
David Haefner
Vice President at Michigan Laser Manufacturing- Claim this Profile
Click to upgrade to our gold package
for the full feature experience.
Topline Score
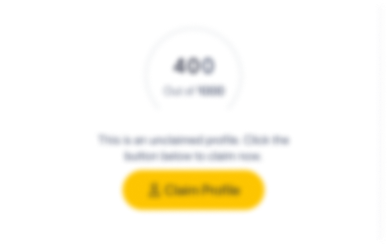
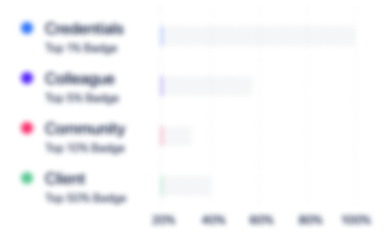
Bio


Experience
-
Michigan Laser Manufacturing
-
United States
-
Machinery Manufacturing
-
1 - 100 Employee
-
Vice President
-
Mar 2019 - Present
-
-
-
-
Vice President
-
Mar 2019 - Mar 2019
-
-
-
-
Business Development
-
May 2017 - Feb 2019
-
-
-
MetoKote Corporation
-
United States
-
Motor Vehicle Manufacturing
-
100 - 200 Employee
-
Plant Manager
-
Jan 2009 - Dec 2011
Frequently Iinteract with customer frequently on collaborative continuous improvement effortsIntegrate plant operational measures to meet customer expectationsImplement current state and future state projects for plant floor improvementsCommunicate daily with staff on performance goals versus actualInteract hands on with floor staff to understand job challengesImplement scheduling systems in conjunction with Ryder logisticsAnalyze financial measurements versus budgetary goals
-
-
Plant Manager
-
Oct 2007 - Jan 2009
Communicated vision of future state to support plant objectivesIncreased yearly sales by 40%Tracked and analyzed plant costs - operated at a 35% deleverage pointDefined annual budget for plant operations - all costs inclusiveImproved line efficiency which reduced direct labor content by 30% over six month periodInterfaced with customers frequently and implemented problem solving methodologies.
-
-
Plant Manager
-
Feb 2005 - Oct 2007
Managed environmental system for 24 months, violation freeManaged lowest operating costs within business modelMaintained one of the highest customer approval ratingsDeveloped system for personnel training and development Implemented TS 16949 and acted as management representative
-
-
-
-
Lean Enterprise Manager
-
Mar 2003 - Feb 2005
Increased efficiency by 20% and decreased product lead time by 15 daysDeveloped supermarket inventory systems which allowed for streamlined schedulingReduced in process inventory $200,000 by combining assembly stepsReduced staff by 10% by implementing work cellsCreated 20,000 square feet of extra floor space Increased efficiency by 20% and decreased product lead time by 15 daysDeveloped supermarket inventory systems which allowed for streamlined schedulingReduced in process inventory $200,000 by combining assembly stepsReduced staff by 10% by implementing work cellsCreated 20,000 square feet of extra floor space
-
-
-
Dedoes Industries
-
United States
-
Manufacturing
-
1 - 100 Employee
-
Quality Manager
-
Apr 2000 - Mar 2003
Organized and reported on company wide internal audit of quality system twice a year, and initiated corrective actions to address potential non-conformancesDirected two major new product launches simultaneously with incoming AQL and internal processesGenerated reports with performance indicators for monthly executive management reviews of the quality systemVisited China to verify testing practices, documentation of results, and testing fixtures were appropriate for launch of new products.
-
-
Education
-
Walsh College
MBA, Busines -
Adrian College
BS, Biology
Community
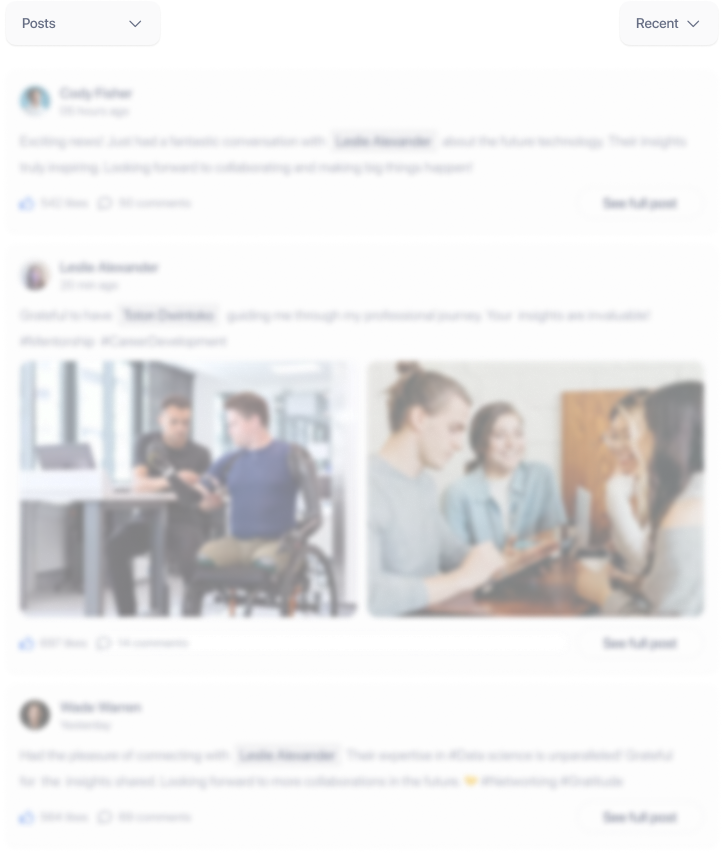