Daniel Sierra
Production Engineer at INEOS Styrolution America LLC- Claim this Profile
Click to upgrade to our gold package
for the full feature experience.
Topline Score
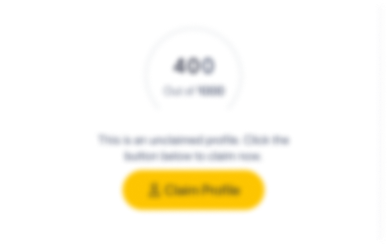
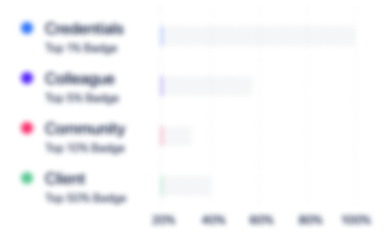
Bio


Credentials
-
Dust Hazard Analysis & Risk Assessment
Primatech Inc.Mar, 2019- Oct, 2024 -
Layers of Protection Analysis (LOPA) for Process Safety Management (PSM)
Primatech Inc.Mar, 2019- Oct, 2024 -
Process Hazard Analysis (PHA) for Team Leaders
Primatech Inc.Jun, 2018- Oct, 2024
Experience
-
INEOS Styrolution America LLC
-
United States
-
Chemical Manufacturing
-
300 - 400 Employee
-
Production Engineer
-
Aug 2019 - Present
-
-
Process Engineer
-
Jun 2017 - Aug 2019
o Provide daily process support for a continuous mass, polystyrene plant producing general-purpose (GPPS), hi-impact (HIPS), and a styrene-methyl methacrylate (NAS) polymers. o Provide technical support on capital projects for asset improvements and process optimization.o PHA Leader – Prepare, organize, and coordinate PHA studies for site PHA revalidations and MOC design reviews, as needed. Lead PHA studies and prepare final reports to site management.
-
-
-
INEOS Styrolution America LLC
-
United States
-
Chemical Manufacturing
-
300 - 400 Employee
-
Operations Engineering Co-op
-
Jan 2017 - Apr 2017
General process engineering support for plant shutdown, turnaround, and startup. Oversaw implementation of major capital projects for repacking towers. Performed equipment inspections and closure signoffs for process engineering. General process engineering support for plant shutdown, turnaround, and startup. Oversaw implementation of major capital projects for repacking towers. Performed equipment inspections and closure signoffs for process engineering.
-
-
-
INEOS Styrolution America LLC
-
United States
-
Chemical Manufacturing
-
300 - 400 Employee
-
Operations Engineering Intern
-
May 2016 - Aug 2016
-
-
-
LyondellBasell
-
United States
-
Chemical Manufacturing
-
700 & Above Employee
-
Production Engineering Co-op
-
Aug 2015 - Dec 2015
Worked in a chemical plant that produces propylene oxide. Projects included evaluating fire cases for relief valves as well as sizing relief valves. I became very knowledgeable about furnaces and fired equipment as one of my projects involved gathering information on furnace equipment documents, the furnace designs and systems, as well as interlocks. One project allowed me to troubleshoot a system and come up with my own recommendations for solutions. Through this I became very knowledgeable on piping designs, pumps and pumping curves, and performing system pressure calculations. Show less
-
-
-
INEOS Styrolution America LLC
-
United States
-
Chemical Manufacturing
-
300 - 400 Employee
-
Operations Engineering Intern
-
May 2015 - Aug 2015
Projects included making changes to procedures (which also involved performing operator training), upgrading/replacing process equipment, commissioning the startup of a sample panel and taking samples, and redesigning a vent system. All of these projects allowed me to become very familiar with the MOC process. Smaller projects included evaluating heat exchanger equations and updating unit SOC's and alarm points. Through this experience I have learned much about the manufacturing of ethylbenzene and styrene monomer. Show less
-
-
-
LyondellBasell
-
United States
-
Chemical Manufacturing
-
700 & Above Employee
-
Process Engineering Co-op
-
Aug 2014 - Jan 2015
Worked with the Sulfur Recovery Complex in a refinery. Projects included updating amine rich loading inferentials, creating tools to better understand unit rich loading, determine how much amine is discarded and a solution to recapture it, and creating a tool to monitor sour water and NESHAP water generated in refinery. During my time here I was involved with turnaround, and inspecting various equipment. Through this experience I learned much about the sulfur recovery process and amine treating, as well as curde oil refining in general. Show less
-
-
-
Syngenta
-
Switzerland
-
Farming
-
700 & Above Employee
-
HSSE Intern
-
May 2014 - Aug 2014
Worked on updating potable water program for water sampling as required by TCEQ regulations, Created a site-wide map for all Satellite Accumulation Areas to improve current program for documenting them. Updated inventory of all confined spaces in plant to satisfy regulatory requirements. Learned about waste management for Class 1, Class 2, and Hazardous materials; also learned about DOT regulations. Worked on updating potable water program for water sampling as required by TCEQ regulations, Created a site-wide map for all Satellite Accumulation Areas to improve current program for documenting them. Updated inventory of all confined spaces in plant to satisfy regulatory requirements. Learned about waste management for Class 1, Class 2, and Hazardous materials; also learned about DOT regulations.
-
-
-
University of Houston
-
United States
-
Higher Education
-
700 & Above Employee
-
Student Staff Member
-
Jul 2012 - Jun 2013
-
-
Education
-
University of Houston
Master of Business Administration - MBA -
University of Houston
B.S. Chemical Engineering, Minors: Chemistry and Energy & Sustainability
Community
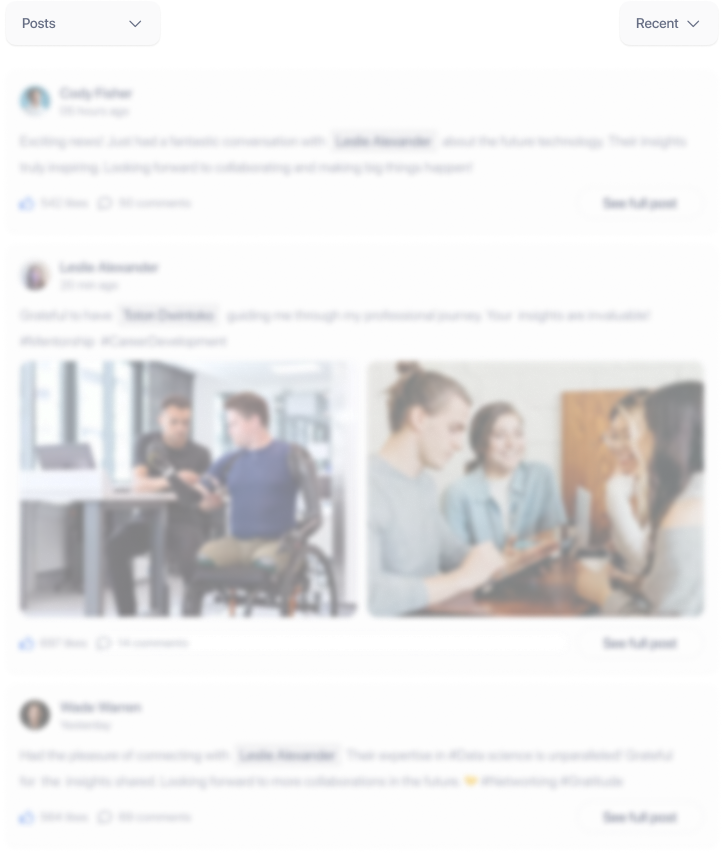