David Baron
Director Of Operations at SteelTank Brewing Co.- Claim this Profile
Click to upgrade to our gold package
for the full feature experience.
Topline Score
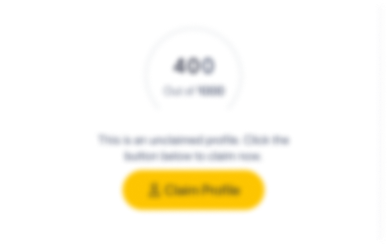
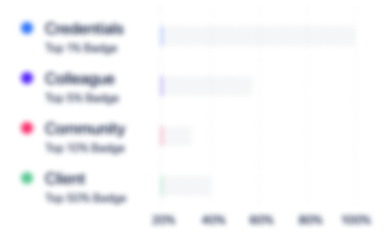
Bio


Experience
-
SteelTank Brewing Co.
-
United States
-
Food and Beverage Services
-
1 - 100 Employee
-
Director Of Operations
-
Sep 2020 - Present
-
-
-
HUSCO International
-
United Kingdom
-
1 - 100 Employee
-
Manufacturing Engineer
-
May 2015 - Present
Support New Product Development. Create and develop manufacturing system concepts. Work with design engineers and production from the start of the quote to the runoff of new production equipment, Including assembly stations, work cells, test stations, material handling equipment, and packaging for new products/new processes. Supports the new product development process through PFMEA, DFM, and CAPP activities to ensure safety, quality, delivery, and cost targets are met. • Maximize Operations Production and Efficiency. Implement/modify manufacturing processes. Work with production employees to continually improve production operations, system maintenance and design concepts through coaching, equipment design/modification/selection, training, and participation in PPI activities. • Upgrade Material and Equipment. Work with advanced engineering and equipment suppliers to determine designs and configurations for new equipment and upgrades. Preparation of financial analysis for capital expenditures for tooling and equipment. Monitor and control all phases of new equipment. • Demonstrate Project Management. Demonstrate my technical expertise in project management including, tracking, team assignments, status reports, facilitate effective problem solving, Technical resource for specific manufacturing methods • Collaborate with Other Departments. Interface between Design and Production to ensure designs are acceptable for manufacturing, Work with peers and other support personnel with specifics to training on production equipment, problem solving, and preventive maintenance. • Advocate for Continuous Improvement. Actively supports continuous improvement activities through equipment and process design, coaching, training, and participation in plant level continuous improvement activities (PPI, 5S, etc.). • Strong Team Player and Contributor. Able to work well with colleagues and produce results within a fast-paced and high pressure atmosphere. Show less
-
-
-
Poclain Hydraulics
-
France
-
Industrial Machinery Manufacturing
-
700 & Above Employee
-
Manufacturing Engineer
-
Mar 2014 - May 2015
Develop, evaluate and improve manufacturing methods via process and capital budget improvements and equipment modifications. Analyze and plan workforce standards, space requirements and work flow. Design and layout of equipment, workspace and office space for maximum efficiency. Responsible for tool and gage design. Confer with Product Development Team concerning tooling to ensure efficient production methods; Serve and support to purchased products according to specifications and quality standards; Responsible for documentation control. Estimate production times, staffing requirements and related costs to provide information to management decisions. Confer with management, engineering and other staff regarding manufacturing capabilities, production schedules and other considerations to improve and understand the production processes. Evaluate and apply standard methods to estimate future manufacturing requirements and potential. Responsible for developing and meeting operations budgets within engineering. Develop, submit and stay within capital expenditures for departments. Act as change unit to promote team work, respect, creativity, employment and confidence. Show less
-
-
-
-
Production Supervisor
-
Jul 2012 - Feb 2014
Oversee and supervise 43 people. Scheduled all work centers Implemented Machining Cells to reduce manufacturing lead time in key areas Worked with The Lean Frog business resource to set up a Lean Program to streamline flow. I played a major role in the re-layout of the machinery of our 250,000 sq. ft. facility which has improved flow and increased production by 10% in a 6 month time period. Improved shop productivity by 15%, in formal program to reduce setup time, and improve operational efficiencies. Implemented formal tool-crib 5S program, which included consolidation of suppliers and implementation of electronic ordering system. Reduced tool-crib maintenance time by 30% and reduced the square footage by 45%. Applied formal 5S program to staging areas. Responsible for all interviews and screenings for potential shop floor candidates. Involved in performance reviews, disciplinary actions, and the dismissal of employees. Worked with insurance groups on improving shop safety programs. Show less
-
-
-
Product Service & MFG
-
United States
-
Machinery Manufacturing
-
1 - 100 Employee
-
Sales / Estimating
-
Oct 2009 - Jul 2012
Estimator/Sales and CNC Programmer Working directly with customers to help bring in manufacturing work. I was responsible for the setup of all Manufacturing Routings including labor standards. I provided the material and labor quotations to all customers. I helped in the implementation of training programs for both CNC and manual machines. When there was downtime I would program all new jobs for all CNC machine and turning centers. I worked with Local Technical business resource to help streamline business, customer, and employee relations. Show less
-
-
-
Hader-Seitz Inc
-
Machinery Manufacturing
-
1 - 100 Employee
-
Manufacturing Engineer
-
Mar 2003 - Oct 2009
Implemented Machining Cells to reduce manufacturing lead time in key areas. Worked with Local Technical business resource to set up a Lean Program on a family of product. Improved shop productivity by 10%, in formal program to reduce setup time, and improve operational efficiencies. Implemented a CNC CAM programming system that has resulted in $55,000+ in annual savings. Implemented formal tool-crib 6S program, which included consolidation of suppliers and implementation of electronic ordering system. Program reduced expenditures by 50%, reduced tool-crib maintenance time by 65% and reduced the square footage by 65%. Implemented formal 6S re-organization program in Quality Department, which has reduced Quality support maintenance time by 20%. Applied formal 5S program to staging areas, which resulted in a reduction of material handling time by 25%. Responsible for setup of all Manufacturing Routings including labor standards. Responsible for all interviews and screenings for potential shop floor candidates. Involved in performance reviews, disciplinary actions, and the dismissal of employees. Worked with insurance groups on improving shop safety programs. Coordinated & implemented formal forklift training program. Provide labor quotations to sales department. Show less
-
-
Education
-
New Berlin West High School
High School Diploma
Community
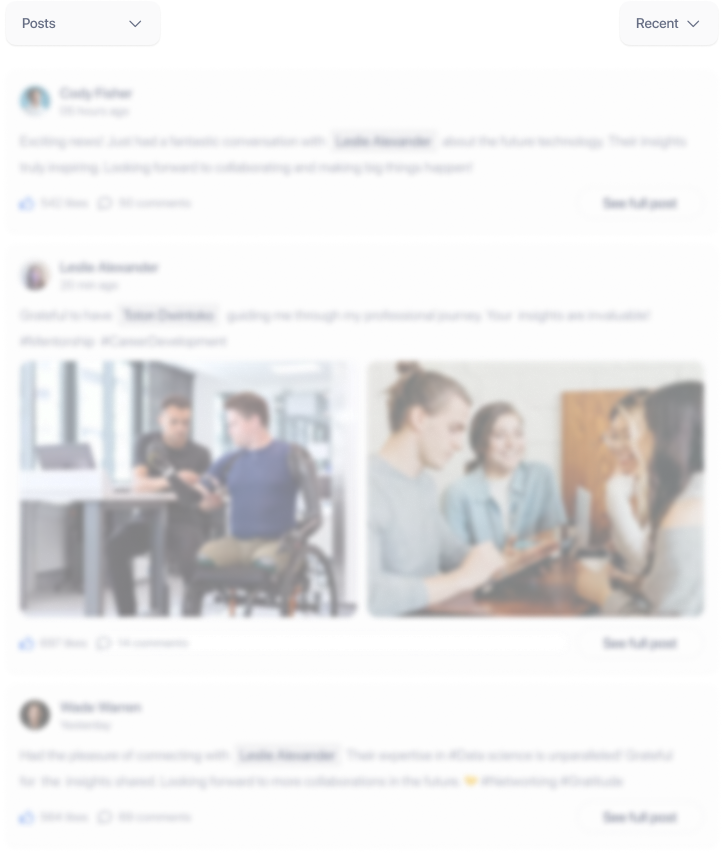