Damian B.
HCA at Coast Care Partners- Claim this Profile
Click to upgrade to our gold package
for the full feature experience.
-
English -
Topline Score
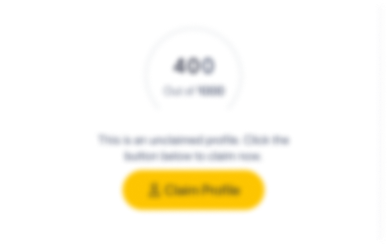
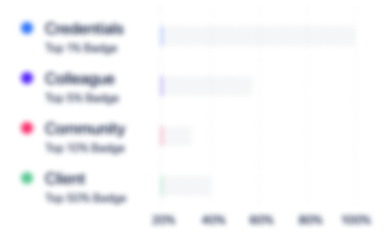
Bio


Experience
-
Coast Care Partners
-
United States
-
Individual and Family Services
-
1 - 100 Employee
-
HCA
-
Sep 2018 - Present
- In-Home Supportive Services; A Caregiver Who Cares. - In-Home Supportive Services; A Caregiver Who Cares.
-
-
-
Becton Dickinson Company (Safety Syringes, Inc. )
-
United States
-
Medical Equipment Manufacturing
-
300 - 400 Employee
-
Material Associate 2
-
Jul 2017 - Aug 2018
Performs manual and clerical duties related to shipping, receiving, storing, issuing, and delivering a variety of materials, equipment, and supplies.· Performs physical counts of inventory· Packs products for shipments· Transports materials between departments, facilities, and/or production floor· Transacts inventory/material movements in an accurate and timely manner and in accordance to strong inventory control practices.· Strong time management skills with an ability to multi-task· Selects and transacts materials for work orders and sales orders· Follow the federal and international regulations regarding hazardous substance transportation· Notify lead of any issues and discrepancies, research discrepancies and customer complaints· Assures the accurate counting, staging and storage of materials and supplies· Operates warehouse vehicles such as electric pallet jacks, pallet jacks, and related material handling equipment in narrow aisles and shipping docks· Follow all standard operation procedures and GMP guidelines· Adhere to all safety training and instructions and have knowledge of materials and safety· Ability to interpret instructions, specifications, etc. with minimal supervisionReceives incoming shipments and parts from freight carriers, examines returned goods and associated records to determine nature of return. Warehouses returned products for reconditioning, evaluation and loaner requirements. Assists in Shipping and other Service Depot areas as needed. Processes Service records affter product servicing, updates/verifies equipment records and lables as required by product updates, provides Supervisor/management with feedback on technician data quality as recorded on Service records, adjusts billable transactions as needed to meet customer requirement. Work with other department to process units and maintain shipping function, stock inventory on shipping area and maintains UPS equipment. Show less
-
-
Material Handler
-
Oct 2015 - Aug 2018
Follows instructions and works within routine, standard practices, making decisions as required. Works under direct supervision. Performs administrative and physical tasks involved in shipping, receiving, storing and supplying materials (raw, work-in-process, and finished goods), parts, and supplies, to operators, work stations and distribution center. Uses hand/or electric trucks (excluding forklifts). Keeps accurate logs (both written and electronic versions). Effectively works in a team setting, supporting team goals and objectives. Makes effective decisions relative to position requirements. Show less
-
-
-
CareFusion
-
United States
-
Medical Equipment Manufacturing
-
700 & Above Employee
-
Lead Material Handler/Inspector
-
Oct 2015 - Aug 2018
Quality inspectors work with manufacturing professionals during the production process, approving the quality of raw materials before, during and after manufacturing. 1. Approves incoming materials by confirming specifications; conducting visual and measurement tests; rejecting and returning unacceptable materials. 2. Approves in-process production by confirming specifications; conducting visual and measurement tests; communicating required adjustments to production supervisor. 3. Approves finished products by confirming specifications; conducting visual and measurement tests; returning products for re-work; confirming re-work. -Perform inspections, checks, tests, and sampling procedures of incoming materials, parts and components used in the manufacturing of electronic devices -Perform inspections of purchased parts, subassemblies or finished company products according to well defined criteria using standard physical, mechanical and/ or electrical measurements -Rework or reject subassemblies or finished products as required. -Conduct and document process and system audits using written procedures as audit standards -Accurately document the results of the inspections and testing.Maintain all controlled document files and test records in a timely and accurate manner -Coordinate calibration of all test equipment and fixtures -Monitor critical equipment and instrumentation to ensure proper operation and calibration -Participate in the construction and/or revision of SOPs for the inspection function -Assist in the writing and updating inspection procedures, protocol and checklists -Evaluate problems and make initial recommendations for possible corrective action to supervise -Work with production management and Quality Assurance to provide feedback to assemblers regarding accuracy of assembly procedures. -Perform review of Device History Records and other documentation for compliance to established procedures and Good Documentation Practices Show less
-
-
-
Alere Inc.
-
United States
-
Medical Device
-
700 & Above Employee
-
Manufacturing Technician
-
Jul 2016 - Aug 2016
Operate industrial semi-automated manufacturing equipment for the production and packaging of medical diagnostic intermediates and products. Successfully train and utilize computerized materials and inventory tracking systems with a high level of accuracy. Worked on assignments that are semi-routine in nature where ability to recognize deviation from accepted practice is required. Execute timely completion with high level of entry accuracy for Manufacturing Record Procedures (MRPs) associated with daily manufacturing runs. Responsible for performing and documenting routine equipment fault conditions and minor repair with on the job training. Track, verify and document all material part numbers and lot numbers used on production equipment. Perform area and equipment clearances as required for Good Manufacturing Procedure (GMP). Monitor machines and equipment to ensure they are operating and outputting at expected yields and throughput. Responsible for meticulous documentation for all aspects of machine operation, such as setup, operation and lot closure. Responsible for supporting new equipment validation. May require work with hazardous materials, including blood. Adheres to Alere's Quality Management System per ISO, FDA and other regulatory agencies. Accountable for the quality consequences which may occur from improper performance of the specific job. Identify defects that may occur in area of responsibility. Show less
-
-
-
RR Donnelley
-
United States
-
Advertising Services
-
700 & Above Employee
-
Print Press Feeder
-
Dec 2014 - Aug 2015
* Retrieve printing plates from platemaking department to the press for installation. * Assist with install of printing plates, packing sheets, packing blankets and inks. * Ensure paper is loaded in to feeders for running jobs, as well as maintain paper supply throughout the job run. * Provide basic assistance to Press Operator as needed to prepare press make-ready. * Adjust press machine parts of the feeder and delivery system. * Perform routine operational maintenance and minor repairs to equipment. * Remove and recycle old/discarded plates. Show less
-
-
-
The San Diego Union-Tribune
-
United States
-
Newspaper Publishing
-
200 - 300 Employee
-
Production/Machine Operator
-
Nov 2013 - Nov 2014
Worked on insert machine. Lifted bundles of inserts and placed into machines. Assembled and packaged products, stock clerk, Load and unload product. Data Entry as needed. Worked on insert machine. Lifted bundles of inserts and placed into machines. Assembled and packaged products, stock clerk, Load and unload product. Data Entry as needed.
-
-
-
-
Laborer/Kitchen Exhaust Cleaning
-
Sep 2011 - Apr 2012
Clean commercial kitchen exhaust system in all food service establishments and providing preventative maintenance to the systems to prevent fire hazards due to the buildup of grease laden vapors throughout the system. Clean commercial kitchen exhaust system in all food service establishments and providing preventative maintenance to the systems to prevent fire hazards due to the buildup of grease laden vapors throughout the system.
-
-
-
-
Cashier/Food Prep
-
May 2011 - Jul 2011
Assisted customers by providing information regarding menu. Received payment by cash, check, credit card or automatic debits. Prepared specialty foods and drinks according to specific methods. Packaged batches of food which are prepared to order or kept warm until sold. Assisted customers by providing information regarding menu. Received payment by cash, check, credit card or automatic debits. Prepared specialty foods and drinks according to specific methods. Packaged batches of food which are prepared to order or kept warm until sold.
-
-
-
-
Sandwich Artist/Cashier
-
Feb 2011 - May 2011
Cleaned and sanitized work areas, equipment and utensils. Stored food in designated containers and storage areas to prevent spoilage. Prepared a variety of sandwiches and salads according to customers’ orders or supervisors’ instructions, following approved procedures. Washed, peeled and cut various foods to prepare for cooking or serving Cleaned and sanitized work areas, equipment and utensils. Stored food in designated containers and storage areas to prevent spoilage. Prepared a variety of sandwiches and salads according to customers’ orders or supervisors’ instructions, following approved procedures. Washed, peeled and cut various foods to prepare for cooking or serving
-
-
-
-
Warehouse Assoc./ Assembly Line
-
May 2010 - Dec 2010
Performed general rough labor; assembled products for company; packaged and stocked them in warehouse for shipping; used such tools as a manual forklift, basic and some advanced hand and power tools; Lift 30-200 lbs constantly, daily. Performed general rough labor; assembled products for company; packaged and stocked them in warehouse for shipping; used such tools as a manual forklift, basic and some advanced hand and power tools; Lift 30-200 lbs constantly, daily.
-
-
-
-
Barista/ Cashier
-
Jul 2007 - Jun 2009
Exhibited what Starbucks calls “Excellent Customer Service” on all secret shoppers and regular customers; took on assistant manager duties for long period of time; open and closed down store using checklist of tasks each time to insure proper job was done; made customers drinks to ultimate satisfaction; cashier Exhibited what Starbucks calls “Excellent Customer Service” on all secret shoppers and regular customers; took on assistant manager duties for long period of time; open and closed down store using checklist of tasks each time to insure proper job was done; made customers drinks to ultimate satisfaction; cashier
-
-
Education
-
San Diego Continuing Education West-City Campus
GED, General Studies
Community
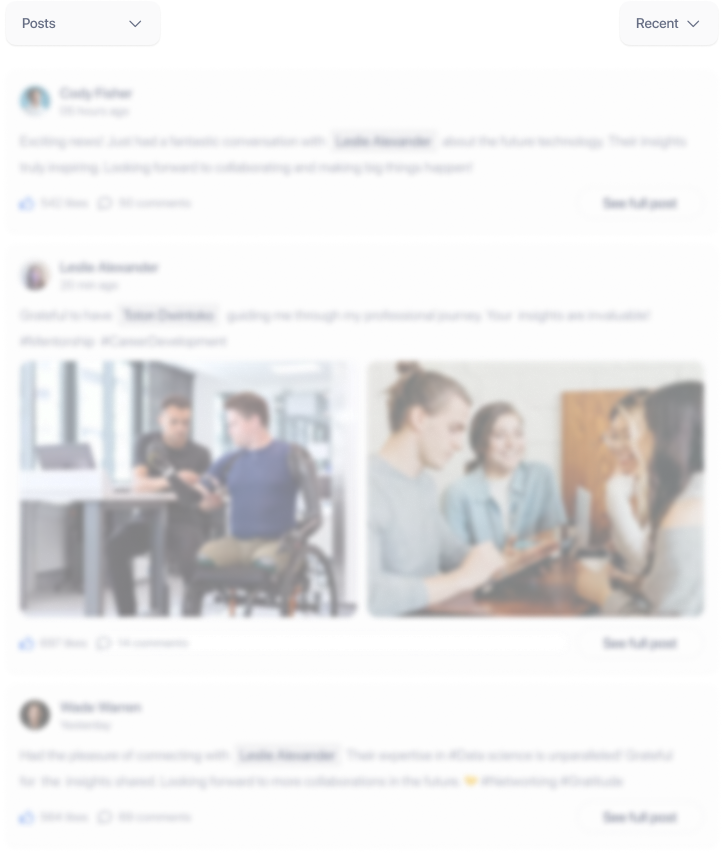