David Kulik, PE
Electrical Engineer at WEBB-STILES COMPANY- Claim this Profile
Click to upgrade to our gold package
for the full feature experience.
Topline Score
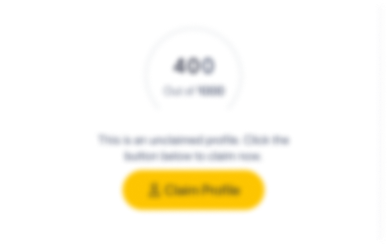
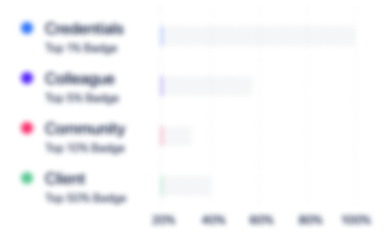
Bio
0
/5.0 / Based on 0 ratingsFilter reviews by:
Experience
-
WEBB-STILES COMPANY
-
United States
-
Industrial Machinery Manufacturing
-
1 - 100 Employee
-
Electrical Engineer
-
May 2014 - Present
-
-
-
RedViking
-
United States
-
Automation Machinery Manufacturing
-
1 - 100 Employee
-
Senior Project Engineer
-
May 2007 - May 2014
IPT conveyor control system based on a Siemens Step7 platform for PLC & HMI. Profibus, Ethernet & ASi bus communication protocols were used to interface with field devices and AGV’s. The control system coordinated the movement of 20 AGV’s with respect to work completed at 22 operating stations. My panel designs included MCP (1), track supply panels (3), HMI panels (3) & data communication panels (2). Following panel design I wrote the code for PLC & HMI’s. Robotic (Nachi) stations… Show more IPT conveyor control system based on a Siemens Step7 platform for PLC & HMI. Profibus, Ethernet & ASi bus communication protocols were used to interface with field devices and AGV’s. The control system coordinated the movement of 20 AGV’s with respect to work completed at 22 operating stations. My panel designs included MCP (1), track supply panels (3), HMI panels (3) & data communication panels (2). Following panel design I wrote the code for PLC & HMI’s. Robotic (Nachi) stations controls design with Atlas Copco nut runners and Allen Bradley CompactLogix. Ethernet and DeviceNet communication protocols were used between PLC, Robots & nut runners. The control system received engine type information from the plant’s network and selected the proper robot and nut runner bolt patterns and torque specifications. Interference zones were created to allow two robots to operate on the same engine. My panel designs included MCP (1), Robot gate plug enclosures (2), robot interface (2) and HMI (1). PLC and PanelView applications were developed to properly identify the pass/reject per bolt. High speed bullet assembly consisted of 5.56 mm bullet: case fabrication, case quality determination and bullet assembly. These high speed process (1200 rounds per minute) required a design philosophy based on reduced program scan and optimized communications. Tracking bullet/case flow thru the respective processes required physical properties traceability to each piece. Special control requirements included: high speed analog measurements (case and overall length, powder level, and lead presences), coordinate chain speed (100 inches/sec) across three drives to hold position within 1/8”, maintain Class 1 Div. 2 electrical classifications. My responsibilities included panel design, HMI application and PLC code. ControlNet communications protocol was used between PLC, drives and plant PLC interface. Show less IPT conveyor control system based on a Siemens Step7 platform for PLC & HMI. Profibus, Ethernet & ASi bus communication protocols were used to interface with field devices and AGV’s. The control system coordinated the movement of 20 AGV’s with respect to work completed at 22 operating stations. My panel designs included MCP (1), track supply panels (3), HMI panels (3) & data communication panels (2). Following panel design I wrote the code for PLC & HMI’s. Robotic (Nachi) stations… Show more IPT conveyor control system based on a Siemens Step7 platform for PLC & HMI. Profibus, Ethernet & ASi bus communication protocols were used to interface with field devices and AGV’s. The control system coordinated the movement of 20 AGV’s with respect to work completed at 22 operating stations. My panel designs included MCP (1), track supply panels (3), HMI panels (3) & data communication panels (2). Following panel design I wrote the code for PLC & HMI’s. Robotic (Nachi) stations controls design with Atlas Copco nut runners and Allen Bradley CompactLogix. Ethernet and DeviceNet communication protocols were used between PLC, Robots & nut runners. The control system received engine type information from the plant’s network and selected the proper robot and nut runner bolt patterns and torque specifications. Interference zones were created to allow two robots to operate on the same engine. My panel designs included MCP (1), Robot gate plug enclosures (2), robot interface (2) and HMI (1). PLC and PanelView applications were developed to properly identify the pass/reject per bolt. High speed bullet assembly consisted of 5.56 mm bullet: case fabrication, case quality determination and bullet assembly. These high speed process (1200 rounds per minute) required a design philosophy based on reduced program scan and optimized communications. Tracking bullet/case flow thru the respective processes required physical properties traceability to each piece. Special control requirements included: high speed analog measurements (case and overall length, powder level, and lead presences), coordinate chain speed (100 inches/sec) across three drives to hold position within 1/8”, maintain Class 1 Div. 2 electrical classifications. My responsibilities included panel design, HMI application and PLC code. ControlNet communications protocol was used between PLC, drives and plant PLC interface. Show less
-
-
-
Ford Motor Company
-
United States
-
Motor Vehicle Manufacturing
-
700 & Above Employee
-
Controls Engineer
-
May 2005 - May 2007
Supported the launch of Ford’s new V6 3.5 Liter Duratec engine (D35). In this capacity, I worked with OEM's for the design, build and installation of engine assembly facilities. These activities included: specification writing, drawing review, factory buy-offs, manufacturing equipment start-up assistance, facility support after plant buy-off. Control's engineer for “in-house” projects that supported the D35launch. I designed control systems (AutoCAD drawings and software applications)… Show more Supported the launch of Ford’s new V6 3.5 Liter Duratec engine (D35). In this capacity, I worked with OEM's for the design, build and installation of engine assembly facilities. These activities included: specification writing, drawing review, factory buy-offs, manufacturing equipment start-up assistance, facility support after plant buy-off. Control's engineer for “in-house” projects that supported the D35launch. I designed control systems (AutoCAD drawings and software applications) for new facilities that could be completed by plant forces. Specifically, I integrated new facilities into the plant’s existing equipment. Typical tasks included: adding new conveyor sections, servo rotates & turn tables (Indramat), EMS RF Tag read/write units, Interbus communication channel revisions, and ASi bus additions. The plant’s automation equipment is supported on a Schneider Premium PL7 platform. I’ve developed my own the PL7 programming logic for these equipment additions.
-
-
Automation Engineer
-
May 1990 - May 2005
Responsible for all automation in the Econoline Final Assembly area. Provided controls design, AutoCAD drawings, machine / robot programming and facility start-up assistance for all “In-house” projects. Examples of my “In-house” projects: automatic VIN stamping of frames, robotic primer application to body flange, robotic loading of leaf springs, vehicle frame transfer automation (lift & carry from one moving line to another), conversion of eddy current motor control to VFD motor control on… Show more Responsible for all automation in the Econoline Final Assembly area. Provided controls design, AutoCAD drawings, machine / robot programming and facility start-up assistance for all “In-house” projects. Examples of my “In-house” projects: automatic VIN stamping of frames, robotic primer application to body flange, robotic loading of leaf springs, vehicle frame transfer automation (lift & carry from one moving line to another), conversion of eddy current motor control to VFD motor control on production lines, and conversion of “relay” based panels to PLC control. For all automation in the plant, I designed system control improvements, error proofing, troubleshoot breakdowns and modified programming to facilitate plant requirements. Control equipment that I supported: Allen Bradley PLC2, PLC5 & SLC500. Allen Bradley motion controllers, Allen Bradley VFD’s and servos, Allen Bradley PanelView, ABB robots (IRB6000, 3000 & 90), GE Motor Control Centers, plus a wide range of I/O devices (prox switches, photo eyes, limits, encoders, light screens, floor mats, vision systems and pressure transducers).
-
-
-
-
Technical Services Manager
-
1984 - 1988
I managed a department responsible for the operation and maintenance of natural gas measurement facilities, communication (radio, telephone, and microwave) equipment, SCADA systems, electronic measurement systems, and pipe line corrosion (internal and external) facilities. These facilities were primarily located in the High Island area of the Gulf of Mexico. I managed a department responsible for the operation and maintenance of natural gas measurement facilities, communication (radio, telephone, and microwave) equipment, SCADA systems, electronic measurement systems, and pipe line corrosion (internal and external) facilities. These facilities were primarily located in the High Island area of the Gulf of Mexico.
-
-
Education
-
Lamar University
MBA -
Wayne State University
BSEE, Electrical Engineering
Community
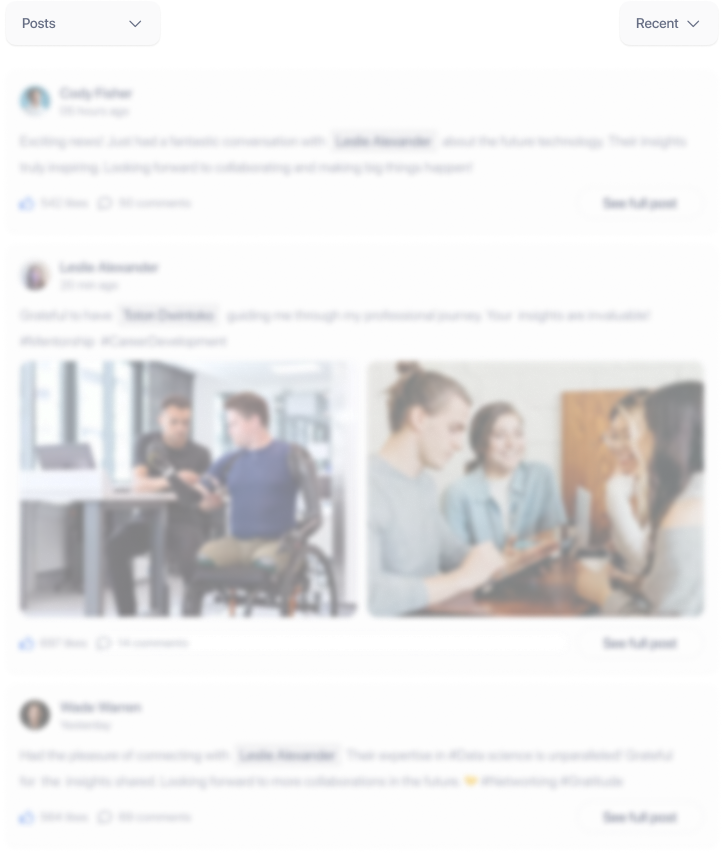