David Juarez
Buyer/ Supply Chain at FPE: Fluid Power Energy/Filtration Systems, Inc- Claim this Profile
Click to upgrade to our gold package
for the full feature experience.
Topline Score
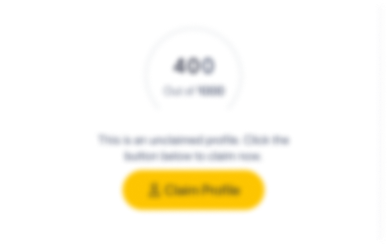
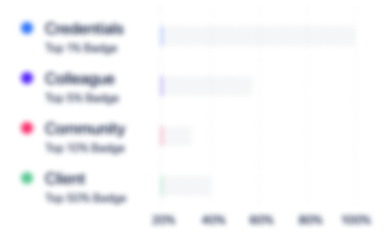
Bio

Brent Stinebaugh
David is consistently a pleasure to work with. As a purchaser, he is detailed, organized, and always fair. His communication and follow-up with vendors is outstanding.

Brent Stinebaugh
David is consistently a pleasure to work with. As a purchaser, he is detailed, organized, and always fair. His communication and follow-up with vendors is outstanding.

Brent Stinebaugh
David is consistently a pleasure to work with. As a purchaser, he is detailed, organized, and always fair. His communication and follow-up with vendors is outstanding.

Brent Stinebaugh
David is consistently a pleasure to work with. As a purchaser, he is detailed, organized, and always fair. His communication and follow-up with vendors is outstanding.

Experience
-
FPE: Fluid Power Energy
-
United States
-
Oil and Gas
-
1 - 100 Employee
-
Buyer/ Supply Chain
-
Jan 2021 - Present
-
-
-
ProSonix Steam Injection Heating Solutions
-
United States
-
Machinery Manufacturing
-
1 - 100 Employee
-
Buyer/ Production Supervisor
-
Aug 2018 - Nov 2019
Reported directly to the president and owner of the company. Directed overall production operations ensuring the achievement of production objectives at the lowest cost consistent with the company quality standards and customer delivery requirements. Organized and controlled release of work order documents to the assembly force to support on-time delivery goals and to inform the sales team of production status to our customers. Produce metrics/ analytics on inventory usage, forecast and projected inventory levels with a just in time emphasis. Sourced machining of stainless steel to specific tolerances for steam injection heating solutions. Lead and Coordinated weekly production meetings with updated lead times from machining companies and production status.
-
-
-
In-Place Machining Company
-
United States
-
Machinery Manufacturing
-
1 - 100 Employee
-
Buyer/Accounts Payable Specialist
-
Feb 2015 - Apr 2018
Reporteddirectly to the CFO. Responsible for the complete purchasing Process for 2 global machine servicescompanies. Overseen and executed an annual spend of approximately $3.0M annually. Coordinatedwith Machinist, tool crib attendants, maintenance and Engineers to procure goods and services in acritical time base to ensure In-Place is equipped with the essential tools for on time job completion.Purchased all goods and services used by the company in its day-to-day operations such as raw material(A36 plate, brass, Inconel, 316 stainless steel and aluminum). specialized tooling ( custom reamers,progressive taps with precise class of fit for tight tolerances, custom slip/ fixed renewable bushingsand go/no go gages.), shop and administrative supplies ( Kennametal, Sandvick, Green Leaf and David Juarez Davidsjuarez37@gmail.com 2426 South 74th Street, West Allis WI 53219 Cell 262-613-9757Ingersoll inserts, end Mills, tool holders) and a wide range of outside services ( Burnouts/ Stress relief,custom centrifugal castings, precision grinding, chrome and anodize plating and EDM cutting withMicrosoft Great Plains system. I Reconciled all invoices, packing slips and verified compliance with thePurchase order and approved the payment. Classified accounting codes structure to accurately andeffectively report financial activities. Review statements from Vendor’s billing departments andprovided details on payments. Meet and greet with sales Representatives to ensure the companyreceived the best pricing and lead time for consistent orders. Request machining quotes for theengineering department and Sales department with PDF, Cad and solid work drawings. Creating packingslips and UPS/ FedEx shipments for items that needed to ship to job sites and hotels where themachinist was stationed.ACCOMPLISHMENTS: Provided c
-
-
-
-
Buyer
-
May 2013 - Aug 2015
Supply chain manager Reported directly to the CEO. Primarycontact person for specialized vendor base. Managed the planning, procurement, storage anddistribution of goods and services. Established Purchasing policies and procedures to control overspending per department. Provided support to Production scheduling on all materials flow issues tomeet deadlines and customer’s requirements. Coordinate with appropriate departments to scheduledeliveries of material purchased such as: raw steel, out purchased machining, consumables, cement andPPE with the Just-in-time methodology. Researched and visited steel companies across the U.S. andprocured filling material by gathering samples and measuring the density and determining the value inthe counterweights. Procured capital goods for building upgrades, maintenance and equipment such asforklifts, paint booth and overhead cranes. Designed and implemented a tool crib and Kanban programfor specific hardware used on high volume production to minimize inventory costs. Interpretedmachining drawings, Initiated and completed bid/quote process for machined parts and prototypes.Vendor set up- negotiating pricing and terms, face to face contact with outside sales representatives andvisiting suppliers throughout the country. Directed monthly inventory and audit process to ensureaccurate counts for product development.
-
-
-
-
Administrative Purchaser
-
Apr 2011 - May 2013
Reported directly to the Materials Manager.Administer a centralized purchasing program in the procurement of materials and services under the ISO9001 compliance/ checklist. Responsibilities included purchasing, production and inventory control,scheduling, logistics, receiving and warehouse functions. Negotiated prices, lead times and paymentterms of raw materials such as steel punching's, high carbon ferror, moly and nickel along with a diverseselection of commodities. Analyze market trends for pricing raw materials and work with themetallurgist to determine cost effective ways to calculate the alloy’s chemistry. Supplier evaluations andapproval based on previous performance and Supplier Audits. Maintained quality records of suppliersfor yearly audits.
-
-
-
-
Assistant Supervisor
-
Mar 2009 - Sep 2010
Organized weekly tasks and supervised 10 members Maintained communication between sub contractors, residents and visitors in English and Spanish.Managed and executed projects in a timely fashion Organized weekly tasks and supervised 10 members Maintained communication between sub contractors, residents and visitors in English and Spanish.Managed and executed projects in a timely fashion
-
-
-
-
Material Coordinator
-
Aug 2008 - Feb 2009
Utilized department computer systems/programs in an effort to accurately input inventoryAcquired skills needed to safely operate a forkliftPrepared accurate inventory count for approximately 20 shipments per day Utilized department computer systems/programs in an effort to accurately input inventoryAcquired skills needed to safely operate a forkliftPrepared accurate inventory count for approximately 20 shipments per day
-
-
-
-
Assistant Supervisor
-
Feb 2004 - Jun 2007
Managed multiple priorities in a fast-paced environment.Ensured customers' satisfaction, from investigating and resolving complaints to clearing tablesTrained over 50 new wait staff members in quality customer service and product knowledge Managed multiple priorities in a fast-paced environment.Ensured customers' satisfaction, from investigating and resolving complaints to clearing tablesTrained over 50 new wait staff members in quality customer service and product knowledge
-
-
Education
-
Carroll University
Bachelor of Science, Information Technology; an emphasis in Business and Social Applications
Community
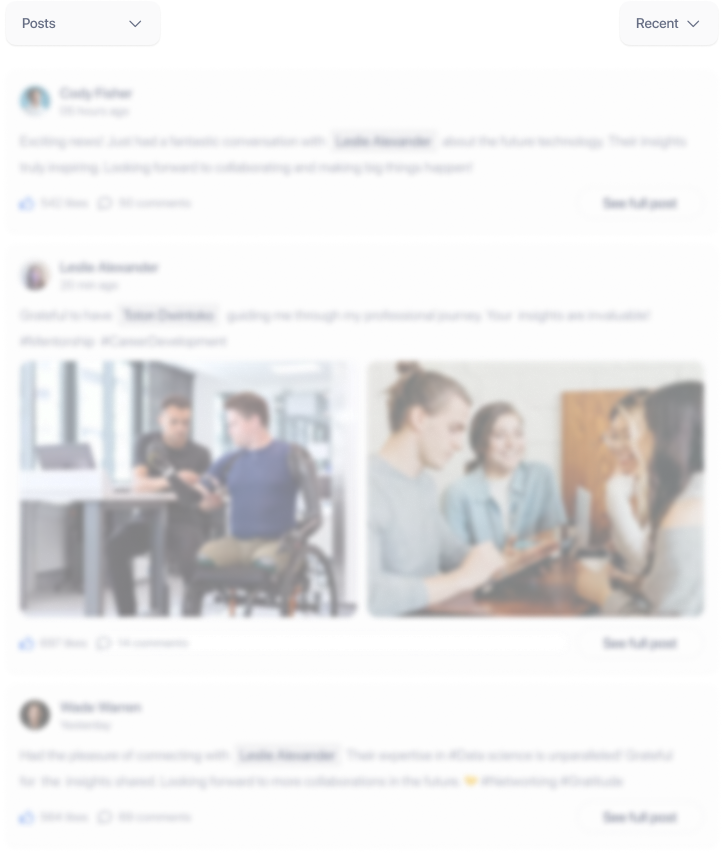