David H Nelson
3D Design Engineer at SG Equipment Ltd.- Claim this Profile
Click to upgrade to our gold package
for the full feature experience.
Topline Score
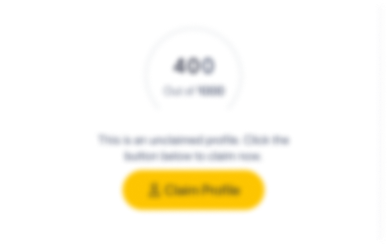
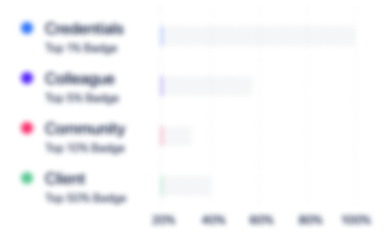
Bio


Credentials
-
IENG MIIE - MECH
-
Experience
-
SG Equipment Ltd
-
New Zealand
-
Machinery Manufacturing
-
1 - 100 Employee
-
3D Design Engineer
-
Jun 2013 - Present
I currently work in the Typhoon/Eurofighter office. I started working on the Deployable Liquid Conditioning System, which is used predominantly on the pilot’s suit & seat for the F35 Fighter. I am in constant liaison with engineers & project management at BAe over the technical development of this equipment. Completing their DRL’s & starting the CE Technical File which is required as per 2006/42/EC Machinery Directive, along with endorsing the applicable technical directives & harmonized standards associated with this equipment. I have also had a hand in designing fuel test equipment on the JSF (Joint Strike Force) fighter jet & am currently leading 3 engineers on the installation of fixing/adhering strain gauges to strategic parts of the F35 fighter. We are using the latest version of Inventor 2016 along with the vault system. Show less
-
-
-
AB GRAPHICS INTERNATIONAL Ltd.
-
Middleton on the Wolds
-
SENIOR DESIGN ENGINEER
-
2012 - 2013
I was brought in to help design two types of ‘Rewind/Unwind Twin Turret’ machines. The Middleton site manufacture & design high speed turrets, while the Carnaby site predominantly design & manufacture high speed rewind/unwind machines. My brief was to visit clients in France, to whom would be the customer & take into account all the best features of other manufacturers machines along with our own & incorporate them into our new design using 3D SolidEdge. I was brought in to help design two types of ‘Rewind/Unwind Twin Turret’ machines. The Middleton site manufacture & design high speed turrets, while the Carnaby site predominantly design & manufacture high speed rewind/unwind machines. My brief was to visit clients in France, to whom would be the customer & take into account all the best features of other manufacturers machines along with our own & incorporate them into our new design using 3D SolidEdge.
-
-
-
LAMBERT AUTOMATION SYSTEMS.
-
Tadcaster
-
PROJECT/3D DESIGN ENGINEER
-
2010 - 2012
I worked as a contractor for 2 years using Solidworks designing & project managing the installation of change parts to the KIT-KAT line at Hershey, USA. I have also been designing module concepts for the medical industry & helped develop a method of measuring defects in sealing technology using ultrasonics. I worked as a contractor for 2 years using Solidworks designing & project managing the installation of change parts to the KIT-KAT line at Hershey, USA. I have also been designing module concepts for the medical industry & helped develop a method of measuring defects in sealing technology using ultrasonics.
-
-
-
BCH Ltd
-
Whiworth - Rochdale
-
3D Design/Project Contract Engineer.
-
Feb 2007 - May 2010
One of my key objectives was to introduce 3D design to the business, as BCH want to improve their ability to compete at an international level. In my first 3 months I designed a micro-liquorice cooking line 125kg which was displayed at the 2008 Interpack show in Dusseldorf. I then installed and commissioned a liquorice line for a business in Denmark in May 2008. All using 3D Inventor.I then enhanced a pilot line to a full manufacturing process for potato extruding – the end result was to produce a 1.1g potato chip. This project is ongoing. I then designed a continuous extruder for use in potatoes, carrots etc using the vermicelli principle. Show less
-
-
-
KINGSPAN-ATLAS Ltd.
-
Sherburn
-
PRODUCT DEVELOPMENT ENGINEER
-
2006 - 2007
I was responsible for maintaining the project from beginning to end, producing project plans, costings, capex, technical application documents, brochures, 3D design drawings along with animated presentations. I worked closely with the MD, managers & shop floor engineers on all the projects & made sure the projects were passed by the BRE, the governing body that carry out fire, water & structural tests etc, on our behalf. I was responsible for maintaining the project from beginning to end, producing project plans, costings, capex, technical application documents, brochures, 3D design drawings along with animated presentations. I worked closely with the MD, managers & shop floor engineers on all the projects & made sure the projects were passed by the BRE, the governing body that carry out fire, water & structural tests etc, on our behalf.
-
-
-
DaCAT Ltd
-
Rillington - Malton
-
DESIGN ENGINEER-FREELANCE.
-
2005 - 2006
During this time, I worked six months for Sollich UK as an Installation Engineer. I also designed high pressure injection moulding dies & factory layout schemes for Malton Plastics. I designed a chocolate/sugar coater for DTG Eng Ltd in Liverpool which is to be patented after trials & also, a miniature continuous 100Kg/Hr toffee cooker for the USA. During this time, I worked six months for Sollich UK as an Installation Engineer. I also designed high pressure injection moulding dies & factory layout schemes for Malton Plastics. I designed a chocolate/sugar coater for DTG Eng Ltd in Liverpool which is to be patented after trials & also, a miniature continuous 100Kg/Hr toffee cooker for the USA.
-
-
-
-
PROJECT DEVELOPMENT MANAGER
-
2001 - 2005
PROJECT DEVELOPMENT MANAGER for the Cadbury Trebor Bassett group, based in York. I was responsible for all projects on site, from the implementation of RAM, ie; the engineering agenda, specification, authorised amount, time, expected benefit, installation & documentation. During this time I have installed, case packing £650k, air conditioning rooms £600k, a new method of printing outer cases £165k, complete manufacturing lines £575k, CFA units with CIP £65k etc. PROJECT DEVELOPMENT MANAGER for the Cadbury Trebor Bassett group, based in York. I was responsible for all projects on site, from the implementation of RAM, ie; the engineering agenda, specification, authorised amount, time, expected benefit, installation & documentation. During this time I have installed, case packing £650k, air conditioning rooms £600k, a new method of printing outer cases £165k, complete manufacturing lines £575k, CFA units with CIP £65k etc.
-
-
-
-
SENIOR DESIGN/PROJECT ENGINEER
-
1994 - 2001
SENIOR DESIGN/PROJECT ENGINEER for the Nestlé group, based at the York R&D Centre. I was responsible for designing purpose built machinery for use in Nestlé factories throughout the world. My duties include full project management from procurement to commissioning of the equipment I had designed. Jobs completed: - Wiped film evaporator 200Kg/Hr continuous, producing high boil sugars, gums for starchless moulding to 98Tc for Asia & America. PATENTED. - Non-Tailing pneumatic nozzle valve, for viscous products. - Miniature Polo mint punches, Japan. - 2T/Hr caramel/toffee cooker, Dijon factory, France. - Violet crumble mixer for Australia. - Ultrasonic cutting system, for Elst factory, Holland. - Batter laying arm for KitKat trials. - Vacuum cooking system 2T/Hr, Sfinx factory, Czechia. - Pressurised lid for Rolo depositor, Fawdon. - CFA layout for Chembong project, Malaysia. - 50-250Kg/Hr Peppermint cracknel cooking plant for S.Africa. - 2T/Hr caramel/toffee cooker, Elst factory, Holland. - 6x2T/Hr caramel/fudge cooker, Franklin Park, USA. - 3xGeared caramel depositor, Franklin Park, USA. - 320 Piston, Non-Tailing caramel depositor, Fawdon. PATENTED. For all of the above machines, complete technical backup was required, including operating manuals, parts manuals, safety procedures, risk assessment etc. So during my time at Nestlé, I covered a full spectrum of Design/Project Engineering. Show less
-
-
-
-
DESIGN ENGINEER
-
1980 - 1994
1992-94 DESIGN ENGINEER, worked on the Development & Design of the Strasbourg Euro-tram Project, responsible for the 3D Modelling of the Saloon, Articulation & Drivers cabin modules chassis & bodywork using the Intergraph EMS 2.1 system. 1990-92 PRODUCTION ENGINEER, responsible for analysing current production processes, install, control & maintain manufacturing sign off through its formal procedure. Process & prepare process build sheets & weld sequence methods. Liaise with managers & supervisors regarding technical & dimensional data. Projects worked on - 165, 166 & 465. 1988-90 B.O.M PLANNER, worked on Class 465 EMU, preparing common parts structure list for MRP system. Contribute to the make or buy decisions & of the development of the kitting system for assigned products & builds. 1987-88 DRAUGHTSMAN, assigned to shop layouts of aluminium produced bodyshells and Jig & Tool Design work, based around bolster production. 1986-87 PRODUCT SUPPORT ENGINEER, working for the Product Support Group carrying out rectification, servicing & customer confidence, on 150 Class vehicles at Derby & 165 Networkers at Selhurst Park & Strawberry Hill depots in London. 1984-86 CAT 4 FITTER. Trained on site & works training school to stand in for people on Progressing & Inspection. Checking, controlling, liaising & signing off components in the Machine shop, Frame shop, Fabrication shop & Press shop. 1980-84 APPRENTICE at the York works training school for 1 year & was accepted as a Fitter & trained a further 3 years on the works site in Maintenance, Tool room, the Lift, Frame, Fabrication, Press, Machine, Traction, Building, Plumbers & Electric shop etc. Show less
-
-
Education
-
Huntington School - York
'O' Level – Technical Drawing, Engineering & Design, Geography.
Community
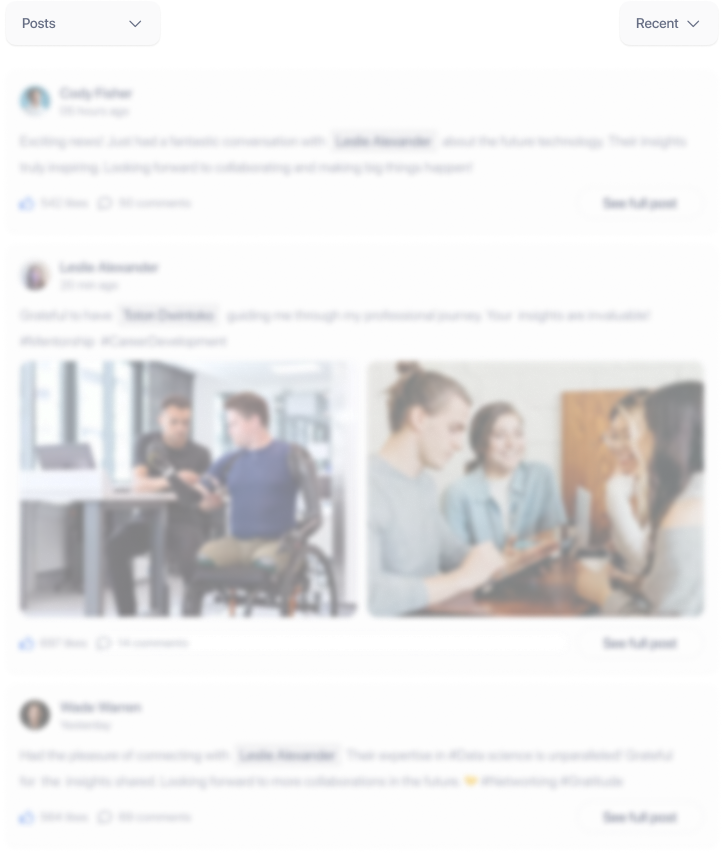