Daniel Lienemann
Supply Chain Manager at LB Foster- Claim this Profile
Click to upgrade to our gold package
for the full feature experience.
Topline Score
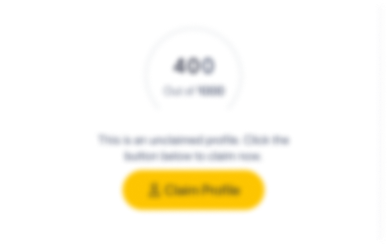
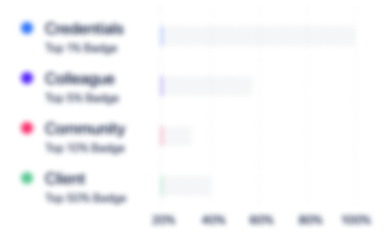
Bio


Experience
-
LB Foster
-
United States
-
Transportation Equipment Manufacturing
-
200 - 300 Employee
-
Supply Chain Manager
-
Feb 2023 - Present
-
-
-
Seegrid
-
United States
-
Automation Machinery Manufacturing
-
100 - 200 Employee
-
Senior Supply Chain Specialist
-
Feb 2022 - Feb 2023
• Primary point of contact for all procurement and supply chain activity since restructuring of company• Project ownership for the material sourcing for new product lines• Analyze new quotations in order to identify price saving opportunities and to solve the increasing amount of component issues that are affecting lead times.• Maintain visibility of the pipeline of work by suppliers in order to ensure that new development is executed in a timely manner• Evaluates current and prospective suppliers through supplier reviews, site visits, and audits, in coordination with Supplier Quality teams, to assure supply capabilities, on-time delivery, quality, and service. • Managed the re-sourcing of materials from multiple underperforming suppliers. Show less
-
-
Supply Chain Specialist
-
Jan 2017 - Feb 2023
• Generate and manage purchase orders in accordance with MRP• Maintain strong working relationships with our suppliers to achieve supplier quality, delivery, capacity and cost performance objectives• Work closely with manufacturing to prioritize and expedite purchase orders based on material needs• Maintain, and monitor the item master, bill of materials, part maintenance, work orders, and planning data to ensure the ERP/MRP system is effectively planning future requirements• Lead of cycle count program, communicate any inventory issues across departments including Manufacturing, Quality, and Finance• Participate in ECN activities internally and externally• Coordinate the return of rejected materials to suppliers in conjunction with Quality• Resolve invoicing issues with Accounting department• Resolve problem shipments with suppliers; receiving issues, packaging standards Show less
-
-
-
GE Power Conversion
-
France
-
Electric Power Transmission, Control, and Distribution
-
700 & Above Employee
-
Shipping & Receiving Lead/Warehouse Specialist
-
May 2011 - Dec 2016
• Team Leader for various groups in shipping, receiving, warehouse, and inventory that range from 2 to 10 employees each. • Interviewed and hired new employees in a group that grew from 5 to 30 employees. • Provide leadership to employees engaged in shipping / receiving / material handling and directing daily priorities ensuring on time delivery for internal and external customer orders. • Responsible for regional offsite warehousing facilities. Developed and maintained relationships with multiple offsite warehousing facilities (30,000 and 50,000 square feet each). Coordinated all logistics throughout the facilities and maintained inventory accuracy. • Executes continuous improvement of warehousing areas to ensure fast and accurate flow. • Ensure the team is performing proper SAP transactions that are executed throughout the process in a timely manner to drive inventory integrity. • Participates in cycle count program, physical inventories, and inventory reconciliation to meet overall inventory accuracy goals. • Ensures the accuracy and condition of all incoming and outgoing items and reconciles errors with purchasing, accounts payable, and vendors. • Provide direction to Project Management, Mangers, Sales, Services and Group Leads on customer shipments and incoming material for production and future shipments. Primary contact for customer service regarding special requests and order status. • Determine the method of shipment, utilizing knowledge of shipping procedures, routes and rates. • Works with the quality team to create non-conforming reports and determine course of action for material in question. • Processed return material authorization shipments. • Key member of a continuous risk assessment team. Team proactively examined processes to determine where risk exists. New and safer processes were then created and documented for shop use. • Active member of Kaizen and continuous process teams. Show less
-
-
-
Westinghouse Air Brake Tech
-
United States
-
Appliances, Electrical, and Electronics Manufacturing
-
1 - 100 Employee
-
Storeroom Manager
-
Aug 2005 - May 2011
• Received incoming material and entered data into Oracle. • Transferred parts to and from warehousing areas. • Processed domestic shipments via supplied carriers. • Pulled and delivered material for production lines. • Maintained transactions to ensure accurate inventory. • Performed daily cycle count and reconciliation. • Assembled raw component kits and shipped to vendors for assembly. • Operated various fork lifts. • Worked with the production planners, customer service, and the plant manager to ensure that our supply flow activities were properly executed. Show less
-
-
Education
-
Point Park University
Bachelor of Science (BS), Accounting -
Westmoreland County Community College
Associate of Science (AS), E-Commerce/Electronic Commerce
Community
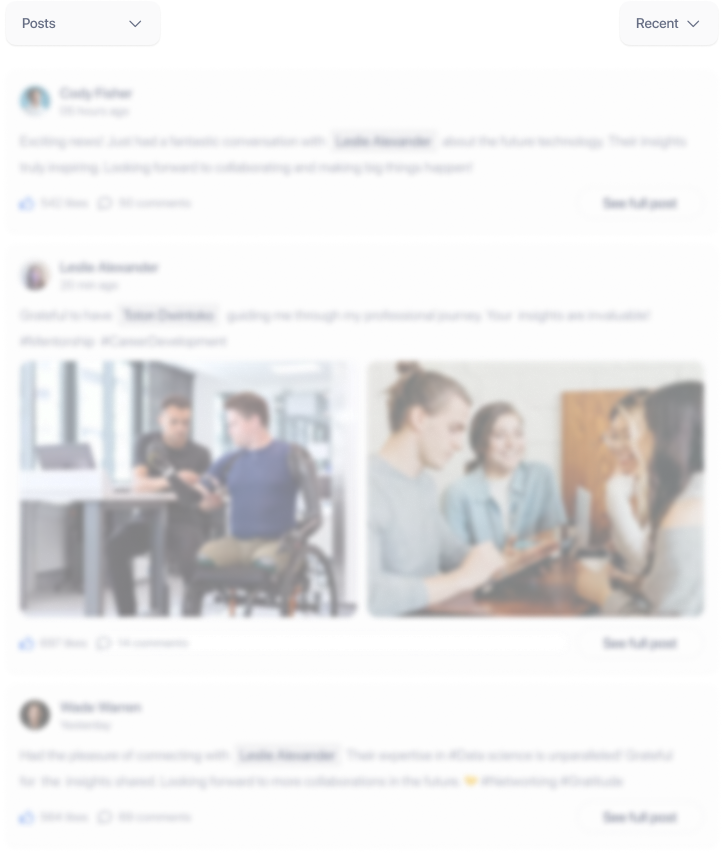