Denis Snieders
Facilities Manager at Auto Natie Group- Claim this Profile
Click to upgrade to our gold package
for the full feature experience.
-
Dutch Native or bilingual proficiency
-
French Professional working proficiency
-
German Elementary proficiency
-
English Full professional proficiency
Topline Score
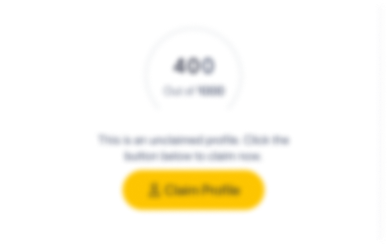
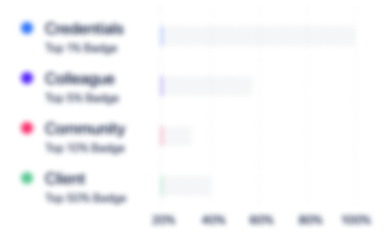
Bio


Experience
-
Auto Natie Group
-
Belgium
-
Motor Vehicle Manufacturing
-
1 - 100 Employee
-
Facilities Manager
-
Dec 2015 - Present
-
-
Facilities Manager
-
Dec 2018 - Present
-
-
Facilities management
-
Dec 2015 - Present
-
-
Facilities management
-
Sep 2018 - Present
-
-
-
WONDERCAR
-
Motor Vehicle Manufacturing
-
1 - 100 Employee
-
Facilities Manager
-
Dec 2015 - Present
-
-
Facilities management
-
Feb 2019 - Present
-
-
-
EQIN
-
Netherlands
-
Oil and Gas
-
100 - 200 Employee
-
Operational manager
-
Apr 2012 - Oct 2015
- Responsible for outbound, inbound goods, damage registration, invoice verification, repair, availability, control costs, statutory inspections, for all branches in Belgium and France - Working out and introducing a workable and affordable inspection system for the whole of the Belgian fleet. (including the goods that come from Netherlands) - Recruitment of new staff (warehouse personel, technical service, project managers, site managers) and monitoring of the training… Show more - Responsible for outbound, inbound goods, damage registration, invoice verification, repair, availability, control costs, statutory inspections, for all branches in Belgium and France - Working out and introducing a workable and affordable inspection system for the whole of the Belgian fleet. (including the goods that come from Netherlands) - Recruitment of new staff (warehouse personel, technical service, project managers, site managers) and monitoring of the training programs. - Holding working meetings with department heads (inbound, outbound, inside sales, service and maintenance) - Monthly reporting to management in the Netherlands (headquarters in Utrecht) I could always submit an operational cost that was 10% lower than budget. I stayed within the margins concerning FTE and regularly came with cost-cutting ideas - Preparation and maintenance of the ISO and VCA P en OHSAS certification -Keeping toolboxes: guarantee and ensure that everyone attending these toolboxes and understood the contents hereof. -The organization and follow-up of periodic inventory counts - Watching over safe work of employees:Preventing accidents by monitoring, discussing near misses, giving toolboxes and creating a safe working environment. this by regulating the use of PPE, the use of safe and standardized tools and make safe work a state of mind. - Change management: At the request of the Management Board our technical department is centralized in Rotterdam. Only lifting and hoisting remained in Belgium. After a little over a year, they changed opinion and the regions received their service and maintenance back . This meant adjustments to infrastructure and manpower. also these services were not included in the operational plan and not included in the budget. People who were made redundant in the previous year, had to be found suddenly again. - Best practices: many of my procedures and practices were adopted by other regions within the company.
-
-
Operational site manager Antwerp
-
Mar 2002 - Mar 2012
- Responsible for inside sales, outbound, inbound goods, damage registration, invoice verification, repair, availability, control costs, statutory inspections, for the region of Antwerp - After the departure of the director (one left himself and one was forced) I had to lead the Belgian firm temporarily during the transition period (twice 6 months) - Development and supervision of the building of the new Belgian headquarters on the Oosterweelsteenweg. -… Show more - Responsible for inside sales, outbound, inbound goods, damage registration, invoice verification, repair, availability, control costs, statutory inspections, for the region of Antwerp - After the departure of the director (one left himself and one was forced) I had to lead the Belgian firm temporarily during the transition period (twice 6 months) - Development and supervision of the building of the new Belgian headquarters on the Oosterweelsteenweg. - Recruitment of new staff (warehouse, technical service, project managers, inside sales) and monitoring of the training programs. - Holding working meetings with department heads (inbound, outbound, inside sales, service and maintenance) - As manager of the head office I was chairman of the site managers meetings - Preparation and maintenance of the ISO and VCA certification - Keeping toolboxes - Control of all incoming invoices. For both operational costs (all expenses arising from operating costs, rerents, telephone, gas, electricity, cleaning, inspection, transportation, ...) and personnel costs. - Member of the Belgian management team. Together with our director, HR manager, financial manager and sales manager I formed the belgian MT which was responsible for the proper functioning of EQIN NV - Contract negotiations with suppliers (Such as transport, rerent suppliers, mobile telefoon,...) - Introduction of an (self made) electronic filing system. When I started in the company it sometimes took up to a week to compile a dossier. Mostly all the necessary documents were not found.by creating a local and standardized registration it became possible to make a file in 2 minutes complete.
-
-
-
Dematic
-
United States
-
Transportation, Logistics, Supply Chain and Storage
-
700 & Above Employee
-
proces consultant
-
Feb 1995 - Feb 2002
- consultant for handling division at Synchro (95-96) Synchro partners (suppliers seats VW) had a productivity problem. there was a stoppage of the production line of more than 30%. My task was to reduce it by 90%. After 11 months this was achieved - Sales engineer Process Systems (97-99) sales process projects in the food and pharmacy. mainly piping, automatic valves, and automation (PLC / DCS, SCADA) communication via Profibus and Asibus - Sales manager Definox &… Show more - consultant for handling division at Synchro (95-96) Synchro partners (suppliers seats VW) had a productivity problem. there was a stoppage of the production line of more than 30%. My task was to reduce it by 90%. After 11 months this was achieved - Sales engineer Process Systems (97-99) sales process projects in the food and pharmacy. mainly piping, automatic valves, and automation (PLC / DCS, SCADA) communication via Profibus and Asibus - Sales manager Definox & Proces Consultant (Egemin Products & trades 2000- 2002) Here I came into contact with Definox, a product that was distributed by Egemin. I was asked by the sales director to give definox a boost in the market. I especially made internal promotion within Egemin and arranged that all projects were carried out with Definox. A showpiece was the introduction of Definox in the pharmaceutical industry. the EPO line at Janssens Beerse was carried out with Definox valves instead of the permanent marks. It took two years for Definox was included in the Preferred supplier list of Janssens Pharma. - Another showpiece was the installment of the biggest manifold of dairy industry in Belgium. This manifold was built in Nantes (France). cut into 4 pieces, and at night (with exceptional transport) the pieces were driven to Lummen. There they were welded orbital and connected via ASI bus to the scada software of the customer. Works began Friday and Monday, the customer went into production Show less - consultant for handling division at Synchro (95-96) Synchro partners (suppliers seats VW) had a productivity problem. there was a stoppage of the production line of more than 30%. My task was to reduce it by 90%. After 11 months this was achieved - Sales engineer Process Systems (97-99) sales process projects in the food and pharmacy. mainly piping, automatic valves, and automation (PLC / DCS, SCADA) communication via Profibus and Asibus - Sales manager Definox &… Show more - consultant for handling division at Synchro (95-96) Synchro partners (suppliers seats VW) had a productivity problem. there was a stoppage of the production line of more than 30%. My task was to reduce it by 90%. After 11 months this was achieved - Sales engineer Process Systems (97-99) sales process projects in the food and pharmacy. mainly piping, automatic valves, and automation (PLC / DCS, SCADA) communication via Profibus and Asibus - Sales manager Definox & Proces Consultant (Egemin Products & trades 2000- 2002) Here I came into contact with Definox, a product that was distributed by Egemin. I was asked by the sales director to give definox a boost in the market. I especially made internal promotion within Egemin and arranged that all projects were carried out with Definox. A showpiece was the introduction of Definox in the pharmaceutical industry. the EPO line at Janssens Beerse was carried out with Definox valves instead of the permanent marks. It took two years for Definox was included in the Preferred supplier list of Janssens Pharma. - Another showpiece was the installment of the biggest manifold of dairy industry in Belgium. This manifold was built in Nantes (France). cut into 4 pieces, and at night (with exceptional transport) the pieces were driven to Lummen. There they were welded orbital and connected via ASI bus to the scada software of the customer. Works began Friday and Monday, the customer went into production Show less
-
-
Education
-
Mensura
Interne Preventie Adviseur -
Expert VBA
Self Study -
Bureau Veritas
interne auditor, ISO 9001 14001-18001 -
Deloitte Academy
Training: Functionerings- & Evaluatie (PMP) gesprekken -
several external sales training
Senoir Sales Engineer -
EHEDG guidelines training
-
HACCP training
haccp in food & Pharma -
Syntra Antwerpen en Vlaams Brabant
Microsoft office (excel, word, powerpoint) expert
Community
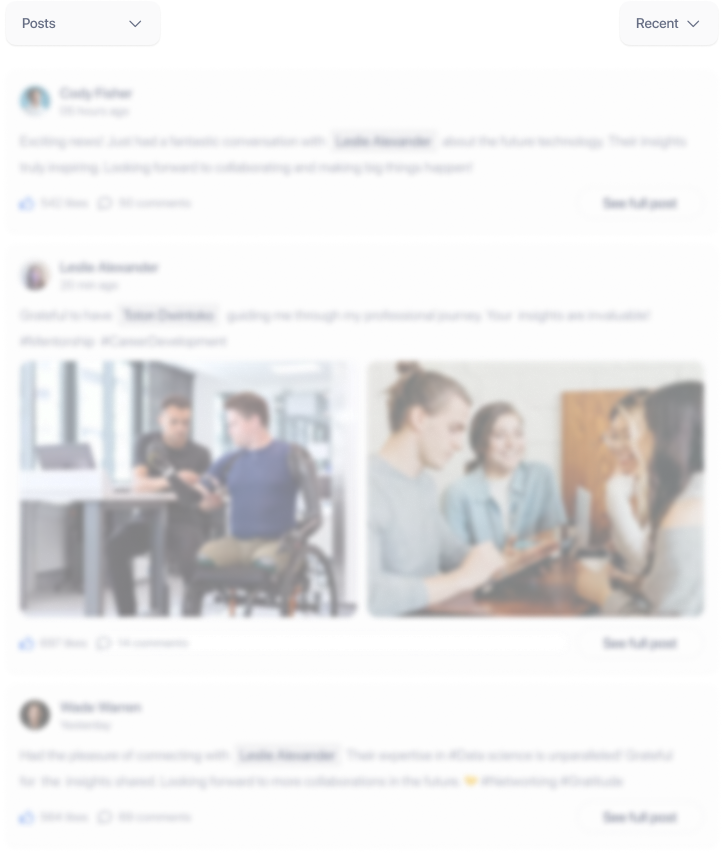