DeEtte Delaney
Plant Manager at KPI Concepts- Claim this Profile
Click to upgrade to our gold package
for the full feature experience.
Topline Score
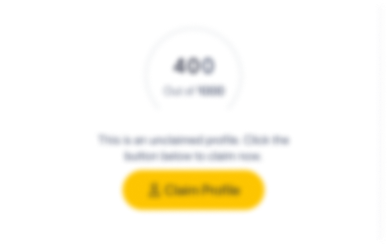
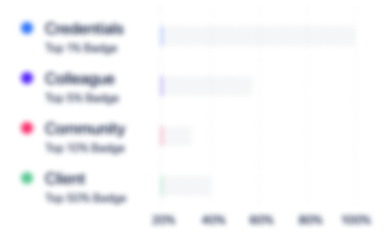
Bio

Cliff Carson
DeEtte is both a Quality Manager and a Program Manager. In either position she is a valuable asset to those who depend on her, seek her advice, or need her to take on a complicated Project. DeEtte is an excellent organizer and intensely monitors the metrics of performance assuring good outcomes to those Projects she takes on.

Cliff Carson
DeEtte is both a Quality Manager and a Program Manager. In either position she is a valuable asset to those who depend on her, seek her advice, or need her to take on a complicated Project. DeEtte is an excellent organizer and intensely monitors the metrics of performance assuring good outcomes to those Projects she takes on.

Cliff Carson
DeEtte is both a Quality Manager and a Program Manager. In either position she is a valuable asset to those who depend on her, seek her advice, or need her to take on a complicated Project. DeEtte is an excellent organizer and intensely monitors the metrics of performance assuring good outcomes to those Projects she takes on.

Cliff Carson
DeEtte is both a Quality Manager and a Program Manager. In either position she is a valuable asset to those who depend on her, seek her advice, or need her to take on a complicated Project. DeEtte is an excellent organizer and intensely monitors the metrics of performance assuring good outcomes to those Projects she takes on.

Experience
-
KPI Concepts
-
United States
-
Retail Office Equipment
-
1 - 100 Employee
-
Plant Manager
-
Dec 2017 - Present
𝑆𝑢𝑝𝑝𝑙𝑖𝑒𝑟 𝑜𝑓 𝑄𝑢𝑎𝑙𝑖𝑡𝑦 𝑆𝑡𝑜𝑟𝑒 𝐹𝑖𝑥𝑡𝑢𝑟𝑒𝑠 𝑡𝑜 𝑀𝑎𝑗𝑜𝑟 𝑅𝑒𝑡𝑎𝑖𝑙𝑒𝑟𝑠 (𝐴𝑙𝑑𝑖, 𝐻𝑦𝑉𝑒𝑒, 𝐶𝑎𝑠𝑒𝑦’𝑠, 𝑇𝑎𝑟𝑔𝑒𝑡) • Responsible for the full P&L and overall plant productivity, and employee safety for a non-union manufacturing plant producing store fixtures (displays, cabinets, shelving, check lanes) for leading brands across the US. • Manage a leadership team consisting of a Production Control Manager, Maintenance Manager, Engineer/Continuous Improvement Manager, and Purchasing Manager leading the hourly staff all aspects of manufacturing operations and delivering results that meet quality, customer service, safety, innovation, and cost criteria. • Direct the short- and long-term operating planning for the manufacturing operation, developing strategies to exceed objectives in cost reduction, quality improvement, and new product development. • Oversee all processes and manufacturing lines, including cutting (CNC and Saws), secondary operations, welding, and assembly cells. • Develop and implement new layouts, including all assembly cells and warehouse storage in the facility and Layouts to launch new designs for various products, enhance material flow, increase efficiencies, and minimize required labor input. • Spearheaded the introduction and execution of process improvement and capital project initiatives, including 5S, Standard Work, SOPs, and several equipment installation and repair projects. • Create and maintain programs that provide a safe, OSHA work environment and EPA compliant plant. 𝐊𝐞𝐲 𝐀𝐬𝐬𝐢𝐠𝐧𝐦𝐞𝐧𝐭𝐬 • Improved On-Time Delivery from 74% to 99.6% • Increased Net Income by 5.1% • Led project team that successfully implemented a corporatewide ERP system across four divisions and three locations and implemented the Preventive Maintenance module of the ERP system at the Utah facility Show less
-
-
-
Day & Zimmermann
-
United States
-
Construction
-
700 & Above Employee
-
Director of Programs
-
Aug 2016 - Nov 2017
𝑂𝑝𝑒𝑟𝑎𝑡𝑖𝑛𝑔 𝐶𝑜𝑛𝑡𝑟𝑎𝑐𝑡𝑜𝑟/𝑃𝑟𝑖𝑚𝑒 𝐶𝑜𝑛𝑡𝑟𝑎𝑐𝑡𝑜𝑟 𝑓𝑜𝑟 𝑈𝑆𝐺 𝑜𝑤𝑛𝑒𝑑 & 𝑝𝑟𝑖𝑣𝑎𝑡𝑒𝑙𝑦 ℎ𝑒𝑙𝑑 𝑎𝑚𝑚𝑢𝑛𝑖𝑡𝑖𝑜𝑛 𝑚𝑎𝑛𝑢𝑓𝑎𝑐𝑡𝑢𝑟𝑖𝑛𝑔 𝑓𝑎𝑐𝑖𝑙𝑖𝑡𝑖𝑒𝑠.• Responsible for managing a $100M+ portfolio of awarded contracts, engineering projects, and production programs with full budgetary accountability and leading a team of 3 direct employees, including a program manager and 2 engineers coordinating to ensure execution of all program initiatives between two union facilities in IA and TX.• Set goals for programs according to the strategic objectives of the organization and devised evaluation strategies to monitor performance and determine the need for improvements.• Ensured all relocations and new production start-ups had customer approvals for all procures, including First Article plans and testing requirements for the D&Z/AO operations and those of the company’s suppliers. • Implemented master production scheduling system and prioritized assignments to support critical path activities to meet customer qualification and production schedule requirements.• Collaborated with directors to support cost estimating for capital improvement projects, including equipment, tooling, and facility upgrades.• Supervisory PM responsibility for Navy Primers (MK45, MK48), Mortars (60MM, 81MM), Supplementary Charge, Fuzes.𝐊𝐞𝐲 𝐀𝐬𝐬𝐢𝐠𝐧𝐦𝐞𝐧𝐭𝐬• Member of the management team that orchestrated a 6-month plant turnaround and added $2.5M to the overall goal.• Direct project manager responsible for a M67 Grenade ($65M multi-year Contract) and Primers• Secured multiple additional contracts including M67 Grenade – $13.6M, Various Primers - $6M, Navy Primers - $2.5M, and Mortars - $15M Show less
-
-
Program Manager
-
Feb 2014 - Aug 2016
• Performed program management functions for the Iowa operation with a $35M annual budget and Texas operation with a $65M annual budget, developing the funding packages and coordinating design and performance on all contracts, capital projects, and major maintenance projects for the ammunition plants.• Directed multiple relocation teams consisting of design engineers, controls engineers, manufacturing engineers, operations, maintenance, purchasing, and transportation. • Accountable for planning and directing all phases or portions of major projects and programs involving estimating, material and labor, work scope development, and scheduling of work to ensure completion within estimated time limits and budget requirements.• Coordinated and prioritized all functional areas (safety, quality, engineering, supply chain, production, maintenance, contracts) to support multiple production programs and ongoing production projects.• Managed cross-functional matrixed teams for production initiatives, including manufacturing engineers, operations representatives, quality engineers, purchasing, and production planners. Completed Projects• Texas - $700k - Relocation of all production operations (Navy primers, 120MM primers, fuzes, FRPC) from Arkansas to Texas.• Texas - $100k – Relocate 40# Demo Shaped Charge from Kansas to Texas.• Iowa - $2.3M – Installation of an x-ray inspection system (Artillery).• Iowa - $1.2M – Installation of automatic x-ray inspection system (Ignition Cartridge).• Iowa – PM responsibilities for MICLIC M58A4, M112 C4, 120MM Tear Down, 120MM Refurbish, 75MM Blanks, Hellfire Show less
-
-
Engineering Project Manager
-
Jan 2009 - Jan 2014
• Managed projects for two decommissioned plants, leading major and large-scale relocation projects moving production operations for Detonators, Artillery, FASCAM, MICLIC, Mortars - 61MM, 81MM, & 120MM, ICM, and MLRS from KS and TX to locations in TN and IA. ($4M)• Oversaw an additional relocation of production operations for C4 (M112), Ignition Cartridges, and Spider from the TN location to the IA location. ($2M)• Responsible for the capital projects through all engineering phases, including feasibility, conceptual, design, cost estimates, scheduling, and relocation execution.𝐊𝐞𝐲 𝐀𝐬𝐬𝐢𝐠𝐧𝐦𝐞𝐧𝐭• Successfully turned around two major design projects and neutralized a projected cost growth of 19% Show less
-
-
-
HNI Corporation
-
United States
-
Furniture and Home Furnishings Manufacturing
-
700 & Above Employee
-
Quality Manager ~ HON Company Division
-
Dec 2007 - Jan 2009
𝐺𝑙𝑜𝑏𝑎𝑙 𝑂𝑓𝑓𝑖𝑐𝑒 𝐹𝑢𝑟𝑛𝑖𝑡𝑢𝑟𝑒 𝑀𝑎𝑛𝑢𝑓𝑎𝑐𝑡𝑢𝑟𝑒𝑟• Responsible for developing and implementing quality initiatives using lean manufacturing tools to drive continuous improvement in a 350 employee 50K sq. ft. ISO-9001 certified manufacturing plant producing wood office furniture, including desks, cabinets, and file cabinets.• Directed a team of 12 Quality Engineers and Quality Auditors reviewing and maintaining quality standards and specifications on inbound raw materials and outbound finished goods.• Conducted quarterly quality training on standard work procedures along with Critical to Quality (CTQ) procedures with quality inspectors, quality engineers, and operators• Performed daily quality audits to ensure final product conformity to quality standards.• Co-leader of the Engineer Training Program – targeted at ensuring the engineering staff had a complete understanding of their duties and the tools to perform them effectively.𝐊𝐞𝐲 𝐀𝐬𝐬𝐢𝐠𝐧𝐦𝐞𝐧𝐭𝐬• Implemented the revised HON Quality system and a plant-wide Quality Training Program, resulting in 20% scrap reduction• Implemented and trained personnel in HON’s Product Life Cycle Management system for the product launch of the Attune family – over 70 new items across seven different production lines. Show less
-
-
Factory Manager - Hearth & Home Technologies
-
Sep 2006 - Dec 2007
• Directed the $15M P&L over 8 product departments within a 500-employee 300K sq. ft. ISO-90001 certified plant producing finished goods and components for fireplace products across 20 production lines delivering $90M+ in annual revenue.• Responsible for leading a team of 5 Production Supervisors, 1 Manufacturing Engineer, and 7 Team Leaders developing, coaching, and delivering lean training for 100 hourly employees. • Led numerous Rapid Continuous Improvement (RCI) Events track and executed goals focusing on achieving safety, quality, delivery, and cost.• Participated and led several kaizen teams introducing new processes and procedures to improve plant design and layouts efficiency.• Launched 3 new lines within targeted time frames, one of which was less than 6 weeks.• Lead writer and editor of the application for the 2007 Shingo Prize for Excellence in Manufacturing. HHT-Mt. Pleasant was ultimately awarded this prize.• Championed the relocation of a production line from a facility in Washington state in less than 6 weeks, including the introduction and training of employees to become certified welders• Decreased warranty dollars by 38%• Lowered Service Call Rate by 15%• Cut the Cost of Quality by 23%• Reduced Defects (internal) by 40% Show less
-
-
Quality Systems Manager ~ Hearth & Home Technologies Division
-
Oct 2003 - Sep 2006
• Oversaw a team of 4 direct reports, including Technical Services Manager, Quality Engineer, Quality Manager, and Safety Manager, leading up to 20 indirect reports accountable for developing and administering quality standards and setting the strategic direction of the Quality Services Department - Technical Services, Quality, and Safety.• Accountable for directing the activities and training of Members of the department and assisting in the training and motivation of all Members with regard to quality, safety, and environmental issues.• Developed and coordinated the execution of the ISO 9001 quality system, including implementation of HON 20 step Quality System.• Responsibilities included implementing lean, customer problem resolution, and improving process capability in all aspects of the plant.• Assisted in the development and execution of the Strategic Goal Alignment process. Show less
-
-
-
Federal-Mogul Powertrain
-
United States
-
Motor Vehicle Manufacturing
-
700 & Above Employee
-
Sr. Quality Engineer
-
Dec 2002 - Oct 2003
𝑀𝑎𝑛𝑢𝑓𝑎𝑐𝑡𝑢𝑟𝑒𝑟 𝑜𝑓 𝐶ℎ𝑎𝑚𝑝𝑖𝑜𝑛 𝐵𝑟𝑎𝑛𝑑 𝑆𝑝𝑎𝑟𝑘𝑝𝑙𝑢𝑔𝑠 𝑓𝑜𝑟 𝑂𝐸 𝑎𝑛𝑑 𝐴𝑓𝑡𝑒𝑟𝑚𝑎𝑟𝑘𝑒𝑡 𝐴𝑝𝑝𝑙𝑖𝑐𝑎𝑡𝑖𝑜𝑛𝑠• Developed, deployed, and monitored quality strategies for a 600-employee union-UAW 130K sq. ft. manufacturing plant producing Spark plugs for Champion, Daimler-Chrysler, Denso, Briggs & Stratton, and Harley-Davidson producing ~$80M in annual revenue.• Led a team of 2 direct reports accountable for all Small Engine and Aftermarket Customer and Manufacturing issues, reporting to the Corporate Ignition Group Quality Manager.• Established facility KPIs and customer satisfaction ratings, led process improvement initiatives, and trained "Back to Quality Basics" (APQP, FMEA, Control Plan, PPAP, and MSA), resulting in scrap reduction, increased productivity, and enhanced customer ratings. • Led the ISO 14001 Certification team, developed benchmarking and best practices, and trained staff on using in 5S, Value Stream Mapping, Continuous Flow, and Six Sigma.𝐊𝐞𝐲 𝐀𝐬𝐬𝐢𝐠𝐧𝐦𝐞𝐧𝐭𝐬• Scrap reduction team leader steering team to a 20% scrap reduction goal (5.5% of COGM) for 2003.• Leader of the Engineering Change (ECN) Implementation team reduced the number of unimplemented ECNs by 78%. Show less
-
-
Quality Manager
-
Jul 2001 - Dec 2002
• Managed a team of 4 direct reports, including Managers and Engineers, and 9 indirect Quality Auditors accountable for all aspects of the Quality System, including internal and external customer satisfaction and successful maintenance of QS-9000 Certification.• Responsible for implementing short and long-term corrective action systems, lean manufacturing techniques, and implementation and training of ISO 9001 standards, including implementing an integrated Quality Software System to control documents, actions, internal and external audits, and engineering changes.• Designed and implemented lean manufacturing training to turn around inefficiencies in plant equipment utilization, inventory management, and cell layout.• Management representative on the Contract Negotiation Team successfully negotiated the first four-year contract in the company’s history.𝐊𝐞𝐲 𝐀𝐬𝐬𝐢𝐠𝐧𝐦𝐞𝐧𝐭𝐬• Led the way in removing Needs Improvement Status at DaimlerChrysler raising quality rating from 68% to 97%• Reduced external PPM from 104 to 27• Scrap costs were reduced from 8% of COGM to 6.9% of COGM through scrap reduction teams' aggressive use. Show less
-
-
Business Unit Manager (Metalworking - 08/1997- 05/2000) & (Assembly - 05/2000- 07/2001)
-
Aug 1997 - Jul 2001
• Managed all manufacturing and engineering functions related to two departments, including the metalworking departments consisting of cold forming, turning, welding, thread rolling, plating, and the assembly department.• Responsible for ~$25M in business unit budgets accountable for all financial and operational performance requirements, and directing a team of ~15 Engineers, Superintendents, and Supervisors) and ~300 hourly UAW employees across three shifts with a daily. manufacturing volume of 600K+ units per day of spark plugs and components: shells, wires.𝐊𝐞𝐲 𝐀𝐬𝐬𝐢𝐠𝐧𝐦𝐞𝐧𝐭𝐬• Implemented and trained Supervisors in the ‘STOP’ for Safety program growing plant safety scores from 64 to 87• Team leader for numerous ‘Kaizen’ events, transitioning several operations from batch manufacturing to continuous flow processing. Used Lean Manufacturing and Visual Factory principles to improve Customer Delivery Performance from 77% to 98% while decreasing lead time by 80%, WIP by 20%, and Scrap by 10%.• Reduced perishable tooling consumption ($6 Million budgeted) by 17%. Show less
-
-
Education
-
University of Iowa
BS, Industrial Engineering -
University of Iowa - Henry B. Tippie College of Business
Executive MBA
Community
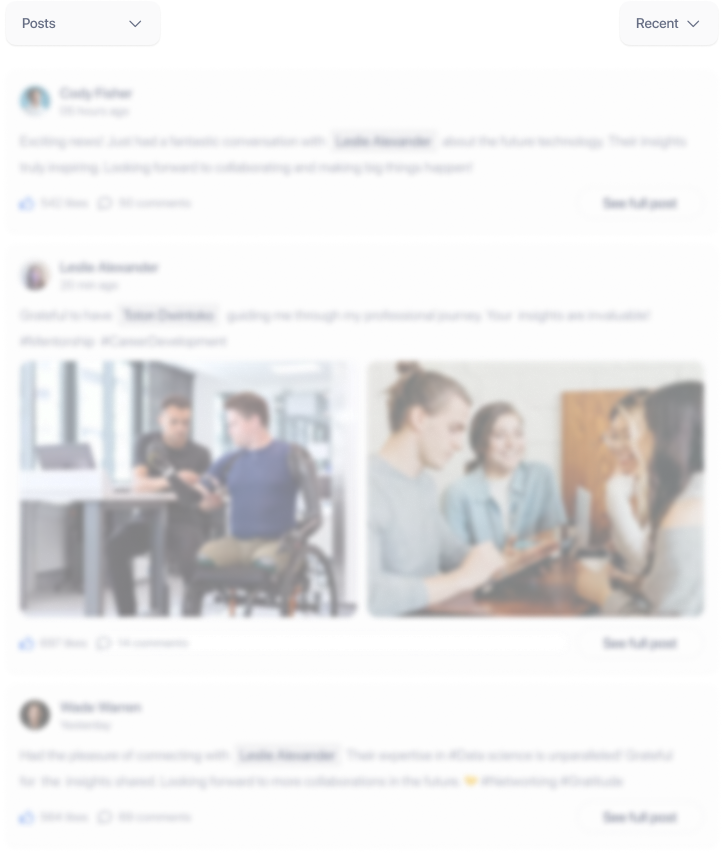