David Boyd
Director Planning & Procurement at Tailored Pet Nutrition- Claim this Profile
Click to upgrade to our gold package
for the full feature experience.
Topline Score
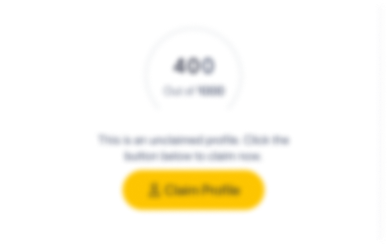
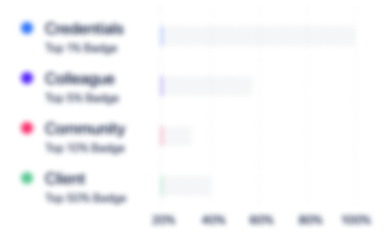
Bio
0
/5.0 / Based on 0 ratingsFilter reviews by:
Experience
-
Tailored Pet Nutrition
-
United States
-
Manufacturing
-
1 - 100 Employee
-
Director Planning & Procurement
-
Nov 2019 - Present
I am currently a member of a team building out the Supply Chain for a DTC business. My primary responsibilities include Operational Planning, Procurement, NetSuite Item Master & WMS, Fulfillment Budgeting, Standard Costing & Cost Modeling and Supply Chain Continuous Improvement. I am currently a member of a team building out the Supply Chain for a DTC business. My primary responsibilities include Operational Planning, Procurement, NetSuite Item Master & WMS, Fulfillment Budgeting, Standard Costing & Cost Modeling and Supply Chain Continuous Improvement.
-
-
-
The J.M. Smucker Company
-
United States
-
Food and Beverage Manufacturing
-
1 - 100 Employee
-
Manager Corporate Warehouse Processes
-
Sep 2018 - Oct 2019
Oversaw the warehouse systems and business processes for over 34 sites - internal and 3PL - in North America. Lead the warehousing team composed of three associate managers and two analyst whose main responsibilities are to support the distribution network and improve site operations and metrics through continuous improvement projects and enhancements. Corporate liaison process and systems support for the North America distribution network. Provided warehouses support on day to day process/systems issues, WMS/ERP training and projects. Show less
-
-
-
Ainsworth Pet Nutrition
-
United States
-
Food and Beverage Manufacturing
-
1 - 100 Employee
-
Sr. Manager Warehouse Capabilities
-
Sep 2017 - Sep 2018
Warehouse Capabilities Team:1) HighJump WMS implementations at 8 sites (including warehouses, distribution centers and manufacturing facilities) in 18 months. 2) Lead the Warehouse Capabilities Team in continuous WMS improvement initiatives including but not limited to: WMS optimization through internal systems engineering and development, continuous improvement documentation and training and structed inventory control analysis and leadership.
-
-
Manager of Supply Chain Integration and Analysis
-
Feb 2012 - Sep 2017
Project Manager for TransPlace 3PL/TMS Implementation:1) Increase network scalability to prepare for 5 year growth execution and $500K annual savings2) Dispatch and carrier scheduling and relations business unit outsourced to 3PL for internal repurposing to Customer Service3) Coordinated all efforts between functional business units and technical groups to ensure deadlines and cost objectives where met which resulted in a smooth operational go-liveProject Manager for CHEP to PECO pallet migration:1) Cost analysis for 600K pallet throughput annually2) Coordinated migration with all plants (APN & Co-Man)3) Contract negotiations to drive cost down4) Provided Executive level updates & sought approval5) Projected savings in excess of $300K annuallyFinancial, Network & Capacity Analyses:1) Implemented and modeled the 1st zero based Delivery budget model, $17MM annually, for monthly Rate, Load Mix reconciliation and analysis.2) Created Network DC capacity models for “large customer wins” to ensure network readiness3) Lead weekly operational calls for 3PL Distribution Center & WMS integration for Wagner Logistics4) West Coast Solution Due Diligence Team & Total Delivered Cost Model creation & analysis Show less
-
-
Continuous Improvement Analyst
-
Aug 2010 - Feb 2012
Project Manager for Continuous Improvement Program (LEAN) implementation1) Program design & provided quarterly Executive level updates2) Companywide training & communication on LEAN principles3) OEE Benchmarking & analysis & plant floor integration for OEE Automation4) Team efforts resulted in a reduction of scrap from 6% to a sustained 3% and $4MM savings annually
-
-
-
-
Operations Manager
-
Dec 2009 - Aug 2010
US Operations Team Restructuring & Data Management function transfer to US Office:1) Appointed Manager for US Operations in 2008 for 8 team members2) Projected Savings of $300K annually through labor repurposing3) Annual Enrollment Team Resource Planning to ensure smooth delivery of service4) Creation of Operations Team Budget Matrix & Escalation Model5) Provide annual review and mid-year feedback to team membersCustomerWise (CRM) implementation:1) Workflow established for client issue/Ad-hoc request resolution2) Standardization of tasks across client platform and elimination of workflow bottlenecks3) Improved accuracy through clearer requirements for Ad-hoc reports (US vs. CA Benefits)Monthly Vendor Premium Payment Process Design:1) Architected product for revenue generation and client relations2) Addressed gaps in process for CI opportunities Show less
-
-
Benefits Analyst
-
Apr 2007 - Dec 2009
Client Implementations & on-going Services:1) Technical liaison for 8 implementations within 4 years2) Performed scheduled & Ad-hoc on-going deliverables throughout implementations cycles3) Created LOA Tracking Database
-
-
-
GNC
-
United States
-
Retail
-
700 & Above Employee
-
Compensation, Benefits & HRIS Analyst
-
May 2000 - Apr 2007
Lawson HRIS & Payroll Implementation Team: 1) Mass pay change upload Process for Federally mandated Min Wage Increases (1,500 employees) 2) Time Accrual Policy to systems admin process design and on-going administration Start Rates Database - process improvement that migrated from an Excel macro to automated database used by 3 HR coordinators: 1) Automated & administered weekly system update based on sales and new hires 2) Automated notification letters for start rate adjustments. 3) Storage of history to eliminate paper reports for coordinators Performed multiple process improvements via automation and/or creation systems: 1) Monthly Performance Evaluation Process (PEP) notification to all HQ employees 2) Annual Open Enrollment Process and employee packets 3) Turnover reporting 4) I-9 Process Creation Built tracking tools and reports and distributed to field management on a monthly basis. Show less
-
-
Education
-
Point Park University
Bachelor of Arts (B.A.), Human Resources Development -
Pittsburgh Technical Institute
Associate of Science (A.S.), Mechanical Drafting and Mechanical Drafting CAD/CADD
Community
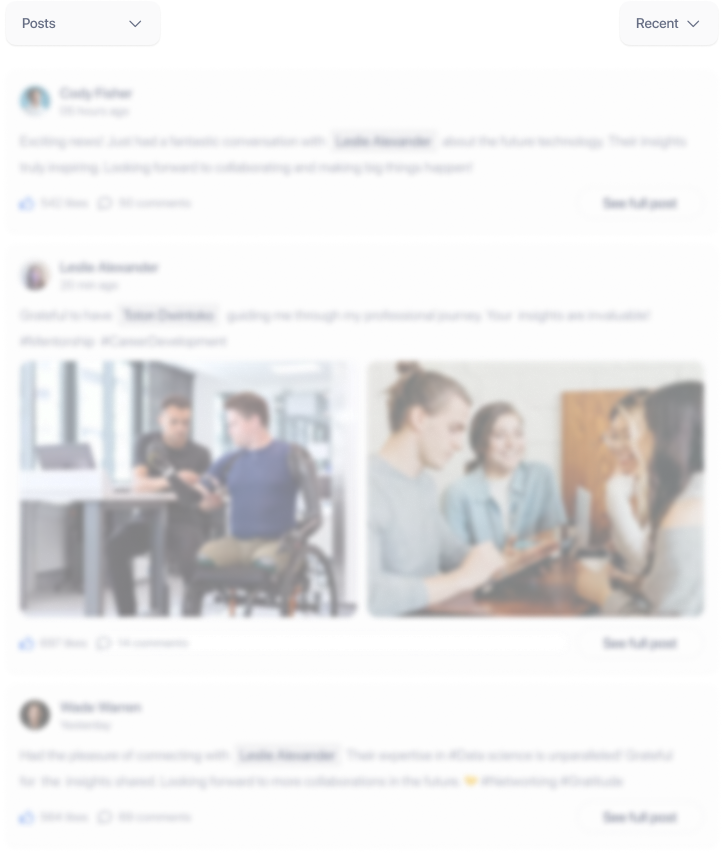