Dean Weiberg, MA, CAMA
Senior Consultant at IDCON INC- Claim this Profile
Click to upgrade to our gold package
for the full feature experience.
Topline Score
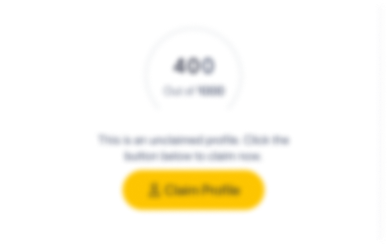
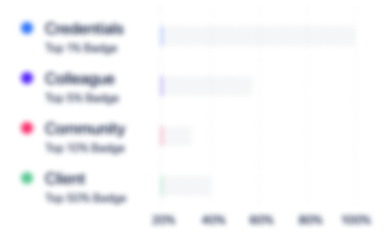
Bio

Peter Chalich
I had the opportunity to work with Dean for several years while he was at Cleveland Cliffs’ Hibbing site. He and the team at Hibbing took the basic building blocks of industrial reliability and forged them into award winning industrial maintenance and reliability programs. This takes vision, leadership and managerial savvy. I am glad to have had the opportunity to work with Dean and would not hesitate recommending him for leadership roles in these areas.

Peter Chalich
I had the opportunity to work with Dean for several years while he was at Cleveland Cliffs’ Hibbing site. He and the team at Hibbing took the basic building blocks of industrial reliability and forged them into award winning industrial maintenance and reliability programs. This takes vision, leadership and managerial savvy. I am glad to have had the opportunity to work with Dean and would not hesitate recommending him for leadership roles in these areas.

Peter Chalich
I had the opportunity to work with Dean for several years while he was at Cleveland Cliffs’ Hibbing site. He and the team at Hibbing took the basic building blocks of industrial reliability and forged them into award winning industrial maintenance and reliability programs. This takes vision, leadership and managerial savvy. I am glad to have had the opportunity to work with Dean and would not hesitate recommending him for leadership roles in these areas.

Peter Chalich
I had the opportunity to work with Dean for several years while he was at Cleveland Cliffs’ Hibbing site. He and the team at Hibbing took the basic building blocks of industrial reliability and forged them into award winning industrial maintenance and reliability programs. This takes vision, leadership and managerial savvy. I am glad to have had the opportunity to work with Dean and would not hesitate recommending him for leadership roles in these areas.
0
/5.0 / Based on 0 ratingsFilter reviews by:
Credentials
-
Certified Asset Management Assessor (CAMA)
World Partners in Asset ManagementDec, 2019- Sep, 2024
Experience
-
IDCON INC
-
United States
-
Business Consulting and Services
-
1 - 100 Employee
-
Senior Consultant
-
Nov 2019 - Present
-
-
-
Road Machinery & Supplies Co.
-
United States
-
Machinery Manufacturing
-
100 - 200 Employee
-
Controller
-
Nov 2017 - Nov 2019
-
-
-
Weiberg's Inc.
-
United States
-
Medical Practices
-
Owner
-
Jan 1989 - Nov 2019
-
-
-
Tritec Of Minnesota Inc
-
United States
-
Appliances, Electrical, and Electronics Manufacturing
-
Financial Controller
-
Nov 2014 - Oct 2017
-
-
-
-
Area Manager - Asset Mangement
-
May 2012 - Sep 2014
Reporting the site General Manager – VP, the Asset Manager leads the efforts of the maintenance planning, scheduling, reliability, and project engineering. Overall accountability for 4 direct reports, and MOR of 14 indirect reports consisting of planners, schedulers, reliability engineers, and reliability technicians. The Asset Management department was formed in June of 2012 to provide leadership and clarity to the support functions of the organization by separating them functionally and organizationally from the execution of work.
-
-
Area Manager - Business Improvement
-
Oct 2011 - May 2012
Member on a corporate cross functional team in cooperation of external consultants to deploy an organizational structure project across Cliffs North American Iron Ore based on the Stratified Systems Theory. In addition, implemented process improvements utilizing the learnings of the Theory of Constraints, Lean, 5s, and Six Sigma DMAIC (Define, Measure, Improve and Control) methodologies.
-
-
-
-
Area Manager - Site Maintenance and Reliability
-
2008 - Dec 2012
Reporting the site General Manager – VP, the Maintenance Manager leads the efforts of the maintenance planning, scheduling, reliability, and execution. Overall accountability for 7 direct reports, and MOR of approximately 35 indirect reports consisting of planners, schedulers, reliability engineers, supervisors, reliability technicians and crafts. Reporting the site General Manager – VP, the Maintenance Manager leads the efforts of the maintenance planning, scheduling, reliability, and execution. Overall accountability for 7 direct reports, and MOR of approximately 35 indirect reports consisting of planners, schedulers, reliability engineers, supervisors, reliability technicians and crafts.
-
-
-
-
Sr. Section Manager - Site Maintenance and Reliability
-
2006 - 2008
The Sr. Section Manager reported directly to the site General Manager – VP was responsible for the central service including the Machine, Component Rebuild, Fabrication, and Paint Shop. Additionally, this department was responsible for the water treatment and waste facility, two return water barge operations and return water booster pump house. The reliability department reported to this department as well as all maintenance and reliability initiatives to be deployed site wide.
-
-
Section Manager Concentrator Maintenance
-
2005 - 2006
Led the maintenance planning, scheduling, reliability, and execution in the concentrator. In this position I had 8 direct reports and approximately 30 crafts. The concentrator department consisted of 9 autogenous mills, cyclone systems, vibrating screens, a combination of three and four foot separators, and associated equipment.
-
-
-
-
Business Support Manager - Mining
-
2004 - 2005
Prepared the budget for the mining department, generated the weekly and monthly cost reports, wrote the Requests for Appropriations for the mine capital equipment requests, and performed cost analysis for equipment justification.
-
-
Operations Coordinator and Maintenance Scheduler
-
2003 - 2004
As the maintenance scheduler I worked with the operating and maintenance departments in prioritizing, planning, and scheduling the available resource to assure we are working on the right equipment at the right time. Laid out the major repairs for the plants and created the GANTT charts in MS Project. Negotiated with the union’s contracting out committee for the justification for the use of contractors for both major rebuilds and emergency maintenance.
-
-
-
-
Site Predictive Maintenance Cordinator
-
2002 - 2003
-
-
Lead CMMS Implementation Coordinator
-
2002 - 2003
Lead implementation coordinator of Minntac’s Computerized Maintenance Management System (CMMS). I coordinated all implementation efforts for Minntac and facilitated between US Steel Corporate and Minntac to assure the implementation efforts were consistent with corporate standards. Our team Developed materials and delivered training for two locations.
-
-
Maintenance Shift Manager - Pellet Plant
-
2000 - 2002
Supervised two maintenance crews in the agglomerating department. My focus was on safety and efficiency with an emphasis on planned maintenance to maintain equipment reliability.
-
-
-
-
Maintenance Planner - Pellet Plant
-
1999 - 2000
Planned maintenance for 18 crafts people and two supervisors in the Agglomerating Departments. This area primarily consisted of five miles of conveyors, 8 - 8 x 10 double deck screens, 40+ slurry and fresh water pumps, vacuum systems, cooling water systems, pellet stacking and compressed air systems.
-
-
Operations Coodinator - Pellet Plant
-
Oct 1990 - 1999
-
-
Education
-
The College of St. Scholastica
MA, Management -
The College of St. Scholastica
BA, Business -
Mesabi Range Community College
AA, General Ed. -
Mesabi Community College
AAS, Marketing and Management
Community
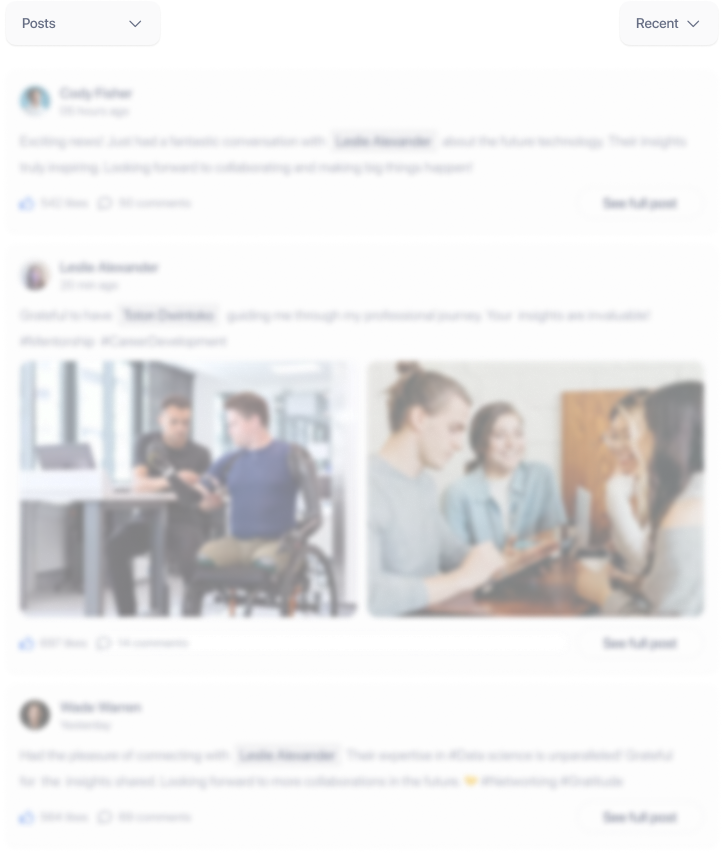