Damian Pogson
EMEA Service Centre Engineer at Juniper Systems- Claim this Profile
Click to upgrade to our gold package
for the full feature experience.
Topline Score
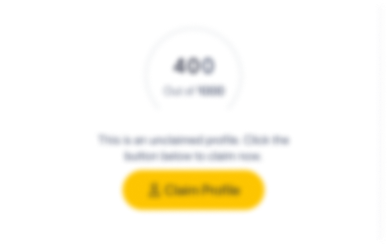
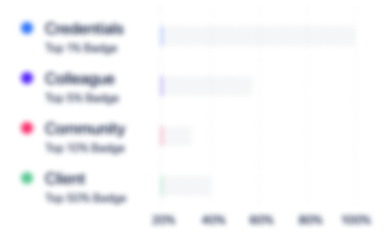
Bio
0
/5.0 / Based on 0 ratingsFilter reviews by:
Experience
-
Juniper Systems
-
United States
-
Appliances, Electrical, and Electronics Manufacturing
-
100 - 200 Employee
-
EMEA Service Centre Engineer
-
Nov 2017 - Present
Service, repair and support of the current and future Juniper systems product portfolio. Juniper systems is an industry-leading provider of ultra-rugged data collectors, precision GPS receivers, and niche-market software solutions. Our products are designed to be waterproof, dust proof, able to endure multiple drops to concrete, and function perfectly in the most extreme temperatures. Service, repair and support of the current and future Juniper systems product portfolio. Juniper systems is an industry-leading provider of ultra-rugged data collectors, precision GPS receivers, and niche-market software solutions. Our products are designed to be waterproof, dust proof, able to endure multiple drops to concrete, and function perfectly in the most extreme temperatures.
-
-
-
Vax Ltd
-
United Kingdom
-
Manufacturing
-
100 - 200 Employee
-
Inspection & Test Technician (NPI & After sales)
-
Nov 2015 - Oct 2017
Test and inspection of all VAX domestic and commercial products. Inspection of units that may have caused damage to property or personal injury. Create parts lists and service manuals for new and existing products. Support external retailers, repair agents and service centers. Assist with any identified quality issues. Investigate parts issues and queries. Investigate reasons for high return rates. Performance is Everything and this is certainly true for the New Product Introduction (NPI) team where our objectives are to ensure that our customers receive products that are not only meet their expectations but also satisfy all national and international product compliance standards. In the first instance, a multi-functional team work very closely with the VAX NPD team to ensure that new products are fully tested and comply with VAX and TTI Group test specifications. These are industry leading and exacting standards that are applied to all new VAX products. The team also work closely with the OEMs to ensure that they have robust processes, systems and procedures in place. In the event of customers finding a problem with their machine the team are quick to diagnose the fault and apply formal processes to determine the root cause and work closely with the OEMs to put effective solutions in place to ensure that future customers do not have the same concerns again.
-
-
-
-
Development Engineer
-
Jun 2007 - Nov 2015
Provide support for hardware and software issues that may occur on a daily basis for all members of the Reverse Logistics Centre including Express Repair Centres. Provide advice and guidance to all members of the Reverse Logistics Centre including Express Repair Centres. Respond in a timely fashion to raised Help-desk tickets within SLA. Ensure all ticket’s are closed to prevalent quality standards. Practice Electro Static Discharge awareness in order to prevent accidental damage to equipment. Assist the Training, Quality and Production departments in preparation of New Product Introduction within the repairs division, such that a repairs solution is in place for all products sold. Assist with preparation, distribution and understanding of all documents issued in order for technicians to develop best practice for repairs. Assist the Quality Department with technical investigations within the repairs process in order to demonstrate continual improvement. Provide on-line support to technicians in order to maximise the effectiveness of the repair process. To assist, where necessary, with the repair of handsets within the production environment in order to maximise the effectiveness of the business.
-
-
-
Carphone Warehouse
-
Computer and Network Security
-
1 - 100 Employee
-
Level 3 Repairs Technician
-
2004 - 2007
Provide support to L1 and L2 engineers.Carry out higher-level repairs and diagnostics.Achieve set targets.Software updates, Data wipe and IMEI re-build.The set-up and use of specialist software and equipment.Electronic component replacement.Functionality testing.
-
-
Level 2 Repairs Technician
-
2002 - 2004
Level 2 Mobile Phone Repairs
-
-
Level 1 Repairs Technician
-
Sep 2001 - 2002
Level 1 Mobile Phone Repairs
-
-
Education
-
University College Birmingham
Bachelor of Engineering (B.Eng.), Electrical, Electronics and Communications Engineering -
Matthew Boulton College, Birmingham
College, GNVQ Advanced in Electrical and Electronics Engineering -
Matthew Boulton College, Birmingham
GNVQ Intermediate in Engineering, Distinction -
Solihull Training Group
Youth Training - EnTra, Electrical and Electronics Engineering -
Kingsbury School Erdington
High School, GCSE's: English, Maths, Science, Business Studies, Design & Technology, Geography
Community
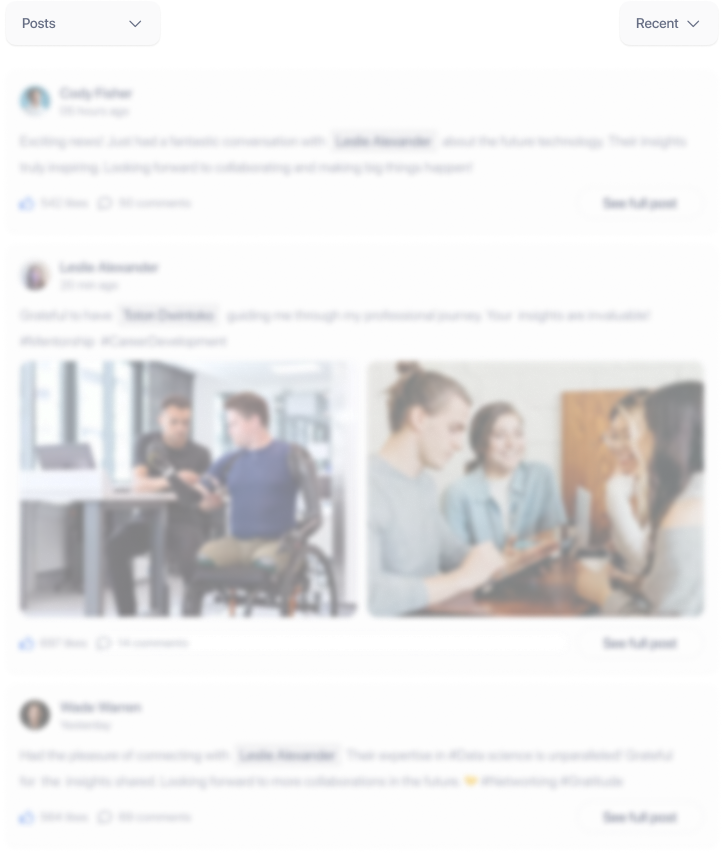