David Baker
Operations Analyst at IRRAS AB- Claim this Profile
Click to upgrade to our gold package
for the full feature experience.
Topline Score
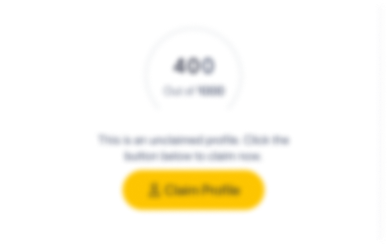
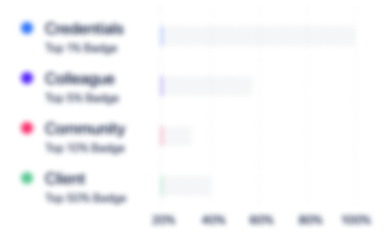
Bio


Experience
-
IRRAS AB
-
Sweden
-
Medical Equipment Manufacturing
-
1 - 100 Employee
-
Operations Analyst
-
Aug 2022 - Present
• Requirements gathering, design, publishing, and maintaining Power BI reports for sales, supply chain, operations, and quality departments. • Working cross functionally to enhance reporting ability across different departments in the organization. • Responsible for data integrity and serves and primary subject matter expert on Jeeves ERP system. • Leading discussion sessions for cost effective new product cut over planning. • Cross referencing and auditing HubSpot CRM (Customer… Show more • Requirements gathering, design, publishing, and maintaining Power BI reports for sales, supply chain, operations, and quality departments. • Working cross functionally to enhance reporting ability across different departments in the organization. • Responsible for data integrity and serves and primary subject matter expert on Jeeves ERP system. • Leading discussion sessions for cost effective new product cut over planning. • Cross referencing and auditing HubSpot CRM (Customer relationship management) program for accuracy between the Jeeves ERP. • Responsible for all material and production planning leading. • Creating, analyzing, and modeling complex data sets to actionable formats for stakeholders. • Responsible for international distributor management inclusive of inventory audits, customer shipments, and overall business health.
-
-
Master Scheduler
-
Jun 2020 - Aug 2022
• Creating forecasted master planning schedule based on commercial demand plan, including corresponding material resource plan (MRP) and highlighting and driving resolution of any inventory risks before supply issues occur. • Responsible for hypothesis and what-if demand and supply planning with different inventory and sales forecast scenarios. • Constructing weekly build forecasts and coordinating with manufacturing and engineering team for rough cut capacity planning and load… Show more • Creating forecasted master planning schedule based on commercial demand plan, including corresponding material resource plan (MRP) and highlighting and driving resolution of any inventory risks before supply issues occur. • Responsible for hypothesis and what-if demand and supply planning with different inventory and sales forecast scenarios. • Constructing weekly build forecasts and coordinating with manufacturing and engineering team for rough cut capacity planning and load leveling. • Building and executing user acceptance test plans for ERP (JEEVES) validation and implementation. • Executing ERP transactions comprising of material movements, material scrap and manual adjustments, item master data, customer and supplier creation, applied tax codes and posting templates, sales orders, material receipts, and work order creation and completion. • Working knowledge of international shipment criteria and lead times. Inclusive of commercial invoices, tariff or schedule B codes, VAT Identification Number, and customs clearance. • Facilitating and verifying material shipments with 3PL (Third Party Logistics) partners to customers in both the United States and internationally. • Processing and sending of invoices to customers after confirmation of sales order completion. • Preparing and optimizing reports to translate data into relevant decision-making information. • Promoting a positive company culture to increase employee happiness, retention, and overall well-being.
-
-
-
Mitchell International
-
United States
-
Software Development
-
700 & Above Employee
-
Project Manager 2
-
Mar 2020 - Jun 2020
• Working with cross-functional team to plan, schedule, execute, and close customer and internal projects. • Drafting and maintaining custom reports to identify issues, project lateness, and action items in SalesForce CRM software. • Ensuring project team understands all aspects of assigned projects and their responsibilities. • Creating and adhering to project schedule mutually agreed upon by internal and customer teams for all projects and initiatives. • Leading Lean Six Sigma… Show more • Working with cross-functional team to plan, schedule, execute, and close customer and internal projects. • Drafting and maintaining custom reports to identify issues, project lateness, and action items in SalesForce CRM software. • Ensuring project team understands all aspects of assigned projects and their responsibilities. • Creating and adhering to project schedule mutually agreed upon by internal and customer teams for all projects and initiatives. • Leading Lean Six Sigma continuous improvement projects to reduce project lateness and establish procedures and best practices for project managers. • Authoring and maintaining departmental SOPs to document current procedures and establish standard work activities. • Facilitating project meetings with potential new vendors to validate appropriate integrations and necessary business practices.
-
-
Project Manager 1
-
Sep 2018 - Mar 2020
• Working with cross-functional team to plan, schedule, execute, and close customer and internal projects. • Drafting and maintaining custom reports to identify issues, project lateness, and action items in SalesForce CRM software. • Ensuring project team understands all aspects of assigned projects and their responsibilities. • Creating and adhering to project schedule mutually agreed upon by internal and customer teams for all projects and initiatives. • Leading Lean Six Sigma… Show more • Working with cross-functional team to plan, schedule, execute, and close customer and internal projects. • Drafting and maintaining custom reports to identify issues, project lateness, and action items in SalesForce CRM software. • Ensuring project team understands all aspects of assigned projects and their responsibilities. • Creating and adhering to project schedule mutually agreed upon by internal and customer teams for all projects and initiatives. • Leading Lean Six Sigma continuous improvement projects to reduce project lateness and establish procedures and best practices for project managers. • Authoring and maintaining departmental SOPs to document current procedures and establish standard work activities. • Facilitating project meetings with potential new vendors to validate appropriate integrations and necessary business practices.
-
-
-
INOVIO Pharmaceuticals, Inc.
-
United States
-
Biotechnology Research
-
100 - 200 Employee
-
Buyer/Planner
-
Nov 2016 - Sep 2018
• Established and managed production and engineering build schedules and ordered any necessary part or materials need to fulfill necessary needs. • Resolved inventory shortages and created production build schedule based on clinical and engineering needs and created necessary contingency plans for multiple demand and inventory scenarios. • Managed product sterility including preparing sterilization documents and managing a 90-day shelf-life. • Created and managed part master data… Show more • Established and managed production and engineering build schedules and ordered any necessary part or materials need to fulfill necessary needs. • Resolved inventory shortages and created production build schedule based on clinical and engineering needs and created necessary contingency plans for multiple demand and inventory scenarios. • Managed product sterility including preparing sterilization documents and managing a 90-day shelf-life. • Created and managed part master data including part numbers, inventory locations, lead times, safety stocks, reorder points, min/max values, and costs leading to the ability to accurately run MRP reports, identify issues and accurately resolve any material shortages or overages. • Worked with warehouse, quality control and manufacturing departments to identify material discrepancies to resolve and update Macola ERP system and disposition inventory to correct material locations. • Drafted and executed multiple user acceptance testing documents to validate Macola ERP software to handle required real-world scenarios. • Designed and managed Kanban process on the manufacturing floor and cleanroom areas for continuous flow of parts. • Prepared and processed requisitions and purchase orders for machinery, equipment, tools, raw materials, parts, services, and supplies. • Collaborated with offsite vendor to reconcile their raw material inventory counts and accurately account for scrap rates to effectively plan for our production orders. • Oversaw a cross-functional teams to develop new SOPs, bill of materials, product structures and forms to better establish revision controls. • Issued and closed production work orders, and setup processes to streamline the internal inventory transfer processes. • Partnered with finance department to resolve purchase order discrepancies. • Managed materials for international shipments to over 15+ countries in 10+ languages.
-
-
Distribution Associate
-
May 2016 - Nov 2016
• Verified goods received against purchase orders and entered received materials into ERP system for proper inventory tracking. • Maintained records of goods, rejected unsatisfactory items, and ensured documentation accuracy including necessary production travelers, RoHS2 compliance material certifications and other necessary documentation. • Inspected incoming materials for workmanship, dimensions, tolerances, and usability requirements. • Created non-conforming material reports and… Show more • Verified goods received against purchase orders and entered received materials into ERP system for proper inventory tracking. • Maintained records of goods, rejected unsatisfactory items, and ensured documentation accuracy including necessary production travelers, RoHS2 compliance material certifications and other necessary documentation. • Inspected incoming materials for workmanship, dimensions, tolerances, and usability requirements. • Created non-conforming material reports and assisted with root cause investigation for all materials that did not meet product specifications. • Researched cycle counting modules in ERP system to establish procedures to better control inventory accuracy. • Communicated improvement opportunities and concerns within warehouse and manufacturing areas.
-
-
-
Target
-
United States
-
Retail
-
700 & Above Employee
-
Senior Target Protection Specialist
-
Apr 2013 - May 2016
• Responsible for reducing inventory discrepancies by 20% through the use of online inventory tracking applications, on-hand physical counts and reverse logistic reporting. • Promoting a safe and secure work environment by training new hires and current workforce on safety and security procedures which decreased store safety incidents by 50%. • Increasing communication throughout security team by giving direction and creating policies that provided each team member with tools to… Show more • Responsible for reducing inventory discrepancies by 20% through the use of online inventory tracking applications, on-hand physical counts and reverse logistic reporting. • Promoting a safe and secure work environment by training new hires and current workforce on safety and security procedures which decreased store safety incidents by 50%. • Increasing communication throughout security team by giving direction and creating policies that provided each team member with tools to effectively communicate. • Coordinating with local law enforcement when detainments were made of shoplifters. • Investigating and reporting employee theft. • Managing the security team schedule to provide the best coverage for theft prevention. • Chosen by top management to lead Black Friday implementation plan.
-
-
Guest Service Attendant (Front End Manager)
-
Oct 2011 - Apr 2013
• Lead team members in increasing sales, customer satisfaction and customer loyalty by resolving problems quickly and efficiently, partnering with the correct people at all times, increasing customer service levels and overall store employee morale • Recorded and counted up to $120,000 in cash per day from the previous day’s sales. • Managed up to 30 employees at a time which included guest service team members, cashiers, Starbucks team members and Target café team members. • Ordered… Show more • Lead team members in increasing sales, customer satisfaction and customer loyalty by resolving problems quickly and efficiently, partnering with the correct people at all times, increasing customer service levels and overall store employee morale • Recorded and counted up to $120,000 in cash per day from the previous day’s sales. • Managed up to 30 employees at a time which included guest service team members, cashiers, Starbucks team members and Target café team members. • Ordered front end and general facility supplies for the store and created efficient planning and ordering guides for each supply which included lead times, storage location and sensitivity for each item. This lead to a decrease of storage room needed by 400% with minimal stock outs.
-
-
Cart Attendant
-
May 2011 - Oct 2011
In charge of restoring and maintaining supply of carts in the store. Managed cleaning supplies and bathroom cleanliness.
-
-
Education
-
California State University San Marcos
Bachelor’s Degree, Global Supply Chain Management -
La Costa Canyon High School
Community
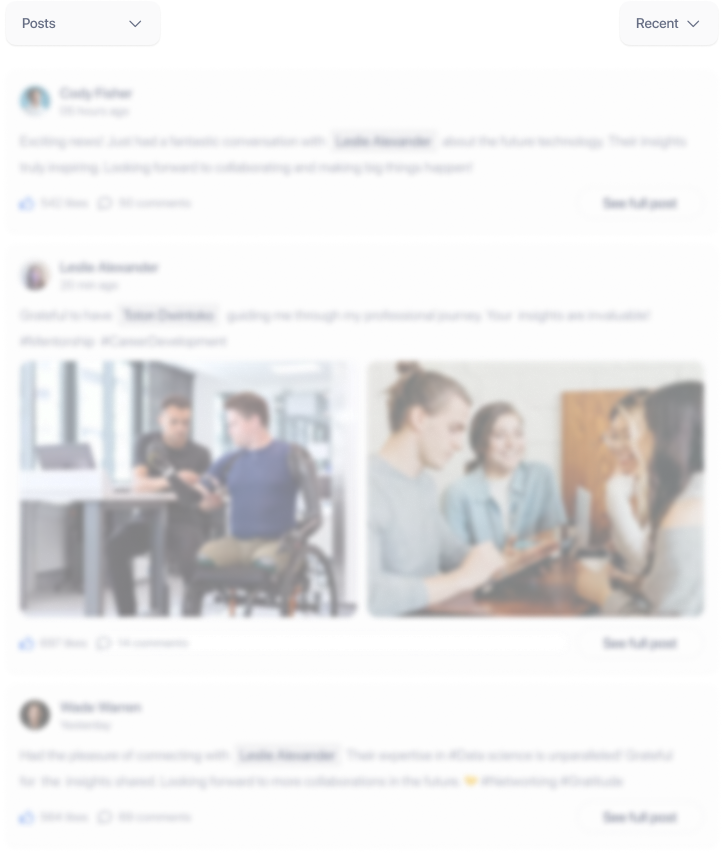