Dan Wheeler
Customer Quality Engineer at Kionix, Inc.- Claim this Profile
Click to upgrade to our gold package
for the full feature experience.
Topline Score
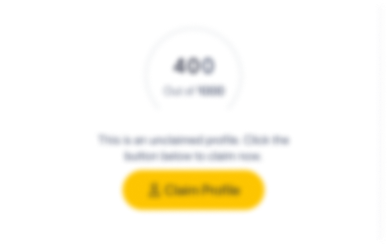
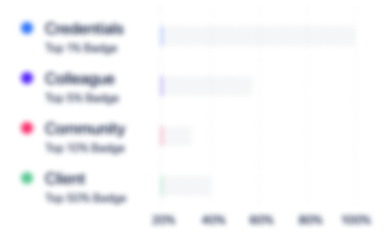
Bio


Experience
-
Kionix, Inc.
-
United States
-
Appliances, Electrical, and Electronics Manufacturing
-
1 - 100 Employee
-
Customer Quality Engineer
-
Apr 2009 - Present
o Primary customer contact for entire customer base (Consumer & Automotive).o Issue, review and approve all customer RMAs (Return material authorizations).o Team Champion on all 8D problem solving reports.o Team member for failure analysis of returned suspect components.o Lead member of team to develop customer return database and automated report generation system.o Internal auditor for TS16949 & ISO9001 o Primary customer contact for entire customer base (Consumer & Automotive).o Issue, review and approve all customer RMAs (Return material authorizations).o Team Champion on all 8D problem solving reports.o Team member for failure analysis of returned suspect components.o Lead member of team to develop customer return database and automated report generation system.o Internal auditor for TS16949 & ISO9001
-
-
-
Borg Warner Automotive
-
France
-
Restaurants
-
Metallurgical Lab. Supervisor
-
2005 - 2009
o Scheduled, monitored and developed all Metallurgical Technicians (7 Techs)o Identified and purchased lab equipment and supplies.o Developed and documented new process testing procedures. To include contamination analysis, defective component NDT (Non-destructive testing) analysis, Microstructure sample analysis & raw material incoming inspection.o Reviewed metallurgical & testing reports and communicated results to end customer(s). o Scheduled, monitored and developed all Metallurgical Technicians (7 Techs)o Identified and purchased lab equipment and supplies.o Developed and documented new process testing procedures. To include contamination analysis, defective component NDT (Non-destructive testing) analysis, Microstructure sample analysis & raw material incoming inspection.o Reviewed metallurgical & testing reports and communicated results to end customer(s).
-
-
-
BorgWarner Morse TEC
-
India
-
Automotive
-
1 - 100 Employee
-
Quality Control Supervisor
-
1999 - 2009
o Managed supplier quality & development of all raw material suppliers.o Issued and reviewed all SCARS.o Completed supplier on-site assessments and monitored suppliers for on-going performance.o Reviewed and issued disposition for Supplier PPAP submissions (Strip Steel and Wire)o Member of TC MRB.o Member of TC scrap reduction committee (press room and supplier).o Scheduled all sort area operators and monitored performance.o Performed set-up on Vision and Eddy-current sorting equipment, verified rejected components and reported results upon completion to production and quality.o Identified and purchased sort/inspection equipment.
-
-
Quality Technician - Customer Support
-
1994 - 1999
o Primary quality technical support for Ford, General Motors, After Market and other customer accounts/plants.o Facilitated and or performed root cause analysis and corrective action reports for customer rejected components. Presented root cause analysis and actions implemented onsite at customer locations.o Performed warranty analysis (Ford AWS).o Performed customer onsite containment and managed contract quality support.o Launch technical and quality support for new product kick-offs at customer locations.
-
-
Community
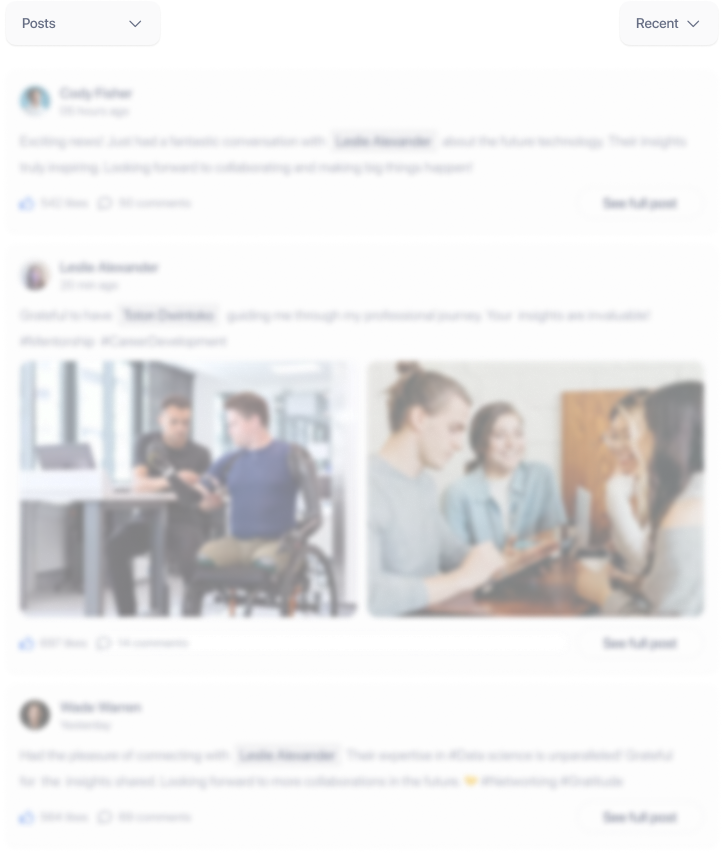