Dave Evans
Operations Manager at Avcorp Industries- Claim this Profile
Click to upgrade to our gold package
for the full feature experience.
Topline Score
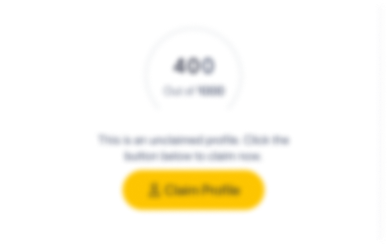
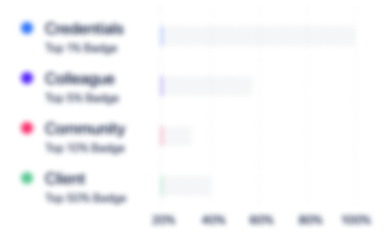
Bio
0
/5.0 / Based on 0 ratingsFilter reviews by:
Experience
-
Avcorp Industries
-
Canada
-
Aviation and Aerospace Component Manufacturing
-
1 - 100 Employee
-
Operations Manager
-
Oct 2021 - Present
-
-
-
CORE Energy Recovery Solutions
-
Germany
-
Renewable Energy Equipment Manufacturing
-
1 - 100 Employee
-
Production Manager
-
Feb 2021 - Dec 2021
-
-
-
BOMBARDIER
-
Canada
-
Aviation and Aerospace Component Manufacturing
-
700 & Above Employee
-
Operations Unit Manager
-
Mar 2017 - Feb 2021
Global 7000 / 8000 program Global 7000 / 8000 program
-
-
-
Atlantic Packaging Products Ltd.
-
Canada
-
Packaging and Containers Manufacturing
-
500 - 600 Employee
-
Plant Superintendent
-
Mar 2016 - Feb 2017
-
-
-
Bombardier Aerospace
-
Netherlands
-
Business Consulting and Services
-
-
Apr 2012 - Oct 2015
Lead the Q400 Aerostructures business in a 24/6 environment, continuously meeting schedule whilst adapting the flow to incorporate variability in the production line based upon customer demand (Options). Integrated a new Production Bay and incorporated new work centres for the Q400 program. Successfully managed the Q400 Aerostructures program on schedule during a turbulent period which saw multiple changes of master schedule in 24 months (unprecedented during the programs history). Led a team of Engineering, Methods, Logistics, Procurement, Quality and onsite Fabrication to build the 1st Cargo–Combi variant of the Q400 from drawing board to first Flight in less than 17mths. Led incremental change management processes to facilitate the transition of work to an offsite vendor whilst re-balancing the production build, during an 18 mth phased transition in the Fuse integration of the Q400. Managed between 120 – 140 people over 4 work centres and 5 Speciality Support shops, working over a 24 Hr period. Successfully implemented the Achieving Excellence System in all Production environments. Reduced staff levels by 15% utilising Yamazumi techniques that incorporated flexibility and ergonomic factors to increase productivity. Show less
-
-
-
Dec 2008 - Apr 2012
Embedded internal consultant aligned with external consultants to implement dynamic change on the Toronto site by the adoption of the Achieving Excellence System utilising Lean methodologies such as, but not limited to Problem Solving; Kaizen; Six Sigma; Yamazumi; Value Stream mapping and 5S. Led the Project team for the development of the Bombardier Achieving Excellence System Academy from which the site improvement models of Broad & Shallow, Narrow & Deep were implemented. Developed Aerostructures as a Business Unit using Hoshin Kanri (Policy Deployment) as the foundation of the department; created an aligned Balanced scorecard; 3 year Masterplan and future state via a Blue Sky Vision process. Created standards and implemented the methodology to measure deviance against these standards. Developed a strong link to operational management via daily meetings and coached to ensure that improvements were measured and implemented. Implemented the Achieving Excellence System within the Toronto site by embracing the adoption of Lean thinking methodologies. As an Internal consultant developed a Pilot Work Centre into a world class manufacturing unit. Embedded into the Logistics Organisation to decrease inventory; increase cycle times and the introduction of Kanbans via the Kaizen process. Show less
-
-
-
-
Press & Plate Room Superintendent
-
Sep 2005 - Oct 2008
Lead a highly unionised operation (Teamsters), to improve operational and managerial performance to meet major changes in the newspaper market in Toronto changing a conventional newspaper print site into a commercially viable manufacturing business. Responsible for 19 supervisors, 146 full time and 48 part time employees. Managed an operational budget of $18.4 million CDN, and operational control of paper inventory in excess of $70 Million. Implemented a negotiated operational manning reduction twice in two years throughout the press room with zero impact to the sites efficiency. As a member of the management bargaining team achieved a landmark contract renegotiation within the Province of Ontario, negotiating major contract changes that took place during an existing Union Contract which still had over two years left to completion. Led the operational sub-committee of management and union officials that successfully implemented contractual changes with no disruption to the business. Reported to the Steering Committee of National Union officials (Teamsters) and Toronto Star Senior management of which I was also a member Led a Pressroom taskforce of employees and management in the implementation of a web width reduction program in the summer of 2007. Planned and implemented the roller exchange program of 2,600 rollers in 12 weeks, brought under budget by $3.4 Million and ahead of schedule by 3 days using lean manufacturing techniques. Implemented Computer To Plate technology into the Plate making department, reorganised the work-flow and training, whilst managing the subsequent loss of positions. Show less
-
-
-
-
-
Jan 2002 - Sep 2005
Continuously improved printing in terms of health and safety performance, customer service, quality, pro-duction efficiency and costs to meet business needs and satisfy agreed customer requirements. Responsible for managing 8 Managers and 181 shop floor staff. Developed and led a managerial team in continuous improvement initiatives. Delivered leadership, motivation and discipline of personnel, in 365 days a year 24 hours a day production environment. Improved both operational and financial performance of a large printing business, including reducing unit cost by 7.4% (£2.2 million) over a 4-year period. Project member for waste management continuous improvement team, which achieved a first year saving of £260,000 ($600,000) Designed, implemented and operated a flexible working system within a highly unionised environment, the first within the group manufacturing division. Show less
-
-
-
Jan 2000 - Jan 2002
Responsible for all site operations: Production of 4 National newspaper tiles & up 12 differing regional titles.Health & Safety of all site personel (180) Performance Management and optimisatiojn of production assets
-
-
-
Jan 1998 - Jan 2000
-
-
Education
-
Loughborough University
Post Graduate Certificate: Certificate, Management
Community
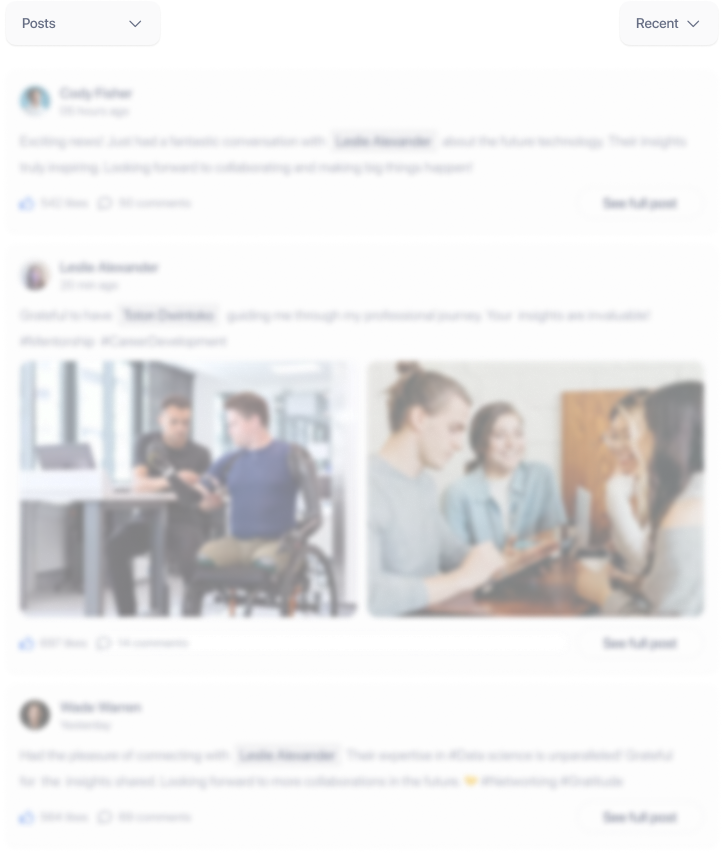