David Wu
Branch Manager at Flocor- Claim this Profile
Click to upgrade to our gold package
for the full feature experience.
Topline Score
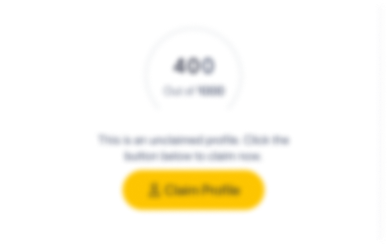
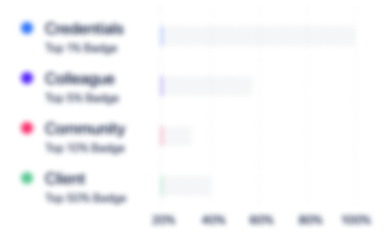
Bio


Experience
-
Flocor
-
Canada
-
Wholesale
-
1 - 100 Employee
-
Branch Manager
-
May 2021 - Present
-
-
-
Flowserve Corporation
-
United States
-
Industrial Machinery Manufacturing
-
700 & Above Employee
-
Plant Manager
-
2016 - 2020
• Managed team of 15 associates while achieving continuous bookings growth ($4.8M in 2016 to $6.7M through 2019) and revenue (from $4.3M in 2016 to $6.5M through 2019).• Built and led resilient safety culture without any LTA in over 15 years.• Created positive team environment by interacting with staff on ongoing basis, communicating to personnel on all company initiatives, and by keeping staff focused on improving key performance indicators (KPI’s) during monthly's town halls and daily production meetings.• Interacted and delivered robust customer service by resolving concerns and delivering products with 96%+ on-time delivery, routinely year over year.• Directed initiatives, confirming all quality procedures were adhered to daily and all new and refurbished goods were delivered to customers’ satisfaction. Captured all Failure Analysis (FA) and Root Cause Analysis (RCA) in Non-Conformance Reports (NCRs) and Corrective Action Reports (CARs).
-
-
Quality Repair Center (QRC) Engineer
-
2005 - 2016
• Developed quality repair work-scope for all in-house and budgetary requirements within timelines requested by customers; guided sales and customers with technical engineering advice.• Produced work-scope for all subcontract work and followed-up through verbal communication with subcontractor on daily basis.• Communicated daily with internal customers (managers, shop staff, sales, buyer, fellow engineers) and external customers (end-users and distributors) on all aspects of pump and seal repairs.• Managed role of Service Quality Representative (SQR) on daily basis at Sarnia's QRC, ensuring repairs were managed and refurbished per procedures.• Certified all approved work-scopes were released to shop floor with shop routers, procedures, drawings; checked daily all routers were signed off accordingly during repair process.• Led in any RCA following quality procedures and communicated findings with internal and external customers when completed.
-
-
-
Suncor
-
Canada
-
Oil and Gas
-
700 & Above Employee
-
Reliability Engineer
-
1999 - 2005
• Released daily Disassembly, Clean and Inspection (DCI) work scope to planners / shop staff for rotating equipment prior to assessment.• Developed quality repair work-scope for all in-house rotating equipment repairs daily, after DCI review.• Guided unionized trades on repaired work-scopes, ensuring rotating equipment was refurbished following repair documentation on a daily basis.• Prepared daily technical specification to buyers on all buyouts and subcontract repair work; liaised with subcontractors, providing repair details and witnesses.• Contributed technical equipment support to Operation teams on daily basis, assisting in FA and helping define root cause on any repeat failures on pumps and seals.• Processed and/or reviewed any Preventative Maintenance Program on rotating equipment and helped lead vibration team with training and analysis on daily basis.
-
-
Education
-
Lakehead University
Bachelor of Engineering - BE, Mechanical Engineering -
Lambton College
Diploma of Mechanical Engineering Technology
Community
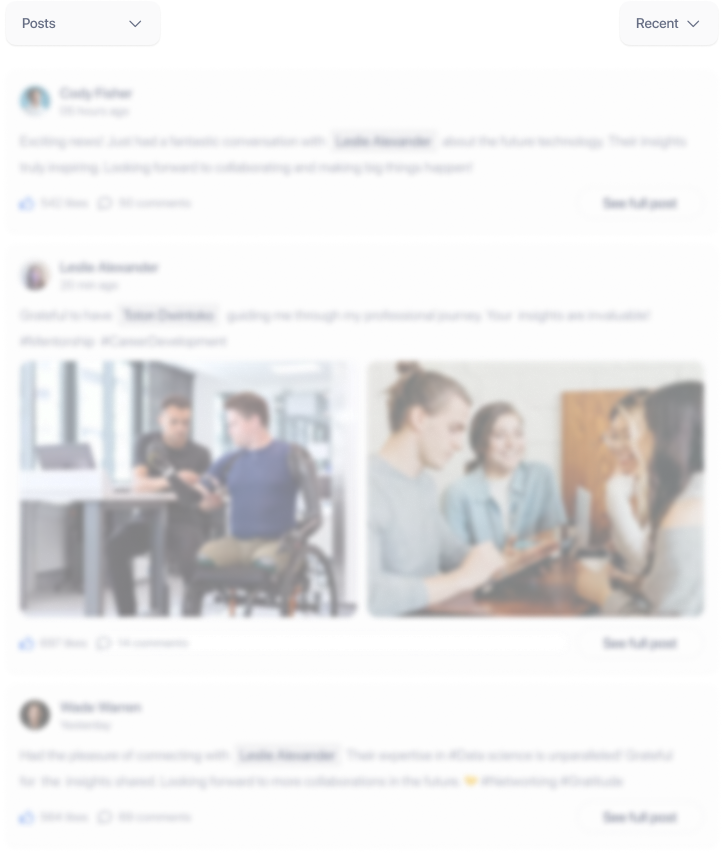