David Pechin
Process Equipment Consultant at Solopower- Claim this Profile
Click to upgrade to our gold package
for the full feature experience.
Topline Score
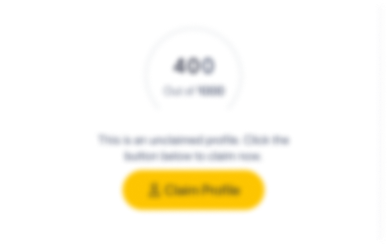
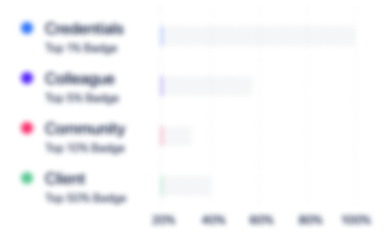
Bio

Edith Maverick Folger
Dave is a great developer to work with. He knows his stuff, takes in all the knowledge he can find about any project, balances the various needs and constraints of the stakeholders, and designs/builds a system that does the job reliably and well.

Edith Maverick Folger
Dave is a great developer to work with. He knows his stuff, takes in all the knowledge he can find about any project, balances the various needs and constraints of the stakeholders, and designs/builds a system that does the job reliably and well.

Edith Maverick Folger
Dave is a great developer to work with. He knows his stuff, takes in all the knowledge he can find about any project, balances the various needs and constraints of the stakeholders, and designs/builds a system that does the job reliably and well.

Edith Maverick Folger
Dave is a great developer to work with. He knows his stuff, takes in all the knowledge he can find about any project, balances the various needs and constraints of the stakeholders, and designs/builds a system that does the job reliably and well.

Experience
-
Solopower Systems, Inc.
-
United States
-
Renewable Energy Semiconductor Manufacturing
-
1 - 100 Employee
-
Process Equipment Consultant
-
Jul 2014 - Present
Provide equipment and process support for front-end CIGS solar cell manufacturing company. Team with customer staff to startup new and existing manufacturing tools and related equipment at the customers' facility. Collaborate on anneal and selenization processes to confirm operational repeatability, process efficacy and to maximize manufacturing and process yields. Provide guidance to the process development staff on process equipment capabilities, boundary conditions, and options to enhance process equipment functionality.
-
-
-
Nanosolar
-
United States
-
Renewable Energy Semiconductor Manufacturing
-
1 - 100 Employee
-
Member of Technical Staff
-
Jun 2012 - Sep 2013
Supported front-end CIGS manufacturing utilizing a continuous web for GIG ink, Anneal, and selenization processes to produce solar cells on an aluminum-foil substrate. Improved in-situ process monitoring for the above processes with respect to O2ppm, particulates, and Se Vapor concentrations. Supported yield improvement activities in ink deposition and Anneal thermal budget/H2 concentration experiments, and provided a technical resource to the equipment support and process teams. Supported critical tool down events.
-
-
-
Boston Scientific
-
United States
-
Medical Equipment Manufacturing
-
700 & Above Employee
-
Principle Engineer, Equipment Engineering
-
Jan 2007 - Jun 2012
Responsible for software validation remediation effort at San Jose site. Collaborated with an international team to define new equipment and software validation process. Lead cross-functional teams to roll out new policies and processes at the site. Managed and tracked program, as well as audited the site to verify implementation effectiveness. Presented to the executive staff on progress and completion. Created or improved process equipment, designed and implemented new test fixtures and methods. Member of the NCMR board, and subject matter expert on equipment and software validation.
-
-
-
PerkinElmer Optoelectronics
-
Biotechnology Research
-
300 - 400 Employee
-
Sr. Equipment Engineer
-
Sep 2002 - May 2005
Supported manufacturing and test of X-Ray imaging devices on 500mm x 500mm glass substrates. Primary responsibility included PECVD, PVD, Thermal Evaporation, and Test. Improved PECVD throughput by 200% by reducing non value added time. Process timing change also produced a 300% reduction in device charge retention, which allowed increased scan speeds for the end user. Implemented a new thermal evaporator which did not meet specifications. Worked with vendor to resolve contract issues and make unit functional. Defined new project with management to re-design evaporator sources and software to provide 750uM films and control CsI/TlI concentration percentage. New tool exceeded customers new performance requirements due to improved scintillator control.
-
-
-
Candescent Technologies
-
San Jose, CA
-
Equipment Engineer/Manager
-
Sep 1998 - Feb 2001
Supported FED pilot fab for emitter, faceplate and test areas. Improved emitter yield by implementing improved thermal monitoring of vacuum ovens. Improved Cpk of thick film extrusion coater through polyimide handling and extrusion head maintenance. Installed and qualified new testers for both faceplate and emitter lines. Specified and installed new vacuum oven for polyimide curing on schedule and under budget. Promoted to equipment engineering manager. Supported FED pilot fab for emitter, faceplate and test areas. Improved emitter yield by implementing improved thermal monitoring of vacuum ovens. Improved Cpk of thick film extrusion coater through polyimide handling and extrusion head maintenance. Installed and qualified new testers for both faceplate and emitter lines. Specified and installed new vacuum oven for polyimide curing on schedule and under budget. Promoted to equipment engineering manager.
-
-
-
Novellus Systems acquired by Lam Research Corporation
-
Semiconductor Manufacturing
-
400 - 500 Employee
-
Mgr. Customer Satisfaction
-
1988 - 1996
Facilitated technical communication to both internal and external customers for the Tungsten business unit. Implemented MWBI metric to track tool performance. Worked with the field and product engineering to develop BKM's and drive MTBF to >200hrs for all systems. Supported CE marking effort for the Tungsten and legacy toolsets, responded to all 3rd party observations and drove certification for the business unit. Tool technical lead for customer escalations. Resolved difficult tool/process issues and helped repair relationships resulting from extended downtimes.
-
-
Education
-
DeVry Institute of Technology
BSEET, Electrical Engineering
Community
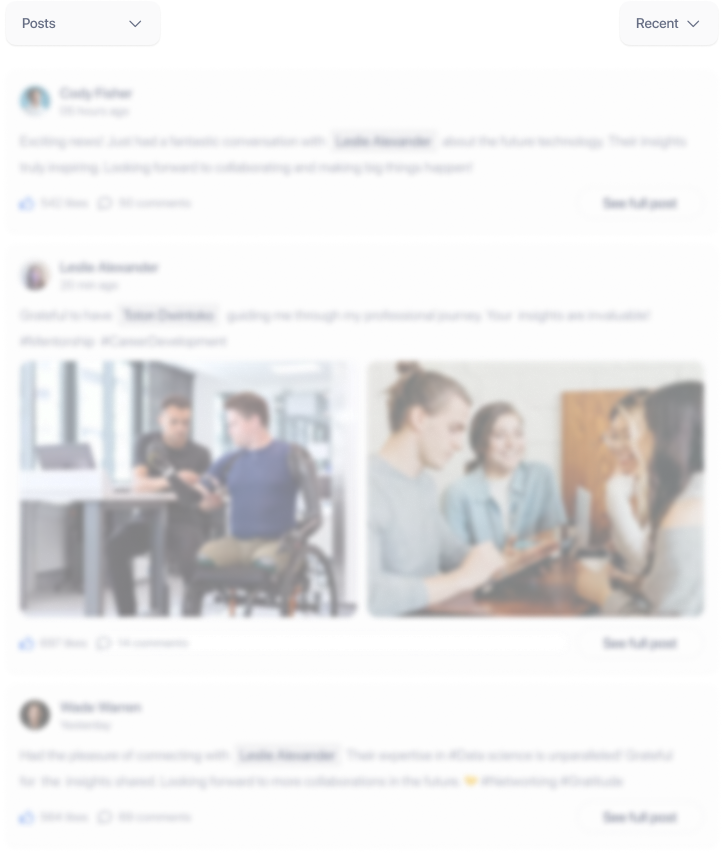