Dan Ramsden
PSIM Mechanical Integrity Engineer at INEOS Olefins & Polymers USA, LLC- Claim this Profile
Click to upgrade to our gold package
for the full feature experience.
-
English Native or bilingual proficiency
Topline Score
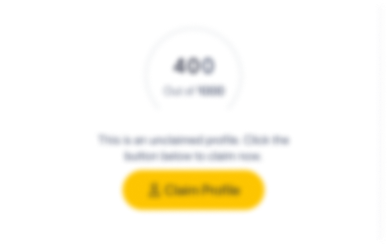
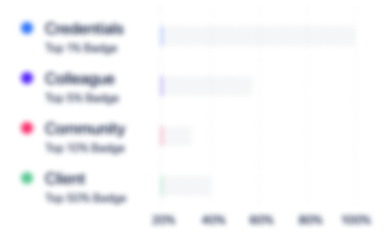
Bio


Credentials
-
Engineer Intern (EIT)
Indiana State Board of Registration for Professional EngineersMay, 2013- Oct, 2024 -
Advanced Process Safety Management Compliance Auditing
Cognascents Consulting Group -
Layer of Protection (LOPA) Analysis
ABS Group -
Process Hazard Analysis Leader (PHA)
ABS Group -
Root Cause Analysis (RCA), Incident Investigation and Advanced RCA
ABS Group -
Safety Integrity Level (SIL)
ABS Group
Experience
-
INEOS Olefins & Polymers USA, LLC
-
United States
-
Chemical Manufacturing
-
1 - 100 Employee
-
PSIM Mechanical Integrity Engineer
-
Apr 2020 - Present
•As a Senior Consulting Engineer I provided process safety and mechanical integrity leadership and technical support to INEOS O&P’s five manufacturing sites which includes polymer units, crackers and olefins units, storage caverns and NGL fractionation. •Developed and implemented new PHA/LOPA risk assessment criteria/methodologies for challenging topics such as metal alkyls (TEAl), organic peroxides, hydrocarbon storage caverns, and butadiene popcorn polymer •Lead Project and Compliance PHA’s as a trained PHA/LOPA leader and provided guidance on complex topics such as fired heater and flare systems, brittle fracture, equipment overpressure, reactive chemistry, and rotating equipment hazards •Created a novel risk assessment methodology for butadiene (BD) purification and storage to ensure best practices in prevention and mitigation of BD reactive monomer hazards. Facilitated assessments with operations and engineering teams and associated action items were presented to and accepted by site leadership. •Provided technical reviews for various corporate and site PSIM initiatives •Lead a team of leaders, operations representatives and engineers to optimize and resolve safety critical equipment PM’s to reduce backlog of overdue PM’s due to technical challenges, impracticable PM’s plans, and inaccurate PHA/LOPA scenarios •Lead and/or supported significant process safety incident investigations •Supported a ~$1bn olefins unit expansion project by tracking, reviewing and driving resolution/alternative means of closure for the ~322 PHA/LOPA action items including a risked based prioritization of open action items needing closure to allow for startup •Lead Mechanical Integrity Auditor for PSM/RMP compliance audits at all sites, networking with 3rd parties to find and resolve issues, reworded previous actions into practical actionable AI's and working with MI site stakeholders from technicians to inspectors to engineering authorities to ensure AI resolution Show less
-
-
-
Dow
-
United States
-
Chemical Manufacturing
-
700 & Above Employee
-
Senior Production Engineer
-
Aug 2018 - Apr 2020
• Provided operational/process support while ensuring safety and environmental compliance for continuous world scale anhydrous hydrogen cyanide (HCN) production units • Qualified as HCN control operator and operated plant for ~ 2 months during union contract negotiations • Improved operating discipline and optimized advanced process control parameters to achieve new daily, weekly, monthly and annual production records for assigned units • Trained and qualified operators on process technology, procedures, plant operation, and critical process safety parameters for HCN process • Managed ~$5 million in catalyst inventory, coordinated and supervised catalyst change outs, and determined replacement schedule based on yields/performance for 6 HCN production reactors Show less
-
-
-
INEOS Bio
-
League City, Texas
-
Process Engineer
-
Oct 2014 - Aug 2018
Plant Engineering and Projects • Led Six Sigma Green Belt project to prevent fouling heat exchangers with a estimated cost benefit of $1.75 million • Significantly improved the reliability of the plant flare system, nitrogen system and reverse osmosis water systems which eliminated costly plants shutdowns • Created and analyzed plant capital and operating cost estimates, design packages, equipment specifications, PFD’s, SOP’s, commission documentation and risk assessments for assigned projects and process changes • Performed mass and energy balance calculations and process modeling with ASPEN for process and equipment design, optimization and troubleshooting • Routinely led cross-functional teams of operators, engineers, maintenance, and research personnel to solve plant operational and safety issues • Mentored recent engineering graduates, interns and other site engineers Site Basis of Safety Engineer • Reviewed and approved site Management of Change documentation to ensure compliance with corporate process safety requirements and industry best practices • Performed Risk Assessments for process and equipment changes, operating condition changes, safety system bypasses and plant trials • Led Process Safety Hazard Analysis (PHA) using various methodologies including HAZOP, LOPA and What-If analysis • Led incident and equipment failure investigations to determine root cause and develop preventative and corrective actions using various methods such as causal factor charting, 5-whys, and fault tree analysis Show less
-
-
-
Eli Lilly and Company
-
United States
-
Pharmaceutical Manufacturing
-
700 & Above Employee
-
Process Engineer
-
Jan 2012 - Sep 2014
Expansion Project / Process Shutdown and Startup • A Technical Lead and Start-up Engineer for a $92 million insulin API process expansion project that safely managed the activities of operations, quality, engineering, technical services, crafts while executing construction, maintenance cleaning and startup activities • Developed in-depth process simulation models to support process design and determined initial conditions for startup of new and upgraded process steps • Worked with design and construction firms to develop detailed design for new/improved unit operations • Created, executed and approved commissioning and qualification documentation such as IQ,OQ,SQ and PQ • Created, executed and approved equipment changeover protocols, idling/startup procedures • Supported shutdown and changeover activities as lead engineer on shift • Supported Plant Shutdown/Startup as a Lead Engineer Process Support • Supported 3 insulin API manufacturing processes which included troubleshooting process equipment, instrumentation, process control loops, control systems for the implementation of new technologies in a cGMP environment • Used statistical modeling tools and historical process data to monitor, troubleshoot and improve insulin manufacturing processes identify sources of variability, deviations and to determine state of process control • Led RCA investigations and implemented recommendations for process events and safety incidents • Performed mass and energy balances on reactors, microfiltration units, ultrafiltration units, ion exchange chromatography columns, enzymatic reaction columns, heat exchangers, pumps and other process equipment • Created, reviewed and approved technical documents such as P&IDs, equipment procedures, PFD’s, and SOP’s • Authored management of change documentation for small and large projects Show less
-
-
-
Georgia Institute of Technology
-
Atlanta, GA
-
Undergraduate Researcher
-
Aug 2010 - Aug 2011
● Investigated the use of catalysis to degrade lignin into constituent components for use as a biofuel ● Developed, synthesized and characterized heterogeneous catalysts and substrates ● Analyzed degraded lignin compounds ● Operated, calibrated, diagnosed, and repaired analytical equipment ● Investigated the use of catalysis to degrade lignin into constituent components for use as a biofuel ● Developed, synthesized and characterized heterogeneous catalysts and substrates ● Analyzed degraded lignin compounds ● Operated, calibrated, diagnosed, and repaired analytical equipment
-
-
-
Symrise AG
-
Germany
-
Food and Beverage Manufacturing
-
700 & Above Employee
-
Process Engineer Intern
-
Jun 2010 - Aug 2010
• Determined relief scenarios and sized a relief valve for a reactor and heat exchangers • Performed mass and energy balances on reactors, distillation columns, crystallizers, centrifuges, and hydroclones • Determined areas experiencing product losses/inefficiencies and recommended process improvements • Fitted physical data to equations in ChemCad for use in process simulation • Determined relief scenarios and sized a relief valve for a reactor and heat exchangers • Performed mass and energy balances on reactors, distillation columns, crystallizers, centrifuges, and hydroclones • Determined areas experiencing product losses/inefficiencies and recommended process improvements • Fitted physical data to equations in ChemCad for use in process simulation
-
-
Education
-
Georgia Institute of Technology
Bachelor of Science (B.S.), Chemical and Biomolecular Engineering
Community
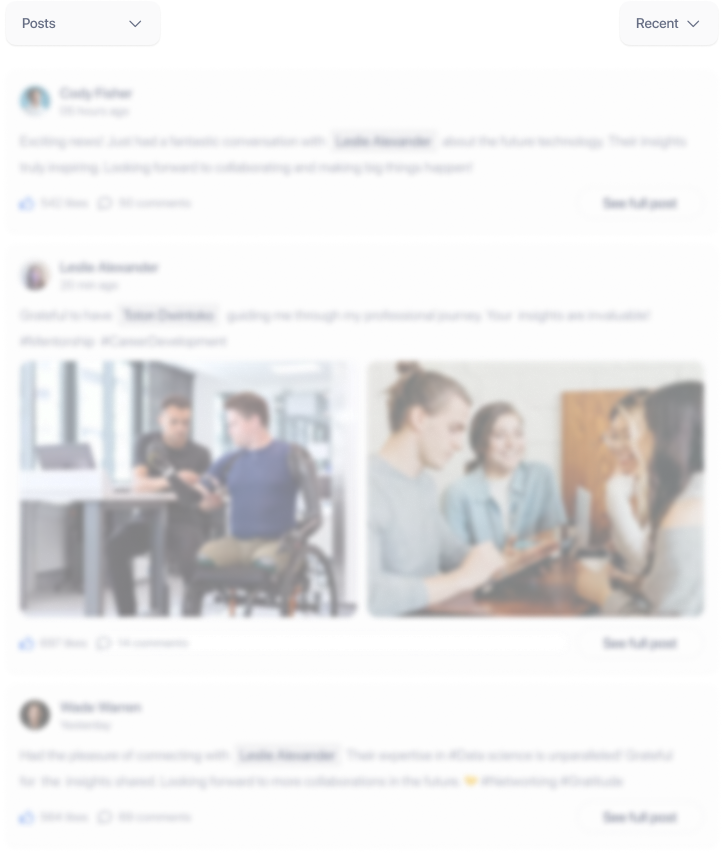