Del Calkins
Global Continuous Improvement Manager at Ichor Systems, Inc.- Claim this Profile
Click to upgrade to our gold package
for the full feature experience.
-
English -
Topline Score
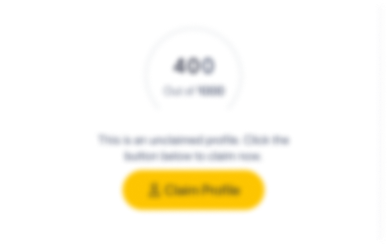
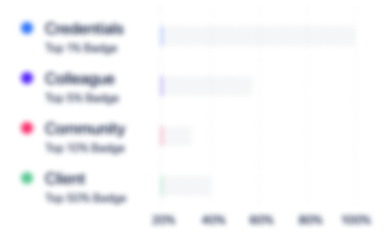
Bio


Credentials
-
Internal Auditor Certification
- -
Lean Manufacturing Mastery Certificate
- -
Six Sigma Black Belt Certification
-
Experience
-
Ichor Systems, Inc.
-
United States
-
Semiconductor Manufacturing
-
400 - 500 Employee
-
Global Continuous Improvement Manager
-
May 2020 - Present
Develop and manage a global Continuous Improvement program. Work with GM level and other global top managers to implement a program that can be mirrored at all locations. Create and deliver training programs to global community. Developing lean practitioners and deploy advanced level multi-day workshops. Manage a top tier employee suggestion and awards program, engaging the workforce to participate in daily improvements and create forward momentum into future improvements. Develop and manage a global Continuous Improvement program. Work with GM level and other global top managers to implement a program that can be mirrored at all locations. Create and deliver training programs to global community. Developing lean practitioners and deploy advanced level multi-day workshops. Manage a top tier employee suggestion and awards program, engaging the workforce to participate in daily improvements and create forward momentum into future improvements.
-
-
-
Dravon Medical Inc
-
United States
-
Medical Equipment Manufacturing
-
1 - 100 Employee
-
Plant Manager
-
2017 - May 2020
Oversee the day-to-day operational activities across the facility for a manufacturer of custom medical bags and disposable medical clamps that are used in major hospitals and healthcare facilities around the world. Manage 4 direct reports and responsible for 22 employees across the plant. Report performance of KPIs to CEO for review and basis for improvement. Coordinate all facility requirements, including contracting and hiring outside contractors, obtaining building and use permits, and enforcing regulatory requirements from various agencies such as the FDA and EPA. Work closely with Engineering and Marketing at trade shows. Make direct customer contact to resolve purchase order scheduling differences, resolve delivery questions, and coordinate responses to technical questions. Team with Controller and CEO to occasionally provide input on preparing a customer quotation. Key Achievements: Achieved a 60% increase in production output by analyzing labor content and setting realistic goals for the team. Reduced lead time from eight to six weeks by building a schedule board and setting up a cross-functional team to assist with factory floor planning. Steered the reorganization of warehouse and inventory systems, leading to organized and labeled storage, making it easier to locate and track material, and reducing the stock outs. Implemented OSHA improvements and other plant safety programs, enhancing safety awareness and communication, which helped to reduce recordable accidents for 2019 to one, compared to three in 2018. Introduced KPI program for goal achievement and visibility, helping to sustain production and quality improvements. Show less
-
-
-
ProTech Industries, Inc.
-
United States
-
Truck Transportation
-
1 - 100 Employee
-
Lean Manufacturing Manager | Quality Manager | Safety Manager
-
2015 - 2016
Assisted with the implementation of Lean Manufacturing goals and strategies for improving the operations and processes for a manufacturer of truck accessories and bodies for pickup trucks, flatbeds, and Class 8 vehicles. Evaluated all continuous improvement activities and implemented plans to optimize performance and processes. Employs Lean methodologies and tools to help accomplish business objectives. Key Achievements: Slashed past-due shipments from $450K to $112K, a 75% reduction, by leading a root cause analysis project, discovering the reasons for the past due, and implementing corrective actions. Developed custom daily schedules for each department and established/enforced strict rules for adherence, improving on-time delivery from 46% to 98%, making past due shipments nearly non-existent. Enhanced efficiencies and On-Time Deliveries by 87% by applying Lean principles; developed a master schedule for the seven different departments so that products would be completed in time to ship together as needed. Introduced quality programs to ensure first-pass quality and reduce RGAs by 77%; set up accountability meetings so that team leads and employees could understand why a product was returned and how to avoid the same type of quality problems going forward. Show less
-
-
-
Cornell Pump Company, LLC
-
United States
-
Industrial Machinery Manufacturing
-
100 - 200 Employee
-
Lean Manufacturing Manager
-
2011 - 2015
Contributed to the creation and implementation of best practice Lean vision, strategy, policies, processes, and procedures to improve operational performance for a manufacturer of industrial pumps for agricultural, mining, oil/gas, and industrial applications. Established operational performance metrics to provide visibility of performance and efficiency. Trained and educated workforce on Lean tools and concepts, while serving as main resource for the culture of continuous improvement. Key Achievements: Identified an overabundance of shafts in stock; made adjustments to MRP system to stop all outside processing of these shafts and similar parts, cutting inventory by $150K and saving $65K monthly by eliminating unnecessary labor. Championed 35% increase in On-Time Delivery (OTD) by mapping a process to reveal several steps that were leading to delays; implemented better visibility and communication while making minor tweaks to system, which allowed OTD to move up to 85% to 90%. Developed and implemented pull systems and First-In/First-Out inventory system, freeing up two bottlenecked work areas and improving the build rates at the assembly area through a kitting process. Spearheaded and managed numerous Kaizen improvement projects from initiation through delivery. Created and administered in-house Lean certification courses to educate employees in Lean processes, speed up the buy-in process, and produce several Lean leaders to drive the transformation. Show less
-
-
-
Danner | LaCrosse
-
Portland, OR
-
Production Supervisor
-
2009 - 2011
Played a vital role in ensuring the production levels and goals were met for a manufacturer of footwear. Motivated, coached, and assisted production team perform at its full capacity. Established production processes and procedures for product changes, quality concerns, and overall efficiencies. Monitored plant for efficient flow of material and proper rotation of stock; watched material usage to reduce scrap and improve material usage. Ensured and enforced expected product workmanship quality. Managed 6 direct reports and 90 employees. Key Achievements: Orchestrated an aggressive production expansion, with productivity improvements and efficiencies. Accomplished a 40% reduction in first-pass quality errors by initiating a personal accountability program where everyone signed a production ticket as the work flowed through each station. Managed second shift team through a growth period from 40 to 90 employees, realizing a near seamless transition. Surpassed production goals daily by maintaining a presence on the shop floor and encouraging the employees to do their best while communicating goals and working hands-on with them, setting a pace. Show less
-
-
-
Saint-Gobain Crystals
-
Washougal, WA
-
Manufacturing Supervisor
-
2008 - 2009
Directed day-to-day operations for a manufacturer of crystal wafers for key clients in the semiconductor industry. Supervised a team of 20 employees, ensuring utilization of resources and raw materials in the most efficient and productive manner possible. Demonstrated solid leadership skills to maximize productivity, safety, product quality, KPIs, and superior service levels. Key Achievement: Identified a bottleneck in the flow of wafers; adjusted shift start/stop times, combined cleanup responsibilities, and scheduled machine run times to unclog department and get parts moving into next work area, attaining a 66% increase in output, slashing machine startup time by 78%, and boosting machine run time by 48%. Show less
-
-
-
Toray Composite Materials America, Inc.
-
United States
-
Chemical Manufacturing
-
200 - 300 Employee
-
Shift Manager | Operations Analyst
-
2007 - 2008
Supervised and coordinated the daily operations for assigned shift consisting of 2 supervisors, 12 machine operators, 2 warehouse employees, and a 5-person maintenance team for a manufacturer of carbon fiber. Managed the workforce to achieve productive goals and performance standards. Monitored team members, allowing for continuous feedback and mentoring to help each team member grow and succeed. Ensured compliance to safety programs. Key Achievements: Evaluated production efficiencies, identified deficiencies, and developed/implemented corrective action plans to optimize functionality, output, and productivity. Directed complete overhaul of inventory and materials management strategies, which entailed disposing of over $1M in expired product and implemented strict internal controls using a first-in/first-out methodology to circumvent any future loses. Performed within a multidisciplinary executive management team to review activities within internal business units; developed appropriate corrective actions, re-training programs, and purchasing protocols. Show less
-
-
-
Consolidated Metco
-
United States
-
Truck Transportation
-
700 & Above Employee
-
Production Supervisor
-
2004 - 2006
Supervised production operations in accordance with policies and procedures for a manufacturer of lightweight aluminum components. Trained and coached production staff; managed shift schedule. Supported quality control by making adjustments as necessary during shift to produce product within specifications. Maintained SOPs and job safety protocols. Applied solid problem-solving skills to address and resolve issues impacting operations. Key Achievements: Ensured critical production capacity to meet stringent delivery deadlines. Led team of senior operators to design a shift change procedure and checklist that allowed machines to continue to run longer through shift change, adding 40 additional hours of run time per week. Show less
-
-
Education
-
University of Phoenix
Master of Science - MS, Management (Human Capital) -
University of Phoenix
Bachelor of Science - BS, Business Management
Community
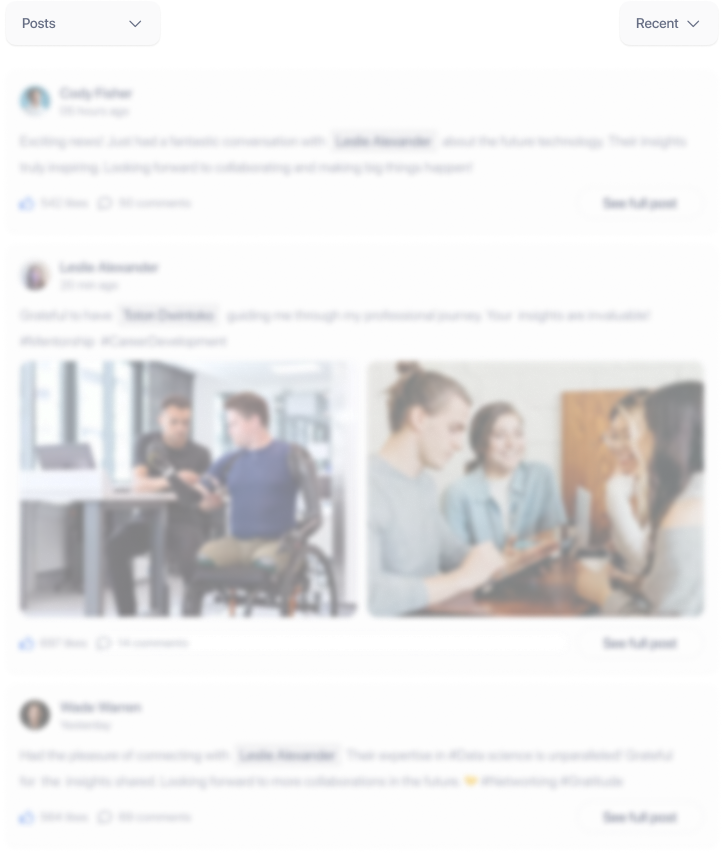