Danish Hamid
Project Manager at POWER ZONE- Claim this Profile
Click to upgrade to our gold package
for the full feature experience.
-
Arabic Elementary proficiency
-
English Full professional proficiency
-
English Full professional proficiency
Topline Score
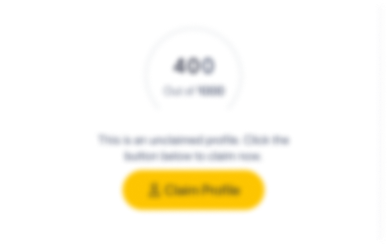
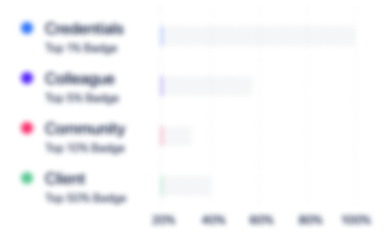
Bio


Credentials
-
Approved Engineering Degree
Saudi Council of EngineersFeb, 2023- Nov, 2024 -
Project Management Professional (PMP)®
Project Management InstituteApr, 2023- Nov, 2024
Experience
-
POWER ZONE
-
Saudi Arabia
-
Appliances, Electrical, and Electronics Manufacturing
-
1 - 100 Employee
-
Project Manager
-
Jul 2019 - Present
• Appointed as a single point of contact with the internal and external stakeholders for effective communication and swift resolution of the project issues.• Led cross-functional teams of up to 80 team members and subcontractors to successfully complete 07 projects totaling over SR 30 million in value.• Defined KPIs for the project and team members and provided performance feedback to the management on the resources.• Oversaw the development and establishment of Key project deliverables like Project Management Plan, Risk Management Plan and Project control documents like the schedule Baseline, Work Breakdown Structure, Progress Measurement Systems including CPMS and PPMS.• Planned and Monitored project execution works to ensure they are being carried out as per the approved work method statements.• Monitored, maintained the profit/loss and cash flow for the projects and apprised the management through monthly status presentations.• Identified, managed and monitored the negative and positive risks throughout the duration of the projects.• Captured the lessons learned throughout the course of the project and sharing with the team members.• Coordinated the formal closure of the punch items, signing of the certificate of initial and final acceptance by the customer.• Reduced project costs by negotiating with vendors, suppliers, and subcontractors, saving up to 10% in project expenses.• Ensured compliance with HSE plan and safety standards, resulting in zero accidents or injuries on all projects.• Negotiated and prepared change requests, resulting in a 10% increase in project revenue.• Monitored and facilitated payment milestones and collections with the Finance department. Show less
-
-
Assistant Project Manager
-
Jun 2018 - Jun 2019
• Monitored the development of Project baseline schedules, WBS and the Progress measurement systems by making sure that these metrics were completed on schedule and properly updated.• Improved project profit margins by 20% by identifying and eliminating project inefficiencies.• Reviewed, negotiated, analyzed, and managed construction contracts and change orders, resulting in 10% cost savings.• Compiled and organized data to create presentations for top management meetings and reported on progress, identifying the metrics that best reflected the progress of the project.• Led punch-list and project close-out activities to ensure that project met contractual obligations and was delivered on timeand within budget.• Created detailed minutes for all important client meetings, distributing minutes to attendees and following up to ensure action points were completed. Show less
-
-
Project Engineer
-
May 2012 - May 2018
• Managed communication with subcontractors by tracking project progress, coordinating daily activities, and reviewing all material deliveries, resulting in a smoother construction process and on-time project completion.• Controlled project scope by ensuring the design and project specifications were met, which reduced physical change orders by 15%.• Monitored site activities by conducting daily construction inspections and ensuring the targets in the construction work plans were being met, to ensure efficient construction and customer satisfaction.• Collaborated with project managers, supervisors and quality control teams to develop and maintain a schedule for raising RFIs and conducting inspections on time, resulting in meeting project deadlines.• Supervised field activities to make sure best practices were being followed while providing training on local safety regulations, leading to improved job safety. Show less
-
-
-
TAFE - Tractors and Farm Equipment Limited
-
India
-
Motor Vehicle Manufacturing
-
700 & Above Employee
-
Industrial Engineering Intern
-
Jan 2012 - May 2012
As an Industrial Engineering Intern, my role on this project was to identify the internal and external complaints from customers occurring frequently and proposing the process improvement strategies to reduce the frequency of these complaints. Key Responsibilities • Identified and analysed the internal and the external customer complaints from the past 6 months and traced them back to the production stage from where they originated. • Prepared PFMEA and identified improvement areas which improved the risk priority number. • Conducted root cause analysis of the bottle neck stages to identify the source of the issues. • Proposed improvement strategies like re-layout of tyre storage yard, implementing trolleys for shifting the tyres to the shop floor etc. which reduced the labour costs by USD 2,500 per month. Show less
-
-
Education
-
R. V. College of Engineering, Bangalore
Bachelor's degree, Engineering/Industrial Management -
Burn Hall School
High School, A
Community
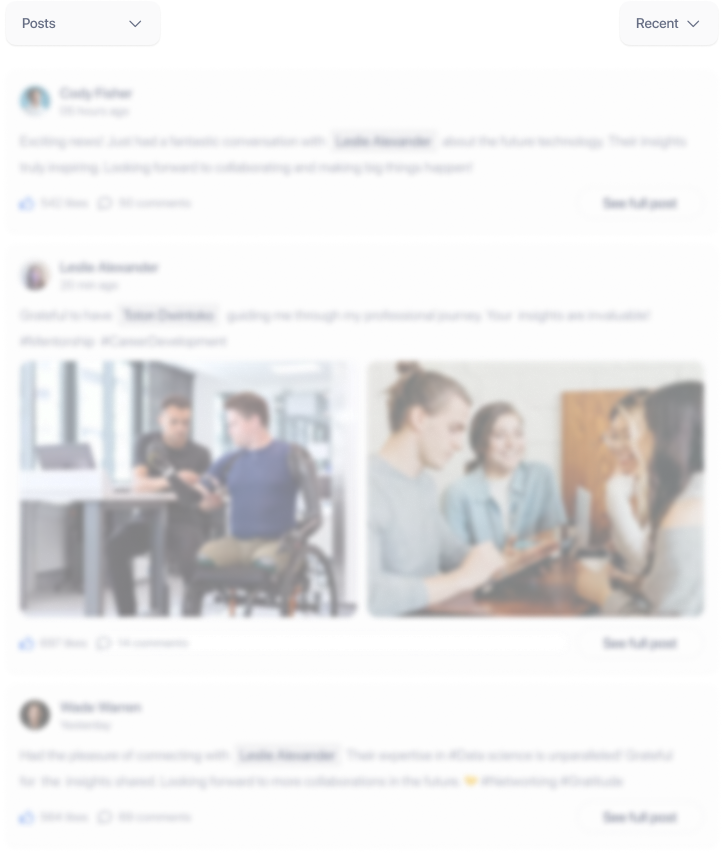