David Eng
Operations Manager at Croll Reynolds- Claim this Profile
Click to upgrade to our gold package
for the full feature experience.
Topline Score
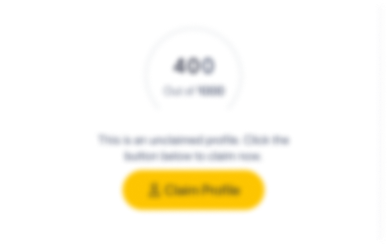
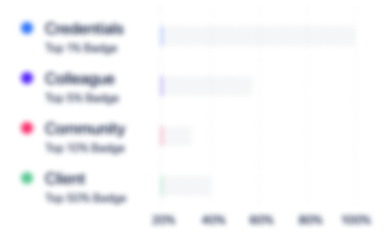
Bio


Experience
-
Croll Reynolds Co., Inc.
-
United States
-
Industrial Machinery Manufacturing
-
1 - 100 Employee
-
Operations Manager
-
Mar 2014 - Present
Project management of all open orders for custom fabricated vacuum systems supporting a global market. Manage procurement of special materials needed for custom built equipment specifically designed to meet customers manufacturing requirements. Internal communications with Engineering, Quality, Purchasing, Accounting & Shipping departments to maintain production schedules. Review progress through the supply chain to ensure the timely approvals and orders placed to meet delivery goals. Communicate with customers on critical milestone dates that would impact the contractual delivery date. Improve internal communications by creating a team vs. individual effort.
-
-
-
-
Director of Operations
-
2009 - 2013
Managed manufacturing and packaging operations to support sales.Created forecasts, production schedules and inventory levels to maximize inventory turns. Negotiate and procure all raw materials for manufacturing and packaging departments. Managed manufacturing and packaging operations to support sales.Created forecasts, production schedules and inventory levels to maximize inventory turns. Negotiate and procure all raw materials for manufacturing and packaging departments.
-
-
-
Maxell Corporation of America
-
Computers and Electronics Manufacturing
-
1 - 100 Employee
-
Director of Operations
-
2007 - 2009
Managed Logistics, Strategic Planning and Sales Support staff totaling 17 employees. Created strategies to achieve biannual budget goals. Improved communications between corporate headquarters and our manufacturing facility in Mexico to shorten lead time and increase production flexibility. Coordinated with marketing Department to design a New Product Introduction template to streamline time to market process. Managed Logistics, Strategic Planning and Sales Support staff totaling 17 employees. Created strategies to achieve biannual budget goals. Improved communications between corporate headquarters and our manufacturing facility in Mexico to shorten lead time and increase production flexibility. Coordinated with marketing Department to design a New Product Introduction template to streamline time to market process.
-
-
-
PNY Technologies
-
United States
-
Computers and Electronics Manufacturing
-
200 - 300 Employee
-
Director of Procurement
-
1995 - 2007
Developed long and short term support strategies in a fast paced technology market. Developed an efficient supply chain to maximize customer satisfaction and minimize inventory devaluations. Conducted quarterly supplier performance reviews with strategic suppliers. Managed 5 buyers in NJ, CA Purchasing Manager and 3 buyers in Santa Clara site. Directed and supervised activities of international purchasing office in Japan.Created supply chain, provided forecasts and implemented sourcing strategies to launch new product lines. Supply chain for Video Cards included drop shipments from the US and Asia to CM’s to meet scheduled timelines. Initiated process improvements from vendors to reduce costs by 5% bi-annually.
-
-
-
-
Production Control Manager
-
1988 - 1995
Coordinated and scheduled production through facilities in Fairfield, NJ and Anaheim, CA. Created a production schedule for over 200 people in the manufacturing process to ensure prompt deadline dates.Coordinated priorities and timing with managers in graphics, cylinder, print, conversion, shipping, customer service and sales departments. Directly supervised the production coordinator, purchasing agent and administrative assistant. Supplied all components needed to follow the production schedule in Anaheim. This involved the timing of shipping components from various parts of the country. Accustomed to a crisis management environment.
-
-
Education
-
Fairleigh Dickinson University
Community
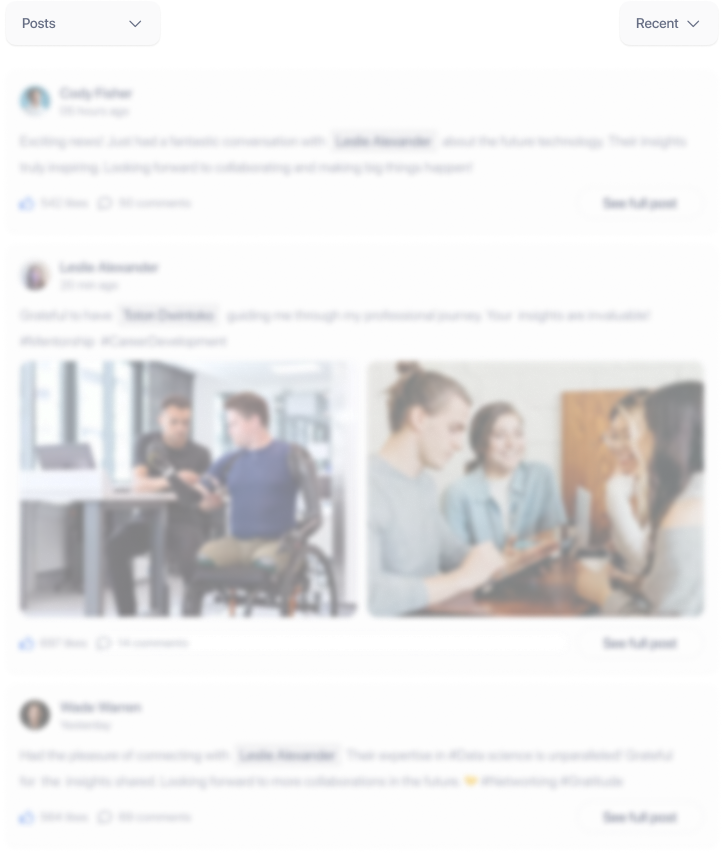