Dan Osterhouse
Design Engineer at WACO Aircraft Corp- Claim this Profile
Click to upgrade to our gold package
for the full feature experience.
Topline Score
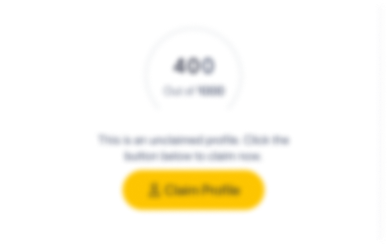
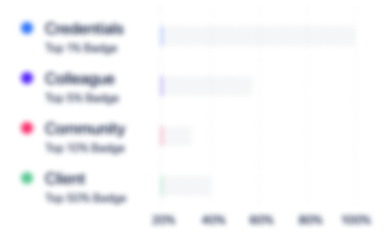
Bio
0
/5.0 / Based on 0 ratingsFilter reviews by:
Experience
-
WACO Aircraft Corp
-
United States
-
Airlines and Aviation
-
1 - 100 Employee
-
Design Engineer
-
Jul 2020 - Present
▪ Design and fully detail aircraft components and assemblies using SolidWorks ▪ Develop Jigs and fixtures to improve production processes. ▪ Collaborate with other team members to improve quality and consistency. ▪ Design and fully detail aircraft components and assemblies using SolidWorks ▪ Develop Jigs and fixtures to improve production processes. ▪ Collaborate with other team members to improve quality and consistency.
-
-
-
Consumers Concrete
-
United States
-
Construction
-
1 - 100 Employee
-
Cement Mixer Truck Driver
-
Jul 2019 - Jul 2020
- Delivering concrete to various job sites in the area. - Driving a six-axle truck with a GVWR of 80,000 pounds. - Delivering concrete to various job sites in the area. - Driving a six-axle truck with a GVWR of 80,000 pounds.
-
-
-
Ralph Moyle, Inc.
-
United States
-
Truck Transportation
-
1 - 100 Employee
-
Regional Truck Driver
-
Nov 2018 - Jul 2019
- Obtained Class A CDL driver’s license - Driving tractor trailer delivering goods to all the Great Lakes Region (MN, WI, IL, IN, MI, OH, PA) Plus Iowa, Missouri, Kentucky, and Tennessee. - Obtained Class A CDL driver’s license - Driving tractor trailer delivering goods to all the Great Lakes Region (MN, WI, IL, IN, MI, OH, PA) Plus Iowa, Missouri, Kentucky, and Tennessee.
-
-
-
-
Tool Designer
-
May 2018 - Jul 2018
- Visi CAD training to design large injection molds for the automotive industry. - Design large injection molds for the automotive industry. - Visi CAD training to design large injection molds for the automotive industry. - Design large injection molds for the automotive industry.
-
-
-
Michigan Tool Works
-
United States
-
Machinery Manufacturing
-
Program Manager
-
Nov 2017 - May 2018
- Create and maintain progress reports for fifteen to twenty tools for six different customers. - Hold design review meetings both internally and with customer to achieve best tool designs. - Order mold components, steel and graphite. - Review inspection reports for tool tuning. Create PowerPoint files for customers approval showing how we can change the tool to bring the part to print. - Create and maintain progress reports for fifteen to twenty tools for six different customers. - Hold design review meetings both internally and with customer to achieve best tool designs. - Order mold components, steel and graphite. - Review inspection reports for tool tuning. Create PowerPoint files for customers approval showing how we can change the tool to bring the part to print.
-
-
-
-
Designer
-
Feb 2017 - Nov 2017
▪ Review and approve tooling models for production tooling. Incorporate appropriate draft and add steel safe conditions if necessary. ▪ Support program managers by troubleshooting components for customer approval. ▪ Review and revise injection molds per customer requests. ▪ Design fixtures for CMM, pad printing, etc. ▪ Run SolidWorks Plastics to verify best gating position to minimize warp and optimize weld lines, gas traps and ease of fill. ▪ Review and approve tooling models for production tooling. Incorporate appropriate draft and add steel safe conditions if necessary. ▪ Support program managers by troubleshooting components for customer approval. ▪ Review and revise injection molds per customer requests. ▪ Design fixtures for CMM, pad printing, etc. ▪ Run SolidWorks Plastics to verify best gating position to minimize warp and optimize weld lines, gas traps and ease of fill.
-
-
-
Concept Molds
-
United States
-
Plastics Manufacturing
-
1 - 100 Employee
-
Tool Designer
-
Mar 2015 - Jan 2017
- Design injection molds for optimum cavitation, gating and cooling to achieve the best molding process. Splitting the tool for manufacturability. Detailed components per customer requirements and pulled electrodes for EDM. - Design injection molds for optimum cavitation, gating and cooling to achieve the best molding process. Splitting the tool for manufacturability. Detailed components per customer requirements and pulled electrodes for EDM.
-
-
-
Mol-Son, LLC
-
United States
-
Product / Tool Designer
-
Jun 1985 - Mar 2015
- Led a group of design engineers to give direction and prioritize design projects. - Developed product design concepts with design parameters as determined by sales. - Created concept drawings for MS Power Point presentations for customer design reviews. - Collaborated with both Tool and Product design engineers to optimize the DFM to improve cost, quality and delivery. - Used Pro/Engineer Mechanica to perform finite element analysis ensuring the strength and durability of the design. - Performed simulated mold flow analysis using Mold-flow MPI (Pro-E plastic advisor) to increase the capability and efficiency of the molding process, providing a higher quality part. - Redesigned existing components to reduce cost by using one or a combination of the following: Recommend using a less expensive material, optimizing the design to remove unneeded material, complete redesign or the addition of material to increase the capability of the molding process. - Performed simulated mold flow analysis using Mold-flow MPI (Pro-E plastic advisor) to increase the capability and efficiency of the molding process, providing a higher quality part. - Developed fully detailed component drawings that meet ISO standards including GD&T. - Designed mold layouts for optimum cavitation, gating and cooling to optimize the molding process. -- Splitting the tool for manufacturability. Detailing components per customer requirements.
-
-
Education
-
ITT Technical Institute
Associate's degree, Tool Engineering Technology
Community
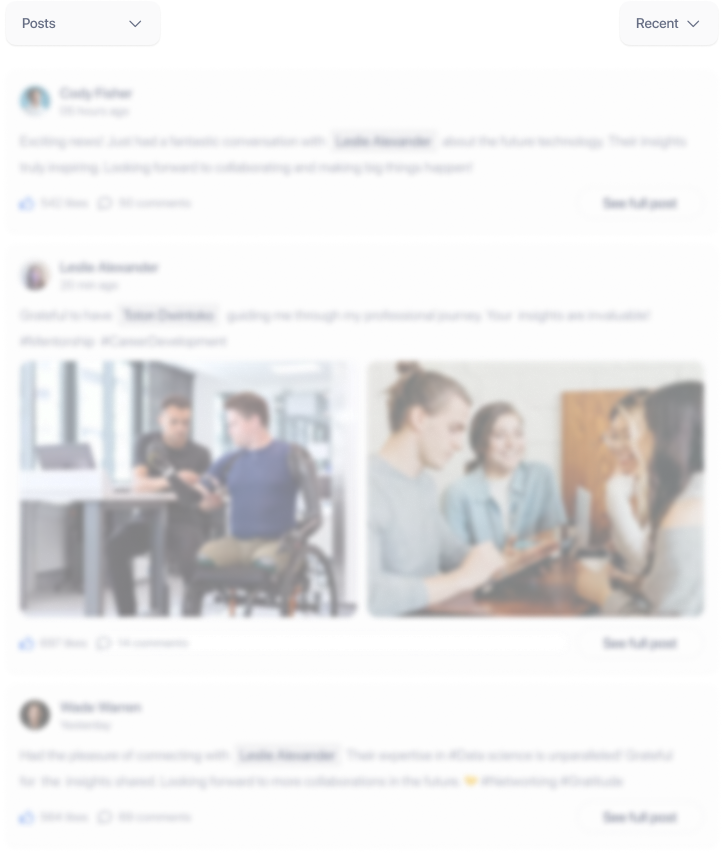