David Marshall, BS, MBA
Process/Project Engineer at US Motion | Frencken America- Claim this Profile
Click to upgrade to our gold package
for the full feature experience.
Topline Score
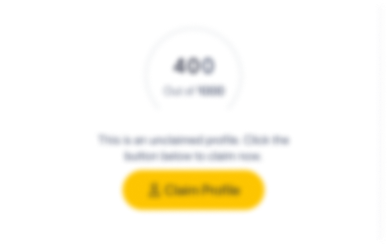
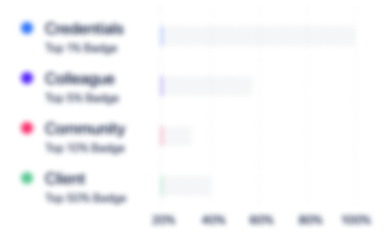
Bio

LinkedIn User
I worked with Dave for 11 years. Probably his best work came after the 2000 telecom meltdown where businesses like ours were suddenly struggling to survive. Without a lot of money to spend on capital equipment improvements, Dave was tasked with Leaning out the factory to reduce costs with a minimum of expense. Dave works very well at all levels and particularly well with hourly personnel with a combination of cat herding and humor during his kaizen events. I was in charge of the manufacturing design group and the machine shop and one thing that that he drove home was that we needed quick implementation of the of the improvement suggestions generated by the team. Any over time restrictions were put on hold during his events and we were expected to work late into the evenings or come early in the morning to complete that days ideas to maintain enthusiasm for the event and to show team members that their ideas would be implemented and very quickly. The effect on the team was a an eye opening feeling of empowerment that their suggestions for improvement were taken very seriously which of course lead to more Ideas and complete buy-in from the kaizen team. I learned a lot from Dave on motivating and creating enthusiasm during this particularly difficult time.

Randy Neumann
Dave and I worked together on an almost daily basis for over the last couple of years. We collaborated on many NPI (new product) projects together for Philips. He was always diligent, resourceful, and went out of his way to be proactive.

LinkedIn User
I worked with Dave for 11 years. Probably his best work came after the 2000 telecom meltdown where businesses like ours were suddenly struggling to survive. Without a lot of money to spend on capital equipment improvements, Dave was tasked with Leaning out the factory to reduce costs with a minimum of expense. Dave works very well at all levels and particularly well with hourly personnel with a combination of cat herding and humor during his kaizen events. I was in charge of the manufacturing design group and the machine shop and one thing that that he drove home was that we needed quick implementation of the of the improvement suggestions generated by the team. Any over time restrictions were put on hold during his events and we were expected to work late into the evenings or come early in the morning to complete that days ideas to maintain enthusiasm for the event and to show team members that their ideas would be implemented and very quickly. The effect on the team was a an eye opening feeling of empowerment that their suggestions for improvement were taken very seriously which of course lead to more Ideas and complete buy-in from the kaizen team. I learned a lot from Dave on motivating and creating enthusiasm during this particularly difficult time.

Randy Neumann
Dave and I worked together on an almost daily basis for over the last couple of years. We collaborated on many NPI (new product) projects together for Philips. He was always diligent, resourceful, and went out of his way to be proactive.

LinkedIn User
I worked with Dave for 11 years. Probably his best work came after the 2000 telecom meltdown where businesses like ours were suddenly struggling to survive. Without a lot of money to spend on capital equipment improvements, Dave was tasked with Leaning out the factory to reduce costs with a minimum of expense. Dave works very well at all levels and particularly well with hourly personnel with a combination of cat herding and humor during his kaizen events. I was in charge of the manufacturing design group and the machine shop and one thing that that he drove home was that we needed quick implementation of the of the improvement suggestions generated by the team. Any over time restrictions were put on hold during his events and we were expected to work late into the evenings or come early in the morning to complete that days ideas to maintain enthusiasm for the event and to show team members that their ideas would be implemented and very quickly. The effect on the team was a an eye opening feeling of empowerment that their suggestions for improvement were taken very seriously which of course lead to more Ideas and complete buy-in from the kaizen team. I learned a lot from Dave on motivating and creating enthusiasm during this particularly difficult time.

Randy Neumann
Dave and I worked together on an almost daily basis for over the last couple of years. We collaborated on many NPI (new product) projects together for Philips. He was always diligent, resourceful, and went out of his way to be proactive.

LinkedIn User
I worked with Dave for 11 years. Probably his best work came after the 2000 telecom meltdown where businesses like ours were suddenly struggling to survive. Without a lot of money to spend on capital equipment improvements, Dave was tasked with Leaning out the factory to reduce costs with a minimum of expense. Dave works very well at all levels and particularly well with hourly personnel with a combination of cat herding and humor during his kaizen events. I was in charge of the manufacturing design group and the machine shop and one thing that that he drove home was that we needed quick implementation of the of the improvement suggestions generated by the team. Any over time restrictions were put on hold during his events and we were expected to work late into the evenings or come early in the morning to complete that days ideas to maintain enthusiasm for the event and to show team members that their ideas would be implemented and very quickly. The effect on the team was a an eye opening feeling of empowerment that their suggestions for improvement were taken very seriously which of course lead to more Ideas and complete buy-in from the kaizen team. I learned a lot from Dave on motivating and creating enthusiasm during this particularly difficult time.

Randy Neumann
Dave and I worked together on an almost daily basis for over the last couple of years. We collaborated on many NPI (new product) projects together for Philips. He was always diligent, resourceful, and went out of his way to be proactive.

Experience
-
US Motion | Frencken America
-
United States
-
Automation Machinery Manufacturing
-
1 - 100 Employee
-
Process/Project Engineer
-
Nov 2020 - Present
-
-
-
International Aerospace Coatings
-
Ireland
-
Airlines and Aviation
-
100 - 200 Employee
-
Corporate Quality Systems and Process Improvement Engineer
-
Feb 2018 - Oct 2020
-
-
-
Zodiac Aerospace
-
France
-
Aviation and Aerospace Component Manufacturing
-
700 & Above Employee
-
Lean Manager
-
Nov 2014 - Jan 2018
• Lean consultant to Engineered Material’s division of aerospace honeycomb, formulations, prepreg fiberglass material products, and detailed structures. • Program Manager for the development and execution of Hoshin Kanri strategy deployment. • Support 4 different Value Stream Managers in the quest for continuous improvement & 5S+1. • Lean Steering Committee Facilitator, Lean Team Coach, Safety Committee team coach/member. • Ongoing coaching and engaging all employees in employing problem solving tools. Current activities utilizing 8D’s, and A3’s to reduce Honeycomb Block scrap and improve Panel process flow activities’. • Site focal point for implementing corporate FOCUS plan consisting of 4 key pillars and cultural change initiatives to succeed in operational excellence: enhanced KPI operational metrics and reporting, MRP cleansing and improvement, Supply Chain, and implementing S&OP. • Developed, standardized, and implemented KPI Daily Metric System boards for all work cells. Show less
-
-
-
The Everett Clinic
-
United States
-
Medical Practices
-
700 & Above Employee
-
Lean Consultant
-
Jan 2010 - Oct 2014
• Facilitated several RPI events in support of the clinics Orthopedic Model Line project. Primary objectives were to implement standard work for: scheduling, after visit summary, casting orders, medication and results plan, and reduce patient wait time by 20%. • Conducted 5S workshop in our ENT department to reduce MA/Nurse search time for meds, supplies, and instruments. Implemented a kanban system to eliminate expiration of meds. • Completed redesign of Microbiology Lab to improve work flow, reduce setup for ID and sensitivity specimens from 4.8 min to 2 min, reduce risk of contamination, allow room for new technology equipment, and prepare the lab for CAP certification in 2013. • Responsible for training specialty providers and staff in lean basics, applications for using A3’s, ACT team (Kaizen improvement) system, Value Stream mapping, our Data Management System (DMS), and project management. • Co-lead ROI project to justify purchasing the EPIC OpTime surgery software module for our Ambulatory Surgery Center. Resulted in 2.4 year payback, 9 FTE savings, 29% reduction in process steps. • Designed and mentored a project planning education program for TEC executive management team. • Implemented waterstrider concept and Kanban system throughout our newly opened 65,000 s.f. clinic to ensure all supplies are ready and available to our Provider, Nursing and MA staff. • Drove to merge Lean with Infection Control to enhance OR turnover cleaning in our Ambulatory Surgical Center. Developed standard work to reduce decontamination and disinfection issues while improving cleaning efficiency and reducing travel. Show less
-
-
-
Philips Lifeline
-
Medical Equipment Manufacturing
-
400 - 500 Employee
-
Supply Chain Engineering, Senior Process Engineer
-
2007 - 2009
• Facilitate Value Stream Map and Lean Kaizen events for Mid/High product line. • Manage projects for ultrasound Proto Shop NPI engineering process activities ensuring all Lean, Six Sigma, and DFM principles are in place through all supply chain operation processes. • Compose all development, implementation, and maintenance of assembly instructions and SOP’s for mid to high priced ultrasound products. • Programmed all process activities for new HD 15 Ultrasound engineering builds leading up to First Customer Shipment including the following hands on design and lean implementation activities: o Balanced line, layout, 2 bin replenishment, BOM structure, workstation design, 5S, tooling, ergonomics, training, MRP, and administrative process flow. o Team member working on site with suppliers to ensure cost, quality, and delivery of materials. • Facilitate lean activities for all mid to high priced ultrasound systems. Recently completed A3 for one piece flow in our HD 11 assembly line reducing headcount from 12 to 10, WIP from 30 to 4 units, and floor space from 1867 s.f. to 890 s.f. This floor space savings provided space for our new HD 15 assembly line. • Completed A3 to introduce one piece flow through test area and synchronize with assembly, reduce WIP, and improve delivery predictability. Show less
-
-
-
General Dynamics C4 Systems
-
United States
-
Computers and Electronics Manufacturing
-
Senior Manufacturing Engineer
-
Feb 2006 - Jul 2007
• Established all new and sustaining wireless rugged mobile laptop SOP’s and process improvements. • Lean Facilitator and Trainer for rugged, semi rugged, and handtop mobile laptop platforms. • Completed Current State VSM in Service Repair Center to determine process improvement opportunities. I facilitated the 1st lean event in the PCB Repair area improving productivity by 20% and reduced inventory from $1.2M to under $500K. A 2nd lean event was held within the Repair Center and was facilitated by a co-teammate which I trained, resulting in 30% improvement in productivity and performance, and a 25% first pass yield improvement. The 3rd lean event was in the CTO area and resulted in a 35% cycle time reduction. • Facilitated and trained all Operations personnel in “Lean 101” to enhance lean principles and tools. • Rugged laptop NPI team member. Responsibility was to gather, examine, and interpret information from all team resources and generate solutions to problems and make good business decisions. • Worked on site with foreign and domestic suppliers to develop and improve their processes as a team. o Overseeing of builds on supplier sites to balance supply and demand and ensure the timely and profitable movements of goods from demand to consumption. o Measure supply chain performance and build trust relationships with our supply chain partners. o Negotiated and problem solved on site supplier issues as a team to contribute cost savings for both. Show less
-
-
-
Meridian Yachts
-
Canada
-
1 - 100 Employee
-
Lean Manager
-
Feb 2004 - Feb 2006
• Senior Manager reporting to Plant Manager. • Negotiated and facilitated successful implementation of lean events, projects, process improvements, and training for all of Meridian Yachts personnel utilizing the TPS program. • Led 8 major lean events and 15 separate lean/5S projects within our lamination, woodshop, assembly, and wire harness shops contributing to an annual cost savings of $575,000. • Completed Current and Future State Value Stream Map of our 34’ yacht to determine non-value added process improvement opportunities. First lean event was the development of Standard Work. • Completed 1st Six Sigma green belt project to improve our bonded window installation quality. • Staffed with corporate Lean team to work at our Maxum boat plant and follow a specific one-year Lean implementation roadmap plan. Objective was to leverage learning’s and than facilitate and negotiate the implementation plan within our own facility utilizing employee involvement teams. • Team member involved in Value Stream Mapping the Spokane wire harness processes in preparation of transitioning to Arlington facility. Successfully completed transition without impact to quality, productivity schedule, cost, or performance while implementing process improvement solutions. Show less
-
-
-
Telect
-
United States
-
Business Consulting and Services
-
Senior Industrial Engineer/Production Manager/Lean Facilitator
-
Jan 1993 - Feb 2004
• Lean and 5S Facilitator. Trained all Operations personnel in TPS lean principles and led 11 lean events and assisted with 3 leading to a reduction of; costs by $942K, lead times by 55%, floor space by 45%, WIP by 90%, NVA time by 20%-40%, safety issues by 66%, and 5S levels from 1 to 3 (out of a score of 5). • Project Manager responsible for setting up new Integrated Systems Division with plant layout, processes, tooling, and equipment. Project completed on schedule. • Staff member of Fiber Optic NPI manufacturing team. Accountable for reviewing new designs for quality, costs, manufacturability, and lean process development. • Managed 70 manufacturing employees which included developing a yearly $2 million budget, determined capacity plans and constraints, and set up job schedules for on time delivery, quality, cost, and productivity. • Accountable for meeting product delivery schedules, maintaining a safe work environment, motivating, staffing, training, and performance measurement systems. • Facilitated employee involvement and lean work teams to achieve measurable team KPI’s. • Owner and trainer of global Oracle ERP software for BOM, WIP, and Capacity applications. • Facilitated on-site training at Mexico and Poland facilities on Oracle ERP applications. • Core team member of the first Telect acquisition. Worked as Operations Project Manager for product transition from the acquired company in Monterrey, Mexico to our Guadalajara, Mexico plant. • Project Manager for completing layout of manufacturing plant and move to new facility on scheduled date while managing time to implement responsible applications for new Oracle ERP applications. • Diagnosed all cost analysis related to production capital equipment and process changes. Show less
-
-
-
Boeing Commercial Airplanes
-
1 - 100 Employee
-
Methods Analyst
-
Apr 1986 - Dec 1992
• Senior Load Analyst for tooling, machine shop, and emergent production shops; managed six employees. • Developed and made recommendations for production shop process flow improvements utilizing Lean concepts. • Analyzed facility layouts and recommended changes as required. • Cost analyzed and recommended new equipment needs. • Senior Load Analyst for tooling, machine shop, and emergent production shops; managed six employees. • Developed and made recommendations for production shop process flow improvements utilizing Lean concepts. • Analyzed facility layouts and recommended changes as required. • Cost analyzed and recommended new equipment needs.
-
-
Education
-
Webster University
MBA, Business Administration and Management, General -
Montana State University-Bozeman
Bachelor of Science, Industrial Technology, Minor: Industrial and Management Engineering -
University of Washington
Lean Six Sigma Green Belt Certification -
University of Michigan College of Engineering
Lean Certification
Community
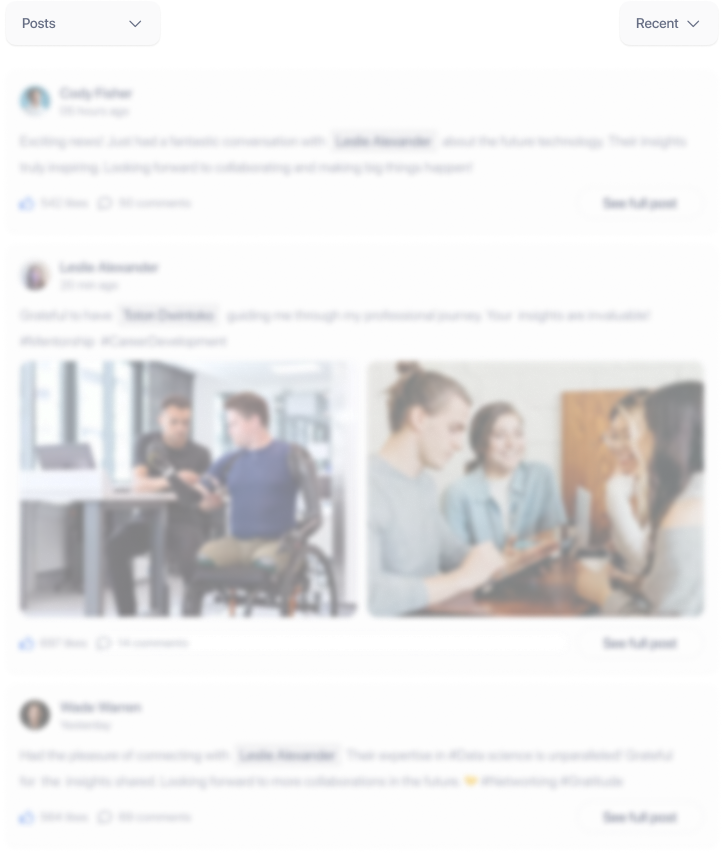