David Kivisto
General Manager at Envoy Source- Claim this Profile
Click to upgrade to our gold package
for the full feature experience.
Topline Score
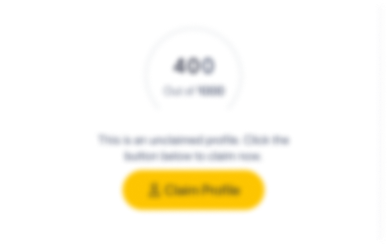
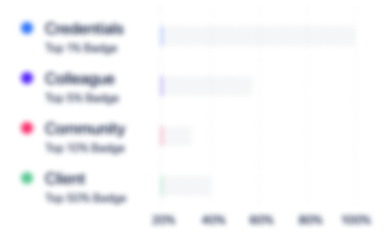
Bio

Erika Gilbert Jarrett, PHR, SHRM-CP
In my 20 years as an HR professional, Dave is one of the most in touch Operational Leaders I have had the opportunity to work with. He is operationally savvy and understands how to connect with and empower people to strive for excellence. When people buy in to the company vision, they can move mountains. Dave is a motivating and engaging leader who focuses on building a team culture focused on safety, customer service, and quality delivery. I recommend Dave if you are looking for a team builder to take your operation to the next level.

Sinan Aunallah
I had the opportunity to work with Dave Kivisto for over 10 years. During this long journey, I’ve seen Dave take on many challenges in the organization and come up with genius solutions with positive outcomes. Dave is an outstanding individual who has an innovative mindset when faced with solving challenges and issues. He certainly added a tremendous amount of value to Technicolor and continues to do so currently. Dave is an outstanding Mentor, Leader, and a Colleague who possesses excellent organizational and communication skills. Under his leadership, many of us were able to flourish and develop our careers and professional growth. Throughout his career, Dave has had the opportunity to interact with many customers, vendors, and top management from various corporate levels internally and externally within Technicolor. He has gained the experience of a top executive and would serve as an excellent professional leader to any organization. I highly recommend Dave Kivisto for any position that he pursues in the future.

Erika Gilbert Jarrett, PHR, SHRM-CP
In my 20 years as an HR professional, Dave is one of the most in touch Operational Leaders I have had the opportunity to work with. He is operationally savvy and understands how to connect with and empower people to strive for excellence. When people buy in to the company vision, they can move mountains. Dave is a motivating and engaging leader who focuses on building a team culture focused on safety, customer service, and quality delivery. I recommend Dave if you are looking for a team builder to take your operation to the next level.

Sinan Aunallah
I had the opportunity to work with Dave Kivisto for over 10 years. During this long journey, I’ve seen Dave take on many challenges in the organization and come up with genius solutions with positive outcomes. Dave is an outstanding individual who has an innovative mindset when faced with solving challenges and issues. He certainly added a tremendous amount of value to Technicolor and continues to do so currently. Dave is an outstanding Mentor, Leader, and a Colleague who possesses excellent organizational and communication skills. Under his leadership, many of us were able to flourish and develop our careers and professional growth. Throughout his career, Dave has had the opportunity to interact with many customers, vendors, and top management from various corporate levels internally and externally within Technicolor. He has gained the experience of a top executive and would serve as an excellent professional leader to any organization. I highly recommend Dave Kivisto for any position that he pursues in the future.

Erika Gilbert Jarrett, PHR, SHRM-CP
In my 20 years as an HR professional, Dave is one of the most in touch Operational Leaders I have had the opportunity to work with. He is operationally savvy and understands how to connect with and empower people to strive for excellence. When people buy in to the company vision, they can move mountains. Dave is a motivating and engaging leader who focuses on building a team culture focused on safety, customer service, and quality delivery. I recommend Dave if you are looking for a team builder to take your operation to the next level.

Sinan Aunallah
I had the opportunity to work with Dave Kivisto for over 10 years. During this long journey, I’ve seen Dave take on many challenges in the organization and come up with genius solutions with positive outcomes. Dave is an outstanding individual who has an innovative mindset when faced with solving challenges and issues. He certainly added a tremendous amount of value to Technicolor and continues to do so currently. Dave is an outstanding Mentor, Leader, and a Colleague who possesses excellent organizational and communication skills. Under his leadership, many of us were able to flourish and develop our careers and professional growth. Throughout his career, Dave has had the opportunity to interact with many customers, vendors, and top management from various corporate levels internally and externally within Technicolor. He has gained the experience of a top executive and would serve as an excellent professional leader to any organization. I highly recommend Dave Kivisto for any position that he pursues in the future.

Erika Gilbert Jarrett, PHR, SHRM-CP
In my 20 years as an HR professional, Dave is one of the most in touch Operational Leaders I have had the opportunity to work with. He is operationally savvy and understands how to connect with and empower people to strive for excellence. When people buy in to the company vision, they can move mountains. Dave is a motivating and engaging leader who focuses on building a team culture focused on safety, customer service, and quality delivery. I recommend Dave if you are looking for a team builder to take your operation to the next level.

Sinan Aunallah
I had the opportunity to work with Dave Kivisto for over 10 years. During this long journey, I’ve seen Dave take on many challenges in the organization and come up with genius solutions with positive outcomes. Dave is an outstanding individual who has an innovative mindset when faced with solving challenges and issues. He certainly added a tremendous amount of value to Technicolor and continues to do so currently. Dave is an outstanding Mentor, Leader, and a Colleague who possesses excellent organizational and communication skills. Under his leadership, many of us were able to flourish and develop our careers and professional growth. Throughout his career, Dave has had the opportunity to interact with many customers, vendors, and top management from various corporate levels internally and externally within Technicolor. He has gained the experience of a top executive and would serve as an excellent professional leader to any organization. I highly recommend Dave Kivisto for any position that he pursues in the future.

Credentials
-
Lean Manufacturing Certificate Program at the University of Michigan
University of Michigan- College of Engineering- Center for Professional Development
Experience
-
Envoy Source
-
United States
-
Transportation, Logistics, Supply Chain and Storage
-
1 - 100 Employee
-
General Manager
-
Mar 2021 - Present
Oversee all facility activities to include P&L owner for this Electronic Device packaging operation to include intensive QC of inbound devices, warehousing of high value items, and packaging/shipping of serialized goods with extremely strict quality and accountability guidelines of a high profile client. Designed facility flow, implemented Lean processes throughout the facility, and built and high performance team to transition the Operation from a significant loss in its first 6 months to a healthy overall profit in the subsequent 12 months after starting with the company. Steady gains realized month by month during this transition. Show less
-
-
-
Technicolor Creative Studios
-
United States
-
Entertainment Providers
-
700 & Above Employee
-
Senior Director of Operations
-
Dec 2017 - Feb 2021
• Direct all operations departments in the facility and collaborate with support groups including HR, LP, QA, and Finance, scheduling product to be inducted and scanned into the Q-Scan system and managing WHS and Distribution for the facility• Manage 40K SKUs in a National Return Center Operation, scanning into 3 primary categories from Q-Scan through miles on conveyors/diverts and into hundreds of pack out chutes • Designed and implemented a new scheduling program, utilizing inbound SKU data to improve flow through the facility, resulting in decreasing downtime and maximizing plant utility, leading to $1.3M savings in operating costs the 1st year• Overcame temporary agency change and pay rate challenges by developing a labor planning process and work station assignments, more effectively utilizing workforce, resulting in a 25% headcount reduction while increasing run efficiency and eliminating WIP caused by bottlenecks• Engage with associates on floor and implemented one on one mentoring and training initiatives, a key element to achieve a 25% increase in productivity •Created “Intel Day” scanning strategy that involves inducting/scanning returns with high quantity SKUs and concentrating a reduced staffing model into hot zones, resulting in CPU reductions of 25% to 33%• Established inbound appointment scheduling to match optimal client mix percentage to maximize efficiency, resulting in reduced downtime and lower costs •Developed bulk/manual processing stations for high-velocity and cumbersome sized SKUs to eliminate bottlenecks• Introduced flow improvements of packaging rework lines, increasing throughput by over 25% while reducing quality defects by 50%•Installed visual aids in pack out chutes to maximize efficiency, decreasing packing time by 60% •Eliminated 2nd shift following the implementation of improvement actions Show less
-
-
Sr. Director of Operations/Reverse Logistics
-
Dec 2017 - Feb 2021
-
-
Technicolor - Senior Director of Packaging Operations
-
Jul 2013 - Dec 2017
• Managed 1200 employees within 4 different buildings consisting of packaging, custom packaging, and building display ready pallets • Established a training verification program including 3 successful verifications to earn certification, increasing productivity on the lines by 30%• Developed Kitting Operation to improve material, component accuracy, timeliness, and flow of materials to the assembly lines, increasing efficiency and allowing for process improvement to achieve a 99.9% inventory accuracy• Assigned by the President in 2011 to help the Memphis team increase packaging line output from 14K to 24K per line, following inviting and hosting key Memphis personnel in the Michigan plant and teaching best practices• Led project to relocate Michigan operation to Memphis upon closing of MI Pkg Operation in 2015 by completing building redesign, increasing service clients from 5 to 60 in 2014 with 48 automated assembly lines at $1M to $1.5M per line• Designed facility layout for optimal material flow for front line packaging through the 922K sq ft facility that is the largest of its kind globally, leading to 2M units leaving daily as the highest volume plant in the world• Led efforts to achieve ISO Certification in multiple facilities and departments over several years, resulting in meeting audit compliance standards and managing customers with tight processes including quality and security specifications • Spearheaded Operation Courage to train managers and supervisors to be good leaders and consistently seek opportunities to mentor employees, increasing efficiency and productivity through leadership training Show less
-
-
Community
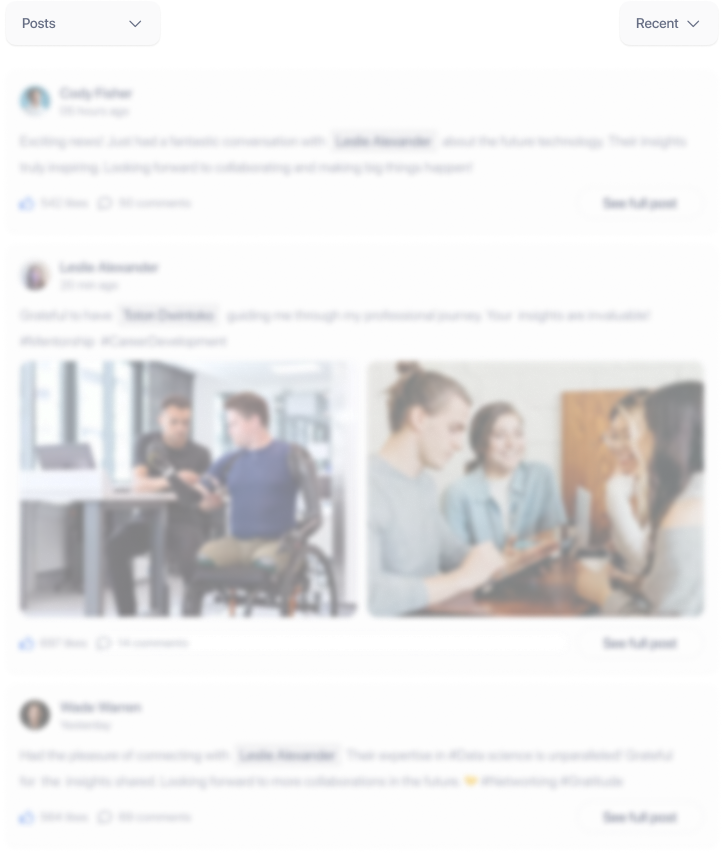