David Jackson
Steelmaking Process Coordinator at Valbruna ASW- Claim this Profile
Click to upgrade to our gold package
for the full feature experience.
-
English -
Topline Score
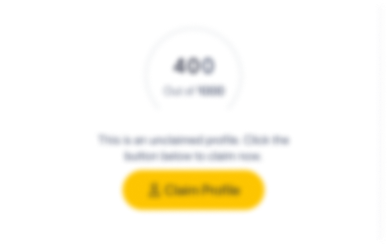
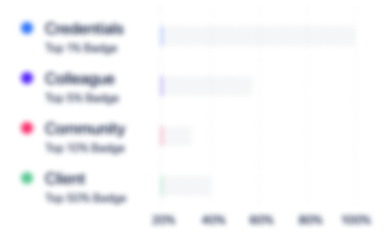
Bio


Credentials
-
Pipe Welding: Technical Standards
(TSSA) -
Forecasting & Allocation Management
ERP, US Steel -
Six Sigma Yellow Belt, Green Belt Training Ongoing
Continuous Casting Certificate: Association for Iron & Steel Technology, Chicago, IL
Experience
-
Valbruna ASW
-
Canada
-
Industrial Machinery Manufacturing
-
1 - 100 Employee
-
Steelmaking Process Coordinator
-
Jun 2022 - Present
Recruited as a Melt Shop Process Coordinator for this premier specialty steelmaking facility, I oversee 2 Operating Shift Managers while promoting safety program compliance and supporting all safety program initiatives. • Assisting shift managers to drive productivity. • Liaising between operating groups and maintenance services to address and resolve mechanical and electrical deficiencies. • Collaborating with quality and process metallurgists to ensure quality compliance and… Show more Recruited as a Melt Shop Process Coordinator for this premier specialty steelmaking facility, I oversee 2 Operating Shift Managers while promoting safety program compliance and supporting all safety program initiatives. • Assisting shift managers to drive productivity. • Liaising between operating groups and maintenance services to address and resolve mechanical and electrical deficiencies. • Collaborating with quality and process metallurgists to ensure quality compliance and meet KPIs. • Carefully examining melt shop process for improvement and efficiency. • Providing business case details to drive process improvements requiring capital. Key Accomplishments: ** Spearheading process improvements to reduce cost, optimize operational efficiency, and drive innovation. ► Working on bringing Best Practice Methodology to Welland to gauge yield loss and mitigate waste. >> Participated in training of new equipment currently being installed. >> Meeting with Senior level Operating Group to discuss the strategic plan. ► Automating systems to enhance accuracy and innovation. >> Partnering with IT architects to deploy new systems. ► Maximizing skill optimization of organizational workforce. >> Repurposing obsolete process and operations to value-added roles during cultural transition. Show less Recruited as a Melt Shop Process Coordinator for this premier specialty steelmaking facility, I oversee 2 Operating Shift Managers while promoting safety program compliance and supporting all safety program initiatives. • Assisting shift managers to drive productivity. • Liaising between operating groups and maintenance services to address and resolve mechanical and electrical deficiencies. • Collaborating with quality and process metallurgists to ensure quality compliance and… Show more Recruited as a Melt Shop Process Coordinator for this premier specialty steelmaking facility, I oversee 2 Operating Shift Managers while promoting safety program compliance and supporting all safety program initiatives. • Assisting shift managers to drive productivity. • Liaising between operating groups and maintenance services to address and resolve mechanical and electrical deficiencies. • Collaborating with quality and process metallurgists to ensure quality compliance and meet KPIs. • Carefully examining melt shop process for improvement and efficiency. • Providing business case details to drive process improvements requiring capital. Key Accomplishments: ** Spearheading process improvements to reduce cost, optimize operational efficiency, and drive innovation. ► Working on bringing Best Practice Methodology to Welland to gauge yield loss and mitigate waste. >> Participated in training of new equipment currently being installed. >> Meeting with Senior level Operating Group to discuss the strategic plan. ► Automating systems to enhance accuracy and innovation. >> Partnering with IT architects to deploy new systems. ► Maximizing skill optimization of organizational workforce. >> Repurposing obsolete process and operations to value-added roles during cultural transition. Show less
-
-
-
Harsco Corporation
-
Environmental Services
-
700 & Above Employee
-
Site Manager
-
2019 - Aug 2022
As a Site Manager, I worked for this division representing the world’s largest, most comprehensive provider of onsite material processing and environmental steel to the worldwide steel and metals industry that provides customers with waste management solutions. Oversight included 48 direct and 2 indirect reports with nearly $3.5 CAPEX and up to $1M P&L with 20+ heavy equipment pieces while reporting to the company President of North America. This role involved: •… Show more As a Site Manager, I worked for this division representing the world’s largest, most comprehensive provider of onsite material processing and environmental steel to the worldwide steel and metals industry that provides customers with waste management solutions. Oversight included 48 direct and 2 indirect reports with nearly $3.5 CAPEX and up to $1M P&L with 20+ heavy equipment pieces while reporting to the company President of North America. This role involved: • Boosting environmental performance and fostering health/safety compliance using the study of process, procedure, and evaluation of commercially available technology while driving profitability. • Devising CAPEX plans. Key Accomplishments: ** Recognized as a change leader for driving significant cost reductions, efficiencies, and safety improvements. ► Salvaged thousands in yearly fuel costs while gauging significant maintenance costs and optimizing productivity. >> Reinforced fiscal accountability in discretionary spending and equalizing equipment usage. ► Reengaged site staff in rectifying gaps in Joint Health and Safety Committee meetings. >> Met ISO audit goals, improved internal systems, and sustained zero reportable incidents. >> Coached staff and trialed slag handling methods. >> Addressed environmental non-compliance through executing high-risk activities assessment. ► Introduced product/service improvements to vendors. >> Weighed performance vs. benchmarks. >> Executed CPT Pilot Study on fleet of Rock Trucks; presented study to procurement for evaluation, consideration, and equipment contract negotiations. Show less As a Site Manager, I worked for this division representing the world’s largest, most comprehensive provider of onsite material processing and environmental steel to the worldwide steel and metals industry that provides customers with waste management solutions. Oversight included 48 direct and 2 indirect reports with nearly $3.5 CAPEX and up to $1M P&L with 20+ heavy equipment pieces while reporting to the company President of North America. This role involved: •… Show more As a Site Manager, I worked for this division representing the world’s largest, most comprehensive provider of onsite material processing and environmental steel to the worldwide steel and metals industry that provides customers with waste management solutions. Oversight included 48 direct and 2 indirect reports with nearly $3.5 CAPEX and up to $1M P&L with 20+ heavy equipment pieces while reporting to the company President of North America. This role involved: • Boosting environmental performance and fostering health/safety compliance using the study of process, procedure, and evaluation of commercially available technology while driving profitability. • Devising CAPEX plans. Key Accomplishments: ** Recognized as a change leader for driving significant cost reductions, efficiencies, and safety improvements. ► Salvaged thousands in yearly fuel costs while gauging significant maintenance costs and optimizing productivity. >> Reinforced fiscal accountability in discretionary spending and equalizing equipment usage. ► Reengaged site staff in rectifying gaps in Joint Health and Safety Committee meetings. >> Met ISO audit goals, improved internal systems, and sustained zero reportable incidents. >> Coached staff and trialed slag handling methods. >> Addressed environmental non-compliance through executing high-risk activities assessment. ► Introduced product/service improvements to vendors. >> Weighed performance vs. benchmarks. >> Executed CPT Pilot Study on fleet of Rock Trucks; presented study to procurement for evaluation, consideration, and equipment contract negotiations. Show less
-
-
-
STELCO - The Steel Company of Canada
-
Canada
-
Mining
-
700 & Above Employee
-
Area Manager - Steelmaking/Secondary Refining/Refractories
-
Jan 2015 - May 2017
Overseeing up to 140 direct reports, secondary refining (RHOB/LTS) and $3M CAPEX, this role involved: • Navigating BOF steelmaking and improving Secondary Refining, Refractories & Scrap Department. • Overseeing performance, safety training, compensation, and expenses. • Engaging key vendors in product improvements. • Reporting to the Divisional Manager. Key Accomplishments: ** Reengineered Scrap Department while surpassing unit performance, cost, quality, and… Show more Overseeing up to 140 direct reports, secondary refining (RHOB/LTS) and $3M CAPEX, this role involved: • Navigating BOF steelmaking and improving Secondary Refining, Refractories & Scrap Department. • Overseeing performance, safety training, compensation, and expenses. • Engaging key vendors in product improvements. • Reporting to the Divisional Manager. Key Accomplishments: ** Reengineered Scrap Department while surpassing unit performance, cost, quality, and safety targets. ► Honoured with VIP Award (2017) with Far Exceeds Rating vs. 2016 metrics. ► Reengineered Scrap Department previously managed by a third party––reducing operational costs. >> Crafted new job procedures. Developed commodity specification. >> Implemented new scrap handling department. ► Maximized efficiencies––reduced 4 staff members, eliminated 2 heavy equipment pieces, and optimized materials management. ► Elevated steel ladle life while conserving thousands of dollars in costs. >> Optimized steelmaking refractories.
-
-
Area Manager – HSF (Hot Strip Finishing) Logistics
-
2015 - 2017
I was promoted to coordinate and maintain the facility in HSF logistics while fostering health/safety compliance and cost-efficient operations. This role involved overseeing nearly 118 direct reports and a $1M budget while: • Controlling scheduling of Correction Mill along with Slab Conditioning Department. • Leading shipping activities. • Maintaining “Ready Steel” inventory to ship nearly $200,000 MT/month to the customer and inter-plant. • Navigating operating procedures… Show more I was promoted to coordinate and maintain the facility in HSF logistics while fostering health/safety compliance and cost-efficient operations. This role involved overseeing nearly 118 direct reports and a $1M budget while: • Controlling scheduling of Correction Mill along with Slab Conditioning Department. • Leading shipping activities. • Maintaining “Ready Steel” inventory to ship nearly $200,000 MT/month to the customer and inter-plant. • Navigating operating procedures, safety program, and staff/labour relations while reporting to the Divisional Manager, Rolling Department. Key Accomplishments: >> Reduced thousands in yearly costs. ► Saved numerous costs. >> Streamlined 3 billing roles as SPRINT cost-reduction initiative via automated billing. >> Evaluated processes using Lean Six Sigma principles. ► Decreased costs. >> Deployed 7 internal and compliant programs. ► Lowered truck turnaround time for shipping 40% using automated system while ensuring timely delivery. ► Sustained zero findings in QS Auditing. >> Championed destructive testing lab compliant with TS16949 standards.
-
-
Reliability Specialist - Steelmaking
-
Jul 2012 - Jan 2015
Progressed to direct Corporate Reliability Initiatives in the Steelmaking Division, I was in charge of optimizing operations and processes while reporting to the Area Manager, Reliability. Key Accomplishments: ** Improved overall equipment effectiveness while reducing internal costs and gauging steelmaking process delays. ► Enhanced Total Overall Equipment Effectiveness. >> Maintained accurate production delay records. >> Mitigated equipment failures… Show more Progressed to direct Corporate Reliability Initiatives in the Steelmaking Division, I was in charge of optimizing operations and processes while reporting to the Area Manager, Reliability. Key Accomplishments: ** Improved overall equipment effectiveness while reducing internal costs and gauging steelmaking process delays. ► Enhanced Total Overall Equipment Effectiveness. >> Maintained accurate production delay records. >> Mitigated equipment failures via root-cause analysis and preventative maintenance. ► Condensed internal costs while reducing steelmaking process delays by 5%. >> Leveraged high-performance equipment and steelmaking consumables.
-
-
-
GE Water & Process Technologies
-
United States
-
Environmental Services
-
200 - 300 Employee
-
Account Manager
-
Sep 2010 - Jul 2012
As Account Manager in the Heavy Industry Group, I managed the continuous operations of a large integrated steel producer’s water use/wastewater management service with the focus of expanding business. Some successful strategies that I employed in this role were analyzing production process issues and communicating profitable business solutions in order to maximize customer retention and savings. Applying 6S Methodology helped coordinate and implement effective changes in order to… Show more As Account Manager in the Heavy Industry Group, I managed the continuous operations of a large integrated steel producer’s water use/wastewater management service with the focus of expanding business. Some successful strategies that I employed in this role were analyzing production process issues and communicating profitable business solutions in order to maximize customer retention and savings. Applying 6S Methodology helped coordinate and implement effective changes in order to provide world class reliability and cost efficiency improvements against standard benchmarks. Identifying problems and delivering exceptional service retained existing client account and solidified business relationships. Producing accurate monthly sales forecasts and reports of unit costs for Business Unit Manager helped clarify and communicate accurate results. Skills: Account Management | Operations | Business Development | Production | Business Solutions | Customer Service | Continuous Improvement | 6S Methodology | Change Management | Cost Efficiency | Relationship Building| Forecasting | Reporting Show less As Account Manager in the Heavy Industry Group, I managed the continuous operations of a large integrated steel producer’s water use/wastewater management service with the focus of expanding business. Some successful strategies that I employed in this role were analyzing production process issues and communicating profitable business solutions in order to maximize customer retention and savings. Applying 6S Methodology helped coordinate and implement effective changes in order to… Show more As Account Manager in the Heavy Industry Group, I managed the continuous operations of a large integrated steel producer’s water use/wastewater management service with the focus of expanding business. Some successful strategies that I employed in this role were analyzing production process issues and communicating profitable business solutions in order to maximize customer retention and savings. Applying 6S Methodology helped coordinate and implement effective changes in order to provide world class reliability and cost efficiency improvements against standard benchmarks. Identifying problems and delivering exceptional service retained existing client account and solidified business relationships. Producing accurate monthly sales forecasts and reports of unit costs for Business Unit Manager helped clarify and communicate accurate results. Skills: Account Management | Operations | Business Development | Production | Business Solutions | Customer Service | Continuous Improvement | 6S Methodology | Change Management | Cost Efficiency | Relationship Building| Forecasting | Reporting Show less
-
-
-
-
Process Coordinator - Continuous Casting
-
Jan 2008 - Sep 2010
This challenging role involved managing and coordinating the work of four shift forepersons with up to 20 line staff (per shift). Serving as Acting Area Manager in the incumbent’s absence, I also led unionized process operating workers as backup shift foreperson. Exercising excellent leadership while implementing excellent health and safety standards ensured success in this role. As Project Leader, I facilitated the Rapid Adjustment Moulding Implementation Team (2008/09). Focusing on… Show more This challenging role involved managing and coordinating the work of four shift forepersons with up to 20 line staff (per shift). Serving as Acting Area Manager in the incumbent’s absence, I also led unionized process operating workers as backup shift foreperson. Exercising excellent leadership while implementing excellent health and safety standards ensured success in this role. As Project Leader, I facilitated the Rapid Adjustment Moulding Implementation Team (2008/09). Focusing on consistent health and safety goals, I audited shift group health and safety meetings as Management Representative and noted any need for improvements. I developed agendas and ensured that safety changes were implemented in the compliance system. My steel casting experience was leveraged through thorough training unionized staff in steel casting responsibilities and impact of stringent metallurgical control. I performed strategic analysis of downtime, production, product quality, and labour metrics for continuous improvement. Some formal approaches deployed entailed formalizing process logic control plans into a certified document to meet ISO standards. I provided numerous job specific reports for the Divisional Manager and metallurgical group's analysis report of continuous casting process for audits aligned with ISO standards. A bi-weekly budget team review of cost-effective initiatives and project timelines was conducted. I also successfully participated in daily cross-functional meetings with maintenance groups, Refractory, and Area Managers. Troubleshooting metallurgically unacceptable steel produced as part of 'off-specifications group enabled me to promote effective quality control and assurance. Skills: Management | Team Leadership | Safety Lead| Training & Development | Staff Scheduling | Personnel Management | Problem Solving| Troubleshooting| Preventative Maintenance| Reporting| Forecasting Show less This challenging role involved managing and coordinating the work of four shift forepersons with up to 20 line staff (per shift). Serving as Acting Area Manager in the incumbent’s absence, I also led unionized process operating workers as backup shift foreperson. Exercising excellent leadership while implementing excellent health and safety standards ensured success in this role. As Project Leader, I facilitated the Rapid Adjustment Moulding Implementation Team (2008/09). Focusing on… Show more This challenging role involved managing and coordinating the work of four shift forepersons with up to 20 line staff (per shift). Serving as Acting Area Manager in the incumbent’s absence, I also led unionized process operating workers as backup shift foreperson. Exercising excellent leadership while implementing excellent health and safety standards ensured success in this role. As Project Leader, I facilitated the Rapid Adjustment Moulding Implementation Team (2008/09). Focusing on consistent health and safety goals, I audited shift group health and safety meetings as Management Representative and noted any need for improvements. I developed agendas and ensured that safety changes were implemented in the compliance system. My steel casting experience was leveraged through thorough training unionized staff in steel casting responsibilities and impact of stringent metallurgical control. I performed strategic analysis of downtime, production, product quality, and labour metrics for continuous improvement. Some formal approaches deployed entailed formalizing process logic control plans into a certified document to meet ISO standards. I provided numerous job specific reports for the Divisional Manager and metallurgical group's analysis report of continuous casting process for audits aligned with ISO standards. A bi-weekly budget team review of cost-effective initiatives and project timelines was conducted. I also successfully participated in daily cross-functional meetings with maintenance groups, Refractory, and Area Managers. Troubleshooting metallurgically unacceptable steel produced as part of 'off-specifications group enabled me to promote effective quality control and assurance. Skills: Management | Team Leadership | Safety Lead| Training & Development | Staff Scheduling | Personnel Management | Problem Solving| Troubleshooting| Preventative Maintenance| Reporting| Forecasting Show less
-
-
Education
-
Niagara College
Ontario College Diploma -
McMaster University
Metallurgy, Iron & Steel Certificate:
Community
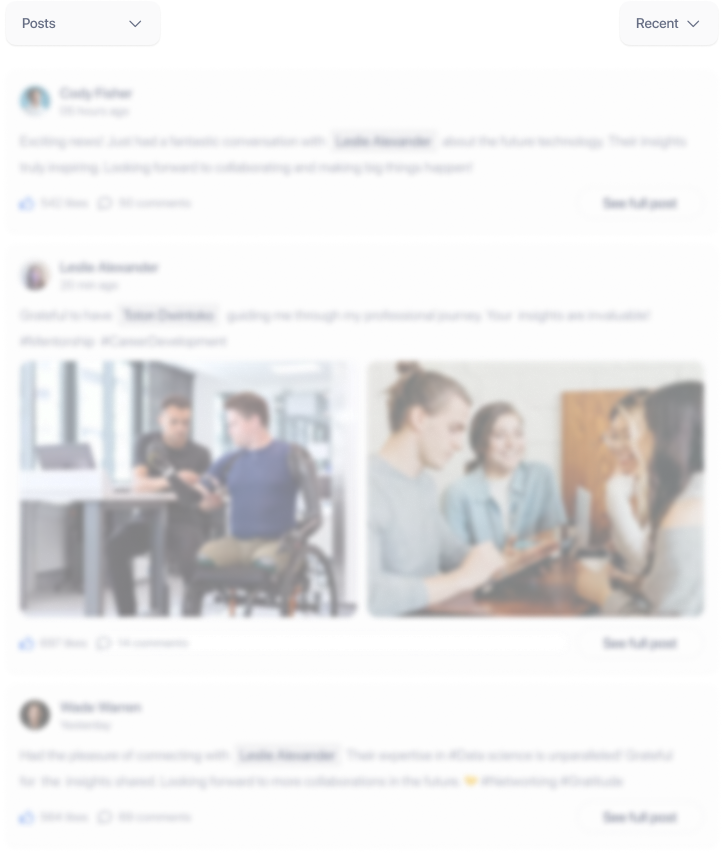