of non-conforming product at all stages of quality-related processes.• Manage the QMS internal audit process: maintain and improve audit tools and train audit team.• Oversee the verification and validation of all quality-related processes and equipment.• Manage the quality equipment calibration process.• Train all staff in the relevant aspects of the QMS.• With the management team, drive process Kaizens in all areas of the company, pursue continuous improvement through training and process improvement.
-
-
Quality Coordinator
-
May 2016 - Nov 2018
Coordinates and supports quality assurance processes, initiatives, continuous improvement and customer fulfillment. Assist operations and quality management to ensure process control and product conformity is satisfied in accordance with established procedures and policies. *Coordinate and conduct Internal Audits for an AS9100/ISO 9001 certified Quality System*Oversee Internal and External Corrective Action Program*Compile and report monthly key process measures*Maintain calibration and preventive maintenance programs*Perform inspections of received, in-process, and finished products to meet quality specifications and standardsAccomplishments: • Keystone Alliance for Performance Excellence (KAPE) – Baldrige Criteria Examiner 2017
-
-
-
-
Project Manager: ISO 17025 Implementation
-
Jul 2015 - Apr 2016
• Evaluated current Quality Management System’s processes and procedures and performed gap analysis to determine elements missing to meet requirements of ISO 17025: 2005 • Facilitated work-out sessions to develop new Mission, Vision, and Core Value statements. • Developed action plans, trained personnel on standard, and coordinated sessions to create new and enhance existing processes. Documented company’s QMS with process maps and procedures as necessary • Conducted training of personnel at four site locations on Standard requirements and new procedures • Assisted in selecting a Registrar and acted as liaison to coordinate and schedule required proficiency testing and registration audits. Accomplishments: • Keystone Alliance for Performance Excellence (KAPE) – Baldrige Criteria Examiner 2016
-
-
-
-
Business Excellence Coordinator
-
Jan 2012 - Jun 2015
• Business Excellence Team Lead – Managed multi-functional, interdisciplinary team in identifying, developing, and deploying process improvement opportunities throughout the company, aligned to company goals and objectives, based on the Baldrige Framework• Team Coordinator SAP/Master Data Specialist – PDM team lead for several SAP site implementations; coordinated workload of department for engineering changes and special product requests; administered PDM helpdesk, troubleshooting system errors and requests• Company Representative to Registrar for ISO 9001 - Consolidated multiple quality programs for ISO 9001:2008, ISO 17025, and ISO 14001 into one integrated Management System allowing for easier maintenance of audit requirements and document control• Lead Auditor for ISO 9001 - Developed interactive system for identifying, scheduling and tracking Internal Process Audits for multiple production locations• Metrics/Management Review – Compiled and presented company data on Delivery Performance, Vendor/Customer Complaints, Engineering Changes, and status of Quality Management System• SharePoint Portal Administrator – Upgraded and programmed several antiquated systems into cohesive, interactive databases for recording, communicating and analyzing sales activities, complaints, audit plans, and document management; managed and maintained site for internal communicationsAccomplishments: • Keystone Alliance for Performance Excellence (KAPE) – Baldrige Criteria Examiner 2012, 2015• Process Audit Training, April 2014
-
-
Quality Assurance Administrator/SAP PDM Administrator
-
May 2004 - Dec 2011
• Baldrige Application team – Project lead, co-authored 3 Malcolm Baldrige National Quality Award applications, organized teams, compiled data and benchmarking figures, prepared senior leadership team and multiple facilities for 2 site visits, resulting in 2 Mastery Awards issued by KAPE • SAP PDM - Team member for implementation of SAP ERP system; principal Master Data administrator responsible for product and engineer change requests, BOM adjustments and labor routings• CPAR/DMR Administrator - Compiled and recorded metrics for Corrective and Preventive Actions and Discrepant Materials using an 8D format for Root Cause and Corrective Action• Document Control Coordinator – Wrote, updated, and maintained procedures, work instructions and distributions of controlled documents at multiple production and office locations• Internal Audit Coordinator- Developed audit schedule, conducted internal audits on production lines and administrative areas, wrote and responded to non-conformance reports• Kronos Time and Attendance Administrator – Primary support for plants, maintained installation of patches, developed and trained users on Software/ Hardware, liaison to Kronos tech supportAccomplishments: • Keystone Alliance for Performance Excellence (KAPE) – Baldrige Criteria Examiner 2010• ISO 9001 Auditor Training, 2005
-
-
-
-
Administrative Assistant
-
Oct 1996 - May 2004
• ISO 9001 Plant Representative; implemented program and registered the facility within 10 months, including writing all procedures, training plant personnel, heading internal audit team and maintaining document control • Developed system to track imported raw material freight logistics, resulting in shorter turn-around time and reduced demurrage fees. • Negotiated pricing, purchased, and scheduled “Just in Time” receipts of domestic raw materials; inspected all receipts for specified quality; and maintained raw materials inventory • Responsible for all office activities, including daily production reporting to corporate office; weekly correspondence of plant operations, equipment issues, and market activity; distribution of petty cash and various administrative duties as necessary • Cross-trained in Human Resources, Accounts Payable and Customer Service/Production Planning/Shipping. • Training Completed: Basics of Customer Service, Communication Skills; How to Deal with Difficult Customers; Success through Partnership: The Supervisor & Employee; PA’s Workman’s Compensation Laws; Developing Managing and Maintaining a Safety Program; Writing and Implementing OSHA Safety Plans; Essentials of HR
-
-
-
RPM Couriers
-
Freight and Package Transportation
-
Customer Service Representative
-
Jun 1995 - Oct 1996
• Managed and controlled Customer’s “Just-In-Time” inventories both in-house and off-site • Coordinated freight arrivals, releases and deliveries for Customer’s central distribution center. Prepared all Purchase Orders, Sales Orders, Bills of Lading and Invoices • Assisted in the development and documentation of the Automated Inventory Tracking System • Cross-trained in Human Resources and Accounts Receivable • Wrote procedure manual for computer system and CSR position.
-
-
Education
-
Bryant College
BS, Business Adminsitration
Community
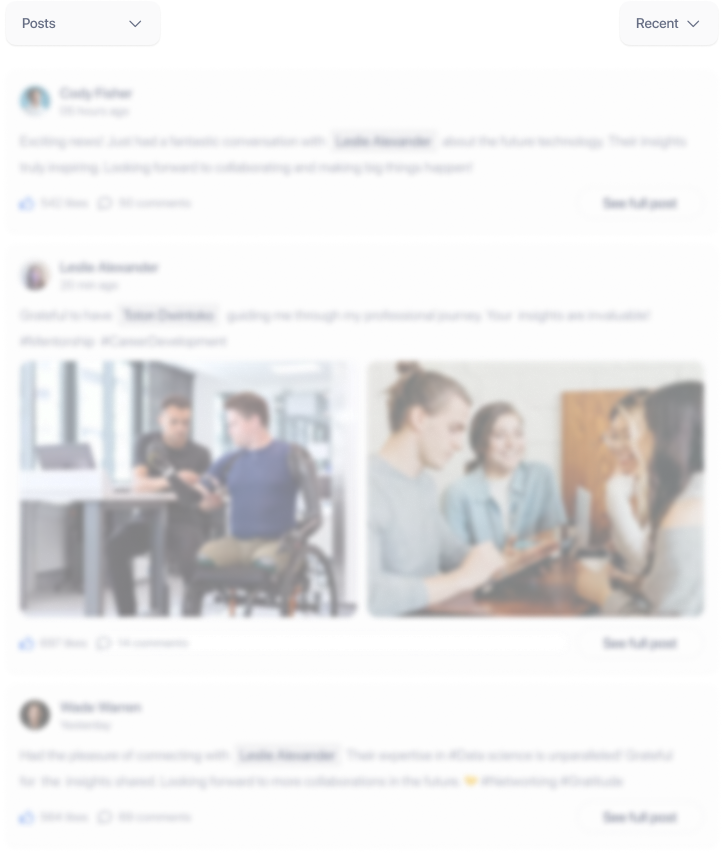