David Schwartz
Continuous Improvement Manager at Sage Products, now part of Stryker- Claim this Profile
Click to upgrade to our gold package
for the full feature experience.
Topline Score
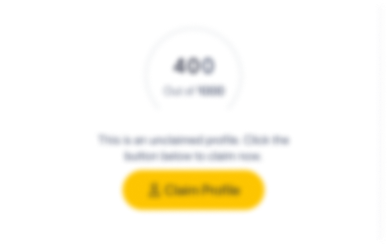
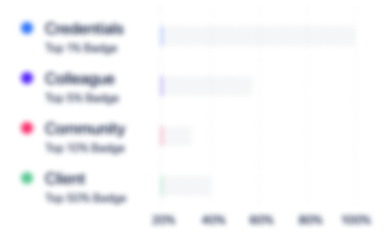
Bio

David Radue
David Schwartz is a sharp engineer who is skilled at defining problems and working to direct, effective solutions. He is very hard working and makes personal sacrifices to ensure the work goals are met whether they are his responsibility or the responsibility of others. David makes persuasive arguments using evidence and clear, logical thought progression.

David Radue
David Schwartz is a sharp engineer who is skilled at defining problems and working to direct, effective solutions. He is very hard working and makes personal sacrifices to ensure the work goals are met whether they are his responsibility or the responsibility of others. David makes persuasive arguments using evidence and clear, logical thought progression.

David Radue
David Schwartz is a sharp engineer who is skilled at defining problems and working to direct, effective solutions. He is very hard working and makes personal sacrifices to ensure the work goals are met whether they are his responsibility or the responsibility of others. David makes persuasive arguments using evidence and clear, logical thought progression.

David Radue
David Schwartz is a sharp engineer who is skilled at defining problems and working to direct, effective solutions. He is very hard working and makes personal sacrifices to ensure the work goals are met whether they are his responsibility or the responsibility of others. David makes persuasive arguments using evidence and clear, logical thought progression.

Credentials
-
Dealing with the Seven Deadly Wastes
LinkedInAug, 2020- Nov, 2024
Experience
-
Sage Products, now part of Stryker
-
United States
-
Medical Equipment Manufacturing
-
1 - 100 Employee
-
Continuous Improvement Manager
-
Mar 2023 - Present
• Responsible for site wide Continuous Improvement strategy and implementation of lean production systems• Manage training department responsible for onboarding, orientation, and initial training of new hires as well as continuous improvement of training programs.• Stryker Global Process Owner for Problem Solving. Leading international team to develop and deploy standardized problem-solving training material across all Stryker sites as part of strategic initiative to improve effective problem solving. Show less
-
-
Associate Manager, Continuous Improvement
-
Jan 2021 - Feb 2023
• Improved efficiency on Primafit line for an additional gain from 1.5 to 1.2 labor hours per case by managing and training rotational resource in lean manufacturing.• Led Pharma Packout Lean Lighthouse to gain 17% labor efficiency through standardized work improvements and line balancing.• Drove completion of form fill labor rate project to create standards and methods to sustain previous gains for the long term and make training new leaders easier.• Reduced form fill changeover time from over 2 hours to 45 minutes through Lean Lighthouse, utilizing SMED and standardized work tools.• Trained management team on lean leadership, emphasizing a people development first approach and kata coaching to foster a continuous improvement mindset.• Established process improvement framework for Primafit 2.0 post-launch, driving daily metrics and problem solving meetings. Developed team leaders to drive continuous improvement leading to shift case rate improvement from 60 to over 120.• Developed two additional lean lighthouse coaches to increase capacity to lead improvement events and help support expanding lean culture.• Directed goal alignment activity with plant management, facilitating working sessions and creating 3-year plan to guide plant and department goals.• Created and deployed training for improved meeting culture throughout plant to address pain points and time management problems following shift to remote and hybrid work. Show less
-
-
-
Stryker Sage
-
United States
-
Medical Equipment Manufacturing
-
400 - 500 Employee
-
Senior Staff Engineer
-
Mar 2018 - Jan 2021
• Led Clean Space Initiative project to upgrade manufacturing and lab spaces to best practices for clean environments. Included boundary control at airlocks, material handling, PPE improvements, and cultural change with cleanliness mindset training.• Coached a one week ‘Lean Lighthouse’ event for the Turn & Position line improving capacity from 194 to 362 cases per shift while also improving efficiency from 0.12 to 0.07 labor hours per case.• Replaced 35% Hydrogen Peroxide process to meet DHS requirements. Sourced new material and validated new process with lower concentration.• Led a four week ‘Lean Lighthouse’ event for the automated mixing lines increasing capacity by 500klbs/month deferring the need for capital investment and identified future improvements.• Trained and deployed the 6S program across all manufacturing and lab areas to effectively manage plant floor visual management and organization.• Ran a one week ‘Lean Lighthouse’ event for the Primafit line resulting in sustained reduction of labor hours per case from 1.85 to 1.6 for a $250k per year impact.• Launched and sustained a plant-wide daily metrics program to manage performance on a day to basis resulting in a leader culture change for accountability and ownership.• Identified root cause of Comfort Shield label leak. Validated necessary product change and developed and launched new test process to resolve problem.• Directed a series of ‘Lean Lighthouse’ activities on Form Fill Seal lines achieving a sustained 20% production efficiency improvement. Show less
-
-
Senior Process Engineer
-
Feb 2016 - Mar 2018
• Reduced seal integrity NCRs by 37% and Customer Claims by 72% on a per lot basis through root cause analysis and implementation of improved controls on a validated process.• Led $2.4M equipment implementation project for upgrading CIP systems on a prioritized project schedule.• Led problem solving activity to reduce Comfort Bath Line 4 stacker downtime by 250 min/month by creating fixtures for equipment setup.• Implemented safety improvements including robotic palletizer cell upgrade, and introduced new hazard identification and risk analysis templates.• Responsible for comfort bath metrics and process ownership• Provided feedback on comfort bath operations for KPI gap identification Show less
-
-
-
-
Product Development & Equipment Engineering Specialist
-
Jul 2014 - Jan 2016
• Created and implemented plant-wide production plan for volume reduction equipment utilization• Supporting new model development through process capability & risk analysis• Performing safety risk assessments throughout plant to support equipment safety upgrades• Implementing temperature interlock system on casting machines to guarantee good parts casting• Installing overhead wheel conveyor system to alleviate 700 wheel per day overcapacity issue in paint booth 3
-
-
Manufacturing Engineering Specialist (Finishing Department)
-
Apr 2013 - Jul 2014
• Visualized overall machining OR% by line in order to show gap and prioritize work• Raised machine line 1 & 2 OR% from 60% to 85% over a three month time period while decreasing cycle time by 5s resulting in overall productivity gain of 650 wheels per day combined• Installed and refurbished used drilling machine in 12 week time window to meet cycle time and surface finish requirements for new model launch
-
-
Manufacturing Engineering Specialist (Casting Department)
-
Jul 2007 - Apr 2013
• Improved quality on low pressure casting single crucible process by 3% through development and installation of novel baffle plate system representing 100 part scrap reduction per day• Increased productivity on casting line 4 by reducing cycle time from 210s to 190s resulting in 144 parts per day improvement• Upgraded capability of rough trim equipment from 16” to 17” allowing 4 casting machines to change to larger rim size, increasing CAPTIN’s overall 17” capacity by 1675 per day and improving line flexibility• Created JKK process standards for entire casting shop to manage daily fluctuations in quality through robust process controls and team member culture• Re-designed die heaters by working with vendor to improve life, reduce cost, and reduce failure rate resulting in 30% cost decrease and overall $140k per year savings• Replaced failed double chamber furnace $17k under budget and two weeks ahead of schedule on expedited project schedule as part of a $300k project• Responsible for day to day analysis of reject data to prioritize work and track down and correct problems Show less
-
-
-
Toyota Motor Manufacturing Indiana
-
Evansville, IN
-
Engineer in Training
-
Oct 2006 - Jul 2007
• Installed a lift assist to remove ergonomic burden and eliminate an extra team member for the off-line bumper assembly area • Resolved productivity issues with line-side equipment as part of pilot development team for Tundra launch • Designed standardized handle and stopper system for conveyance dollies to offload to line-side chutes • Installed a lift assist to remove ergonomic burden and eliminate an extra team member for the off-line bumper assembly area • Resolved productivity issues with line-side equipment as part of pilot development team for Tundra launch • Designed standardized handle and stopper system for conveyance dollies to offload to line-side chutes
-
-
-
Toyota Motor Corporation
-
Motor Vehicle Manufacturing
-
700 & Above Employee
-
Engineer in Training (EiT)
-
Jul 2006 - Oct 2006
Training Activities: Toyota Fundamentals, Toyota Way Foundations, Communicating the Toyota Way, Introduction to TPS, TPS I & II, Intro to Standardization, Standardized Work, Hoshin Kanri, Anti-Harassment Awareness, Diversity I & II, Introduction to TBP, Introduction to PDCA, Project Management I & II, Time Management, Mentee Training, Self Coaching (TEMA) Training Activities: Toyota Fundamentals, Toyota Way Foundations, Communicating the Toyota Way, Introduction to TPS, TPS I & II, Intro to Standardization, Standardized Work, Hoshin Kanri, Anti-Harassment Awareness, Diversity I & II, Introduction to TBP, Introduction to PDCA, Project Management I & II, Time Management, Mentee Training, Self Coaching (TEMA)
-
-
-
Rose-Hulman Ventures
-
United States
-
Industrial Machinery Manufacturing
-
1 - 100 Employee
-
Design Engineer
-
Jun 2005 - Aug 2005
Worked with client and patients to develop a wheelchair design as part of senior design project Created prototype of novel wheelchair that facilitates healing of pressure sores Worked with client and patients to develop a wheelchair design as part of senior design project Created prototype of novel wheelchair that facilitates healing of pressure sores
-
-
-
Rose-Hulman Institute of Technology
-
United States
-
Higher Education
-
700 & Above Employee
-
Teacher's Assistant
-
Sep 2003 - Nov 2004
Assisted with one section using Mechanical Desktop with AutoCAD Assisted with two sections using SolidEdge Performed routine tasks such as grading, proctoring and helping students with in-class problems Arranged out of class optional review sessions at student's request Assisted with one section using Mechanical Desktop with AutoCAD Assisted with two sections using SolidEdge Performed routine tasks such as grading, proctoring and helping students with in-class problems Arranged out of class optional review sessions at student's request
-
-
-
-
Quality Systems Compliance Intern
-
Jul 2004 - Aug 2004
Responsible for analysis of turbine blade heat treatments Performed statistical analysis of new OEM processes Prepared presentations for company and Revised technical manuals Responsible for analysis of turbine blade heat treatments Performed statistical analysis of new OEM processes Prepared presentations for company and Revised technical manuals
-
-
Education
-
Rose-Hulman Institute of Technology
Bachelors of Science, Mechanical Engineering
Community
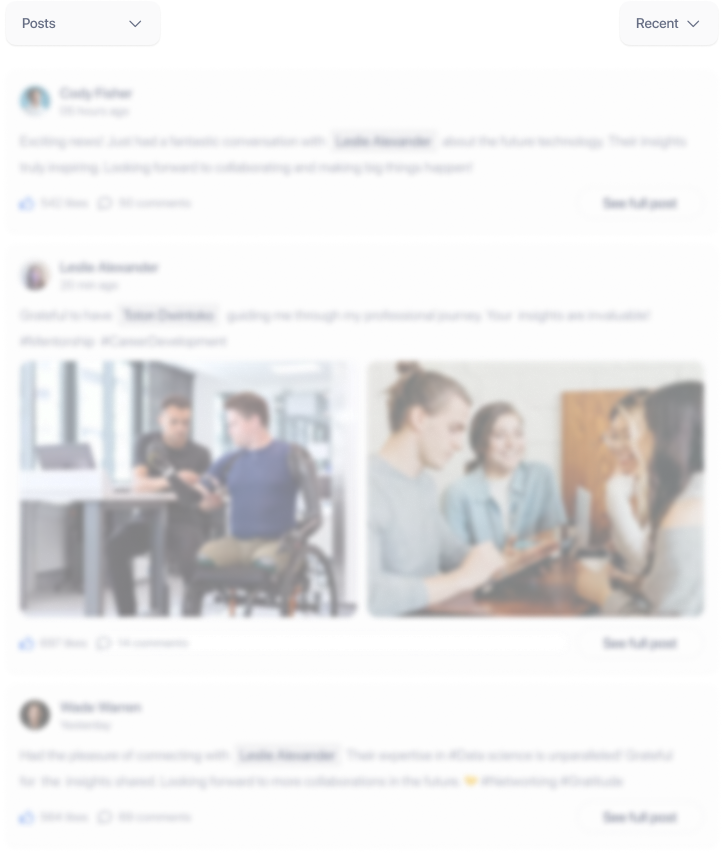