Daniel Sawall
Safety Director at IVI Inc.- Claim this Profile
Click to upgrade to our gold package
for the full feature experience.
Topline Score
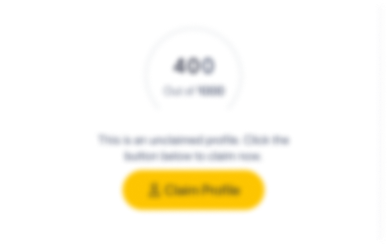
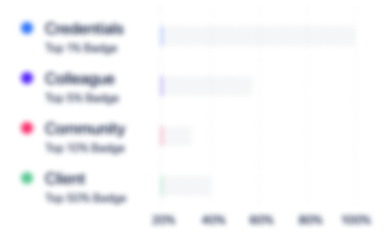
Bio

Chris Campbell
I have worked with Dan for 6 months while at GE. In his capacity as EHS Administrator, he helped develop many of the higher level safety policies - specifically those relating to Higher Risk Operations. Dan also provided training in these Higher Risk Operations to manufacturing employees. Dan has the ability to research operations, identify the significant safety concerns, write those into comprehensible policies, and train employees in the portions relevant to their day-to-day activities. I have also seen him work outside our group in the site's Quality group, and performing equally well. I offer my highest recommendation for Dan in his chosen fields as a solid and talented professional.

Michael (Mike) Vande Voort
Dan has shown that he possesses the knowledge and ability to convey his skills to others helping them to succeed as well as develop as valued employees and as a person. He strives for perfection and takes pride in a job well done. The skill set he possesses is an asset which he can bring to any position that he encounters. It has been my pleasure and privilege to work with him in the past.

Chris Campbell
I have worked with Dan for 6 months while at GE. In his capacity as EHS Administrator, he helped develop many of the higher level safety policies - specifically those relating to Higher Risk Operations. Dan also provided training in these Higher Risk Operations to manufacturing employees. Dan has the ability to research operations, identify the significant safety concerns, write those into comprehensible policies, and train employees in the portions relevant to their day-to-day activities. I have also seen him work outside our group in the site's Quality group, and performing equally well. I offer my highest recommendation for Dan in his chosen fields as a solid and talented professional.

Michael (Mike) Vande Voort
Dan has shown that he possesses the knowledge and ability to convey his skills to others helping them to succeed as well as develop as valued employees and as a person. He strives for perfection and takes pride in a job well done. The skill set he possesses is an asset which he can bring to any position that he encounters. It has been my pleasure and privilege to work with him in the past.

Chris Campbell
I have worked with Dan for 6 months while at GE. In his capacity as EHS Administrator, he helped develop many of the higher level safety policies - specifically those relating to Higher Risk Operations. Dan also provided training in these Higher Risk Operations to manufacturing employees. Dan has the ability to research operations, identify the significant safety concerns, write those into comprehensible policies, and train employees in the portions relevant to their day-to-day activities. I have also seen him work outside our group in the site's Quality group, and performing equally well. I offer my highest recommendation for Dan in his chosen fields as a solid and talented professional.

Michael (Mike) Vande Voort
Dan has shown that he possesses the knowledge and ability to convey his skills to others helping them to succeed as well as develop as valued employees and as a person. He strives for perfection and takes pride in a job well done. The skill set he possesses is an asset which he can bring to any position that he encounters. It has been my pleasure and privilege to work with him in the past.

Chris Campbell
I have worked with Dan for 6 months while at GE. In his capacity as EHS Administrator, he helped develop many of the higher level safety policies - specifically those relating to Higher Risk Operations. Dan also provided training in these Higher Risk Operations to manufacturing employees. Dan has the ability to research operations, identify the significant safety concerns, write those into comprehensible policies, and train employees in the portions relevant to their day-to-day activities. I have also seen him work outside our group in the site's Quality group, and performing equally well. I offer my highest recommendation for Dan in his chosen fields as a solid and talented professional.

Michael (Mike) Vande Voort
Dan has shown that he possesses the knowledge and ability to convey his skills to others helping them to succeed as well as develop as valued employees and as a person. He strives for perfection and takes pride in a job well done. The skill set he possesses is an asset which he can bring to any position that he encounters. It has been my pleasure and privilege to work with him in the past.

Credentials
-
Lean Lead Facilitator
Milwaukee School of Engineering (MSOE)Sep, 2009- Nov, 2024
Experience
-
IVI Inc.
-
United States
-
Industrial Machinery Manufacturing
-
1 - 100 Employee
-
Safety Director
-
Aug 2019 - Present
IVI, Inc. uses technology and experience to develop and install innovative air quality solutions. IVI, Inc. has evolved into one of the only full-service, mechanical contractors in the United States, specializing in industrial ventilation systems. - Manage safety at five locations in Wisconsin, South Carolina and Oklahoma, in addition to providing safety direction and support at job sites across the United States, Canada and Mexico. - Direct resources and activities of the organization to support the Health and Safety programs by providing advice and guidance to employees at all levels of the organization. - Develop and implement job specific safety training. - Develop, implement and maintain standard policies and procedures for health and safety. - Manage the Company’s Emergency Response Team. - Participate in Project Kick-off meetings to assist with and prepare Site Specific Safety Plans. - Implement and maintain a schedule for site visit safety audits – both announced and unannounced. - Manage Company’s Respirator Fit Test and Hygiene Assessment programs.
-
-
-
Milk Specialties Global
-
United States
-
Dairy Product Manufacturing
-
200 - 300 Employee
-
Environmental, Health and Safety Manager
-
Oct 2018 - Aug 2019
• Lead compliance of all applicable company environmental, health and safety (EHS) standards, as well as all federal, state and local regulations for the MSG Fond du Lac and Boscobel plants.• Develop, maintain and manage company EHS programs at both facilities.• Work with the highest ethical standard for legal compliance and demonstrate a true passion for employee safety.• Conduct regular safety and environmental inspections.• Provide monthly EHS training, in addition to providing new employee orientation.• Lead Behavioral Based Safety initiatives including coaching team members to take safety ownership and actively participate in safety observations, together with finding solutions to safety hazards and issues.• Professionally train, coach and advise personnel on all identified safety risks, and establish a proactive approach to providing a safe working environment for everyone.• Collaborate with managers, first-line supervisors and hourly workforce to investigate and manage all injuries, environmental releases and near miss incidents.• Actively participate with the plant management teams and safety committees to develop corrective actions for identified risks.• Manage workers compensation claims for Fond du Lac and Boscobel plants. Monitor return to work instructions given by health care providers, in addition to advising area managers and supervisors on appropriate return-to-work activities.
-
-
-
Suominen Corporation
-
Finland
-
Textile Manufacturing
-
200 - 300 Employee
-
Safety Specialist
-
Feb 2017 - Oct 2018
- Developed and delivered annual Safety Days training for 115 team members; 8-hour class provided monthly covering OSHA required topics in addition to safety best practices- Implemented and managed Behavioral Based Safety program, as well as trained team members how to conduct effective safety walks - Created new Brady Lockout / Zero Energy State (ZES) procedures (over 250 published in 2017)- Developed, implemented and managed Company’s safety programs, policies and procedures- Performed safety walks, audits and inspections to identify unsafe conditions/acts and recommended corrective actions- Led incident investigations including root cause analysis and determining corrective actions- Created Job Safety Analysis (JSA) to be used as tools to prevent incidents- Facilitated cross-functional safety committee
-
-
-
Wisconsin Public Service
-
Utilities
-
300 - 400 Employee
-
Training Consultant
-
Jun 2014 - Feb 2017
- Developed and facilitated safety training; over 1800 days without a lost time incident- Championed Slips, Trips and Falls campaign to reduce injuries: wrote procedures, developed inspection and observation checklists; zero slips, trips and falls injuries in 2015 and 2016- Facilitated 22 “Speak-up Listen-up” classes for 335 Power Generation salaried and represented team members; teach how to give effective feedback and receive feedback with an open mind- SafeStart project manager: delivered SafeStart training to Power Generation salaried and represented team members: taught SafeStart concepts of avoiding the four primary states of rushing, fatigue, frustration and complacency which can lead to critical errors including eyes and mind not on task, moving or being in the line of fire and losing your balance, traction and grip- Coordinated annual Block Training: provide OSHA, environmental and plant-required training- Created new contractor safety orientation DVD to improve safety orientation for contractors and visitors; zero non-employee recordable incidents since inception of new program
-
-
-
Expera Specialty Solutions
-
United States
-
Paper and Forest Product Manufacturing
-
1 - 100 Employee
-
Safety Manager
-
Aug 2011 - Jun 2014
Provided safety leadership for approximately 600 salaried and represented team members.- Collaborated with team members to heighten safety awareness and prevent injuries through hazard recognition and safety observations; 15% increase in reported observations (2012) and 30% (2013)- Championed safety initiatives to abate hazards, as well as improve processes and behaviors; recordable incidents reduced by 20% (2011-2012) and an additional 43% (2012-2013)- Led incident investigation teams; used Why Tree process to determine root causes/corrective actions- Co-chaired cross-functional mill-wide Joint Safety Committee and Area Safety Committees- Served as an Agent of Change to help team members understand all injuries are preventable- Created and delivered effective safety orientation for new hires and monthly safety training for salaried and represented team members to improve safety performance and ensure regulatory compliance- Authored safety policies, procedures and standard work- Managed IndustrySafe website: incidents, hazards and corrective actions, observations and inspections
-
-
-
-
Environmental, Health and Safety Coordinator
-
May 2010 - Aug 2011
Contract position with The QTI Group. - Collaborated with 165 management and represented team members to promote a safe workplace.- LMS Administrator- Authored OSHA VPP Star policies, procedures and work instructions- Created and delivered effective classroom training- Facilitated cross-functional safety committees- Conducted Safety Risk Assessments and EHS inspections to identify and mitigate safety hazards / risks- Performed internal audits to strive for continuous improvement- Administered EHS website, E-Learning and SDS systems- Implemented incentive programs to reward employees for safe acts and promote participation in safety improvement programs- Employed customer service skills to build relationships with contractors, vendors and internal customers
-
-
-
-
Lean Facilitator & Trainer (volunteer)
-
Oct 2009 - Jul 2010
Provided Lean facilitation and training services to businesses to identify and eliminate waste, achieve greater efficiencies and improve competitiveness by applying Lean concepts and tools to efficiently utilize resources to become World Class Enterprise.- Collaborated with ThedaCare Heritage / Peabody Manor for a 2P improvement event: developed plans to redesign the Receiving and Food Services areas to eliminate congestion, increase efficiency, improve safety and increase vendor / staff satisfaction.- Spearheaded Lean and training initiatives for Valley Packaging Industries: used value stream mapping to identify waste and reduce non-value added time to improve processes / efficiencies.- Co-facilitated A3 strategic deployment for the Habitat for Humanity ReStore: identified and eliminated waste; improved processes and efficiency.
-
-
-
-
Technical Writer
-
Mar 2009 - Apr 2009
Contract position with Randstad Staffing.- Collaborated with subject-matter experts to accurately accomplish technical writing initiatives.- Wrote intelligible standard work and training documentation for Oracle applications. Contract position with Randstad Staffing.- Collaborated with subject-matter experts to accurately accomplish technical writing initiatives.- Wrote intelligible standard work and training documentation for Oracle applications.
-
-
-
Verso Corporation
-
United States
-
Paper and Forest Product Manufacturing
-
700 & Above Employee
-
Training Administrator, Instructional Designer and Continuous Improvement Facilitator
-
Jan 2005 - Sep 2008
Provided training and safety leadership for 600 salaried and represented team members.- LMS Administrator- Created effective training content, authored ISO 9001/14001 and OHSAS 18001 documentation, intelligible standard work and safe work practices- Coached High Performance Work Organization teams- Managed and mentored 24 designated trainers- Facilitated value stream activity to eliminate waste in document approval and record retention process; improved approval time by nearly 70% and minimized hard-copy storage by utilizing electronic systems - Led continuous improvement endeavor to address a lost order; regained significant order of five days of production per month (2500 tons of paper)- Collaborated with Safety Manager and Safety Captains to promote STOP program, train employees and increase the number of reported safety observations to heighten safety awareness and reduce incidents; TIR 1.7 and nearly 3,000,000 safe worker-hours without a lost time accident
-
-
Instructional Designer, Training Specialist and Production Worker
-
1978 - 2005
- Started career in Production and progressed to PM97 Lead Operator (Machine Tender)- Served as Training Specialist for special projects, as well as machine start-ups and rebuilds- Authored and controlled intelligible ISO 9001/14001 and OHSAS 18001 documentation- Composed comprehensible learning plans, standard work, equipment/process descriptions, problem solving guides, safe work practices and maintenance manuals- Composed written communications for the Company newsletter and Intranet- Attained ISO 9001/14001 and OHSAS 18001 certifications, improving quality, environmental and safety awareness, while continuously maintaining compliance- Led training initiatives for the safe and efficient start-up of PM97 facility: exceeded target by 25% with zero incidents- Directed continuous improvement waste reduction project: significantly reduced “shrink” (paper waste) by 35%
-
-
Education
-
Fox Valley Technical College
Associate's Degree, Applied Engineering Technology: Emphasis in Quality Assurance and Safety Management -
Milwaukee School of Engineering
Certificate, Lean Lead Facilitator
Community
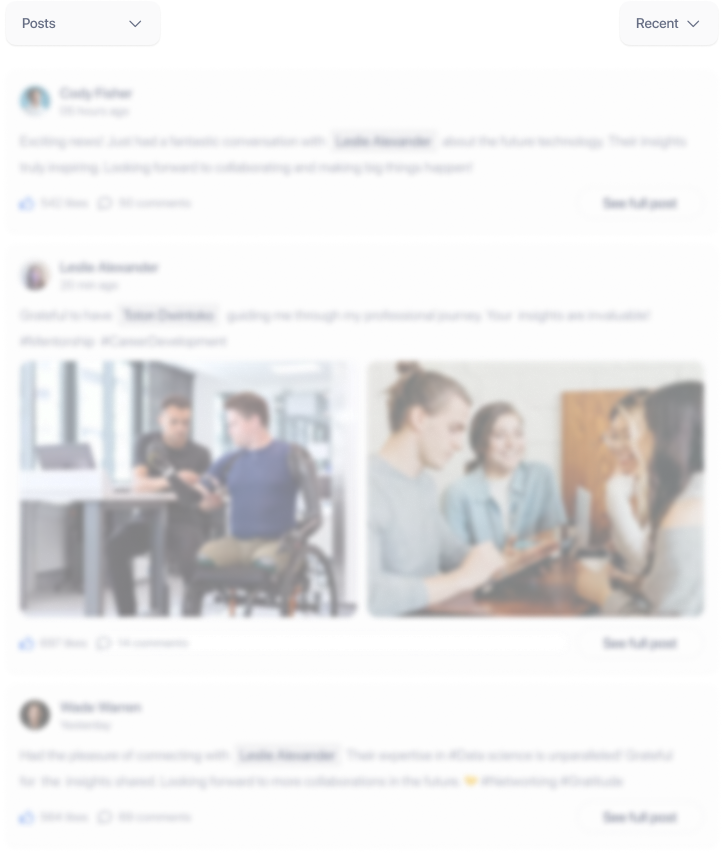