Danny Vines
Chlor-Alkali Cell Services Director and Plant Manager at Olin- Claim this Profile
Click to upgrade to our gold package
for the full feature experience.
Topline Score
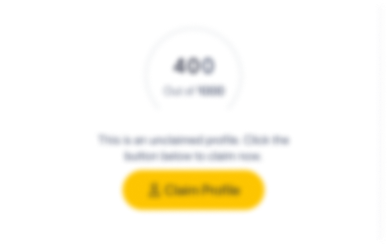
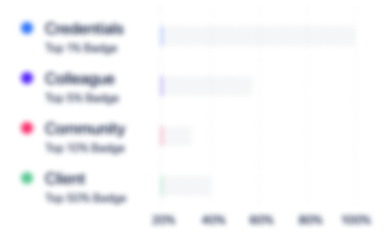
Bio


Experience
-
Olin
-
United States
-
Chemical Manufacturing
-
700 & Above Employee
-
Chlor-Alkali Cell Services Director and Plant Manager
-
Nov 2021 - Present
Responsible for all Chlor-Alkali Cell Services activities for Olin, which includes the Russellville, Arkansas site as well as Cell Services located in Plaquemine, LA, and Freeport, TX and provides oversight of 92 Olin personnel. All Cell Service locations coordinate the movement and repair of new and used chlorine cell components and perform the actual rebuilds at each location. This role is crucial to successful operations and the asset capability of each chlorine plant
-
-
Chemical Engineer and Project Manager
-
Jan 2011 - Oct 2021
I currently serve as the Project Manager for Gulf Coast Diaphragm Cell Rebuilds and serve as the focal point and liason for membrane and diaphragm cell hardware for Olin's Chlorine plants in Texas and Louisiana. I am responsible for managing the the annual rebuild capital for diaphragm technology on the Gulf Coast (Freeport, TX and Plaquemine, LA). I am also responsible for working with cell services and operations personnel at each Olin chlorine plant on the Gulf Coast to address and help resolve any hardware issues associated with the cells. I also serve as one of two Russellville Site engineer's responsible for ensuring day to day operations of the site. I recently served as the Project Manager and Manufacturing Representative for a $2.7 MM capital project at the Russellville Site to build a new production facility to fabricate a new product that is a critical component of diaphragm operation. The faciltiy produced in spec product on the first attempt. Show less
-
-
-
Dow
-
United States
-
Chemical Manufacturing
-
700 & Above Employee
-
Operations Leader
-
Jun 2008 - Dec 2010
As the Operations Leader at the B-2300 block of Texas Operations, I managed 29 operators and 8 processes across 3 different businesses with an RAB of $315 MM (actual replacement cost is ~$550 MM). While in that role, I developed a Run Plant Engineer Training Package (called RPE-101) and leveraged it across the Epoxy Business in Freeport as a result of a gap in RPE training for new hires. Due to the fact that we supported three business (Epoxy (core), DAS, and Specialty Chemicals), I sat on the Leadership Team for Specialty Chemicals as the focal point from B-23. As team leader of the B-23 Training Team, I created two new training packages - an EH&S Training Package which details all aspects of EH&S with respect to B-23 in one location, and a Process Automation Training package to improve both operators' and engineers' knowledge of process automation language and troubleshooting. In addition, I leveraged an "Escalation" process across the Epoxy Business in Freeport - this was also known as incorporating the concept of "what is abnormal that has become normal in your process" to raise awareness and drive EH&S performance to the next level. This process was also leveraged across businesses. Since B-23 is a highly integrated block, I also served on the Site RCl Partnership Team and served as leader of the Plant B Vent/RCl Operations Team for two years to drive improvement in the area of RCl and vent management across Plant B and the site. Show less
-
-
Unit Leader
-
Jul 2005 - May 2008
Unit Leader - I served as the unit leader for the Butylene Oxide and Glycerine process for five months and then transitioned into the role as unit leader for the Epi 3 and HOCl processes. In this role, I was responsible for leading many different aspects of plant operations - mentoring personnel(operators and run plant engineers), EH&S, technical coaching, cost management, efficient training, and effective communication. I improved my EH&S leadership skills by leading the B-23 EH&S Team and helping to drive results by looking at data and putting plans in place to improve performance. I developed a much improved system to track goal performance for both our block and department. Show less
-
-
Improvement Engineer
-
Sep 2000 - Jun 2005
I spent five years as an Improvement Engineer for Allyl Chloride 1 and 2 in the Epoxy Business, in addition to providing a lot of operations support. A lot of the time was spent as Manufacturing Representative on the RCl/HCl Scrubber Project (a $10 MM capital project), which was started up without injury and operated as designed. As an improvement engineer, I received my black belt certification in Six Sigma (MAIC) and a green belt certification in DFSS. I completed five Six Sigma Projects in addition to my capital improvement projects. Most of my projects were associated with the Allyl 2 process where I was able to optimize plant operation and increase production capability by 35%. Show less
-
-
Run Plant Engineer
-
Aug 1998 - Aug 2000
Epi 2 and Allyl Chloride - I continued as the TTU run plant engineer in the B-6800 block and added the Epi 2 and Allyl Chloride plants to my responsibility. As run plant engineer for Allyl Chloride, I was able to help operations set numerous monthly production records. I was one of the main focal points in the B-68 Turnaround in 2000, which was very successful (on schedule and no injuries). And finally, I was the main leader in helping B-68 Operations achieve Stage 2 Empowerment.
-
-
Run Plant Engineer
-
Jan 1996 - Jul 1998
Thermal Treatment Units (TTUs) - I started my Dow career in production as the run plant engineer for the Epoxy Products & Intermediates TTUs. This consisted of five TTUs across two blocks. In this role, I managed 6 different Trial Burns to meet the environmental regulations regarding Boiler Industrial Furnace (BIF). At the same time, I was able to increase capacity by 25% on two units, and 10% one another. In addition, Automatic Waste Feed Cut-Offs were reduced by over 90%.
-
-
Education
-
University of Arkansas at Fayetteville
Bachelor of Science (BS), Chemical Engineering
Community
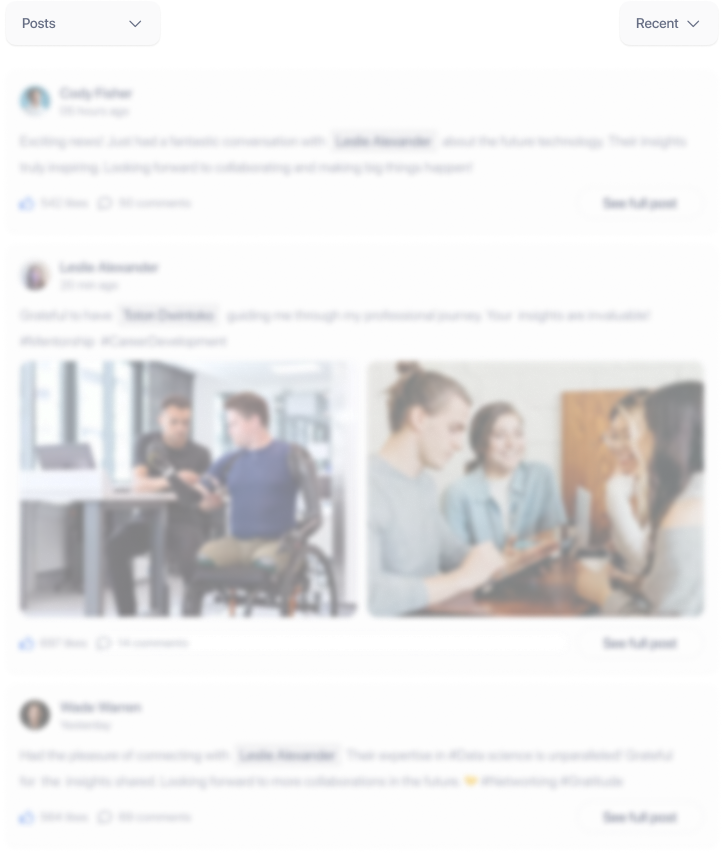