
David Nau
Project Control Manager at Marietta Silos LLC- Claim this Profile
Click to upgrade to our gold package
for the full feature experience.
-
American Sign Language Native or bilingual proficiency
-
Spanish Limited working proficiency
Topline Score
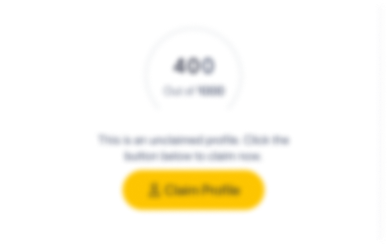
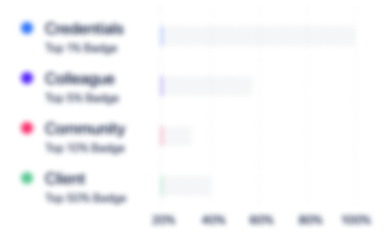
Bio

Mark Nau
David came to work at Alabama Sand And Gravel right out of college and immediately made improvements to the mining operations and profitability of the company.

Mark Nau
David came to work at Alabama Sand And Gravel right out of college and immediately made improvements to the mining operations and profitability of the company.

Mark Nau
David came to work at Alabama Sand And Gravel right out of college and immediately made improvements to the mining operations and profitability of the company.

Mark Nau
David came to work at Alabama Sand And Gravel right out of college and immediately made improvements to the mining operations and profitability of the company.

Experience
-
Marietta Silos LLC
-
United States
-
Construction
-
1 - 100 Employee
-
Project Control Manager
-
Mar 2021 - Present
-
-
-
NAPA AUTO PARTS
-
United States
-
Retail
-
700 & Above Employee
-
Store Manager
-
Sep 2020 - Feb 2021
-
-
-
Couch Aggregates
-
United States
-
Mining
-
1 - 100 Employee
-
District Plant Manager
-
Jun 2017 - Aug 2020
-
-
-
US Silica Company
-
United States
-
Investment Management
-
1 - 100 Employee
-
Operations Manager
-
Aug 2014 - Mar 2016
• Assist in managing operations and budgets.• Aid in budget planning for both Columbia and Hurtsboro Plants• Set a 2 year best EBITDA record at Hurtsboro (200k over previous record of 175k)• Implemented a moisture meter and recalibrated it at the Dryer in Hurtsboro to reduce MMBTU’s. • Oversee Hurtsboro reporting and operating decisions. Streamlining dryer by installing a moisture meter for sand entering the dryer, and working on getting moistures measured post drying. Worked with Legal to get a sub-lease signed and executed. Also worked with Legal to develop a “generic” lease and an exploration lease to show landowners prior to any negotiations. Working on a more detailed and planned capEx. Introduced a new contractor to provide competitive bids, and for greatly improved shutdown capabilities. Initiated and executed PAR for truck fall protection and new truck scales. • Manage operations of Columbia Plant. Streamlining conditioning and float systems. Streamlined filter tables by finding the optimal bed depth, and through the use of a variable speed drive to maintain cake depth. Reducing fines loss through floatation and drying by streamlining. Working with engineers to determine areas of structure that need repaired and/or replaced.• Interim EHS coordinator for the COL and HUR plants after a retirement, until a replacement was in place and comfortable. Submitted semi-annual Title V permit reports.• Initiated and executed a capital plan to increase milling capacities by upwards of 15, while collaborating with Corporate Engineering.
-
-
-
Alabama Sand and Gravel
-
Construction
-
1 - 100 Employee
-
Plant Manager
-
Jan 2010 - Aug 2014
• Manage ops & budgets for two gravel plants, generating annual sales over $10 mil. Budget planning, 3 year capital expense plan; include major maintenance, 10 year mining plan. Hired, trained, and evaluated a staff of over 68 employees. Responsible for compliance with environmental and safety regulations. Participated in strategic planning, expense forecasting, & cash management/investment strategies with VP of Ops and the CEO.• Safety: Weekly safety meetings, compiled safety videos & reports, reported incidents Created and implemented daily pre-shift check lists Compiled routine maintenance plans I implemented an incentive program known as the "rock box". A "u-rock" is written and placed in the box for positive items, such as finding potential safety issues or outstanding performance. The employee with the most "u-rocks" wins an incentive• Mine/Pit I initiated the first use of a motor grader, improve and widen haul roads, and to decrease the potential for passing vehicle accidents. I created mine plans to include – access, entrance, and directional methods to reduce; standing water, hauling distance, costs, & elevation changes for hauling equipment. 10 yr mine plan• Environmental Collaborate with Corps of Engineers to ensure to minimize effects on navigable waterways and wetlands. Established wetland restoration projects with the Corps of Engineers• Contributions Cut costs by $320,000 first year employed. Designed a 10+ year mining plan Supported design, controls, and implementation of SAP. Solely trained all users at AS&G, aided in the “go-live” and training at one Smelting operation located in Selma, Alabama. Designed and implemented a bonus plan, to improve morale during downsizing, increase production and employee recognition. Collaborated with local community to improve perception of mining, county engineers to improve local gravel roads. Communicated with timber operations
-
-
-
University of Akron
-
United States
-
Government Administration
-
Graduate Assistant
-
Aug 2008 - Jan 2010
Graduate Assistant - Intramural Sports Graduate Assistant - Intramural Sports
-
-
-
University of North Alabama
-
United States
-
Higher Education
-
700 & Above Employee
-
Intramural Supervisor
-
Jan 2005 - May 2008
-
-
Resident Assistant
-
Aug 2005 - May 2007
-
-
Education
-
The University of Akron
Master of Education (MEd), Education -
University of North Alabama
Bachelor of Science (BS), Marine Biology
Community
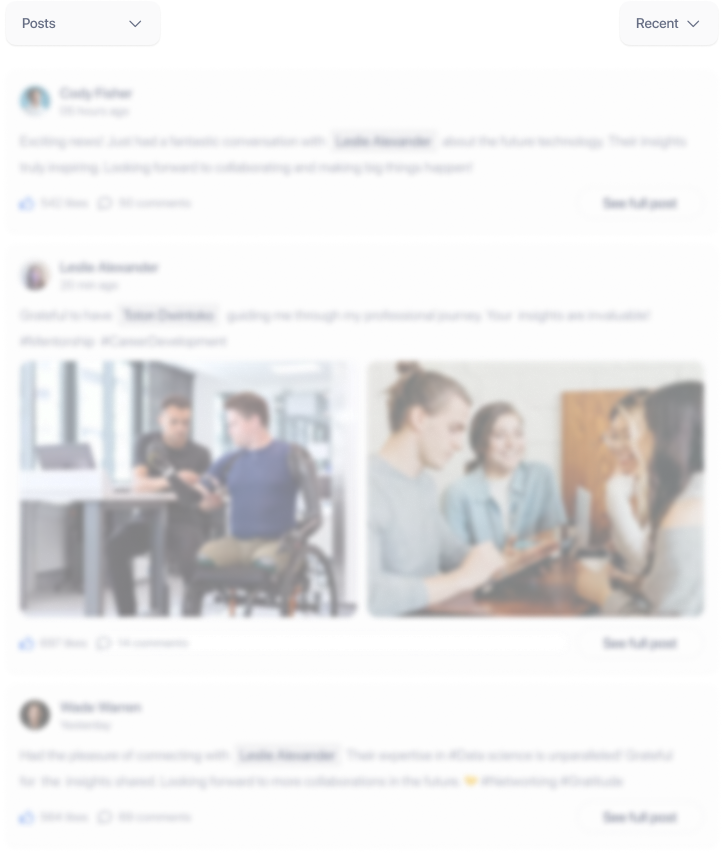