David C. Miller CMQ OE, CQT
Metrologist at Rochester Precision Optics- Claim this Profile
Click to upgrade to our gold package
for the full feature experience.
Topline Score
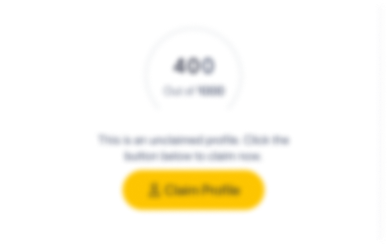
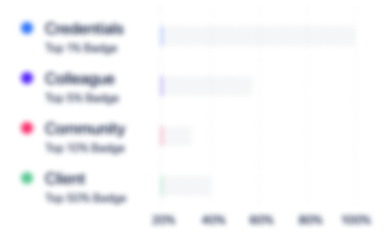
Bio

Mike Nichols
David is an outstanding employee with a good insight into Quality Assurance practices. He is a responsible, ethical individual who can be depended on to deliver every time.

Mike Nichols
David is an outstanding employee with a good insight into Quality Assurance practices. He is a responsible, ethical individual who can be depended on to deliver every time.

Mike Nichols
David is an outstanding employee with a good insight into Quality Assurance practices. He is a responsible, ethical individual who can be depended on to deliver every time.

Mike Nichols
David is an outstanding employee with a good insight into Quality Assurance practices. He is a responsible, ethical individual who can be depended on to deliver every time.

Credentials
-
Certified Manager of Quality/Organizational Excellence - ASQ
ASQ (American Society for Quality)Oct, 2014- Nov, 2024
Experience
-
Rochester Precision Optics
-
United States
-
Industrial Machinery Manufacturing
-
100 - 200 Employee
-
Metrologist
-
Jul 2017 - Present
Member of Molded Plastics Optics Team - Performing measurement of optical assembly components in order to produce quality products that represent exceptional value, are delivered on-time, and while striving to continuously improve. - Interferometer, 3D Profilometer, data analysis in support of Engineering using several digital metrology programs, standard gages. Member of Molded Plastics Optics Team - Performing measurement of optical assembly components in order to produce quality products that represent exceptional value, are delivered on-time, and while striving to continuously improve. - Interferometer, 3D Profilometer, data analysis in support of Engineering using several digital metrology programs, standard gages.
-
-
-
VIVA USA Inc.
-
United States
-
IT Services and IT Consulting
-
200 - 300 Employee
-
Training Analyst
-
Jan 2016 - Jul 2017
Analyst – Training CW VIVA USA Inc. Rochester NY 2016 – Current Leading global project for ISO 9001 certification in Training Quality at energy and utility company with operations in 25 states. 17 month assignment. • Created standard operating procedures using SAP Learning Solutions and integration of global corporate policy • Identified areas in which processes need improvement, including leading the first implementation of instructor and trainee course feedback critical for improvement. • Train and educate Management representative for successful handoff at end of assignment Show less
-
-
-
Seeking New Opportunities
-
For profit or Nonprofit
-
Process Improvement
-
Aug 2015 - Jan 2016
-
-
-
Ontario Plastics of NY Inc.
-
United States
-
Plastics Manufacturing
-
1 - 100 Employee
-
Quality System Manager
-
Feb 2014 - Aug 2015
Responsible for improvement of ISO-9001 based Quality System and direction of quality control (receiving, in-process, and final inspection) in support of daily production. 4 direct reports. •Management Rep for two surveillance audits with no nonconformances and registration maintained. •Greatly reduced waiting and motion waste in retained QC samples area by implementing 5S •Led writing and submission of critical PFMEA for key business services and document technology product customer, resulting in proceeding with order fulfillment. •For one quarter directed 40% understaffed QC inspection team in supporting production while successfully conducting 100% containment inspection for largest customer. Show less
-
-
-
JML Optical Industries, LLC
-
Pittsford, NY
-
Quality Assurance Technician
-
Jul 2012 - Feb 2014
Coordinator of all nonconforming product and related corrective actions (8D's) to customers. Facilitate material review and dispositions. Initiate Supplier Corrective Action Requests. Measure and inspect optical components and assemblies in ITAR Registered environment and ISO 9001:2008 Certified Quality System. Plan and conduct measurement systems analysis to assure integrity of results and prioritizing of improvement opportunities. •Achieved a 70% decrease in cycle time close-out of corrective actions and increased satisfaction for key 3D measurement technology customer •Used and taught concepts of repeatability and reproducibility to standardize key inspections of optical components and assemblies, reduce variation, and increase confidence in results. Show less
-
-
-
Gorbel
-
United States
-
Machinery Manufacturing
-
200 - 300 Employee
-
Manufacturing Manager
-
Jul 2007 - May 2011
Reporting to V.P. of Manufacturing, responsible for managing 4 factories (AL and NY), metal and component purchasing, production scheduling, and inventory control. Six direct reports. •Managed within combined labor, materials, and freight budget - the largest (at the time) sales year in the company’s history. •Six direct reports including two Plant Managers in support of four factories and multiple product lines. •Implemented first Safety Alert system and two OSHA metrics to drive safety improvement three consecutive years Show less
-
-
-
Westec Plastics Corporation
-
United States
-
Plastics Manufacturing
-
1 - 100 Employee
-
Quality Assurance Manager
-
2005 - 2006
Responsible for improvement of ISO-9001 based Quality System and direction of quality control (receiving, in-process, and final inspection) in support of daily production. QA Supervisor with 4 inspectors reported to me. •Communicated directly with and visited medical, consumer, biopharmaceutical customers in assuring quality. •Improved ISO-9001 Quality System per year-over-year audit results, thus assuring registration and avoiding additional compliance cost. Responsible for improvement of ISO-9001 based Quality System and direction of quality control (receiving, in-process, and final inspection) in support of daily production. QA Supervisor with 4 inspectors reported to me. •Communicated directly with and visited medical, consumer, biopharmaceutical customers in assuring quality. •Improved ISO-9001 Quality System per year-over-year audit results, thus assuring registration and avoiding additional compliance cost.
-
-
-
FedEx Office
-
United States
-
Printing Services
-
700 & Above Employee
-
Center Manager
-
2004 - 2005
Focused on creating a consistent and positive customer experience. Supervised all team members and business operations, monitored fulfillment of all production and retail processes, pick-up and delivery, shipping and quality control processes. • Achieved three consecutive months of Mission Statement Measurement improvement for the first time in prior three years Focused on creating a consistent and positive customer experience. Supervised all team members and business operations, monitored fulfillment of all production and retail processes, pick-up and delivery, shipping and quality control processes. • Achieved three consecutive months of Mission Statement Measurement improvement for the first time in prior three years
-
-
-
Saint-Gobain
-
France
-
Wholesale Building Materials
-
700 & Above Employee
-
Technical Manager, then Senior Quality Manager
-
Jun 1997 - Jun 2004
As Senior Quality Manager managed quality leaders in 2 U.S. plants and one Canadian plant in preparation for centralization and corporate registration to ISO-9001. Also led quality planning for NC start-up operation. 5 direct reports. As Technical Manager in Albion responsible for ISO-9001 based quality system improvement and environmental compliance. • Retained sole supplier contract from largest manufacturer of residential windows by writing and facilitating implementation of quality plan • Secured strategic partnership with key commercial roofing customer with collaborative design FMEA • On special assignment from President completed first comprehensive training of 12 Customer Service Reps with documenting of SAP ERP upgrade and ISO-9001 based reorg. • Increased uptime for key forming and coating machinery by leading Total Productive Maintenance learning initiative and implementation of Autonomous Maintenance. • Improved resource yield by designing and implementing project management visibility process. • Mentored Quality Technician to fill Quality Manager position in largest North American plant without increasing headcount. • Obtained first NYSDEC Title V air permit to enable plant’s growth by establishing compliance calendar and creating a system for regulatory document storage and retrieval Show less
-
-
-
Diamond Packaging
-
United States
-
Packaging and Containers Manufacturing
-
1 - 100 Employee
-
Production Supervisor, then Quality & EE Development Mgr.
-
Jun 1990 - Jun 1997
As Production Supervisor supervised 22 direct reports in 3rd Shift Pre-Make Ready, Converting, and Finishing departments. Promoted to Quality & EE Development Mgr reporting to V.P. of Manufacturing with responsibility for achieving first ISO-9001 registration, collaborating with Sales to assure customer satisfaction, quality control (receiving, in-process test and inspection), and improving employee math and English literacy. • As management rep facilitated first registration to ISO-9001 which was a strategic initiative necessary for obtaining global business. • Increased critical fill rates for biggest customer by implementing SPC on key characteristic in conversion processes. • Improved workforce math and reading literacy necessary for Quality System, with on-time and to budget purchasing of outside services. • Eliminated costs of express shipments and associated downtime with design and implementation of visual self-serve critical parts system. • Reduced external failures and reduced quality costs to all-time low by implementing Cost of Quality in collaboration with Accounting. Show less
-
-
-
Deridder Inc.
-
Rochester, New York Area
-
Production Manager
-
1988 - 1990
Lone management presence on 2nd shift and responsible for plant security, accurate and thorough shift-to-shift communication, meeting production schedule and quality requirements including press approvals with customer. Six direct reports. • Improved efficiency of Stripping Department by reorganizing materials floor plan, instituting production reporting system, and the selection and development of group leaders and teams. Lone management presence on 2nd shift and responsible for plant security, accurate and thorough shift-to-shift communication, meeting production schedule and quality requirements including press approvals with customer. Six direct reports. • Improved efficiency of Stripping Department by reorganizing materials floor plan, instituting production reporting system, and the selection and development of group leaders and teams.
-
-
-
Quality Packaging Supply
-
Packaging and Containers Manufacturing
-
1 - 100 Employee
-
Asst. Plant Manager, Production Manager
-
1976 - 1988
Hired as Asst. Plant manager and successor to Plant Manager. As company rapidly grew took on focused Production Manger position with responsibility for meeting customer timeliness requirements, staffing, quality requirements and the critical manufacturing and converting of packaging solutions. Supervised 30, and then managed 3 Department Supervisors while reporting to V.P. Mfg. • Increased on-time deliveries by 50% as member of production control team by implementing first scheduling system using computer generated job tracking. • Developed and documented on-line inspection process for critical safety product that resulted in obtaining multi-million dollar contract. • Increased profitability by developing visual process for efficiently utilizing most expensive raw material off-cuts. • Generated cost savings averaging 75% on outbound freight by renegotiating contracts with common carriers. Show less
-
-
-
Mobil Chemical Company
-
United States
-
Chemical Manufacturing
-
100 - 200 Employee
-
Maintenance Tech., QC Inspector, Operator
-
1975 - 1976
My first paid full-time job as member of Maintenance team. • Extruder heat exchanger cleaning, Inspection, 4 color in-line extruder, flexo press Operator My first paid full-time job as member of Maintenance team. • Extruder heat exchanger cleaning, Inspection, 4 color in-line extruder, flexo press Operator
-
-
Education
-
Monroe Community College
Precision Machining for Optics -
Rochester Institute of Technology
Quality Management -
5 Steps
-
5 Steps
Community
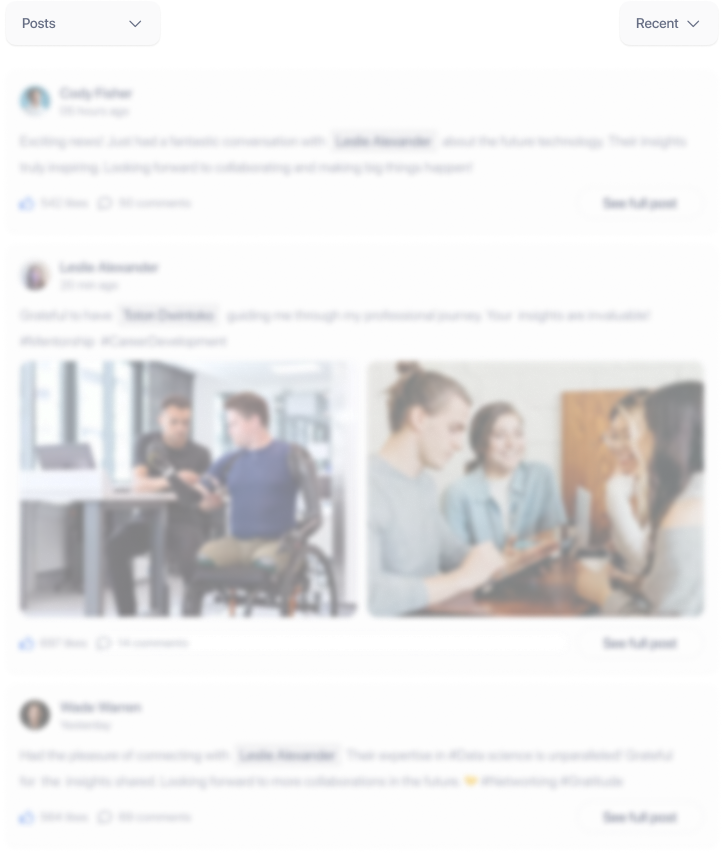