Dan Ratterman
Chief Operating Officer at Shady Rays- Claim this Profile
Click to upgrade to our gold package
for the full feature experience.
Topline Score
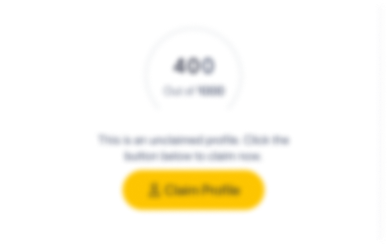
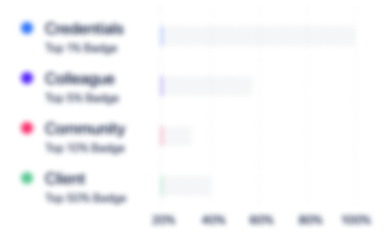
Bio


Credentials
-
Master Graduate
Rapport Leadership InternationalJan, 2018- Nov, 2024 -
Power Communication
Rapport Leadership InternationalJan, 2018- Nov, 2024 -
Lean Six Sigma Green Belt Certification
GE Appliances, a Haier companyNov, 2017- Nov, 2024 -
Leadership Breakthrough 2
Rapport Leadership InternationalMay, 2017- Nov, 2024 -
Leadership Breakthrough 1
Rapport Leadership InternationalFeb, 2017- Nov, 2024 -
ISO 9001-2008
-
Experience
-
Shady Rays Polarized Sunglasses
-
United States
-
Apparel & Fashion
-
1 - 100 Employee
-
Chief Operating Officer
-
Jan 2020 - Present
-
-
Distribution Operations Manager
-
Nov 2018 - Jan 2020
-
-
-
GE Appliances, a Haier company
-
United States
-
Manufacturing
-
700 & Above Employee
-
Manager of Manufacturing Operations
-
Jan 2018 - Nov 2018
Directly lead over 50 Union employees including 4 team leaders where I drive improvements in Safety, Quality, Cost, and Delivery using lean principles.
-
-
Global Commoditiy Leader - Operations Management Leadership Program
-
Jul 2017 - Dec 2017
Buyer of glass for GE Appliances. Glass includes cooktops, refrigerator shelves, control panels, and oven doors.
-
-
Material Flow Engineer - Operations Management Leadership Program
-
Jan 2017 - Jul 2017
· Gained strong understanding of materials in manufacturing · Developed spreadsheet to calculate route times and route utilization · Used spreadsheet to re-design routes and minimize part touches from 3 to 2 · Eliminated mini-markets to create more direct routes with less waste and better part identification · Created foundation for inventory scanning system · Worked with ERP team to develop the back-end of the scanning technology and ran successful trial with… Show more · Gained strong understanding of materials in manufacturing · Developed spreadsheet to calculate route times and route utilization · Used spreadsheet to re-design routes and minimize part touches from 3 to 2 · Eliminated mini-markets to create more direct routes with less waste and better part identification · Created foundation for inventory scanning system · Worked with ERP team to develop the back-end of the scanning technology and ran successful trial with scanners · Re-designed super market to allow for better flow and improved part location consistency
-
-
Area Business Leader - Operations Management Leadership Program
-
Jul 2016 - Dec 2016
· Led Union work force of 41 employees for three sections of plant – Spinefin, Plastics, and Ice Maker Kit · Consistently engaged with employees to build a strong team · Communicated effectively with upper operations management to ensure my sections aligned with the operation strategy of the rest of the plant · Decreased Spinefin average OT hours 32% while maintaining necessary inventory levels
-
-
Process Improvement Engineer - Operations Management Leadership Program
-
Jan 2016 - Jul 2016
· Worked closely with employees and processes on Line 2 in Decatur using the line worker’s thoughts and opinions to make improvements and gain support and engagement · Improved final assembly line speed consistency by 91% by installing a series of cylinder stops and photoeyes · Create a potential savings of $124,000 per year · Gained Six Sigma Green Belt Certification on this project
-
-
-
University of Dayton
-
United States
-
Higher Education
-
700 & Above Employee
-
Student
-
Aug 2011 - Dec 2015
-
-
-
Honda of America Mfg., Inc.
-
Automotive
-
700 & Above Employee
-
Purchasing Co-op
-
May 2015 - Aug 2015
-
-
-
GE
-
United States
-
Industrial Machinery Manufacturing
-
700 & Above Employee
-
Warehouse Efficiency Engineer
-
May 2014 - Aug 2014
As a warehouse efficiency engineer I spent a lot of time maximizing the efficiency of processes. My biggest project included designing and implementing a re-boxing station the put usable parts into a new box if the box had been damaged. This project saves GE around $300,000 a year in scrap costs. As a warehouse efficiency engineer I spent a lot of time maximizing the efficiency of processes. My biggest project included designing and implementing a re-boxing station the put usable parts into a new box if the box had been damaged. This project saves GE around $300,000 a year in scrap costs.
-
-
-
GE
-
United States
-
Industrial Machinery Manufacturing
-
700 & Above Employee
-
Process Improvement Engineer
-
May 2013 - Aug 2013
As a Process Improvement Engineer Co-op, I spent a lot of time in the factory working with line workers and inspecting the prodcution line to maximize efficiency within GE Appliances. This includes creating data analysis charts to analyze prominent issues and create strategic plans to make beneficial changes. As a Process Improvement Engineer Co-op, I spent a lot of time in the factory working with line workers and inspecting the prodcution line to maximize efficiency within GE Appliances. This includes creating data analysis charts to analyze prominent issues and create strategic plans to make beneficial changes.
-
-
-
General Electric Appliances
-
Louisville, Kentucky
-
Central Quality Co-op
-
Jan 2013 - May 2013
As a Central Quality Co-op, I managed quality documentation for two seperate plants within GE Appliances. This included mainitaing a new numbering system that organizes all documents and stardizes processes throughout the entire Appliance Company. I also travelled to a satellite plant to implement the new system. In addition, I became a certified auditor for ISO 9001:2008 and helped perform an audit. As a Central Quality Co-op, I managed quality documentation for two seperate plants within GE Appliances. This included mainitaing a new numbering system that organizes all documents and stardizes processes throughout the entire Appliance Company. I also travelled to a satellite plant to implement the new system. In addition, I became a certified auditor for ISO 9001:2008 and helped perform an audit.
-
-
-
-
Engineering Co-op
-
May 2012 - Aug 2012
As an Engineering Co-op, I created and managed a spreadsheet to show how much money is being made on every part that the company makes. I worked with the VP of Engineering and CEO of the company in weekly meetings to present the information on the spreadsheets to optimize maximum efficiency for all parts. As an Engineering Co-op, I created and managed a spreadsheet to show how much money is being made on every part that the company makes. I worked with the VP of Engineering and CEO of the company in weekly meetings to present the information on the spreadsheets to optimize maximum efficiency for all parts.
-
-
Education
-
Harvard Business School Online
Global Business Certificate, International Business -
Michigan State University
Master Certificate in Supply Chain Management & Procurement, Supply Chain Management -
University of Dayton
Bachelor of Science (B.S.), Industrial Engineering Technology
Community
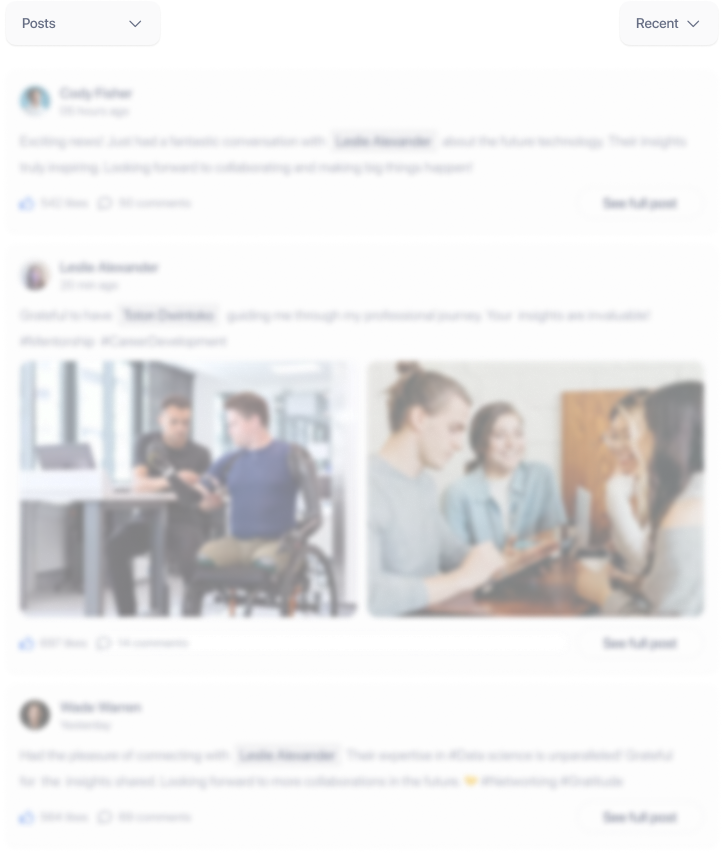