Danish Wajid
Operations & Maintenance Coordinator at Sydney Water- Claim this Profile
Click to upgrade to our gold package
for the full feature experience.
-
English Full professional proficiency
-
Urdu Native or bilingual proficiency
-
Punjabi Limited working proficiency
Topline Score
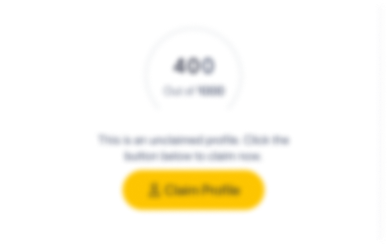
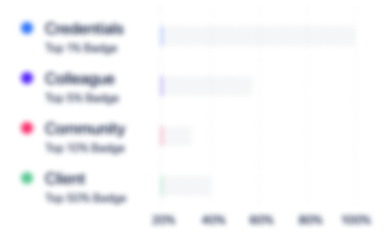
Bio


Credentials
-
Confined Space Entry Cetification
-Apr, 2018- Nov, 2024 -
Advanced First Aid (HLTAID003)
SurvivalJun, 2016- Nov, 2024 -
Return to Work Coordinator
Work Cover NSWApr, 2016- Nov, 2024 -
NEBOSH - International General Certificate in Occupational Safety & Health
National Examination Board of Occupational Safety & Health ( UK )Aug, 2015- Nov, 2024 -
National Licence to Perform High Risk Work (LF)
Work Cover NSWApr, 2016- Nov, 2024
Experience
-
Sydney Water
-
Australia
-
Utilities
-
700 & Above Employee
-
Operations & Maintenance Coordinator
-
Sep 2018 - Present
• Coordination lead for Operational planning/resourcing, Maintenance & Projects planning & scheduling for Blue Mountains Hub (Penrith WRP, Winmalee WWTP, Richmond WRP & North Richmond WWTP)• Contributing to a high performing team culture and commitment to the improvement of safety, customer, health & environmental outcomes • Developing resource planning & resource allocation capability to support the Hub for efficient delivery of work, identifying & addressing any deficiencies • Contributing to the operation of plants in alignment with approved Production Plans ensuring license and regulatory compliance & approved budgets • Coordinating and consolidating work across the Hub into a single monthly forecast and weekly schedule & update the Hub operational calendar• Single point of contact for scheduling Hub maintenance, minor works & capital works for Sydney Water internal (Capital Projects, HV, Networks, SCADA work, Properties, IT), maintenance contractor, other contracted service providers • Providing input into Hub budgets and contribute to decisions regarding risk mitigation, risk acceptance, and incident management activities • Facilitating risk assessments & the development of contingency plans to mitigate consequences of process, assets, operating system failure, security risks for Hub • Using asset management systems including SIRIUS, and Maximo or similar to coordinate operations & maintenance activities • Builing strong relationships with Vendors & Delivery Partners• Developing relationships with key customers and external stakeholders including; EPA, NSW Health, SafeWork NSW, Councils etc • Planning operations, maintenance and project work to ensure no impact on product quality, the environment, customer and community • Providing input into Hub budgets and decisions regarding risk mitigation, risk acceptance, and unplanned events • Managing multiple Vendors and Contractors across multiple sites/teams including concurrent projects
-
-
Senior Production Officer
-
Sep 2017 - Aug 2018
- Lead a high performing team culture and commitment to the improvement of customer and safety outcomes- Provided mentoring, support, technical advice and training to the Hub. Identified capability gaps and collaborated with the Hub Manager to improve team effectiveness- Developed team and individuals. Mentored, provided support and technical advice to the team. Identified capability gaps and collaborated with the Hub Manager to improve team effectiveness. Provided feedback to Hub Manager on individual and team performance.- Responsible for a safe workplace and work activities, participated in health and safety training and activities- Operated the plants in alignment with approved Production plans ensuring license and regulatory compliance, and approved budgets- Performed process and equipment monitoring using SCADA- Performed diagnosis and resolution for more complex process and asset issues, electrical, mechanical and instrumentation issues- Developed and implemented complex shutdown and/or flow management plans for the Hub which minimize disruption & safety risks utilizing asset isolation procedures- Lead plants through audits and IMS reviews- Lead planner for planned maintenance activities on site- Lead weekly and monthly maintenance meetings
-
-
-
-
Operations Supervisor
-
Jan 2016 - Sep 2017
- Worked as an Operations Supervisor at Cleanaway (Technical & Environmental Services). Leading a team consisting of 6 Chemists & 15 Operators. - Ensured compliance of Dangerous Goods transport as per Australian DG transport standards - Ensured any unidentified waste material is properly tested & identified before it is stored (on & off site) - Development of a means of safe treatment of the hazardous waste onsite (chemical/physical treatment) - Found the most economical & environmentally friendly disposal route for a waste material off site (external customer) - Responsible for coordinating maintenance with internal & external service providers - Implementation of DG Goods storage standards onsite - Ensured site remains within its DG goods storage capacity - Provided leadership to staff with respect to storage, handling, waste disposal & treatment. - Coordination with vendors & customers regarding hazardous waste collection, disposal, handling & transport - Ensured the site meets the Australian EPA & legislative standards - Team Leader for Hazardous Household Waste Collections (HHWC), organized by the EPA Australia. Planning & Executing HHWC at various locations over New South Wales. - HAZOP team member for the HAZPAK 2 project & also BluBox Machine - Site team Leader for HazPak project & also BluBox installation & commissioning - Involved in operations management, risk assessments, pre-installation: * Balcon machine used for separating mercury contaminated powder, aluminum fittings & glass from fluorescent tubes/lights * BluBox macine used for e-waste recycling * Acid/Base neutralization unit * T-Mark machine for safe separation/disposal of paint & metal cans * Liquid & solid waste treatment plant * HazPak II
-
-
-
ICI Pakistan Limited
-
Pakistan
-
Chemical Manufacturing
-
700 & Above Employee
-
Shift Coordination Manager
-
Aug 2013 - Oct 2015
Worked as a Shift Coordination Manager responsible for running smooth & safe operations of a 330 TPD Continuous Process Polymer Plant• Lead a team of around 30 employees• Custodian of plant production, quality, energy & waste reduction• Propose & implement energy conservation & waste reduction plans• Carrying out technical plans in liaison with Technical Dept.• Keeping plant operational at peak efficiencies & provide feedback for improvement• Catering any plant emergencies with minimum impact to production & quality• Maintaining industrial peace with unionized non-management staff• Conducting technical trainings of shift managers & operator staff• Plant Shutdown/Start-up activities• Project executions, Commissioning & start-up• Carrying out Job Safety Analysis (JSA), Risk Assessments, Developing work instructions and standard procedures for routine jobs. Carrying out audits of these procedures and also regular audits of Permit to Work• Protection of the environment, by ensuring no abnormal discharge takes place leading to high COD of external effluent waste waterActively involved in the following activities:- In Line Reactor Resurrection Project- Polymer Filter Installation - Coal Fired Heaters Commissioning & Start-up- Polymer Plant Shutdown/Start-up 2013
-
-
Shift Manager Services
-
Jan 2013 - Aug 2013
As a Shift Manager Services gained operations management experience working in an area with: • Water tube & Waste Heat Recovery Boilers• Cooling Towers & Cryogenic Nitrogen Plant• Water Treatment systems such as Reverse Osmosis Plant, Water softening units, Ion Exchange Demineralization water systems• Liquid waste water treatment plant (Effluent Treatment) by activated sludge process & trickling filter systems• Plant & Instrument Air Compressors section (reciprocating & centrifugal compressors)
-
-
Shift Manager Fibers
-
Jun 2008 - Dec 2012
Have worked as a Shift Manager of Fibers Plant, consisting of five Spinning Banks & Drawlines. Main responsibilities included:• Responsible for keeping plant running smoothly, achieving high production and quality results. • Keep up with production requirements & produce product variants, with coordination with ICI Polyester Marketing Team• Ensuring Utilities consumption indexes are within range to achieve efficient product production. Troubleshoot & rectify issues which can hinder plant efficiencies.• Conducting safety audits, permit to work audits & trainings.• Conducting trainings of Non-management & contractual staff• Carrying out Job Safety Analysis (JSA), Risk Assessments, Developing work instructions and standard procedures for routine jobs. Carrying out audits of these procedures and also regular audits of Permit to Work
-
-
Education
-
NFC Institute of Engineering & Technology
B.Sc, Chemical Engineering
Community
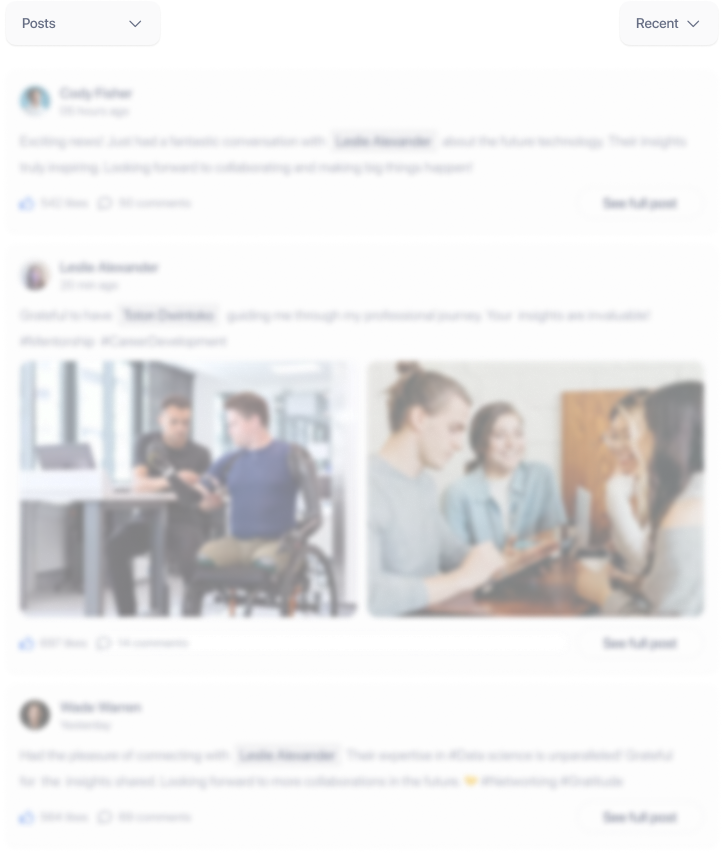