Deepak Rathi
Manufacturing & Operation Head at Lenskart Solutions Private Limited- Claim this Profile
Click to upgrade to our gold package
for the full feature experience.
Topline Score
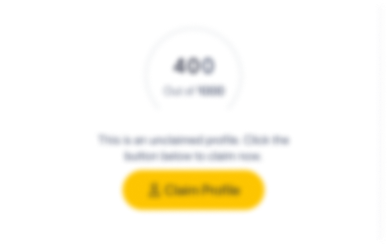
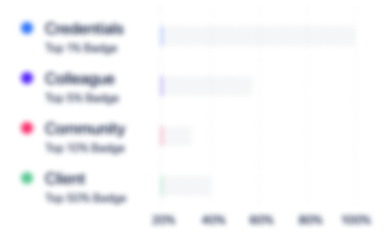
Bio


Experience
-
Lenskart Solutions Private Limited
-
India
-
200 - 300 Employee
-
Manufacturing & Operation Head
-
Nov 2018 - Present
Manufacturing & Operation Head - Sr. Manager • Develop various strategy, policies & KPI for manufacturing process & warehouse operation.• Responsible for entire plant operation. (Manufacturing (Machines & Assembly Line)/Quality/Dispatch/Warehouse/Returns/Stock in)• Managing 600 manpower which include 8 managers & 22 Assistant manager.• Ensuring production & delivery as per defined TAT along with defect free production in the manufacturing.• Directly coordinate with sales, Logistics & customer support team for various strategy & planning.• Direct coordinate with vendors for price negotiation of material, timely delivery & for quality product.• Run the manufacturing process as per defined AOP (Annually Operating Plan). • Ensure to achieve the defined OEE of the MEI machine.• Direct responsible for employee health & safety.• Design & implement various process in manufacturing & WH operation to strengthen the process.Key Achievements.• Successfully implementation of Quality & Repairing structure in the plant.• Over delivery TAT reduced from 4.2 days to 1.9 days.• Production productivity per person (Assembly Line) increased from 20 to 31.• Warehouse productivity(Pickers) per person increased from 60 to 115.• Manufacturing defect rate reduced from 9.2% to 3.1%.• Done various automation in the plant e.g. Auto bag introduction in packing line, Focovison testing in quality process, Redefined the conveyor logics & make separate line for premium orders.• Machines OEE increases from 55% to 82%• Successfully operate the plant under Covid-19 condition.
-
-
-
Micromax Informatics Ltd
-
India
-
Computers and Electronics Manufacturing
-
700 & Above Employee
-
Customer Service Operation Manager
-
Oct 2015 - Nov 2018
Manager – Customer Service Assumed full responsibility for managing all customer service operation, including front & backend operation MSL & part planning, vendor management, logistics management with extra office responsibilities. Oversaw the generation of maximum profitability and ensured 100% customer satisfaction were met while simultaneously performing safety, quality, cost, and inventory management within operating budget constraints. Supervised and directed all employee disciplinary and training programs, safety programs.• Develop various strategy & KPI for front & backend operation along with execution level.• Manage Service Operations of ASC, WH, Logistics through effective co-ordination with concerned. • Ensure Customer Service Process & Policy implementation by organization should be implement at the last person in customer service i.e. Technician of Service Partners• Acumen to plan model wise call creation and assess backend readiness including Spare Parts, WH, Logistics, L4 production.• Managing delivery of development programmes and supporting strategy for the repair centre – New Product Launch and Regular Repair Trainings• Ensuring weekly MIS through Dashboards-trends, highlight/ lowlight and action planning.• Handling 6 vendor (L4 level partner) directly & responsible for their full operation.• Develop strategies on L4 Repair–production, partner expansion, repeat repair reduction, high value part Consumption and quick reactions to frequent failures.• Develop strong Inventory audit mechanism for Inward/ Outward, lost, damaged stock audit and Reconciliation process and control steps• Ensure part supply & defectives return timely for smoothly account operation.• Verification of quality issues raised by partner and then co-ordination with quality & R&D for the improvement.
-
-
-
-
Production Manager
-
Jun 2011 - Oct 2015
Assistant Manager Production & Process Quality Assumed full responsibility for managing all plant operations, including shipping & receiving, maintenance, production, and sanitation with extra office responsibilities. Oversaw the generation of maximum profitability and ensured full production levels were met while simultaneously performing safety, quality, cost, and inventory management within operating budget constraints. Supervised and directed all employee disciplinary and training programs, safety programs, and plant improvement projects.• In charge of 4 area in plant – Main line(mobile assembly line), Repair section, Process quality control & Material marshalling area & ensure production of more than 2 lacs mobile phones per day with 32 assembly line & handling MP of 600 operator & 20 leader. • Managing Sub assembly vendor directly & ensure more than 10 lacs production per day of sub- assembly parts of mobile phones & timely delivered to parent company.• Ensure all quality standard should be operated properly at all line (main & sub).• Before production start ensure line wise material should be prepared & reached to line wise timely.• Along with Production Head discuss three month production plan for main line & sub assembly with production planning team, making internal plan for main line production in accordance with three month plan for HHP and break plan into weekly and daily targets .Attend daily production meeting and analyse daily production targets for HHP main line to arrive at model wise optimum sequence of production in coordination with Head of production shift engineer and production innovation team etc & coordinate with SMD Shift in Charge and Shift Engineer• Monitor all lines on daily basis to ensure compliance on all company defined manufacturing standards and parameters
-
-
-
Videocon Consumer Durables
-
India
-
Consumer Goods
-
200 - 300 Employee
-
IQC Incharge
-
Apr 2010 - Jun 2011
• Worked as an IQC Electrical team in charge• Managing the Supplier quality & process improvement along with Inspection of Incoming Materials of CTV, LCD & LED parts Including Panel, Chassis & Sub-Assy. supported by the Team of 1 Engineer & 4 Operator.• Managing Quality related tasks including Quality compliance Audits, Parts History, Supplier History, Supplier & Internal Quality Targets, RMA, Multi Skill, QM Module management in SAP, Monthly & Weekly Reports. • Managed and worked with suppliers on quality issues for electronic & assemblies including electronic components, semiconductors, PBA, SMD parts, wire assemblies, LCD, CRT/CDT, molding parts & packaging & printing items.• On weekly basis made & represent MIS in FMM meeting.
-
-
Education
-
BHARAT INSTITUTE OF TECHNOLOGY SCHOOL OF ENGINEERING, MEERUT
Bachelor of Engineering - BE, Electrical, Electronics and Communications Engineering
Community
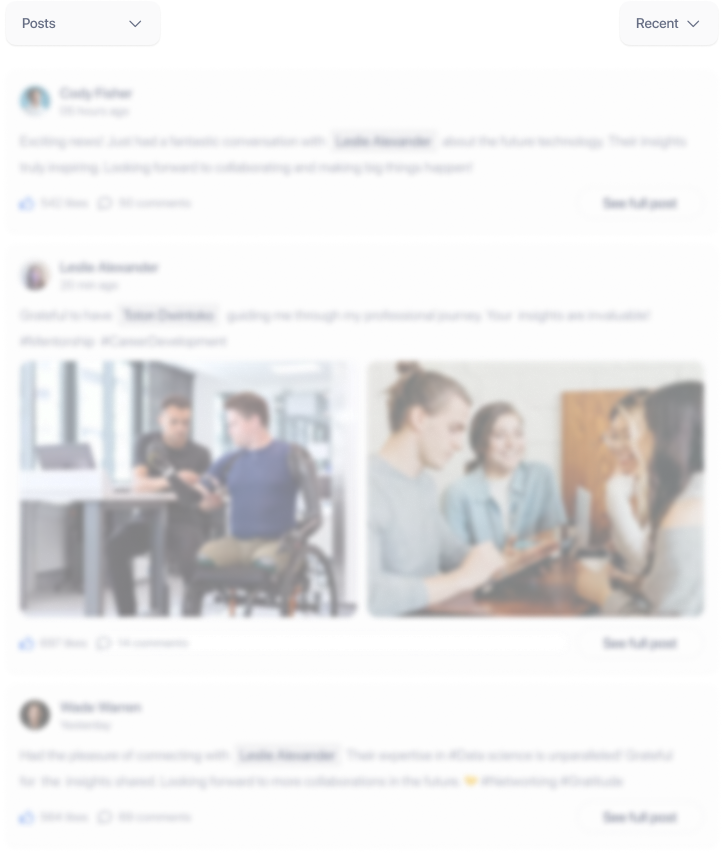