David Atwood
Vice President of Business Development at RenewGas Transportation- Claim this Profile
Click to upgrade to our gold package
for the full feature experience.
Topline Score
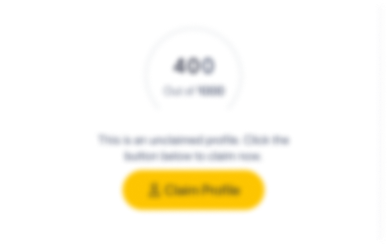
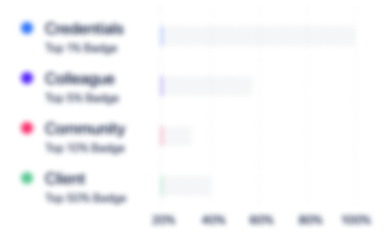
Bio
0
/5.0 / Based on 0 ratingsFilter reviews by:
Experience
-
RenewGas Transportation
-
United States
-
Truck Transportation
-
1 - 100 Employee
-
Vice President of Business Development
-
Mar 2023 - Present
-
-
-
Compass Natural Gas
-
United States
-
Oil and Gas
-
1 - 100 Employee
-
-
Jan 2020 - Feb 2023
● Responsible for all aspects of company transportation operations as well as managing the sales force and prospecting and negotiating special projects● Continued to pursue initiatives to cut costs, boost revenue, and facilitate growth● Grew the sales force and procured resources to expand into oil & gas field work in Pennsylvania and Ohio; continued to manage the company sales efforts ● Negotiated agreements to source additional equipment for special projects● Expanded transportation fleet to 36 CNG trailers, 9 power units, and 9 drivers● Pursued and negotiated hauling agreements with 3rd party carriers to handle overflow hauling ● On-track to deliver over 1BCF of gas in 2022, as well as record revenue and EBITDA Show less
-
-
-
Mar 2019 - Jan 2020
● Responsible for all aspects of company operations and strategic growth plans ● Overhauled and streamlined operations and cut approximately $1MM from annual SG&A and operating expenses● Cut the workforce by 40% while improving company performance and fostering improved employee collaboration● Grew company revenue and profitability to record levels in 2019● Expanded transportation fleet to 29 CNG trailers, 7 power units, and 9 company drivers● Negotiated and signed contracts to fill company trailers at 3rd party filling sites, cutting costs to long-distance customers and expanding the company network throughout Ohio and West Virginia Show less
-
-
-
Dec 2015 - Mar 2019
• Grew delivery fleet to 26 CNG tankers and 6 power units • Serviced industrial and fleet accounts in Pennsylvania, Ohio, and Kentucky, totaling over 500,000 MMBtu annually, as well as on-call utility and drill site work • Manage the capital spending, forecasting, and staffing of the Logistics Dept.• In conjunction with the Transportation Manager, manage the day-to-day deliveries and equipment moves to support the Operations Dept. • Responsible for record-keeping, DOT compliance, maintenance, and operation of all company rolling stock (CNG delivery vehicles and tankers as well as support equipment and trailers).• Responsible for hiring, training, and DOT compliance of company drivers• Negotiate with and manage 3rd party carriers• Negotiate with rolling stock vendors and OEMs (i.e. Hexagon Lincoln, Mack, Freightliner, Agility Systems, etc.)• Generate monthly KPIs and review with staff and Compass management• Manage client relationships with regard to deliveries, consumption, site layout, and conditions • Responsible for the job safety of company drivers and company delivery operations• Support the sales process by discussing delivery operations, monitoring, consumption, and forecasting with prospective customers • Responsible for managing the Compass gas terminal in Montoursville, PA (Quaker), a 4BCF per year gas compressing facility with four full-time employees Show less
-
-
-
Xpress Natural Gas
-
United States
-
Oil and Gas
-
1 - 100 Employee
-
Vice President of Operations
-
Nov 2013 - Jul 2015
● Responsible for all aspects of facility operations, transportation, rolling stock and fixed asset maintenance, safety, department budgeting/forecasting, and state/federal/DOT compliance, with direct hiring, training, management and supervisory authority over all company drivers, terminal operators, dispatchers, maintenance technicians and managers. ● Managed three 24/7 manned CNG terminals in Maine and New York. ● Launched a computerized maintenance management system (CMMS) to track all preventative and corrective maintenance on mobile equipment and company facilities. ● Implemented continuous improvement program for scheduling and dispatching systems and procedures that allowed the company to double delivery volumes from 2013 to 2014 and double again in 2015. ● Established the XNG trucking division with company drivers and tractors in September 2014; by July 2015, fleet had grown to 45 Titan trailers, 5 CNG-powered tractors, and 13 drivers, with more drivers and tractors poised to come online. ● In conjunction with the launch of the XNG trucking division, created driver policies and procedures and a comprehensive training program involving classroom and field instruction for all new drivers. ● Led company through a comprehensive DOT audit in January 2015, resulting in a “Satisfactory” rating (highest DOT rating available). ● Worked with New Brunswick Gas Board and Transport Canada to obtain approval for training and testing materials and to secure XNG licensure to deliver CNG to customers in New Brunswick, Canada. ● Created Emergency Response Action Plans (ERAPs) for customers in New Brunswick and Prince Edward Island and individualized Emergency Response Plans (ERPs) for customers throughout New England. ● Implemented 24/7 site and delivery monitoring system by cross-training terminal operators and utilizing automated programs and GPS vehicle tracking; put additional procedures in place to eliminate driver errors at customer sites. Show less
-
-
-
Schnitzer Steel
-
United States
-
Mining
-
700 & Above Employee
-
-
Jun 2013 - Nov 2013
● Responsible for the daily operation of six feeder yards/transfer stations in the state of NH● Responsible for a 2,500HP boutique shredder, extensive rail operations, metal baling, and non-ferrous metal purchasing, processing, and sales● Changed the monthly breakeven/loss at the shredder to monthly profits of $100,000 + by finding new sources of feed stock, outlets for new finished products, and increasing the volume to drive down the per unit cost to process● Instituted new safety procedures and management tools to better utilize equipment and improve production planning● Launched program to acquire necessary equipment while simultaneously dismantling and selling under-utilized or obsolete equipment Show less
-
-
-
Oct 2009 - Jun 2013
● Responsible for the daily operation of a 30-acre processing center and export terminal - the largest facility of its kind in New England, with 11 supervisors and managers and 85 union and non-union employees ● Coordinated the annual loading of approximately 1,000,000 tons of ferrous steel on ocean-going cargo ships from the on-site deep-water dock ● Organized the annual loading of approximately 72,000,000 lbs. of non-ferrous metals into cargo containers ● Oversaw the construction and operation of an $18MM non-ferrous metal processing plant● Managed a $30MM mega-shredder, producing over 400,000 tons of ferrous steel annually ● Oversaw numerous R&D projects and facility upgrades ● In 2012, the facility won the annual award for Distinguished Promotion of the Port of Boston by the Boston Propeller Club Show less
-
-
-
Sep 2006 - Oct 2009
● Responsible for the creation, maintenance, and growth of a ground logistical network that eventually encompassed 11 company-owned supplier yards across Massachusetts, Rhode Island, New Hampshire, and Maine, hundreds of independent suppliers across the greater Northeast, 2 production hubs, 2 deep-water port facilities, and 5 rail heads. ● Coordinated the loading, unloading, dispatch, and maintenance of 180 company-owned and operated railroad cars.● Oversaw the daily dispatch of 21 company-operated trucks and over 200 independent trucks. ● Negotiated lease terms and rates with independent trucking companies, railroads, and other service providers.● Drafted and implement policies and Standard Operating Procedures for logistical functions and personnel.● Researched, introduced, and implemented a GPS system to track all company tractors, trailers, and mobile processing equipment.● Co-Chair of the Schnitzer Steel National Supply Chain and Logistics Committee.● Renegotiated waste disposal contracts that reduced costs by over $6,000,000 in a 2.5 years. ● Supervised 6 direct reports and over 45 subordinates. Show less
-
-
-
Aggregate Industries
-
United Kingdom
-
Construction
-
700 & Above Employee
-
Transportation Manager (Paving Division)
-
Jul 2005 - Sep 2006
● Responsible for providing all logistical support for paving operations in the Northeast Region, including contracting with independent truck owners/operators, scheduling 24-hour operations, and identifying opportunities to streamline processes and improve efficiency. ● Daily responsibilities included coordinating delivery of @15,000 tons of stone from 9 quarries to 19 asphalt plants and 23 concrete plants, @10,000 tons of stone to private customers throughout New England, @15,000 tons of asphalt from plants to multiple paving job sites, and the transportation of @10,000 tons of asphalt millings from job sites to asphalt plants for recycling. ● Increased independent trucking fleet by more than 20% over YTD 2004, to over 300 trucks scheduled per 24-hour period, through use of a professional business approach and active recruiting. ● Used leadership skills to instill pride in mission accomplishment, improved morale, and significantly reduced annual turnover from @ 400% to zero. ● Created tracking system to charge delinquent trucks to discourage absenteeism and recoup costs of production delays. ● Reported to the Regional President and Managing Committee, on a regular basis, on status of trucking fleet and capability to meet operational demands. ● Supervised 5 direct reports. Show less
-
-
-
United States Marine Corps
-
United States
-
Armed Forces
-
700 & Above Employee
-
-
Aug 2002 - Sep 2004
● Primarily responsible for maintaining all equipment in combat-ready condition for Marine Forces Reserve, the largest Marine Expeditionary Force in the Marine Corps.● Appointed to Strategic Command Action Center (SCAC) during reservist mobilization for Operation Iraqi Freedom. Responsibilities included resolving logistics issues and providing daily briefs to Commanding General. ● Created and implemented equipment demobilization plan for return of 20,000 Marine reservists and over 1,000 major end items from Operation Iraqi Freedom. Show less
-
-
-
Jul 2000 - Aug 2002
● Primarily responsible for all maintenance and tactical logistics for a front-line infantry battalion and, during subsequent deployment and combat operations, for an entire Battalion Landing Team, with attached combat engineer, light and heavy armored assets, and Marine Force Reconnaissance Commando detachment. ● Deployed to Pakistan and Afghanistan as part of Operation Enduring Freedom
-
-
-
Jun 1999 - Jul 2000
● Directly responsible for all aspects of a 40-Marine transportation platoon with respect to operations, maintenance, morale, and combat-readiness; participated in extensive training exercises in Thailand
-
-
Education
-
Northeastern University - Graduate School of Business Administration
M.A., Business Administration -
The Citadel Military College of S.C.
B.S., Business Administration
Community
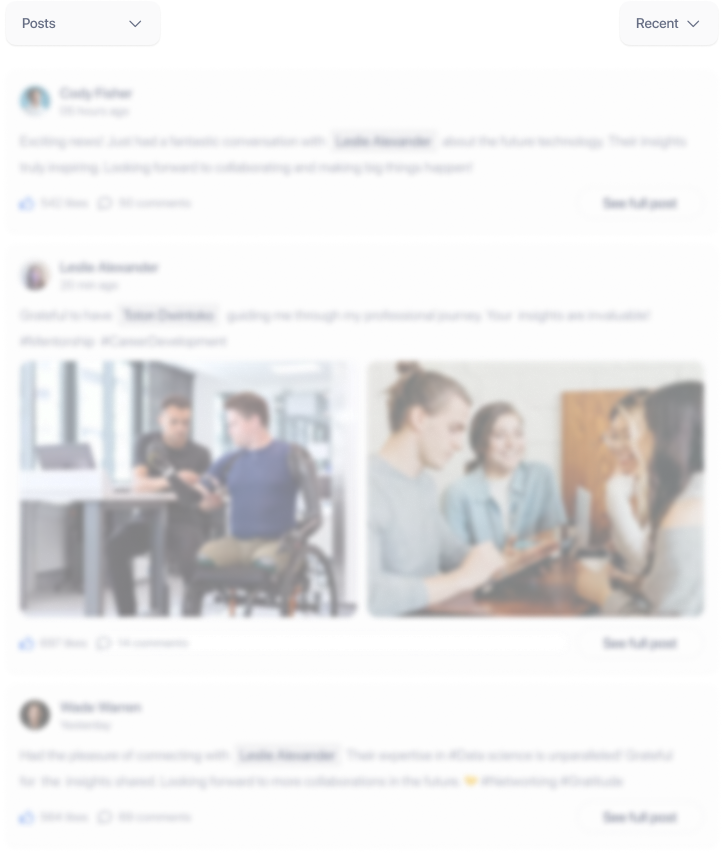