Dawn Middleton
Quality Manager at XLC Services- Claim this Profile
Click to upgrade to our gold package
for the full feature experience.
Topline Score
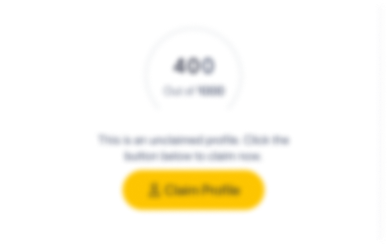
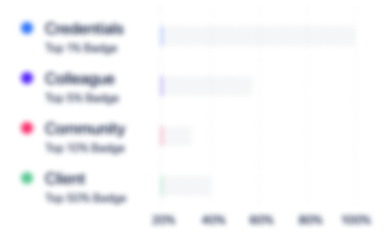
Bio

Brian Murphy, LSSMBB
Dawn is a detail-oriented Quality professional who is able to seamlessly merge the technical/statistical foundation of Quality with the understanding of the needs and desires of the consumer (VOC). I had the distinct pleasure of managing Dawn as we were both posted in Quality Control at Lorillard Tobacco (now ITG Brands). From her first day with the company, Dawn focused her attention on developing a mastery of all departmental tasks (and underlying manufacturing processes) so that she could add value in any role she was asked to fill in the department. It was this developed understanding that enabled her to play a vital role in the identification of incorrect machines setups that were costing the company $1.3 million a year in generated waste. Her work to implement solutions to correct the same assured that the company was able to return that money to the bottom line. Dawn has consistently taken on greater levels of responsibility within the scope of her job assignments and is comfortable in translating the reality on the shop floor into a business case for organizational leaders in order to focus attention on improvement needs. In most of these cases, she has been selected as the "go to person" for executing the changes required due to her level of knowledge and ability. I consider Dawn's departure from ITG Brands to be our loss; she is a conscientious, dedicated employee and would be an asset to any organization that considers hiring her. If you would like to discuss my experiences working with Dawn in greater detail, please do not hesitate to contact me through LinkedIn.

Brian Murphy, LSSMBB
Dawn is a detail-oriented Quality professional who is able to seamlessly merge the technical/statistical foundation of Quality with the understanding of the needs and desires of the consumer (VOC). I had the distinct pleasure of managing Dawn as we were both posted in Quality Control at Lorillard Tobacco (now ITG Brands). From her first day with the company, Dawn focused her attention on developing a mastery of all departmental tasks (and underlying manufacturing processes) so that she could add value in any role she was asked to fill in the department. It was this developed understanding that enabled her to play a vital role in the identification of incorrect machines setups that were costing the company $1.3 million a year in generated waste. Her work to implement solutions to correct the same assured that the company was able to return that money to the bottom line. Dawn has consistently taken on greater levels of responsibility within the scope of her job assignments and is comfortable in translating the reality on the shop floor into a business case for organizational leaders in order to focus attention on improvement needs. In most of these cases, she has been selected as the "go to person" for executing the changes required due to her level of knowledge and ability. I consider Dawn's departure from ITG Brands to be our loss; she is a conscientious, dedicated employee and would be an asset to any organization that considers hiring her. If you would like to discuss my experiences working with Dawn in greater detail, please do not hesitate to contact me through LinkedIn.

Brian Murphy, LSSMBB
Dawn is a detail-oriented Quality professional who is able to seamlessly merge the technical/statistical foundation of Quality with the understanding of the needs and desires of the consumer (VOC). I had the distinct pleasure of managing Dawn as we were both posted in Quality Control at Lorillard Tobacco (now ITG Brands). From her first day with the company, Dawn focused her attention on developing a mastery of all departmental tasks (and underlying manufacturing processes) so that she could add value in any role she was asked to fill in the department. It was this developed understanding that enabled her to play a vital role in the identification of incorrect machines setups that were costing the company $1.3 million a year in generated waste. Her work to implement solutions to correct the same assured that the company was able to return that money to the bottom line. Dawn has consistently taken on greater levels of responsibility within the scope of her job assignments and is comfortable in translating the reality on the shop floor into a business case for organizational leaders in order to focus attention on improvement needs. In most of these cases, she has been selected as the "go to person" for executing the changes required due to her level of knowledge and ability. I consider Dawn's departure from ITG Brands to be our loss; she is a conscientious, dedicated employee and would be an asset to any organization that considers hiring her. If you would like to discuss my experiences working with Dawn in greater detail, please do not hesitate to contact me through LinkedIn.

Brian Murphy, LSSMBB
Dawn is a detail-oriented Quality professional who is able to seamlessly merge the technical/statistical foundation of Quality with the understanding of the needs and desires of the consumer (VOC). I had the distinct pleasure of managing Dawn as we were both posted in Quality Control at Lorillard Tobacco (now ITG Brands). From her first day with the company, Dawn focused her attention on developing a mastery of all departmental tasks (and underlying manufacturing processes) so that she could add value in any role she was asked to fill in the department. It was this developed understanding that enabled her to play a vital role in the identification of incorrect machines setups that were costing the company $1.3 million a year in generated waste. Her work to implement solutions to correct the same assured that the company was able to return that money to the bottom line. Dawn has consistently taken on greater levels of responsibility within the scope of her job assignments and is comfortable in translating the reality on the shop floor into a business case for organizational leaders in order to focus attention on improvement needs. In most of these cases, she has been selected as the "go to person" for executing the changes required due to her level of knowledge and ability. I consider Dawn's departure from ITG Brands to be our loss; she is a conscientious, dedicated employee and would be an asset to any organization that considers hiring her. If you would like to discuss my experiences working with Dawn in greater detail, please do not hesitate to contact me through LinkedIn.

Credentials
-
Certified Quality Engineer
ASQJun, 2016- Oct, 2024 -
Certified Calibration Technician
ASQJan, 2015- Oct, 2024 -
Certified Quality Technician
ASQ
Experience
-
XLC Services
-
United States
-
Transportation, Logistics, Supply Chain and Storage
-
200 - 300 Employee
-
Quality Manager
-
Jan 2017 - Present
Analyze processes to determine areas for improvement and develop new efficient procedures. Perform Root Cause Analyses and CAPAs for non-conformities. Train all new employees on SOPs and ensure current employee trainings are up-to-date. Supervise inspectors, technicians and other staff and provide guidance and feedback. Analyze processes to determine areas for improvement and develop new efficient procedures. Perform Root Cause Analyses and CAPAs for non-conformities. Train all new employees on SOPs and ensure current employee trainings are up-to-date. Supervise inspectors, technicians and other staff and provide guidance and feedback.
-
-
-
ITG Brands
-
United States
-
Manufacturing
-
700 & Above Employee
-
Quality Control Tester/Examiner
-
Mar 2004 - Jul 2016
Assist tester/examiners, manufacturing operators and supervision with non-conforming product. Trainer on defects for tester/examiners. Provide Production Quality Control and manufacturing technical support: root cause analysis, SPC training, and defect clarification. Provided support for cross-training tester/examiners on PQC assignments. Played a key role on Stem Removal Reduction project which increased quality levels and saved the company more that $1 million annually. Assisted supervision in implementing new training procedures. Played a key role during the OMI installation and qualification project. Developed and actively maintained weekly and monthly OMI calibrations and PM's. Provided support and leadership when inspecting critical defects in the warehouse. WCOM Progressive Pillar team focused on identifying areas/causes of waste, provide opportunities for waste reduction and minimizing nonconforming product. Progressive Quality Pillar also focused on improving the knowledge of the quality program and individual ownership and accountability transforming the manufacturing facility from a "Quality Control" culture to "Quality Assurance" culture. WCOM Autonomous Management team focused on decreasing the downtime, improving quality and OEE on making complex.
-
-
-
Spantek
-
India
-
Food and Beverage Services
-
Assistant Supervisor
-
Sep 2002 - Mar 2004
Assisted supervision in monitoring process to assure conformance Assisted management in job shop scheduling of production orders to maximize machine proficiency Trained employees in machinery orientation/familiarity, adjustments, die changes and production of scheduled product to meet specifications Initiated and maintained safety and training programs Insured product being shipped was labeled correctly with product code, work order number, correct quantity, operators name and production date Performed customer visits to ensure receipt of "In-spec" materials
-
-
Education
-
Rockingham Community College
Computer Science
Community
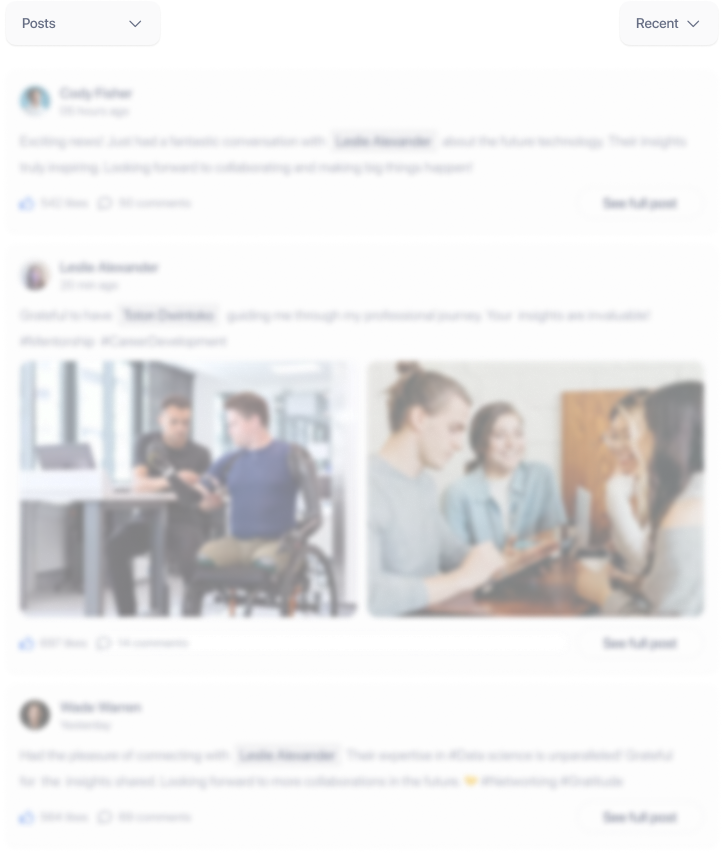