David Murray
Electrician at All Phase Electric Inc.- Claim this Profile
Click to upgrade to our gold package
for the full feature experience.
Topline Score
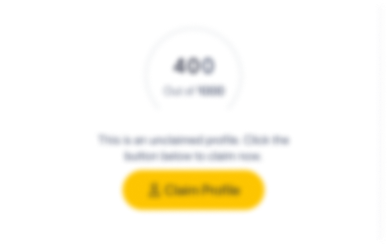
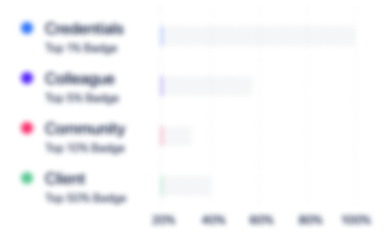
Bio

Kay Stout
David was a participant in career transition workshops at the Imation plant in Weatherford. It was evident that his promotions within the company were based on competency and the ability to interface with the employees to meet goals.

Kay Stout
David was a participant in career transition workshops at the Imation plant in Weatherford. It was evident that his promotions within the company were based on competency and the ability to interface with the employees to meet goals.

Kay Stout
David was a participant in career transition workshops at the Imation plant in Weatherford. It was evident that his promotions within the company were based on competency and the ability to interface with the employees to meet goals.

Kay Stout
David was a participant in career transition workshops at the Imation plant in Weatherford. It was evident that his promotions within the company were based on competency and the ability to interface with the employees to meet goals.
0
/5.0 / Based on 0 ratingsFilter reviews by:
Experience
-
All Phase Electric Inc.
-
United States
-
Construction
-
1 - 100 Employee
-
Electrician
-
Jan 2016 - Present
Industrial, commercial, and residential electrical services Industrial, commercial, and residential electrical services
-
-
-
GE Oil & Gas
-
Oil and Gas
-
1 - 100 Employee
-
Environmental, Health, & Safety Specialist
-
Oct 2011 - Jun 2015
Responsible for all aspects of plant safety including Communications, Procedures, Training, Solid and Hazardous Waste Management, RCRA, Radiation Safety, Lockout/Tagout, HazCom/MSDS’s, PPE, Stormwater PPP, Water Well Permit, Air Permit, Tier II, TRI & AEI reporting. • 2013 EHS Excellence Award • 2012 EHS Award for Inclusiveness and EHS Improvements • Implemented a water recycling system to eliminate the risk associated with exceedances to the Shawnee Municipal Authority. Responsible for all aspects of plant safety including Communications, Procedures, Training, Solid and Hazardous Waste Management, RCRA, Radiation Safety, Lockout/Tagout, HazCom/MSDS’s, PPE, Stormwater PPP, Water Well Permit, Air Permit, Tier II, TRI & AEI reporting. • 2013 EHS Excellence Award • 2012 EHS Award for Inclusiveness and EHS Improvements • Implemented a water recycling system to eliminate the risk associated with exceedances to the Shawnee Municipal Authority.
-
-
-
-
Environmental, Health, Safety, and Security Engineer
-
Sep 2007 - Jul 2011
Responsible for all aspects of plant safety including Communications, Procedures, Training, Process Safety Management, Solid and Hazardous Waste Management, RCRA, Radiation Safety, Hazcom, PPE, Lockout/Tagout, Confined Space, MSDS’s, Stormwater PPP, EPCRA 311, 312 & 313, Title V Air Permit, Agency reporting. • Zero OSHA violations • Zero ODEQ violations- Air permit, RCRA, Radiation, Stormwater • Reduced cost in managing waste by 42% • Implemented a successful ISO 14001, Environmental Management System
-
-
-
Imation
-
United States
-
IT Services and IT Consulting
-
200 - 300 Employee
-
Facilities and Security Engineer
-
2002 - 2007
Responsibilities include all building utilities, fire protection and HVAC Systems. Also, Site Contractor Representative, Capital Project and Asset Management and Site Security.• Installation of new utility plant with chillers, boilers, air compressors and all associated equipment piping. Savings to the plant of around $900k per year.• Construction and installation of new $55M, 30,000 Sq. Ft. building addition with coater and compounding equipment.• Installation of new and replacement of old fire protection systems including water, AFFF foam and CO2.• Researched and designed changes to the plants electrical system to better re-distribute loads between transformers.• Coordinated installation and setup of new security system including Honeywell Rapid Eye camera system and DVR with 14 Rapid dome PTZ cameras. Also new digital card readers at each door.
-
-
Process Engineer
-
2000 - 2002
Responsibilities include monitoring and improving Coater and Punch process performances including yields, runtime, and quality issues. Identify root cause of problems and take corrective action utilizing plant resources as required.• Investigated and determined cause of scratches on punched media and implemented extra polishing step in the die rework procedure.• Designed and implemented the wide web program which resulted in a 20% reduction in coating defects.• Re-designed calendar roll cleaning modules for ease of installation and alignment.
-
-
Maintenance Supervisor
-
1996 - 2000
Lead the maintenance organization to meet or exceed department safety, quality, productivity and cost objectives.• Implemented predictive maintenance procedures using vibration analysis, oil analysis and thermography.• Successfully implemented an on-line maintenance reporting system to track pertinent data such as: maintenance related downtime hours and occurrences, meantime between failure, meantime to repair.• Consistently maintained an on time preventative maintenance completion rate at 95% or better.• Led the recruiting and hiring efforts of additional maintenance staff.
-
-
-
3M
-
Germany
-
Chemical Manufacturing
-
1 - 100 Employee
-
Maintenance Supervisor
-
1991 - 1996
Lead the maintenance organization to meet or exceed department safety, quality, productivity and cost objectives.• Implemented predictive maintenance procedures using vibration analysis, oil analysis and thermography.• Successfully implemented an on-line maintenance reporting system to track pertinent data such as: maintenance related downtime hours and occurrences, meantime between failure, meantime to repair.• Consistently maintained an on time preventative maintenance completion rate at 95% or better.• Led the recruiting and hiring efforts of additional maintenance staff.
-
-
Electrical Instructor
-
1989 - 1991
Responsible for the development, coordination, and instruction of all Electrical Core and Machine Specific courses for maintenance craftspeople.• Designed, developed and delivered five different Electrical Maintenance courses.• Coordination and delivery of maintenance pre-hire tests.• Developed, and implemented a seven week training course for maintenance new hires.• Designed, developed, and coordinated the delivery of maintenance training on a new diskette assembly line.
-
-
-
-
Electronic Technician
-
1980 - 1988
Responsible for the troubleshooting, repair, and calibration of numerous types of electronic test equipment used to manufacture flexible diskettes. • Setup and calibration of test equipment in Maine and Arizona. • Identifying and solving both process and product problems. • Calibration of all endpoint test equipment. • Worked with Division Engineering to determine and correct a source of RFI affecting product yields. Responsible for the troubleshooting, repair, and calibration of numerous types of electronic test equipment used to manufacture flexible diskettes. • Setup and calibration of test equipment in Maine and Arizona. • Identifying and solving both process and product problems. • Calibration of all endpoint test equipment. • Worked with Division Engineering to determine and correct a source of RFI affecting product yields.
-
-
Education
-
Southeastern Oklahoma State University
A.S., Electronics Technology
Community
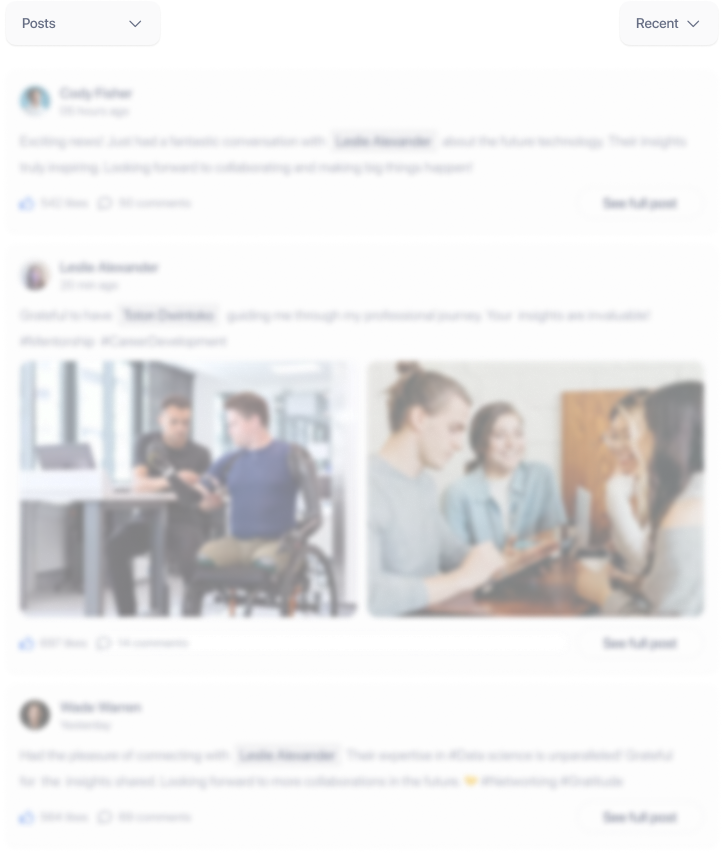