Daniel Crammer
Vice President Operations at CUSTOM LABEL & DECAL, LLC- Claim this Profile
Click to upgrade to our gold package
for the full feature experience.
-
Spanish Professional working proficiency
Topline Score
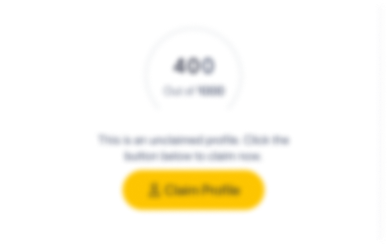
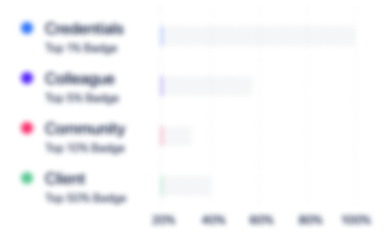
Bio


Credentials
-
FIRST - Level 3 Implementation Specialist
Flexographic Technical AssociationAug, 2011- Oct, 2024 -
GMP Food Safety Certification
Assurance - SAI GlobalMay, 2017- Oct, 2024 -
FIRST Company Certification
Flexographic Technical AssociationAug, 2011- Oct, 2024
Experience
-
-
Vice President Operations
-
Nov 2018 - Present
-
-
-
Best Label Company, Inc.
-
United States
-
Printing Services
-
1 - 100 Employee
-
Production Manager
-
Dec 2007 - Nov 2018
As the Production Manager it is my responsibility to our company and customers to ensure that a high quality product is consistently produced in an efficient and effective manner. It's my duty to provide a safe and healthy work environment to all of our employees. I am responsible for setting financial and efficiency goals for each department within our production facility and for maintaining those goals through the supervisors that oversee each department. I provide support and guidance to all employees and supervisors and hold them accountable for meeting company goals. I am consistently working on continual improvement opportunities and working towards keeping our company at the cutting edge within our industry. Show less
-
-
Assistant Plant Manager
-
Jun 2009 - Sep 2011
As the Assistant Plant Manager my responsibilities included purchasing, job planning, estimating, scheduling, expediting, special projects, & Task Coordinator. Job planning consisted of:-Facilitating meetings with Sales, Customers, & Pre-Press-Reviewing jobs & how to best prepare them so they were setup to be produced efficiently-Identifying current problems & foreseeing future issues-Creating new ideas & resolutions that would remedy problemsEstimating entailed:-Analyzing the difficulty of a job, the equipment it was to be produced on, & the type of materials needed-Allocating the correct type & quantity of materialWhile dealing with the purchasing aspects of the job:-I qualified new & existing vendors-I negotiated deals & contracts with vendors-I negotiated pricing-I researched new & alternative materials to keep costs effective-I reviewed, approved, placed purchase orders-I dealt with expediting materials & handling the on-time arrival of goods-I dealt with processing returns of rejected goodsIn order to perform the duties of scheduling and expediting:-I assessed all machines & their capabilities-I reviewed all jobs & estimated the amount of time needed to perform the job-I created schedules for each machine-I managed customer service & sales requests for customer deadlines & adjusted the schedule accordinglyI was placed in charge of all Special Projects which required me to:-Review customer requirements & needs, then create new workflows or revise SOP's to manage their needs-Research manufacturing processes that would help increase our efficiency-Manage new & current high-profile accounts that required special needsAs the Task Coordinator:-I held daily meetings with the Plant Manager to review deadlines-I delegated work to each department supervisor-Created ongoing tasks to help the continual improvement of our companies workflow-Analyzed results of production when changes in the workflow were made Show less
-
-
Materials Control Supervisor / Shipping and JIT Inventory(High Profile Accounts)
-
Dec 2007 - Jun 2009
I began my career at Best Label by wearing many "hats". I controlled the receiving of all incoming materials. I supplied materials to all operators based on analyzing their needs compared to the work that was supplied to their machines. I assisted operators in their daily operations and setting up their machines. I reviewed the operators daily schedules and supplied the tools that the operators needed in order to perform their tasks. I took over the management of on-site inventories that we kept for high profile customers. I performed all the shipping functions that were needed in order to supply our high-profile customers with their specialized needs. This gave me the opportunity to learn about all of the basic operating procedures that are were performed within our company. Show less
-
-
Education
-
California State University Long Beach, College of Engineering
Construction Engineering Management, Construction Engineering, Construction Management -
Valley Christian High School
Community
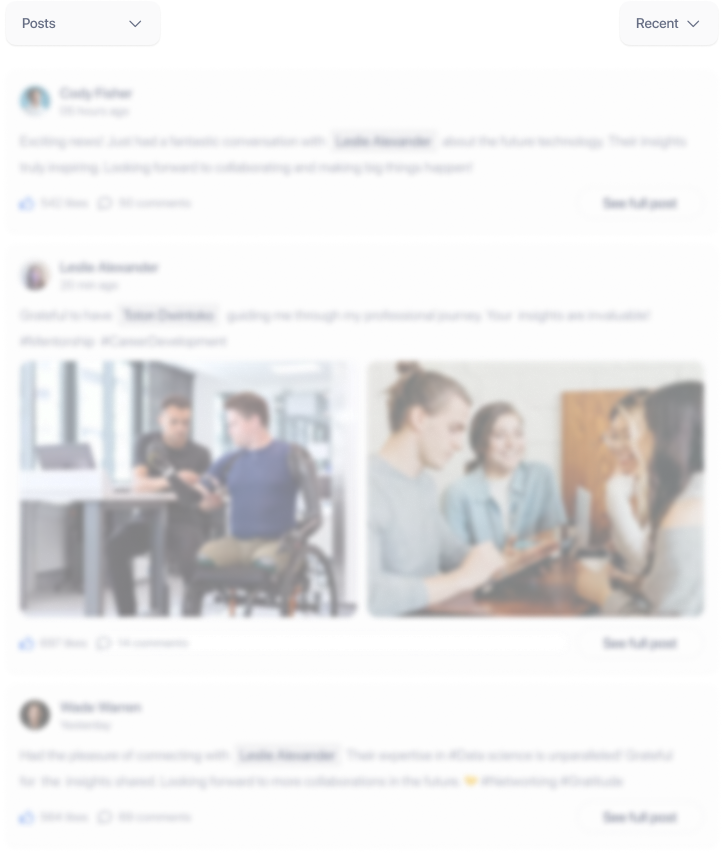