David Zaffino
Program Manager at Viking Plastics- Claim this Profile
Click to upgrade to our gold package
for the full feature experience.
Topline Score
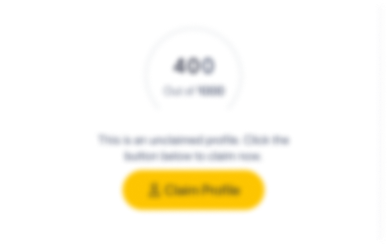
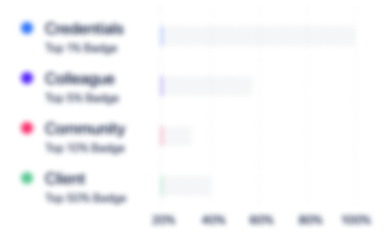
Bio


Experience
-
Viking Plastics
-
United States
-
Plastics Manufacturing
-
1 - 100 Employee
-
Program Manager
-
Aug 2019 - Present
-
-
-
Truck-Lite
-
United States
-
Truck Transportation
-
100 - 200 Employee
-
Tooling Engineer
-
Jan 2018 - Aug 2019
Starting a new chapter; working for the large truck industry focusing on top quality molds to manufacture headlights, side marker and brake lights, and mirrors. Truck-Lite doe complete product development and testing to supply the full assemblies to all major manufacturers of Over The Road trucks and trailers. Starting a new chapter; working for the large truck industry focusing on top quality molds to manufacture headlights, side marker and brake lights, and mirrors. Truck-Lite doe complete product development and testing to supply the full assemblies to all major manufacturers of Over The Road trucks and trailers.
-
-
-
Technimark/Ci Medical Technologies.
-
Latrobe, PA
-
Plastics Engineer
-
May 2016 - Dec 2017
Ci Medical develops medical parts from concept to production. We work with the customer to achieve the most robust product design possible. We manufacture a world class mold to produce the products in one of our four clean rooms, to turn that design into reality. Ci Medical, now part of TECHNIMARK, prides itself on superior quality of every part we produce. No job is too big or small nor are they too complex for us to bring your dream to fruition. We work with world class tool shops using… Show more Ci Medical develops medical parts from concept to production. We work with the customer to achieve the most robust product design possible. We manufacture a world class mold to produce the products in one of our four clean rooms, to turn that design into reality. Ci Medical, now part of TECHNIMARK, prides itself on superior quality of every part we produce. No job is too big or small nor are they too complex for us to bring your dream to fruition. We work with world class tool shops using fine U.S. steel to assure the quality of every part we deliver. Show less Ci Medical develops medical parts from concept to production. We work with the customer to achieve the most robust product design possible. We manufacture a world class mold to produce the products in one of our four clean rooms, to turn that design into reality. Ci Medical, now part of TECHNIMARK, prides itself on superior quality of every part we produce. No job is too big or small nor are they too complex for us to bring your dream to fruition. We work with world class tool shops using… Show more Ci Medical develops medical parts from concept to production. We work with the customer to achieve the most robust product design possible. We manufacture a world class mold to produce the products in one of our four clean rooms, to turn that design into reality. Ci Medical, now part of TECHNIMARK, prides itself on superior quality of every part we produce. No job is too big or small nor are they too complex for us to bring your dream to fruition. We work with world class tool shops using fine U.S. steel to assure the quality of every part we deliver. Show less
-
-
-
Controlled Molding, Incorporated
-
Hadley, PA
-
Project/Design Engineer
-
Jun 2011 - Apr 2016
Design and build plastic injection molds, sample, and run production for low to high volume products in automotive, consumer, and medical industries. Design and build custom assembly equipment. Design and enhance designs of customers' products for optimum performance and durability. Design and build plastic injection molds, sample, and run production for low to high volume products in automotive, consumer, and medical industries. Design and build custom assembly equipment. Design and enhance designs of customers' products for optimum performance and durability.
-
-
-
-
Tool Engineer
-
Apr 2010 - Jun 2011
Evaluate part drawings to establish mold design. Supervise and track progress of design, oversee mold construction and assure milestones are met, attend initial sample and develop plan to meet customer expectations are met, work with process engineering to establish a robust and repeatable process, and work with quality control to assure dimensions and tolerances are held. . Helped complete, sample, and deliver 10 of 19 products to customer that were late. Develop system to increase… Show more Evaluate part drawings to establish mold design. Supervise and track progress of design, oversee mold construction and assure milestones are met, attend initial sample and develop plan to meet customer expectations are met, work with process engineering to establish a robust and repeatable process, and work with quality control to assure dimensions and tolerances are held. . Helped complete, sample, and deliver 10 of 19 products to customer that were late. Develop system to increase accountability for critical project milestones. Reduced tool change-over times by 25% by creating instruction manual for family molds and storage system for inserts. Show less Evaluate part drawings to establish mold design. Supervise and track progress of design, oversee mold construction and assure milestones are met, attend initial sample and develop plan to meet customer expectations are met, work with process engineering to establish a robust and repeatable process, and work with quality control to assure dimensions and tolerances are held. . Helped complete, sample, and deliver 10 of 19 products to customer that were late. Develop system to increase… Show more Evaluate part drawings to establish mold design. Supervise and track progress of design, oversee mold construction and assure milestones are met, attend initial sample and develop plan to meet customer expectations are met, work with process engineering to establish a robust and repeatable process, and work with quality control to assure dimensions and tolerances are held. . Helped complete, sample, and deliver 10 of 19 products to customer that were late. Develop system to increase accountability for critical project milestones. Reduced tool change-over times by 25% by creating instruction manual for family molds and storage system for inserts. Show less
-
-
-
-
Process Technical Advisor/Flow Leader
-
Jun 2007 - Apr 2009
Manage and coordinate work for third shift assembly workers on Lean Manufacturing assembly line. Maintain shipping schedule of finished goods, update incoming product information from internal suppliers, and report daily progress for production control and productivity. Conduct weekly informative safety meetings to all third shift employees. Helped establish Lean Assembly Line for auxiliary cabs for freight locomotives by implementing standard work and material presentation to streamline… Show more Manage and coordinate work for third shift assembly workers on Lean Manufacturing assembly line. Maintain shipping schedule of finished goods, update incoming product information from internal suppliers, and report daily progress for production control and productivity. Conduct weekly informative safety meetings to all third shift employees. Helped establish Lean Assembly Line for auxiliary cabs for freight locomotives by implementing standard work and material presentation to streamline assembly process. Increased productivity (Takt attainment) by 25% of Lean Line throughout 2008. Reduced first aid injuries by 50% through weekly safety meeting with shift employees. Show less Manage and coordinate work for third shift assembly workers on Lean Manufacturing assembly line. Maintain shipping schedule of finished goods, update incoming product information from internal suppliers, and report daily progress for production control and productivity. Conduct weekly informative safety meetings to all third shift employees. Helped establish Lean Assembly Line for auxiliary cabs for freight locomotives by implementing standard work and material presentation to streamline… Show more Manage and coordinate work for third shift assembly workers on Lean Manufacturing assembly line. Maintain shipping schedule of finished goods, update incoming product information from internal suppliers, and report daily progress for production control and productivity. Conduct weekly informative safety meetings to all third shift employees. Helped establish Lean Assembly Line for auxiliary cabs for freight locomotives by implementing standard work and material presentation to streamline assembly process. Increased productivity (Takt attainment) by 25% of Lean Line throughout 2008. Reduced first aid injuries by 50% through weekly safety meeting with shift employees. Show less
-
-
-
-
Tooling Engineer
-
Jan 2000 - Feb 2007
Manufacturer of plastic automotive interior and exterior components including decorative trim and structural support components. Manufacturer of plastic automotive interior and exterior components including decorative trim and structural support components.
-
-
-
-
Tooling Engineer
-
Jan 2000 - Jan 2007
Scheduled and coordinated all preventative maintenance (PM), repairs, and engineering changes to injection molds using outside tool shops. Generated concepts for new injection mold designs and engineering changes for outside tool shops. Organized repairs and modifications to injection molds for quality control compliance with customers, scheduling, and production control. Worked directly as engineering support with customers on new product development. Created, maintained, and updated… Show more Scheduled and coordinated all preventative maintenance (PM), repairs, and engineering changes to injection molds using outside tool shops. Generated concepts for new injection mold designs and engineering changes for outside tool shops. Organized repairs and modifications to injection molds for quality control compliance with customers, scheduling, and production control. Worked directly as engineering support with customers on new product development. Created, maintained, and updated PM schedule of production and service injection molds. Reduced monthly expense for repairs and PM's from $18,000.00 to $12,000.00. Established and developed mold design and mold construction standards for consistent interface with molding machines and mold construction quotes. Reduced start up time of new molds from 8 - 10 hours to four hours. Performed small mold repairs to reduce costs during economic downturn. Saved the mold repair budget an additional $3,000.00 to $5,000.00 per month. Show less Scheduled and coordinated all preventative maintenance (PM), repairs, and engineering changes to injection molds using outside tool shops. Generated concepts for new injection mold designs and engineering changes for outside tool shops. Organized repairs and modifications to injection molds for quality control compliance with customers, scheduling, and production control. Worked directly as engineering support with customers on new product development. Created, maintained, and updated… Show more Scheduled and coordinated all preventative maintenance (PM), repairs, and engineering changes to injection molds using outside tool shops. Generated concepts for new injection mold designs and engineering changes for outside tool shops. Organized repairs and modifications to injection molds for quality control compliance with customers, scheduling, and production control. Worked directly as engineering support with customers on new product development. Created, maintained, and updated PM schedule of production and service injection molds. Reduced monthly expense for repairs and PM's from $18,000.00 to $12,000.00. Established and developed mold design and mold construction standards for consistent interface with molding machines and mold construction quotes. Reduced start up time of new molds from 8 - 10 hours to four hours. Performed small mold repairs to reduce costs during economic downturn. Saved the mold repair budget an additional $3,000.00 to $5,000.00 per month. Show less
-
-
-
-
Tooling Engineer & Program Manager
-
May 1998 - Jan 2000
Maintained and updated preventative maintenance schedule of production and service injection molds and transfer dies. Managed programs for several customers of new injection mold and transfer die designs, for new construction and engineering changes. Assisted in product development with several customers to achieve best quality product. Supervised three-person internal tool repair facility and several external mold repair shops daily. - Created, maintained, and updated PM schedule of… Show more Maintained and updated preventative maintenance schedule of production and service injection molds and transfer dies. Managed programs for several customers of new injection mold and transfer die designs, for new construction and engineering changes. Assisted in product development with several customers to achieve best quality product. Supervised three-person internal tool repair facility and several external mold repair shops daily. - Created, maintained, and updated PM schedule of production and service injection molds. Reduced monthly expense for repairs and PM’s by approximately $3,000.00. ·- Participated in several Kaizon events. One event netted a savings of $250,000.00 over a three-year production run at a total cost of $25,000.00. Show less Maintained and updated preventative maintenance schedule of production and service injection molds and transfer dies. Managed programs for several customers of new injection mold and transfer die designs, for new construction and engineering changes. Assisted in product development with several customers to achieve best quality product. Supervised three-person internal tool repair facility and several external mold repair shops daily. - Created, maintained, and updated PM schedule of… Show more Maintained and updated preventative maintenance schedule of production and service injection molds and transfer dies. Managed programs for several customers of new injection mold and transfer die designs, for new construction and engineering changes. Assisted in product development with several customers to achieve best quality product. Supervised three-person internal tool repair facility and several external mold repair shops daily. - Created, maintained, and updated PM schedule of production and service injection molds. Reduced monthly expense for repairs and PM’s by approximately $3,000.00. ·- Participated in several Kaizon events. One event netted a savings of $250,000.00 over a three-year production run at a total cost of $25,000.00. Show less
-
-
-
-
Lead Tool Engineer/Engineering Manager
-
Jan 1996 - May 1998
Coordinated, scheduled, and supervised mold construction through shop with foreman. Trained detailers and CNC programmer to use Auto-CADD software. Supervised detailers and scheduled their work on a daily basis. Downloaded product files from customers to use for injection mold design, separated 3-D surface files to cavity and core surfaces, built parting line surfaces around cavity and cores used in design and CNC programs. Established engineering department to control injection mold… Show more Coordinated, scheduled, and supervised mold construction through shop with foreman. Trained detailers and CNC programmer to use Auto-CADD software. Supervised detailers and scheduled their work on a daily basis. Downloaded product files from customers to use for injection mold design, separated 3-D surface files to cavity and core surfaces, built parting line surfaces around cavity and cores used in design and CNC programs. Established engineering department to control injection mold designs (all designs were outsourced). Set-up engineering office, computer, drawing plotter, installed software, and developed archive system for drawings and files. This reduced costs from an estimated $80,000.00 each year to under $60,000.00. Utilized experience to design interchangeability into a series of eight molds for a major customer reducing costs by 30%. Show less Coordinated, scheduled, and supervised mold construction through shop with foreman. Trained detailers and CNC programmer to use Auto-CADD software. Supervised detailers and scheduled their work on a daily basis. Downloaded product files from customers to use for injection mold design, separated 3-D surface files to cavity and core surfaces, built parting line surfaces around cavity and cores used in design and CNC programs. Established engineering department to control injection mold… Show more Coordinated, scheduled, and supervised mold construction through shop with foreman. Trained detailers and CNC programmer to use Auto-CADD software. Supervised detailers and scheduled their work on a daily basis. Downloaded product files from customers to use for injection mold design, separated 3-D surface files to cavity and core surfaces, built parting line surfaces around cavity and cores used in design and CNC programs. Established engineering department to control injection mold designs (all designs were outsourced). Set-up engineering office, computer, drawing plotter, installed software, and developed archive system for drawings and files. This reduced costs from an estimated $80,000.00 each year to under $60,000.00. Utilized experience to design interchangeability into a series of eight molds for a major customer reducing costs by 30%. Show less
-
-
-
-
Mold Designer/Technical Support
-
Jul 1994 - Jan 1996
Designed injection, stack, and injection-blow molds for the consumer market. Supported customers with design recommendations and Moldflow® analysis. Designed injection, stack, and injection-blow molds for the consumer market. Supported customers with design recommendations and Moldflow® analysis.
-
-
-
-
Mold Designer
-
Jun 1993 - Apr 1994
Designed custom injection molds for the medical industry. Helped develop first iteration of paperless system between engineering and CNC department. Designed custom injection molds for the medical industry. Helped develop first iteration of paperless system between engineering and CNC department.
-
-
-
-
Mold Designer/Technical Support/Product Designer
-
Jun 1988 - Jun 1993
Designed custom injection molds for the automotive industry. Worked with customers on product design for 'moldability'. Ran Moldflow® analysis to improve process on existing, low profit, molds and for new products for the Engineered Products Division (EPD). Technical liaison for sales group in EPD. Designed custom injection molds for the automotive industry. Worked with customers on product design for 'moldability'. Ran Moldflow® analysis to improve process on existing, low profit, molds and for new products for the Engineered Products Division (EPD). Technical liaison for sales group in EPD.
-
-
-
-
Drafter/Designer
-
Jan 1985 - Jun 1988
Designed custom closures for automotive applications. Designed proprietary and custom tooling for universal mold bases. Maintained all engineering files and priorities. Designed custom closures for automotive applications. Designed proprietary and custom tooling for universal mold bases. Maintained all engineering files and priorities.
-
-
Education
-
Penn State Erie, The Behrend College
Bachelor Degree, Plastics Engineering Technology -
Penn State University
Bachelor of Science, Plastics Engineering Technology -
Penn State Erie, The Behrend College
Associate Degree, Mechanical Engineering Technology
Community
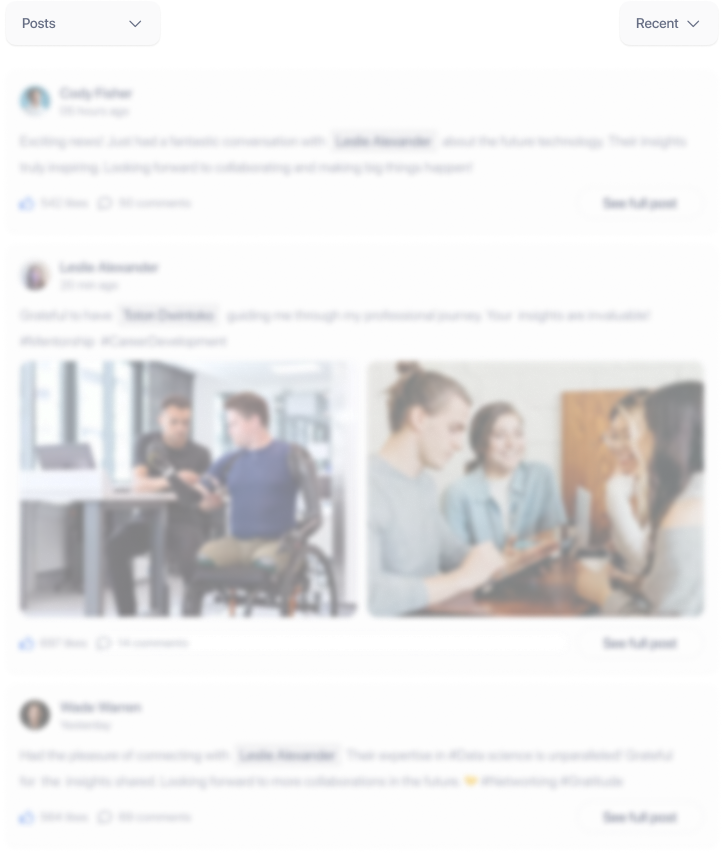