Dan Pearson CSM
Director of Repair Operation at Fortress Solutions (formerly Restor Telecom, Inc.)- Claim this Profile
Click to upgrade to our gold package
for the full feature experience.
Topline Score
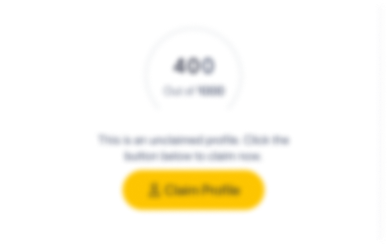
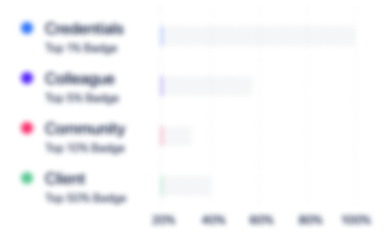
Bio


Experience
-
Fortress Solutions (formerly Restor Telecom, Inc.)
-
United States
-
Telecommunications
-
1 - 100 Employee
-
Director of Repair Operation
-
Mar 2017 - Present
Oversee repair operation of 39 Technicians and 7 Engineers. Evaluate workload and assign work to specific teams. Create processes and procedures to process the workload in the most efficient manner. Evaluate KPI's and throughput, making sure customer equipment is repaired in a timely manner. Oversee repair operation of 39 Technicians and 7 Engineers. Evaluate workload and assign work to specific teams. Create processes and procedures to process the workload in the most efficient manner. Evaluate KPI's and throughput, making sure customer equipment is repaired in a timely manner.
-
-
-
-
Manager of Operations
-
Mar 2017 - Present
-
-
Technical Engineer
-
Apr 2014 - Mar 2017
2014 – Present Promoted with full responsibility to repair and resolve issues escalated from Technician staff. Business-critical initiatives include training Technicians in new products, researching and developing new products, designing processes, creating test beds and repairing samples to determine common problems and parts. • Member of R2 Planning Committee. Develops processes to obtain R2 certification. • Member of Safety Team. Assigned building to regularly inspect for safety… Show more 2014 – Present Promoted with full responsibility to repair and resolve issues escalated from Technician staff. Business-critical initiatives include training Technicians in new products, researching and developing new products, designing processes, creating test beds and repairing samples to determine common problems and parts. • Member of R2 Planning Committee. Develops processes to obtain R2 certification. • Member of Safety Team. Assigned building to regularly inspect for safety concerns. Collaborates with team members to identify and suggest ways to improve plant safety. • Member of Audit Team. Performs ISO audits. Creates reports and identifies opportunities to improve quality. • Researches replacement parts for defective components. • Creates cost analysis ensuring repairs are viable and profitable. • Trains Technicians in developing and releasing products to operations.
-
-
Technician
-
Mar 2013 - Mar 2014
Performed repairs to component-level telecommunication products including 4TEL, 5ESS, Litespan, Timespan, AFC, DR4, 6, 11, Ciena, Corestream, GTD5, Titan, DMS100, and Symmetricom. • Promoted within 12 months.
-
-
-
Panasonic North America
-
United States
-
Appliances, Electrical, and Electronics Manufacturing
-
700 & Above Employee
-
Technical Supervisor – Assistant Manager
-
Jul 2001 - Mar 2013
Promoted to Technical Supervisor, in charge of production and personnel. Promoted to Lead Technician in charge of starting new business group “National Board Repair Center.” Oversaw staff of 75 of contractors and employees in consumer electronics service center operation. Business-critical initiatives included budgeting, cost management and interviewing and hiring outsourced and full-time employees. Created and presented progress reports, managed budget, researched and developed… Show more Promoted to Technical Supervisor, in charge of production and personnel. Promoted to Lead Technician in charge of starting new business group “National Board Repair Center.” Oversaw staff of 75 of contractors and employees in consumer electronics service center operation. Business-critical initiatives included budgeting, cost management and interviewing and hiring outsourced and full-time employees. Created and presented progress reports, managed budget, researched and developed new products and designed repair procedures ensuring the highest quality. Improved processes, performance and profitability: •Trained Technicians on new products ensuring compliance with ISO standards. •Relocated Service Center from Elgin, IL o Kent WA. Traveled to design layout and interview candidates. Hired and trained new employees. Loaded, moved and setup in new location. Supervised all electric, computer and communication wiring. Monitored operations until service center was fully operational. •Created ISO 9000:2008 and ISO13845 quality manual. Implemented quality processes. •Developed factory plasma panel chargeback process including spreadsheet and techniques on generating pictures of defective plasma panels highlighting type of defect and repairs made. First in the country to develop processes and evaluate equipment to change BGA and CSP IC’s. Worked with Pace International to design and manufacture new rework machine. •Achieved Certified Electronic Technician certification. •Achieved ISO7711 and ISO7721 certification. •Traveled to Osaka, Japan to work with Factory Training Department. Developed process to repair DVD Recorder modules. •Developed process to hire temporary personnel. Utilizing flexible workforce enabled NBRC to expand while keeping costs down. •Improved workflow procedures to meet ever-changing repair demands and workforce changes. •Instituted technical training program improving the onboarding process reducing lost production during technician turnover. Show less Promoted to Technical Supervisor, in charge of production and personnel. Promoted to Lead Technician in charge of starting new business group “National Board Repair Center.” Oversaw staff of 75 of contractors and employees in consumer electronics service center operation. Business-critical initiatives included budgeting, cost management and interviewing and hiring outsourced and full-time employees. Created and presented progress reports, managed budget, researched and developed… Show more Promoted to Technical Supervisor, in charge of production and personnel. Promoted to Lead Technician in charge of starting new business group “National Board Repair Center.” Oversaw staff of 75 of contractors and employees in consumer electronics service center operation. Business-critical initiatives included budgeting, cost management and interviewing and hiring outsourced and full-time employees. Created and presented progress reports, managed budget, researched and developed new products and designed repair procedures ensuring the highest quality. Improved processes, performance and profitability: •Trained Technicians on new products ensuring compliance with ISO standards. •Relocated Service Center from Elgin, IL o Kent WA. Traveled to design layout and interview candidates. Hired and trained new employees. Loaded, moved and setup in new location. Supervised all electric, computer and communication wiring. Monitored operations until service center was fully operational. •Created ISO 9000:2008 and ISO13845 quality manual. Implemented quality processes. •Developed factory plasma panel chargeback process including spreadsheet and techniques on generating pictures of defective plasma panels highlighting type of defect and repairs made. First in the country to develop processes and evaluate equipment to change BGA and CSP IC’s. Worked with Pace International to design and manufacture new rework machine. •Achieved Certified Electronic Technician certification. •Achieved ISO7711 and ISO7721 certification. •Traveled to Osaka, Japan to work with Factory Training Department. Developed process to repair DVD Recorder modules. •Developed process to hire temporary personnel. Utilizing flexible workforce enabled NBRC to expand while keeping costs down. •Improved workflow procedures to meet ever-changing repair demands and workforce changes. •Instituted technical training program improving the onboarding process reducing lost production during technician turnover. Show less
-
-
-
Sony
-
Entertainment Providers
-
700 & Above Employee
-
Bench Technician
-
Jun 1997 - Jun 2000
-
-
Education
-
Rock Valley College
Associates, Arts -
Universal Life Church
Doctor of Divinity, Religious Studies -
Devry University
Associates, Electronic Engineering -
Wright College
Associates, Electronic Engineering
Community
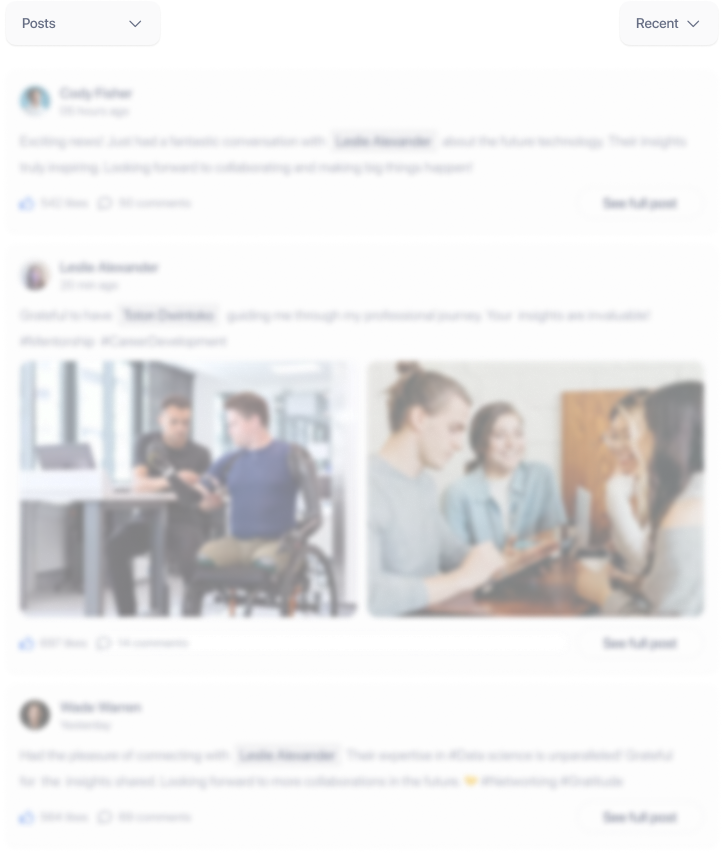