Dan Monahan
Operations Manager at R & D Engineering- Claim this Profile
Click to upgrade to our gold package
for the full feature experience.
Topline Score
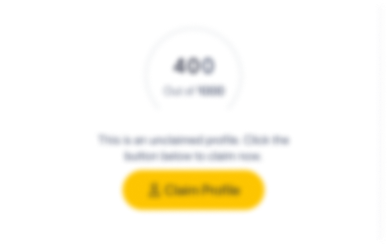
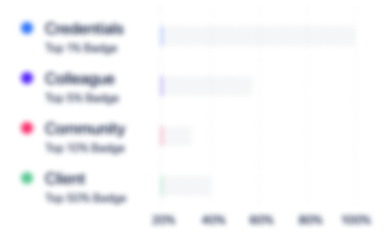
Bio
0
/5.0 / Based on 0 ratingsFilter reviews by:
Credentials
-
Lean Six Sigma Green Belt
New Horizons Computer Learning CentersMay, 2015- Sep, 2024 -
Project Management
University of Minnesota-Twin CitiesJun, 2012- Sep, 2024
Experience
-
R & D Engineering
-
Industrial Machinery Manufacturing
-
1 - 100 Employee
-
Operations Manager
-
Mar 2021 - Present
-
-
-
RevSpring
-
United States
-
Information Technology & Services
-
400 - 500 Employee
-
Operations Manager
-
Jun 2017 - Mar 2021
As Operations Manager at RevSpring I was entrusted for the quality of work of 23 indirect reports and 3 direct reports in a 24/5 manufacturing facility. I managed all operational aspects of the business for RevSpring in Minnesota. This included managing people, safety, quality, on-time delivery, cost and the overall performance of people and machines. I managed the facility, including grounds, janitorial and service agreements for all maintenance and repair of the building and equipment. I was directly involved in recruiting, hiring, and onboarding staff, and if the situation demands, firing as well.Key achievements:• Increased on-time delivery to over 99% in 2019 & 2020• Reduced spoilage & rework and negotiated pricing to save over $20,000 annually on paper• Successfully installed numerous pieces of equipment and changed the floor plan to a 5S model to make the shop more efficient
-
-
-
Streamworks
-
Denmark
-
Information Technology & Services
-
Planner/Scheduler
-
Oct 2015 - Jun 2017
At Streamworks, I led the planning function for custom manufacturing projects and scheduled all work, serving as the information liaison between the sales and production teams. I facilitated cross-functional daily meetings of 20+ staff, including account managers, sales, and department leaders, to set, meet and accelerate organizational goals.Key achievement:• Developed a multi-shift scheduling and plant capacity system, resulting in on-time delivery going from 89% to 98.8%.
-
-
-
ASAP, Inc
-
United States
-
Printing Services
-
1 - 100 Employee
-
Production Manager
-
Jun 2013 - Mar 2015
I supervised 17 employees in a custom manufacturing plant. I helped plan and scheduled jobs and work assignments. I managed the performance of people and machines, handled maintenance and repairs, purchased supplies and consumables and managed inventory. I conducted daily cross-functional production meetings and enforced policies and procedures. I oversaw hiring, employee development, performance evaluations, and administered corrective actions.Key achievements:• Developed SOPs to reduce variables and implemented a machine maintenance program
-
-
-
-
Operations Supervisor
-
May 2012 - Jun 2013
I supervised 24 employees across a large 60-acre facility with a dozen outbuildings and traffic of up to 300 semi-trucks each day. I directed union staff in an intense Safety, Quality, and Environmental culture in a highly regulated industry. I administered union labor agreement and company policies, cross-training and on-the-job equipment certifications, weekly safety training, incident reporting, root cause analysis, and project management. I was accountable for inventory, hiring, safety, assigning work, quality, and regulatory compliance. I conducted daily safety huddles and directed traffic while supervising people from a pickup truck utilizing two-way radios. Working with the railroad was a big learning experience as they were often several days late bringing products. To work around this, I enrolled in the Union Pacific web site to monitor product locations and traffic and visited the train station to meet the operators. I familiarized myself with the engineers and railroad safety regulations within a short period of time and reduced the supply chain backlog of railcars.
-
-
-
Airgas
-
Argentina
-
Retail
-
1 - 100 Employee
-
Facility Manager
-
2010 - 2011
Directed plant-wide production of medical gases, customer service and distribution in a highly regulated industry (FDA, DOT). Managed customer service, production, inventory, logistics and delivery fleet personnel. Directed the safety program, ISO 9001 quality, DOT and FDA regulatory compliance, purchasing, Kaizen projects and the maintenance of equipment, fleet and facilities.• Fostered the relationship with Fairview Hospitals & Clinics, resulting in a new 5-year contract• Implemented Lean and 5S, achieving a 34% reduction in overtime• In one year, exceeded the EBITDA goal at this branch for the first time since 2007
-
-
-
Wallace Carlson Printing
-
United States
-
Printing Services
-
1 - 100 Employee
-
Plant Manager
-
Feb 2008 - May 2010
Directed plant-wide operations, leading 4 department managers and 37 team members. Accountable for strategic direction, procurement, inventory, safety, quality, on-time delivery, 24/5 project scheduling, purchasing, budgets and administering policies and procedures.• Led organizational change to culture via safety, SOPs, quality process and service delivery.• Facilitated daily production meetings with sales, customer service and department managers.• Designed the safety program: ERTK, LOTO and forklift trainings, led the safety team.• Developed green certification program compliant with the Forest Stewardship Council.• Implemented Lean Six Sigma methodologies to improve quality and reduce waste.
-
-
-
Travel Tags
-
United States
-
Printing Services
-
1 - 100 Employee
-
Production Supervisor
-
2005 - 2008
Supervised a staff of 24 across four departments in an ISO 9001 manufacturing environment. Ensured safety, productivity and quality across four departments in a state-of-the art, 140,000 square-foot facility. Performed hiring, employee training and performance management.• Directed work assignments and signed approvals on production runs.• Implemented Lean principles and led multiple Kaizen events.• Developed an employee performance measurement chart and a shift productivity scorecard.• Facilitated team trainings in Lean, safety, diversity, AIB and ISO 9001 quality.
-
-
Education
-
Metropolitan State University
Bachelor’s Degree, Business Administration -
Normandale Community College
BS, Business Administration & Management
Community
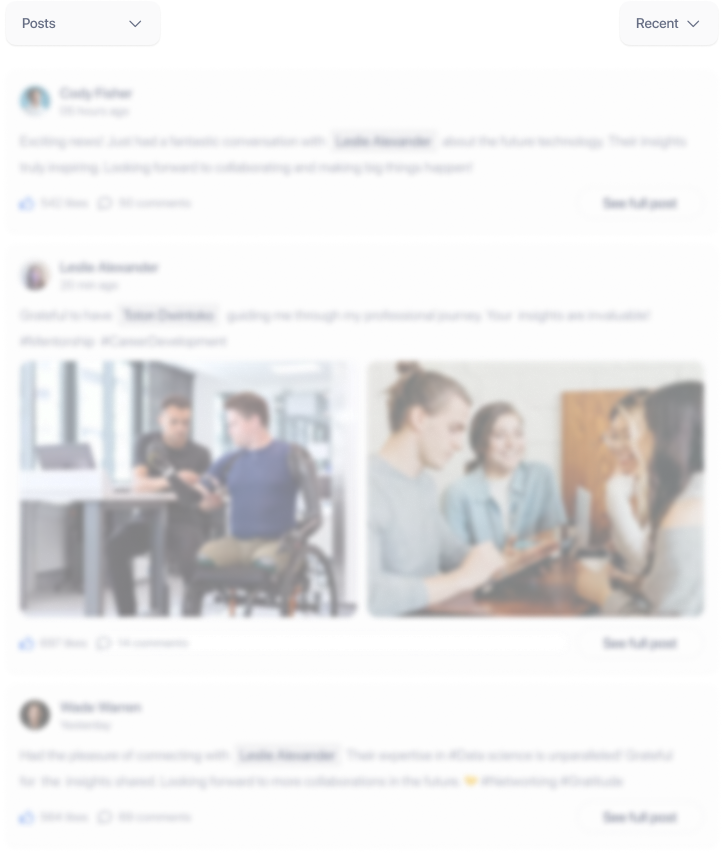