Dean Liakos
Chief Quality and Regulatory Officer at EQi Bio- Claim this Profile
Click to upgrade to our gold package
for the full feature experience.
-
English Native or bilingual proficiency
-
Greek Full professional proficiency
Topline Score
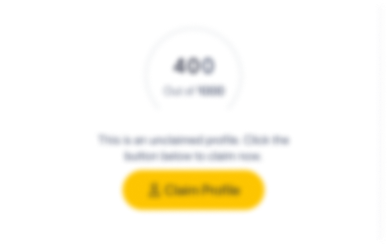
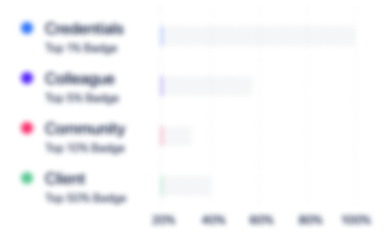
Bio

LinkedIn User
Dean is a highly motivational and dynamic team leader. I have had the pleasure of working along side of Dean for almost 5 years now. I hold him in high regards with respect to good managerial skills, exceptional leadership qualities and work ethics. As a Head of Quality & Regulatory manager, Dean displayed outstanding organisational and time management skills despite pressures exerted by multiple project deadlines. He is a team player and a great listener. He always carries himself in a calm, balanced way tackling any complex/ challenging situations. Dean is clearly interested in helping team members grow. Dean is not only a great people manager to work with but also a kind and a patient mentor who delegated tasks across the team in an efficient and professional manner. I am extremely thankful to have worked along with Dean. He is a great asset for any company he works for.

LinkedIn User
Dean came to Olympus as an experienced Quality Assurance and Regulatory Affairs Manager within the medical industry. His impact at Olympus was instant as he was immediately able to identify gaps within our QA/RA framework and set out to implement a strong QA/RA culture within our organisation including significant process overhaul, ultimately aimed at improving our quality management system. Dean worked superbly amongst various business units and the executive, a highlight being his approachability, clear communication and collaborative business approach which has played a large part in solidifying the importance of the QA/RA function within our organisation and embedding it as a cultural imperative within the way we work. I would openly recommend Dean Liakos to any organisation needing a world class QA/RA professional with a medical background, to drive this function within their organisation.

LinkedIn User
Dean is a highly motivational and dynamic team leader. I have had the pleasure of working along side of Dean for almost 5 years now. I hold him in high regards with respect to good managerial skills, exceptional leadership qualities and work ethics. As a Head of Quality & Regulatory manager, Dean displayed outstanding organisational and time management skills despite pressures exerted by multiple project deadlines. He is a team player and a great listener. He always carries himself in a calm, balanced way tackling any complex/ challenging situations. Dean is clearly interested in helping team members grow. Dean is not only a great people manager to work with but also a kind and a patient mentor who delegated tasks across the team in an efficient and professional manner. I am extremely thankful to have worked along with Dean. He is a great asset for any company he works for.

LinkedIn User
Dean came to Olympus as an experienced Quality Assurance and Regulatory Affairs Manager within the medical industry. His impact at Olympus was instant as he was immediately able to identify gaps within our QA/RA framework and set out to implement a strong QA/RA culture within our organisation including significant process overhaul, ultimately aimed at improving our quality management system. Dean worked superbly amongst various business units and the executive, a highlight being his approachability, clear communication and collaborative business approach which has played a large part in solidifying the importance of the QA/RA function within our organisation and embedding it as a cultural imperative within the way we work. I would openly recommend Dean Liakos to any organisation needing a world class QA/RA professional with a medical background, to drive this function within their organisation.

LinkedIn User
Dean is a highly motivational and dynamic team leader. I have had the pleasure of working along side of Dean for almost 5 years now. I hold him in high regards with respect to good managerial skills, exceptional leadership qualities and work ethics. As a Head of Quality & Regulatory manager, Dean displayed outstanding organisational and time management skills despite pressures exerted by multiple project deadlines. He is a team player and a great listener. He always carries himself in a calm, balanced way tackling any complex/ challenging situations. Dean is clearly interested in helping team members grow. Dean is not only a great people manager to work with but also a kind and a patient mentor who delegated tasks across the team in an efficient and professional manner. I am extremely thankful to have worked along with Dean. He is a great asset for any company he works for.

LinkedIn User
Dean came to Olympus as an experienced Quality Assurance and Regulatory Affairs Manager within the medical industry. His impact at Olympus was instant as he was immediately able to identify gaps within our QA/RA framework and set out to implement a strong QA/RA culture within our organisation including significant process overhaul, ultimately aimed at improving our quality management system. Dean worked superbly amongst various business units and the executive, a highlight being his approachability, clear communication and collaborative business approach which has played a large part in solidifying the importance of the QA/RA function within our organisation and embedding it as a cultural imperative within the way we work. I would openly recommend Dean Liakos to any organisation needing a world class QA/RA professional with a medical background, to drive this function within their organisation.

LinkedIn User
Dean is a highly motivational and dynamic team leader. I have had the pleasure of working along side of Dean for almost 5 years now. I hold him in high regards with respect to good managerial skills, exceptional leadership qualities and work ethics. As a Head of Quality & Regulatory manager, Dean displayed outstanding organisational and time management skills despite pressures exerted by multiple project deadlines. He is a team player and a great listener. He always carries himself in a calm, balanced way tackling any complex/ challenging situations. Dean is clearly interested in helping team members grow. Dean is not only a great people manager to work with but also a kind and a patient mentor who delegated tasks across the team in an efficient and professional manner. I am extremely thankful to have worked along with Dean. He is a great asset for any company he works for.

LinkedIn User
Dean came to Olympus as an experienced Quality Assurance and Regulatory Affairs Manager within the medical industry. His impact at Olympus was instant as he was immediately able to identify gaps within our QA/RA framework and set out to implement a strong QA/RA culture within our organisation including significant process overhaul, ultimately aimed at improving our quality management system. Dean worked superbly amongst various business units and the executive, a highlight being his approachability, clear communication and collaborative business approach which has played a large part in solidifying the importance of the QA/RA function within our organisation and embedding it as a cultural imperative within the way we work. I would openly recommend Dean Liakos to any organisation needing a world class QA/RA professional with a medical background, to drive this function within their organisation.

Credentials
-
Implementing ISO27001
BSIMar, 2022- Nov, 2024 -
Accredited Course in Management Systems Auditing
- -
Graduate Certificate of Management
Victoria University -
Risk management ISO14971:2007
-
Experience
-
EQi Bio
-
Australia
-
Biotechnology Research
-
1 - 100 Employee
-
Chief Quality and Regulatory Officer
-
Jun 2022 - Present
EQi Bio is an Australian start-up operating in the MedTech and IVD space through a novel technology suite. Currently in product development stage my role is to develop a QMS (utilizing an eQMS) from the ground up while developing Veterinary and Human Regulatory Strategies in regards to the IVD medical device being developed. Part of my role also include the Design and Development controls necessary to meet ISO13485 and 21 CFR part 820. EQi Bio is an Australian start-up operating in the MedTech and IVD space through a novel technology suite. Currently in product development stage my role is to develop a QMS (utilizing an eQMS) from the ground up while developing Veterinary and Human Regulatory Strategies in regards to the IVD medical device being developed. Part of my role also include the Design and Development controls necessary to meet ISO13485 and 21 CFR part 820.
-
-
-
Planet Innovation
-
Australia
-
Design
-
300 - 400 Employee
-
Head of Quality and Regulatory
-
Jan 2017 - Jul 2022
PI Design, Develop and Manufacture key technologies/products in the field of Biotech, such as Medical Devices, In Vitro Diagnostics (IVD) and In Vitro Fertilization (IVF). These developments/products are either our own or for our clients. I was responsible for leading the quality and regulatory team and ensuring overall management and company compliance of relevant regulatory requirements and ensuring that its certifications and licenses are always maintained. I had overall responsibility for the management of the Quality System to ensure ongoing compliance with current ISO13485 and 21 CFR Part 820 requirements as well as various other in country regulatory requirements. I was also the QA/RA Management Representative Achievements included long term strategic direction with regards to becoming a manufacturer of our own medical devices and IVD's (including high risk devices and SaMD's), while providing strategic advice for our clients and customers during development and contract manufacturing.
-
-
-
Fairmont Medical Products Pty Ltd
-
Australia
-
Medical Device
-
1 - 100 Employee
-
Quality Assurance and Regulatory Affairs Manager
-
Sep 2014 - Jan 2017
In this role, I had the responsibility of leading, coaching and mentoring the QA/RA team making sure we comply with all TGA and ISO13485 requirements, as well as having the responsibility of complying to international regulatory agencies such as the FDA (U.S.A) and MHRA (UK). Some of my responsibilities at Fairmont Medical include: - Overall implementation & compliance with ISO13485:2016 (Australia) - Ensuring the company’s auditing of the QMS is effective & up to date - Managing the Risk Analysis team & conducting risk analysis on medical devices - Project management – including marketing in new regulatory markets, designing new products, validating, and establishing a sterilising service for medical devices. - Implementing and maintaining change management system. - Completing Technical Files (and DHF's) used in Regulatory Submissions (TGA, FDA, Europe) - Overseeing the QMS Training process - Implementing, reviewing & approving the company’s controlled documentation system including external documentation - Liaising with TGA and ISO auditors
-
-
-
Olympus Australia and New Zealand
-
Australia
-
Medical Equipment Manufacturing
-
200 - 300 Employee
-
Regulatory Affairs & QA Manager
-
Oct 2013 - Sep 2014
In this role I had the responsibility for ensuring all medical devices are registered in accordance with TGA requirements as well as leading and developing a small team of 3 direct reports. Tasks included managing the quality assurance policies, consistent with ISO9001/ISO13485 and controlling new product development processes. During my tenure with Olympus, I established performance standards, processes and audit controls to meet the business requirements as well as identifying and implementing process improvements to increase the efficiency, effectiveness and quality of company operations.
-
-
-
ITL Health Group
-
Australia
-
Medical Device
-
1 - 100 Employee
-
Quality Assurance and Compliance Manager
-
Oct 2008 - Sep 2013
-Responsible for the overall implementation & compliance with ISO13485:2003 and ISO9001:2000-Ensure the company's auditing of the company's QMS is effective & up to date-Chairing product design, development & improvement meetings-Managing the Risk Analysis team & conducting risk analysis on medical devices-Project management - including designing new products, validations, and having to establish a sterilising service for medical devices. -Implementing and maintaining the change management system.-Initiate and revise the company's QMS to comply with regulatory authority requirements-Responsible for validation of sterilisation loads-Ensuring the sterilising part of the company adheres to the quality management system-Responsible for following regulatory requirements with regards to sterilisation -Responsible for handling customer complaints & the issuing of corrective action reports.-Ensure all monitoring of the total manufacturing process conforms to the company's QMS.-Manage and construct technical files used in TGA applications-Conduct QMS and GMP training with relevant personnel-Perform & ensure validation activities are undertaken -Implementing, reviewing & approving the company's controlled documentation system including external documentation-Responsible for implementing OH&S and ensuring all staff are trained and competent-Ensure the maintenance of a preferred supplier list-Liaising with TGA and ISO auditors
-
-
Production Manager
-
Aug 2010 - Mar 2011
-Overseeing production and drawing up a production schedule in accordance to MRP;-Ensuring that the production is cost effective;-Making sure that products are produced on time and are of good quality;-Calculating the human and material resources needed;-Drafting a timescale for each work order;-Estimating costs and setting quality standards;-Monitoring the production processes and adjusting schedules as needed;-Being responsible for the selection and maintenance of equipment;-Monitoring product standards and implementing quality-control programmes;-Liaising among different departments, e.g. suppliers, managers;-Working with managers to implement the company's policies and goals;-Ensuring that health and safety guidelines are followed;-Supervising and motivating the team;-Reviewing the performance of employees;-Identifying training needs-Risk Management
-
-
-
Fairmont Medical Products Pty Ltd
-
Australia
-
Medical Device
-
1 - 100 Employee
-
QA and Regulatory Affairs Manager
-
Jan 2005 - Jul 2008
-Responsible for the overall implementation & compliance with ISO13485:2003 and ISO9001:2000 -Ensure the company's auditing of the company's QMS is effective & up to date -Chairing product design, development & improvement meetings -Managing the Risk Analysis team & conducting risk analysis on medical devices -Project management - including designing new products, validations, and having to establish a sterilising service for medical devices. -Implementing and maintaining the change management system. -Initiate and revise the company's QMS to comply with regulatory authority requirements -Responsible for validation of sterilisation loads -Ensuring the sterilising part of the company adheres to the quality management system -Responsible for following regulatory requirements with regards to sterilisation -Responsible for handling customer complaints & the issuing of corrective action reports. -Ensure all monitoring of the total manufacturing process conforms to the company's QMS. -Manage and construct technical files used in TGA applications -Conduct QMS and GMP training with relevant personnel -Perform & ensure validation activities are undertaken -Implementing, reviewing & approving the company's controlled documentation system including external documentation -Responsible for implementing OH&S and ensuring all staff are trained and competent -Ensure the maintenance of a preferred supplier list -Liaising with TGA and ISO auditors
-
-
-
Mayne Pharma
-
Australia
-
Pharmaceutical Manufacturing
-
400 - 500 Employee
-
Quality Control/Operator
-
Jan 2003 - Oct 2003
Complying with GMP Machine Operating Preparation of production equipment (calibration, sterilisation) Reviewing release paperwork Updating SOP's and WI's Verification and Documentation (BRF) Quality Checking vials and paperwork Conducting line clearances Splitting batches for exportation Complying with GMP Machine Operating Preparation of production equipment (calibration, sterilisation) Reviewing release paperwork Updating SOP's and WI's Verification and Documentation (BRF) Quality Checking vials and paperwork Conducting line clearances Splitting batches for exportation
-
-
Education
-
Monash University
BSC, Pharmacology/Physiology -
Secondary
Community
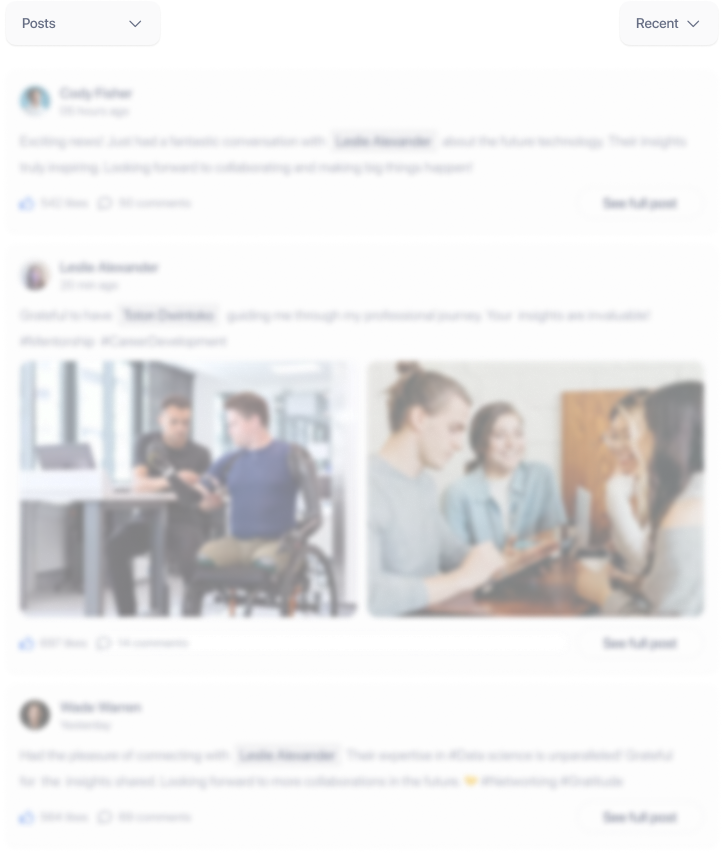